Ceramic PCB assembly is becoming a preferred option for industries that demand high thermal conductivity, stable performance, and strong mechanical strength. Compared to traditional FR4 boards, ceramic circuit boards handle heat better, last longer, and work reliably even in extreme environments. That’s why companies in aerospace, automotive, and medical fields turn to this technology for their critical projects.
Ceramic materials offer natural thermal conductivity, so they don’t need extra heat dissipation layers. That means more compact designs without losing efficiency. With ceramic PCB assembly, you also get enhanced reliability when working with high-power components or complex multilayer designs.
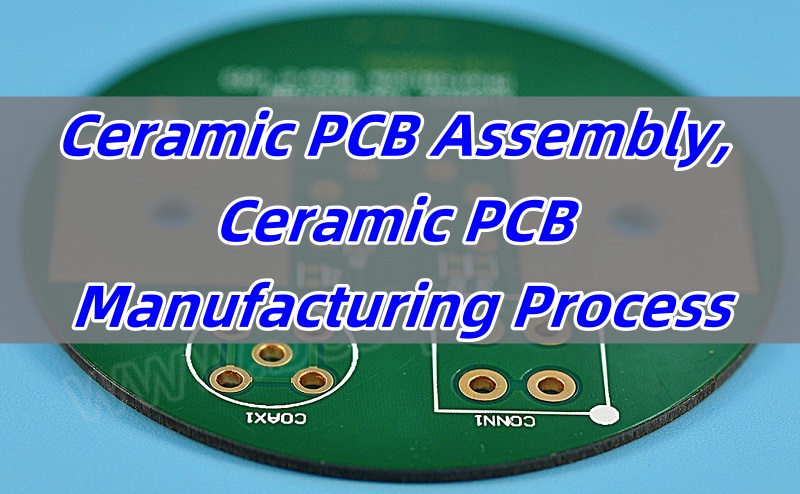
What are the substrates for ceramic PCB?
Ceramic PCBs use different substrates depending on the performance requirements of the application. Alumina (Al2O3) is the most common due to its balanced cost and performance. It provides good thermal conductivity, electrical insulation, and mechanical strength. For even higher thermal performance, Aluminum Nitride (AlN) works better. It handles heat far more efficiently, so it’s often used in power electronics or LED applications. Beryllium Oxide (BeO) is another option, though its use is less common due to safety concerns during manufacturing. Still, it offers excellent thermal conductivity when needed.
What are the different types of ceramic PCB?
Ceramic PCBs come in different types to meet various technical needs. Single-layer ceramic PCBs are the simplest and often used when the design doesn’t need many connections. They work well for LED modules or simple power circuits. Double-layer ceramic PCBs offer more flexibility for designs with higher component counts. They can handle complex circuits with better routing options. For advanced applications, multilayer ceramic PCBs provide even more design freedom. These allow for compact, high-density circuits, perfect for RF modules, medical sensors, and aerospace systems.
What are the components of a ceramic PCB?
Ceramic PCBs contain several essential elements that work together to deliver strong performance. The ceramic substrate forms the base, providing heat management, insulation, and structural support. On top of that, copper traces form the electrical connections. These traces are either directly bonded or printed, depending on the design process. The solder mask covers exposed copper to prevent oxidation, though ceramic PCBs sometimes skip this layer to enhance thermal transfer. Finally, components like resistors, capacitors, and ICs are soldered onto the surface to complete the assembly.
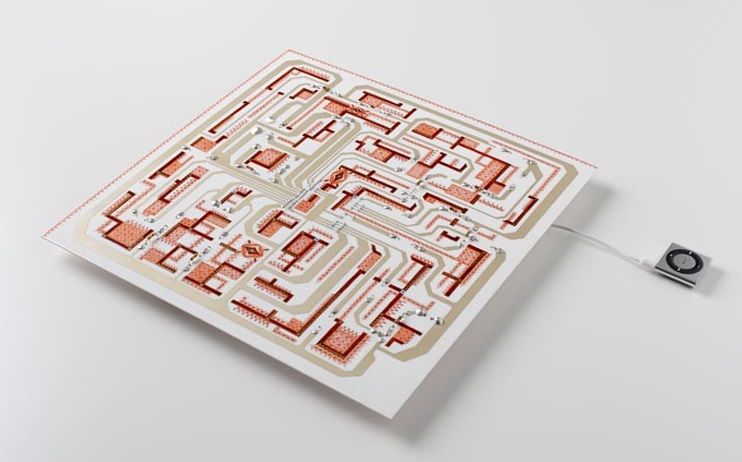
How thick is ceramic PCB?
Ceramic PCBs come in different thicknesses to match the needs of the design. Common ceramic substrate thicknesses range from 0.25mm to 1.5mm, depending on the type of material and required mechanical strength. Thin ceramic boards work well when weight reduction matters, such as in aerospace applications. Thicker boards support larger components and provide additional strength. The copper layer itself also varies, usually from 10μm to 140μm, depending on current-carrying requirements. Choosing the right combination of ceramic and copper thickness ensures good performance without unnecessary cost.
How to make ceramic PCB?
