FR4 PCB is the backbone of modern electronics, offering a perfect balance of durability, cost-effectiveness, and electrical performance. As the most widely used PCB material, it supports various applications, from consumer gadgets to industrial machinery. Whether you need a FR4 PCB prototype, FR4 PCB assembly, or a reliable FR4 manufacturing partner, Best Technology can bring you good service. In this blog, we explore its types, materials, design process, advantages, and why Best Technology is your best choice for FR4 PCB manufacturing.
Best Technology specializes in FR4 PCB design and manufacturing, offering small-batch production and FR4 PCB assembly services tailored to your needs. As a professional FR4 PCB manufacturer, we ensure precision and reliability for every project. If you need a FR4 printed circuit board, please feel free to contact us at sales@bestpcbs.com.
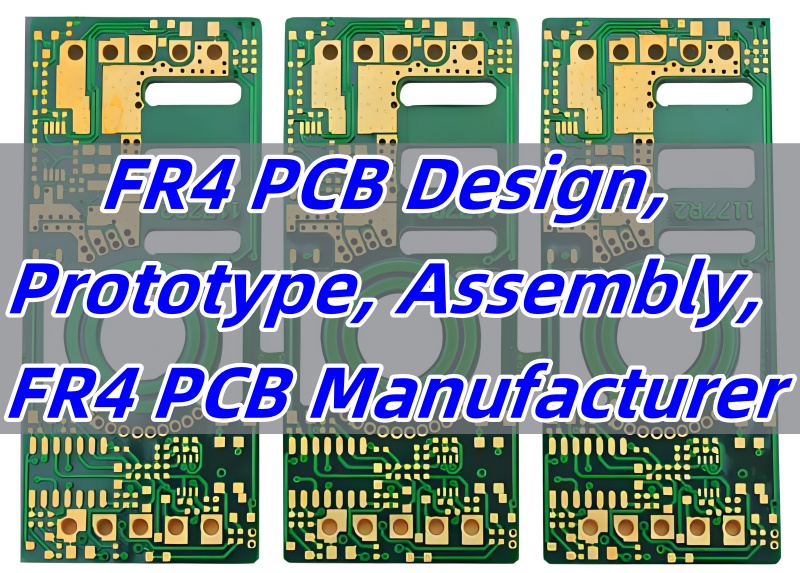
What is FR4 PCB?
FR4 PCB is the most common type of printed circuit board, made from a glass-reinforced epoxy laminate material. It offers excellent electrical insulation, mechanical strength, and thermal resistance, making it ideal for various electronic applications. Due to its versatility and cost-effectiveness, it is widely used in consumer electronics, industrial equipment, and automotive applications.
What are the Different Types of FR4 PCBs?
FR4 PCBs can be categorized based on different classification dimensions, including layer count, flexibility, special functionality, and performance characteristics. Below is a structured breakdown:
1. Classification by Layer Count
Single-Sided & Double-Sided FR4 PCB – Single-sided PCBs have copper on one side, while double-sided PCBs have copper layers on both sides, making them suitable for more complex circuit designs.
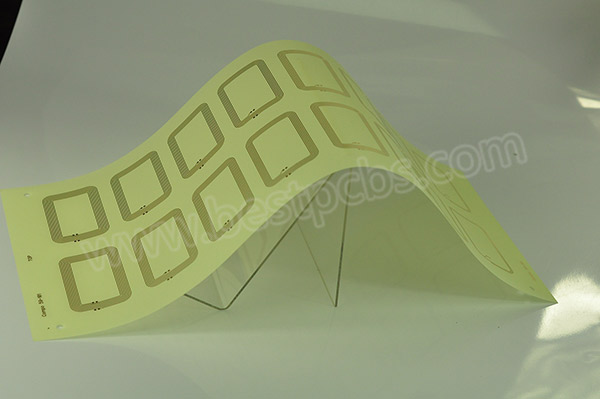
Multilayer FR4 PCB – These PCBs have three or more layers stacked together, allowing high-density circuit integration for advanced electronic applications.
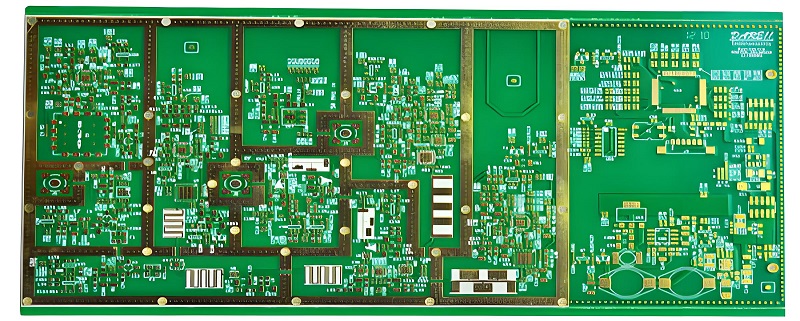
2. Classification by Flexibility
Rigid-Flex FR4 Circuits – The rigid sections utilize FR4 material. A hybrid of rigid and flexible PCB technology, offering mechanical flexibility and compactness for specialized applications like medical devices and wearables.
