Why choose OEM LED PCB? This guide covers benefits, applications, Gerber file handling, SMD5730 production, cost-cutting strategies, and FAQs for OEM LED PCB manufacturing.
As an OEM LED PCB manufacturer, Best Technology focus on OEM LED PCB manufacturing with proven 48 hours rapid prototyping for urgent orders and 3-4 weeks bulk delivery, supported by optimized supply chains for uninterrupted production. Clients consistently report <0.03% defect rates validated through automated AOI and X-ray inspections compliant with IPC Class 3 standards. Our engineers specialize in customizing LED arrays (5-200W), mixed-signal circuits, and hybrid FR4/aluminum substrates to meet precise thermal and optical specifications. Over 85% of projects achieve full functionality in first-round samples through our patented impedance control and solder mask alignment technologies. Flexible order scaling from 50 to 50,000+ units accommodates startups and global brands alike. Trusted by automotive and industrial clients, we ensure 100% NDA compliance and lifetime traceability. Start your OEM LED PCB project today for reliable performance and accelerated timelines. Contact us: sales@bestpcbs.com
What Is OEM LED PCB?
An OEM LED PCB is a customized printed circuit board specifically engineered for integrating light-emitting diodes (LEDs) into electronic systems. It serves as the structural and electrical foundation for LED modules, combining conductive pathways, insulation layers, and thermal management components to ensure stable performance. The core structure typically includes an aluminum substrate (1.0–3.0mm thick) for heat dissipation, a copper circuitry layer (1–6 oz thickness) to manage high currents, and a dielectric insulation layer (50–200μm) to prevent electrical shorts. Surface-mounted LED chips (e.g., SMD5730) are soldered onto designated pads, with layouts tailored to client specifications for dimensions, LED density, and trace routing. OEM LED PCB adhere to standardized certifications such as UL 94V0 for flammability and RoHS for environmental compliance.
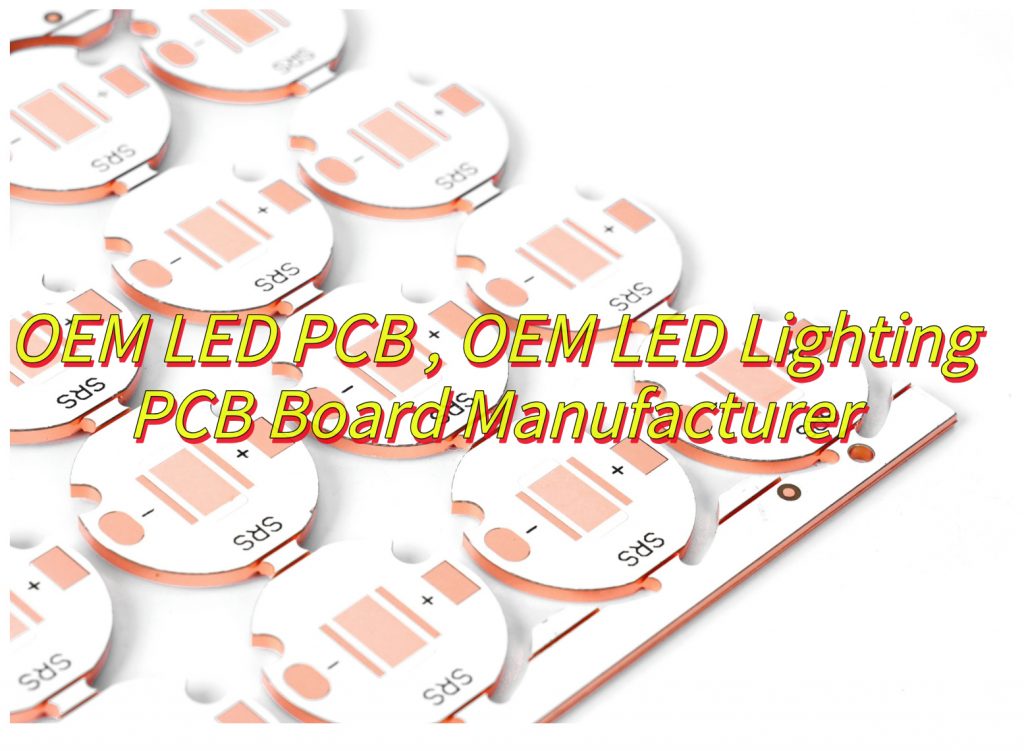
What Are Benefits of OEM LED PCB?