The ceramic PCB manufacturing process begins with circuit design optimization (e.g., Gerber file preparation) to account for ceramic-specific properties such as thermal expansion and mechanical stability. A ceramic substrate (e.g., alumina or aluminum nitride) is then cut into panels from larger sheets. For copper trace formation, two primary methods are used: Direct Bonded Copper (DBC) involves bonding copper foil to the ceramic under high temperature and pressure, followed by photolithography and etching to define precise circuit patterns, making it ideal for high-power applications. Alternatively, Thick Film Printing uses screen-printing of conductive pastes (e.g., silver-palladium) onto the ceramic surface, which are then sintered at high temperatures to solidify the traces, a cost-effective method for simpler designs. After trace formation, laser drilling creates micro-vias (if required), which are metallized using electroless copper plating to ensure electrical connectivity between layers. Surface finishes like ENIG (Electroless Nickel Immersion Gold) or OSP (Organic Solderability Preservative) are applied to protect copper traces from oxidation. Finally, during assembly, solder paste is deposited, components are placed, and reflow soldering or precision-controlled thermal processes are employed to bond components while minimizing thermal stress mismatch between ceramic and metal parts.
What is the difference between ceramic PCB assembly and FR4 PCB assembly?
Ceramic PCB assembly and FR4 PCB assembly follow some similar steps, but the materials and processes vary a lot. In FR4 PCBs, the fiberglass and epoxy resin form the main structure. These materials offer flexibility, but they can’t handle high temperatures well. Ceramic PCBs use ceramic substrates that naturally conduct heat, so they don’t need extra thermal management layers. This simplifies the design, especially for power electronics. During assembly, soldering ceramic PCBs requires more precision since ceramic expands differently from metals. Specialized equipment helps control the process, ensuring components bond properly without cracking the ceramic. Compared to FR4, ceramic PCB assembly often handles higher temperatures, offers better stability, and lasts longer in demanding environments.
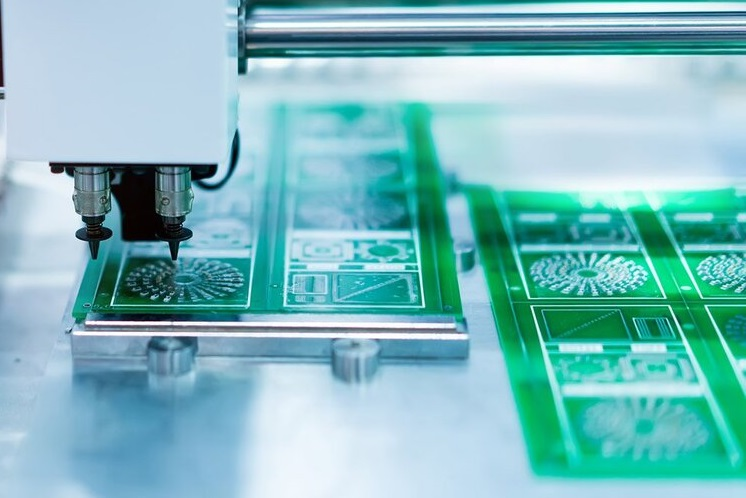
What are the benefits of ceramic PCB?
There are many reasons why companies prefer ceramic PCB assembly for critical projects. Ceramic substrates naturally provide high thermal conductivity, which helps heat-sensitive components stay cool. That extends component life and improves reliability. Ceramic PCBs also offer excellent mechanical strength despite their thin profile. This strength helps them survive harsh conditions, including vibration or sudden temperature changes. Another key benefit is high-frequency performance, which matters for RF applications. Ceramic’s low dielectric loss helps maintain signal integrity. Additionally, ceramic materials resist chemicals, moisture, and aging better than traditional PCB materials. Combined, these benefits make ceramic PCB assembly an excellent choice for high-performance, long-lasting products.
How to choose the best ceramic PCB manufacturer for your project?
Choosing the right ceramic PCB manufacturer makes a huge difference in both quality and cost. Start by checking the manufacturer’s experience with ceramic PCB assembly, especially for your industry. Ceramic handling requires special expertise, so working with an experienced supplier reduces risk. Next, ask about material options. A good manufacturer offers multiple ceramic materials, including alumina, aluminum nitride, and others. Also, review their equipment capabilities. Advanced equipment helps control tolerances and ensures good bonding between ceramic and copper. Don’t forget to check their quality certifications and testing processes. Reliable manufacturers offer full inspection reports, including thermal cycling tests, solderability checks, and X-ray inspections to confirm internal connections. Finally, consider their lead times and ability to support custom designs. Flexibility matters, especially when developing innovative products. By the way, reliable manufacturer is able to promptly reply to inquiries and resolve issues, providing technical support and design consultation to save time and effort in the design and production processes.
Put it in a nutshell, ceramic PCB assembly continues to gain popularity thanks to its unmatched thermal performance, mechanical strength, and long-term reliability. Whether you need multilayer ceramic PCBs, alumina PCBs, or specialized designs for RF or power electronics, ceramic materials offer clear advantages. By partnering with an experienced ceramic PCB manufacturer, you can ensure your products meet high standards and work reliably under tough conditions.
At Best Technology, we specialize in China ceramic PCB assembly and wholesale ceramic PCB assembly, delivering quality products for customers worldwide. With more than 18 years of experience, we offer custom designs, fast lead times, and full inspection services to support your most challenging projects. Get in touch with us at sales@bestpcbs.com for any questions or additional information.