Choosing the right controller for a UAV depends on various factors like the type of UAV, its purpose, your experience level, and budget.
- Purpose: If you use drones for professional missions, you may need a powerful GCS. For temporary flights, a radio controller may be sufficient.
- Budget: If you’re on a tight budget, a pocket radio may be the best option.
- Drones: Top drones are usually equipped with good controllers, so you may not need to buy a separate remote.
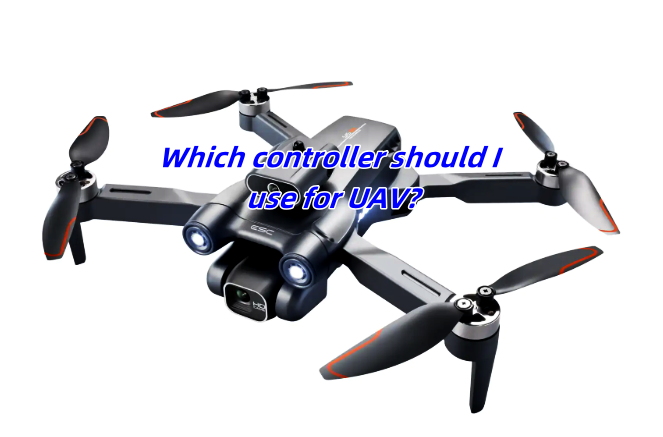
Popular Flight Controllers for UAVs
- DJI Flight Controllers (e.g., A3, N3): Great for commercial applications, high stability, and ease of use.
- Pixhawk (Cube Orange, PX4): Open-source, highly customizable, and suitable for research and commercial use.
- BetaFlight Controllers: Excellent for racing drones and hobbyists.
- Navio2: Turns a Raspberry Pi into a flight controller, ideal for custom applications and experimentation.
What Is a UAV Flight Controller?
UAV is the abbreviation of Unmanned Aerial Vehicle, is the use of radio remote control equipment and self-provided program control device unmanned aircraft, including unmanned helicopter, fixed wing aircraft, multi-rotor aircraft, unmanned airship, unmanned umbrella aircraft. In a broad sense, it also includes near-space vehicles (20-100 km airspace), such as stratospheric airships, high-altitude balloons, and solar-powered drones. From a certain point of view, drones can complete complex air flight tasks and various load tasks under unmanned conditions, and can be seen as “air robots”.
The flight control system is the core system of the UAV to complete the whole flight process such as take-off, flight, task execution and return recovery. Flight control is equivalent to the role of the pilot to the man-machine of the UAV, and we believe that it is one of the most core technologies of the UAV. Flight control generally includes three parts: sensor, on-board computer and servo actuation equipment, and the functions achieved mainly include UAV attitude stabilization and control, UAV mission equipment management and emergency control.
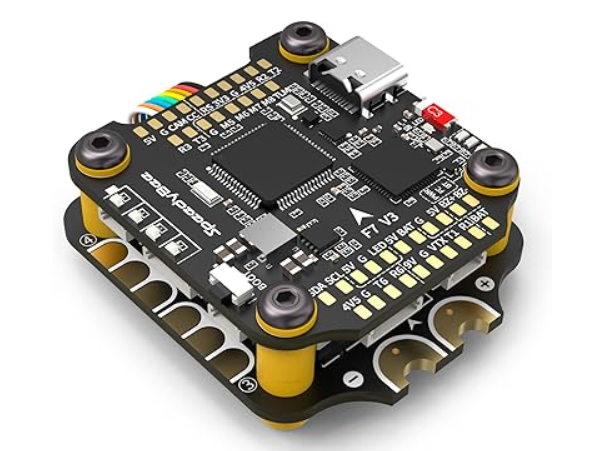
Which Controller Is Used in a Drone?
Two types of controllers are integral to drone operations: the flight controller and the remote controller. The flight controller is mounted on the drone and manages its internal systems. It monitors data from sensors like gyroscopes, accelerometers, and barometers to maintain stability. Additionally, it processes inputs from the pilot, ensuring precise execution of commands.
The remote controller is what the pilot uses to steer the drone. It communicates wirelessly with the flight controller, usually via radio frequencies. Modern remote controllers come equipped with ergonomic designs, customizable buttons, and live feed displays.
For example, DJI drones use advanced proprietary systems, combining high-performance flight controllers with intuitive remotes. Racing drones, on the other hand, often rely on lightweight controllers designed for speed and agility.
Does the Military Use Xbox Controllers for Drones?
Yes, the military sometimes uses Xbox controllers for drones. This might seem unconventional, but it has practical benefits. Xbox controllers are widely recognized and easy to operate. Many soldiers are already familiar with their layout from gaming, which reduces training time.