Here are benefits of OEM LED PCB:
- Custom-Designed for Performance-OEM LED PCB are built to match specific project requirements, optimizing power distribution, thermal management, and component placement for peak efficiency.
- Quality Control from Start to Finish-Manufacturers use premium materials (e.g., 94V0 fire-resistant substrates) and rigorous testing protocols to ensure durability and safety compliance.
- Cost Efficiency Over Time-While initial investments may be higher, OEM solutions reduce long-term costs through energy savings, lower maintenance, and bulk production discounts.
- Direct Technical Support-Partnerships with OEM suppliers often include engineering consultations, troubleshooting, and warranty coverage, streamlining problem resolution.
- Simplified Supply Chains-Single source manufacturing eliminates vendor coordination headaches, ensuring consistent quality and timely delivery.
- Certification Readiness-Reputable OEMs pre-design boards to meet global standards (e.g., UL, CE), simplifying regulatory approvals for your end products.
- Scalability for Growth-OEM manufacturers adapt designs seamlessly for increased order volumes, supporting business expansion without redesign delays.
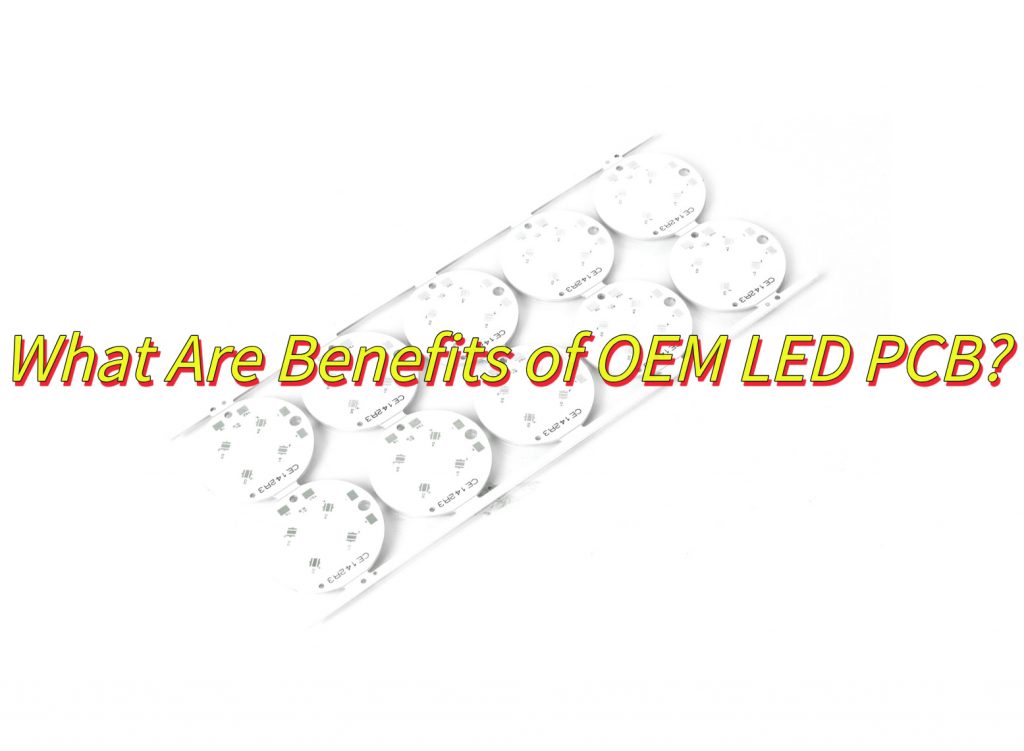
What Are Applications of OEM LED Single Side PCB?
Here are applications of OEM LED Single Side PCB:
- LED Lighting-Used in strip lights, panel lights, and outdoor fixtures for residential, commercial, and architectural projects.
- Electronic Signage-Power storefront displays, channel letters, and digital billboards with high-brightness LEDs.
- Appliances-Found in home devices like refrigerators, ovens, and smart home sensors for efficient operation.
- Automotive-Enable interior lighting (dome lights, dashboards) and exterior signals (license plates, turn indicators).
- Industrial & Safety-Control panels, emergency exit signs, and machinery interfaces rely on their durability.
- Medical Equipment-Used in handheld diagnostics tools and lab devices for clear, long-lasting indicators.
