Ceramic PCBs in Ultra-High Vacuum Environments are essential for advanced technologies, especially in fields like space exploration, particle physics, and semiconductor research. These environments demand highly reliable materials capable of withstanding extreme conditions. However, working with ceramic PCBs in ultra-high vacuum (UHV) requires addressing some unique challenges. In this blog post, weâll explore the key considerations and strategies for using ceramic PCBs in UHV applications to ensure their reliability and performance over time.
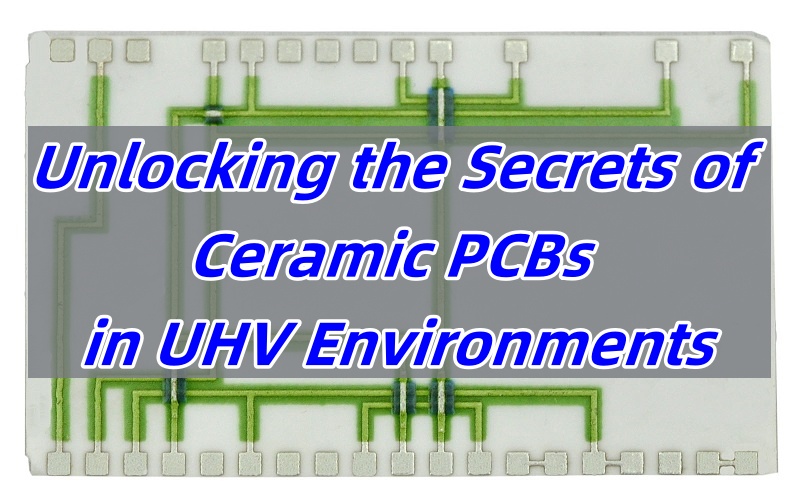
What are Ceramic PCBs?
Ceramic PCBs are specialized circuit boards that use ceramic materials for their base, such as aluminum nitride (AlN) or aluminum oxide (AlâOâ). They stand out for their excellent thermal conductivity, electrical insulation, and mechanical strength. These properties make them ideal for applications where high heat dissipation, electrical isolation, and structural integrity are crucial. Ceramic PCBs are commonly used in demanding industries like aerospace, telecommunications, and medical devices, where reliability and performance are non-negotiable.
What is Ultra-High Vacuum (UHV)?
Ultra-high vacuum refers to an environment where the pressure is lower than 10^-6 pascals (Pa), much lower than standard vacuum levels. In these conditions, there are very few gas molecules, creating an almost airless environment. UHV environments are found in cutting-edge fields such as space research, particle accelerators, and semiconductor fabrication. Working in a UHV environment means dealing with extreme conditions where materials must maintain their properties without the presence of air or other gases, which can significantly affect their behavior.
What Are The Key Challenges for Ceramic PCBs in Ultra-High Vacuum Environments?
Working with ceramic PCBs in ultra-high vacuum (UHV) environments presents several complex challenges that require careful consideration. Outgassing, mechanical stress, and electrical stability are among the most significant concerns.
To ensure the integrity and longevity of ceramic PCBs in these extreme conditions, each of these issues must be addressed through tailored strategies. These strategies may include using high-purity materials, implementing effective grounding techniques, and optimizing thermal expansion properties to mitigate the challenges and maximize the PCB’s performance over time.