For less critical missions, adapting Xbox controllers is cost-effective. They provide a user-friendly interface for operating UAVs without compromising functionality. However, for advanced military drones, specialized controllers with enhanced security and precision are standard. These controllers can handle encrypted communication, complex tasks, and long-range operations.
While the use of Xbox controllers highlights creativity, itâs limited to specific scenarios. For professional-grade UAVs, more robust systems remain the norm.
Can You Use Different Controllers for Drones?
Can you use different controllers for drones? Yes, you can use different controllers for drones, but it requires careful planning. Most drones come with a default remote, but advanced users often switch to alternatives for better functionality. For example, a racing drone enthusiast might replace the stock controller with one offering lower latency and faster response.
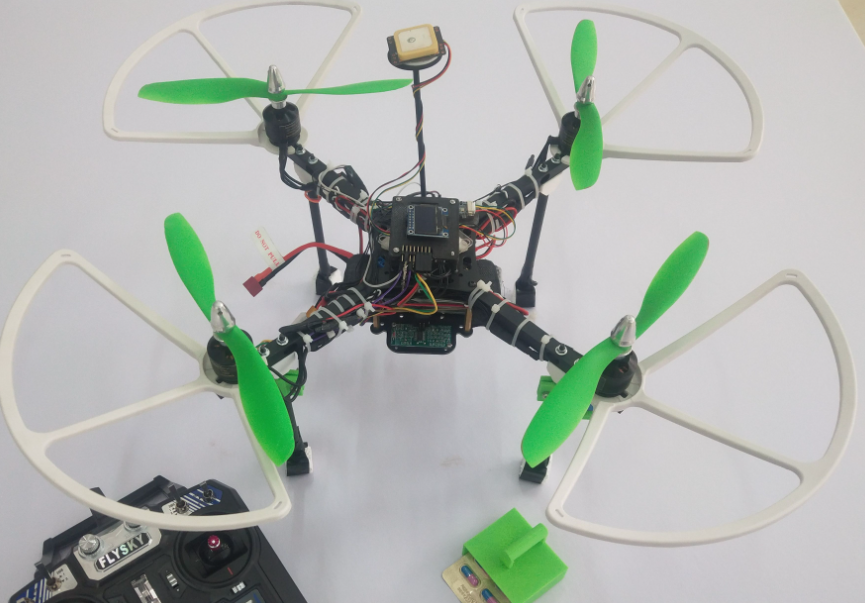
Compatibility is crucial when using a different controller. The new remote must support the communication protocol of the droneâs flight controller. Common protocols include SBUS, PPM, and DSMX. Mismatched systems can result in loss of control or limited functionality.
Some controllers allow users to connect their smartphones or tablets for enhanced capabilities. This is popular with photography drones, where touchscreens can display live video feeds or advanced settings. When experimenting with new controllers, always test the setup in a safe environment.
Which Flight Controller Is Used in DJI?
DJI is a leader in the UAV industry, known for its advanced flight controllers. Popular models include the Naza, A3, and the newer Zenmuse H20 series. These controllers are packed with features tailored for seamless performance:
- Stability: DJI controllers use GPS and IMUs (Inertial Measurement Units) to maintain precise positioning.
- Automation: Intelligent flight modes like waypoint navigation, orbit mode, and follow-me functions are common.
- Integration: DJIâs controllers work seamlessly with their proprietary motors, cameras, and software.
Can a Drone Fly Without a Flight Controller?
No, a flight controller is essential for flying a drone. It processes inputs, balances the drone, and manages its systems. Without a flight controller, the UAV cannot interpret pilot commands or stabilize itself.
Even basic drones rely on flight controllers for manual control. Advanced models use them for automation and sensor integration. Attempting to fly without one would result in erratic movements and likely crashes.
What Is the Best Flight Controller for 2024?
Choosing the best flight controller in 2024 depends on your needs. Here are some top contenders based on performance and features:
- Pixhawk 6X:
A favorite among hobbyists and professionals. It supports advanced automation and is compatible with Ardupilot firmware.
- DJI A3 Pro:
Designed for high-end commercial drones, this controller excels in stability and precision.
- Betaflight F7:
A top choice for racing drones, known for low latency and fast response.
- CubePilot Orange:
Ideal for industrial applications, this controller handles heavy payloads and complex missions.
- Holybro Kakute F7:
Affordable yet reliable, it suits beginners venturing into custom builds.
Key Element in a UAV Controller: Drone Circuit Board
The drone circuit board is the backbone of the UAV controller. It houses essential components that govern the drone’s functions, from navigation to communication. Without this intricate board, a drone would lack the ability to process commands or execute movements effectively.
Best Technology made various drone circuit boards for our customers, we offer one-stop service from pcb design to PCB manufacturing, aiming to give you a best experience. Interested in it? Contact us right now!