- Agriculture-Customizable grow lights and livestock monitoring systems benefit from their low-heat design.
- DIY & Prototyping-Affordable for hobbyists and startups testing new product concepts.
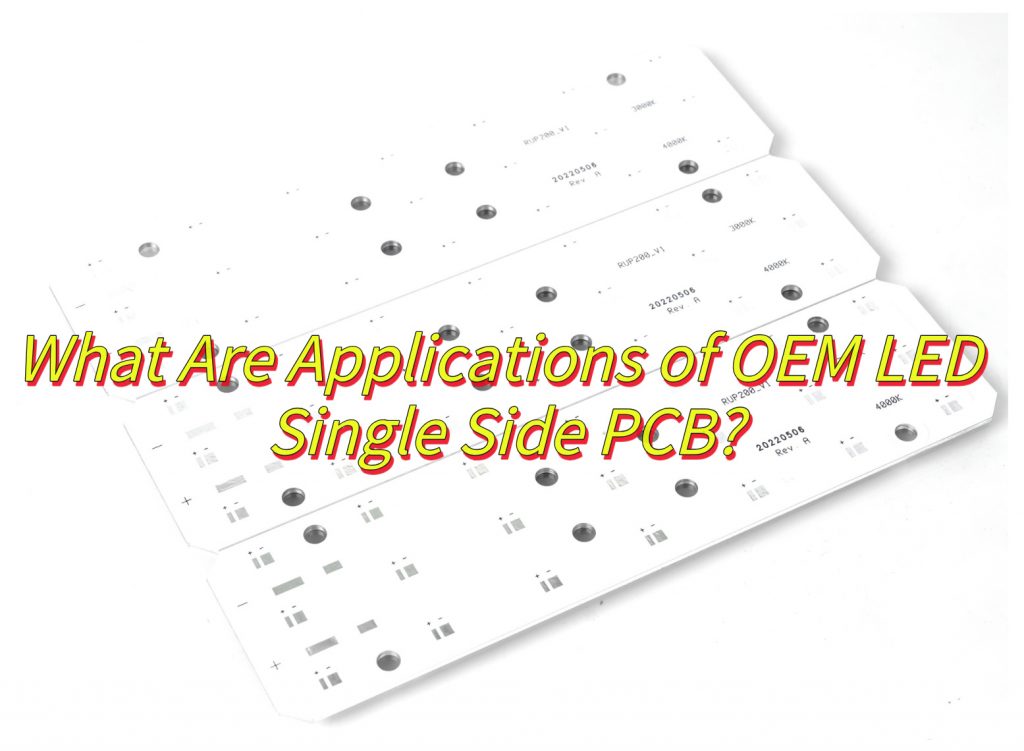
How to Handle Gerber Files for OEM LED PCB Reverse Engineering?
Reverse engineering OEM LED PCB via Gerber files requires precision. Follow these steps to streamline the process:
Source Complete Gerber Files
- Obtain files directly from the manufacturer or a trusted database to ensure all layers (copper, solder mask, silkscreen) are included.
Validate File Integrity
- Check for missing layers or corrupted data using free viewers like GC-Prevue.
Use Specialized Software
- Import files into reverse engineering tools (e.g., Altium Designer, OrCAD, or open-source options like KiCad). These tools decode coordinates and layer stacks.
Analyze Layers
- Start with the copper layer to map traces and pads. Cross-reference with the solder mask layer to identify component footprints.
Identify Components
- Match silkscreen labels to BOM data or use component recognition plugins in software to auto-detect resistors, capacitors, and LEDs.
Reconstruct Schematics
- Trace connections manually or use auto-routing tools to rebuild the circuit diagram. Prioritize high-speed signals (e.g., LED driver circuits).
Verify Dimensions
- Cross-check physical measurements against Gerber data to ensure accuracy, especially for LED spacing and thermal pad sizing.
Document Findings
- Export schematics, BOM, and layout files in standard formats (PDF, CSV, DX F) for manufacturing or prototyping.
Iterate and Test
- Fabricate a small batch and test functionality against the original PCB to refine the design.