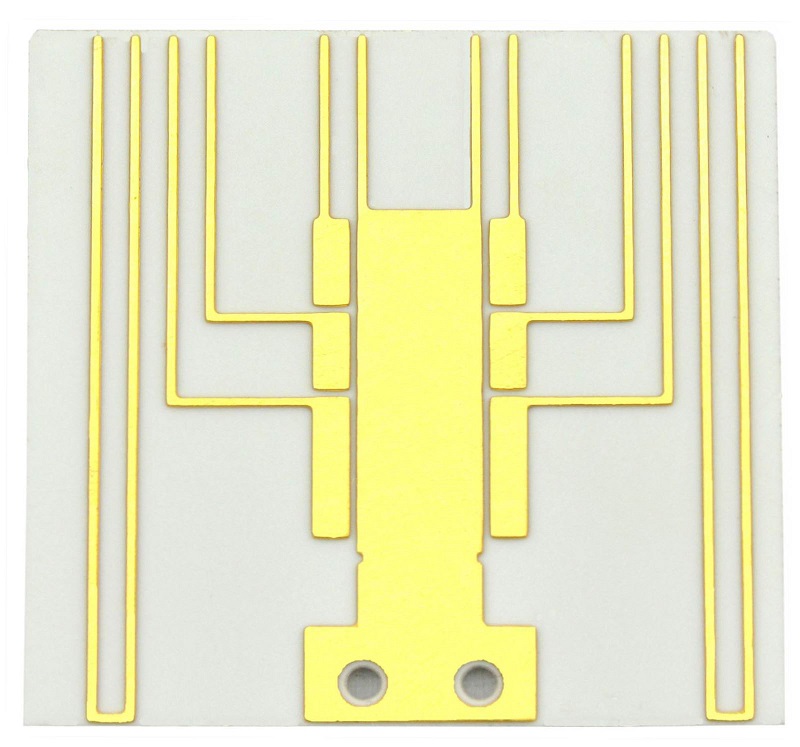
How Does Outgassing Affect Ceramic PCBs in UHV?
Outgassing is the release of gases trapped within the material when exposed to vacuum conditions. This is a major concern for ceramic PCBs in UHV, as the outgassed materials can contaminate the vacuum and affect sensitive equipment. When ceramics are used in UHV, any residual moisture, oils, or other volatile components may vaporize and disrupt the environment.
To address outgassing, ceramic PCBs should undergo a degassing process, often referred to as a âbake-out.â This procedure involves heating the ceramic material in a vacuum chamber to expel trapped gases. Additionally, using high-purity ceramics that have low outgassing rates can help minimize contamination risks and enhance the performance of the ceramic PCBs in UHV environments.
What Are the Mechanical Strength Issues for Ceramic PCBs in UHV?
Ceramic PCBs are highly valued for their thermal and electrical properties, but they are more brittle compared to metals. In UHV conditions, mechanical stress caused by thermal cycling, shock, or vibrations can lead to cracking or failure. This brittleness is especially concerning during launch, transport, or in operations where the ceramic PCB might be exposed to sudden shocks or vibrations.
To improve the mechanical strength of ceramic PCBs in UHV, itâs important to use high-quality, reinforced ceramics such as aluminum nitride (AlN) or silicon carbide (SiC). These materials offer better strength and fracture resistance. Furthermore, packaging and mounting the ceramic PCBs carefully can reduce stress and prevent mechanical damage during handling or operation.
How Do Thermal Expansion Issues Impact Ceramic PCBs in UHV?
Thermal expansion is another concern when working with ceramic PCBs in ultra-high vacuum conditions. Ceramic materials typically have a lower thermal expansion coefficient compared to metals. This can cause issues when ceramic PCBs are used alongside other materials, such as metal connectors or solder joints, which may expand or contract at different rates. The resulting mechanical stress can lead to cracks or fractures, especially under extreme temperature fluctuations.
To mitigate thermal expansion issues, itâs essential to match the ceramic PCB material with metals or alloys that have similar thermal expansion rates. This helps prevent mechanical stress and ensures that the components remain intact even when temperatures fluctuate dramatically in the UHV environment.
How Does UHV Affect the Electrical Performance of Ceramic PCBs?
The absence of air in ultra-high vacuum environments can also affect the electrical performance of ceramic PCBs. In a vacuum, thereâs no air to dissipate static charges, which can lead to issues such as electrostatic discharge (ESD). Additionally, high-voltage applications in UHV can be prone to corona discharge, a phenomenon where electrical breakdown occurs in the air or vacuum.