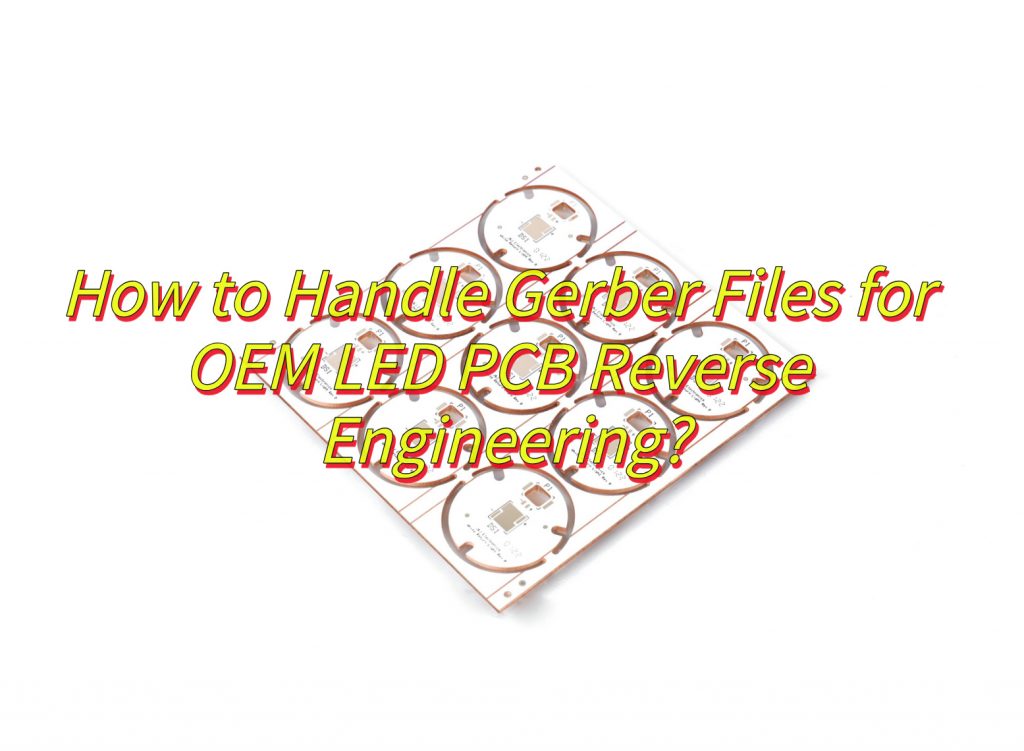
What’s the OEM LED SMD5730 LED Strip PCB Production Process?
Jere are OEM LED SMD5730 LED Strip PCB production process:
1. Material Preparation
- Substrate Selection: Use high-thermal-conductivity aluminum PCBs to manage heat from dense LED arrays.
- Components: Source SMD5730 LEDs, resistors, capacitors, and solder paste (lead-free for RoHS compliance).
2. PCB Design
- Layout: Arrange LEDs in series-parallel circuits to balance current and voltage. Include thermal pads for heat dissipation.
- Copper Tracing: Design wide traces (≥1.5mm) to handle high currents (typically 60mA per LED).
3. Soldering Process
- Stencil Printing: Apply solder paste via laser-cut stencils to ensure precise deposition.
- Pick-and-Place: Mount LEDs and components using automated machines for accuracy.
- Reflow Soldering: Use convection ovens with profile-controlled heating to melt solder and bond components.
4. Quality Inspection
- AOI Scanning: Automated optical inspection checks for solder joints, missing components, and polarity errors.
- X-ray Inspection: Verifies solder quality under components (e.g., BGA resistors).
5. Functional Testing
- LED Light Output: Test luminance uniformity and color consistency across the strip.
- Electrical Testing: Measure voltage drop, current stability, and insulation resistance.
6. Assembly
- Encapsulation: Apply silicone or epoxy resin to protect LEDs from moisture and mechanical stress.
- Cutting & Connectors: Dice strips to standard lengths (e.g., 5m) and attach DC connectors or solder pads.
7. Final QC
- Aging Test: Run strips at full power for 24–48 hours to identify early failures.
- Packaging: Roll strips on reels or cut to custom lengths for OEM clients.
How To Choose a Reliable OEM LED PCB Circuit Boards Manufacturer?
Here are some methods about how to choose a reliable OEM LED PCB circuit boards manufacturer:
Innovation Pipeline
- Evaluate their investment in R&D: Do they offer emerging technologies like flexible PCBs or smart LED systems?
- Check patents or collaborations with LED chip manufacturers (e.g., Cree, Nichia).
Client Feedback & Portfolios
- Request case studies from industries like automotive, horticulture, or architectural lighting.
- Contact their existing clients for unbiased reviews on responsiveness and problem-solving.
Geographic Advantages
- Prioritize manufacturers in regions with mature supply chains (e.g., Shenzhen, Taiwan) for cost efficiency.
- Assess proximity to your HQ for easier audits and faster shipping.
Customization Agility
- Test their willingness to adjust designs mid-production (e.g., modifying LED density or adding sensors).
- Inquire about minimum order quantities for custom shapes or materials.
Sustainability Practices
- Confirm use of recycled materials or energy-efficient processes (e.g., solar-powered factories).
- Ask about take-back programs for end-of-life PCBs.
Crisis Management
- Probe their contingency plans for pandemics, component shortages, or natural disasters.
- Review their track record during past crises (e.g., COVID-19 supply chain disruptions).
Industry Recognition
- Look for awards from trade shows (e.g., LED China, LightFair) or media features.
- Check memberships in associations like the National Electrical Manufacturers Association (NEMA).
How to Reduce OEM 94V0 LED Lighting PCB Assembly Costs?
Here’s how to reduce OEM 94v0 LED lighting PCB assembly cost:
Design for Manufacturability (DFM)
- Simplify PCB layouts to reduce drilling and routing complexity.
- Use standard panel sizes (e.g., 18”x24”) to minimize material waste.
- Choose surface-mount LEDs (SMD) over through-hole components for faster assembly.
Material Substitutions
- Replace exotic substrates (e.g., aluminum) with FR-4 for non-thermal-critical areas.
- Use 94V0-rated materials with lower copper weights (1 oz vs. 2 oz) if permissible.
- Source generic LED packages (e.g., 2835) instead of proprietary designs.
Streamline Production
- Consolidate SMT layers to reduce pick-and-place cycles.
- Eliminate silkscreen printing for non-critical markings.
- Adopt wave soldering over selective soldering for high-volume runs.
Leverage Volume Discounts
- Negotiate pricing tiers for components (resistors, capacitors) at 10k+ quantities.
- Commit to annual purchase volumes for PCB materials to secure bulk rates.
Optimize Supply Chain
- Source passive components from low-cost regions (e.g., Southeast Asia).
- Partner with local suppliers to avoid import tariffs and shipping delays.
Automate Testing
- Implement flying-probe testing instead of manual inspection for mid-volume batches.
- Use open-source software (e.g., JTAG) for functional testing to cut licensing fees.
Quality Cost Control
- Invest in AOI systems to catch defects early, reducing rework costs.
- Cap acceptance quality levels (AQL) at 1.0% to balance yield and inspection costs.
FAQs of OEM LED PCB Manufacturing
- Q: “Why are my PCB assembly costs 20% over budget?”
A: Overspending often stems from design inefficiencies or poor planning. Cut costs by standardizing PCB sizes to reduce panel waste, using generic LED packages (e.g., 3030) instead of custom designs, and negotiating annual component contracts for bulk discounts. Avoid over-engineering with unnecessary features like gold plating or heavy copper layers unless absolutely required. - Q: “How do I stop solder defects like head-in-pillow?”
A: Prevent rework costs with upfront investments. Add automated optical inspection (AOI) after reflow soldering to catch defects early, use solder paste with a tighter particle size distribution, and train operators on proper stencil cleaning protocols. Even small investments here can reduce rework rates by 40%. - Q: “Why are my lead times 30% longer than promised?”
A: Delays often stem from supply chain bottlenecks. Partner with local suppliers to avoid customs delays, stock critical components (e.g., IC drivers) in regional hubs, and use digital tools to track order fulfillment in real time. For high-volume orders, consider dual-sourcing components to avoid single-supplier delays. - Q: “Can I meet 94V0 standards without overspending on materials?”
A: Absolutely—optimize material choices. Use 94V0-rated FR-4 for non-thermal layers, avoid unnecessary copper plating (e.g., 1 oz vs. 2 oz), and source LEDs pre-certified for fire resistance. Work with your material supplier to find cost-effective alternatives without sacrificing safety compliance. - Q: “How do I handle last-minute design changes?”
A: Minimize disruptions with clear change-order fees in client contracts, modular PCB designs for easier component swaps, and pre-production prototyping to catch errors early. Charge clients for late-stage modifications to discourage frequent revisions, and use version control software to track design iterations.