To ensure stable electrical performance, designers must incorporate specific features into the ceramic PCB design. For example, shielding, grounding techniques, and the use of anti-static coatings can help mitigate static charge build-up and reduce the risk of electrical discharge. These measures will help maintain the PCBâs reliability in UHV conditions, preventing interference with sensitive equipment and experiments.
How Can Surface Contamination Impact Ceramic PCBs in UHV?
In ultra-high vacuum environments, even the smallest particle or impurity can significantly affect the performance of sensitive instruments. Surface contamination on ceramic PCBs can lead to outgassing, which contaminates the vacuum and disrupts the operation of surrounding systems. Oils, dust, or foreign particles on the ceramic surface are common contaminants that can negatively impact performance.
To avoid contamination, ceramic PCBs should be thoroughly cleaned before use in UHV conditions. Cleaning methods such as ultrasonic cleaning, chemical cleaning, or using specialized solvents can help remove impurities from the PCB surface. Once cleaned, the PCBs should be handled in cleanroom environments to prevent recontamination.
What Are the Long-Term Effects of UHV on Ceramic Materials?
Exposure to ultra-high vacuum over extended periods can lead to material degradation. For example, high-energy particles, such as cosmic rays or X-rays, can alter the properties of ceramic materials. This degradation can manifest as changes in electrical conductivity, mechanical strength, or thermal performance. Over time, prolonged exposure to UHV can compromise the PCBâs integrity.
To minimize the long-term effects of UHV exposure, it is crucial to select ceramics that are specifically engineered for vacuum environments. These materials should be resistant to radiation and able to maintain their properties under extended exposure to UHV. Regular inspection and maintenance are also essential to ensure the continued performance of ceramic PCBs in such demanding conditions.
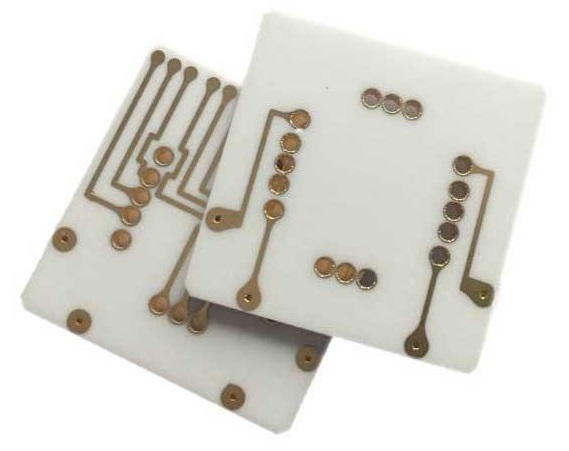
How Can Ceramic PCBs Be Optimized for UHV Environments?
To optimize ceramic PCBs for ultra-high vacuum environments, a combination of factors must be considered. First, using high-purity ceramics with low outgassing rates is essential for ensuring that the PCB does not contaminate the vacuum. Secondly, proper thermal and mechanical design can help prevent issues related to thermal expansion and mechanical stress. Lastly, regular cleaning and maintenance procedures are necessary to maintain the integrity of the ceramic PCBs and avoid contamination.
By addressing these considerations, ceramic PCBs can function effectively in UHV applications, offering exceptional performance in even the most extreme conditions.
Ceramic PCBs in Ultra-High Vacuum Environments play a critical role in various high-performance fields, offering superior thermal, electrical, and mechanical properties. However, working with these PCBs in UHV requires addressing unique challenges like outgassing, thermal expansion, and surface contamination. By selecting the right materials, optimizing the design, and following best practices for cleaning and maintenance, ceramic PCBs can deliver reliable performance in vacuum conditions. Whether used in space exploration, particle accelerators, or semiconductor fabrication, ceramic PCBs remain an essential component for success in these demanding applications. Best Technology offers a wide range of ceramic PCBs with high quality, tailored to meet the specific needs of each customer. Just feel free to reach out to us at sales@bestpcbs.com for more details.