3. Classification by Special Functionality
Heavy Copper PCB – Designed with heavy copper layers to handle high currents and improve thermal performance, often used in power electronics.
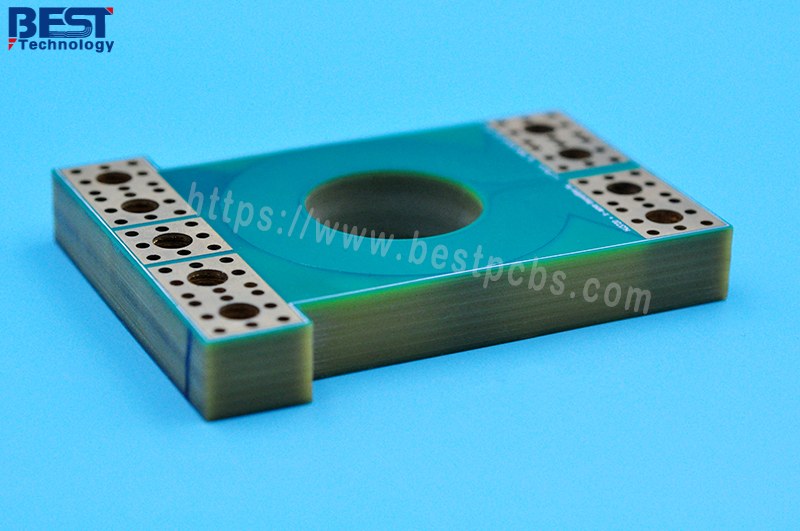
Bus Bar PCB – Built using FR4 material combined with heavy copper layers, providing superior power distribution and heat dissipation in applications requiring high current flow. Limited to designs using pure FR4 base material with heavy copper layers, if additional metal structures are used, the design is no longer considered a standard FR4 PCB.
High-Speed PCB – Optimized for fast signal transmission with minimal interference, commonly used in communication and networking systems.
Impedance Control PCB – Built for applications requiring stable signal integrity, such as high-frequency communication and RF circuits.
Extra Thin PCB – Ultra-thin PCBs designed for compact electronic devices where space is a key constraint.
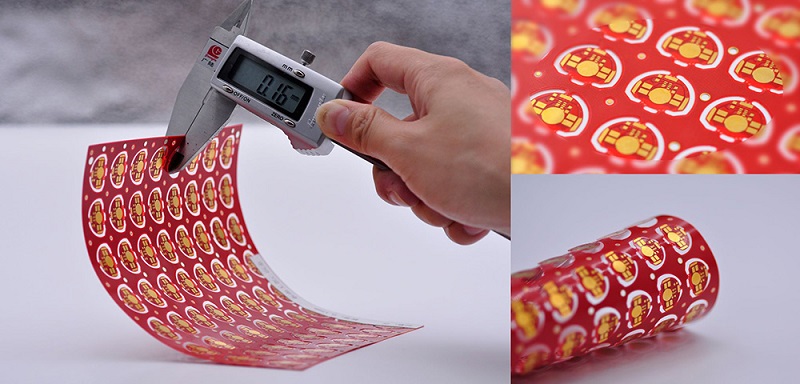
4. Classification by Performance Characteristics
High-TG PCB – Manufactured with high glass transition temperature (TG) material, providing superior heat resistance for demanding applications.
HDI PCB (High-Density Interconnect) – Features microvias and high-density wiring, enabling miniaturized electronic designs with increased functionality.
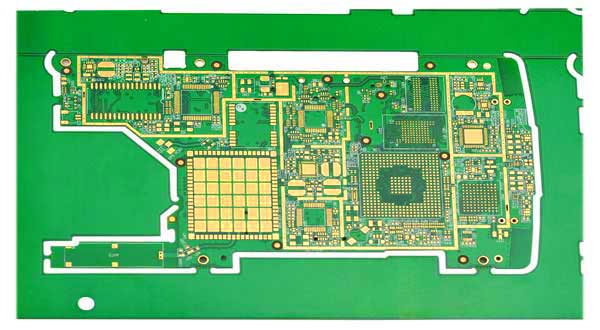
RF Board (Low-Frequency Applications) – Designed for radio frequency circuits operating at lower frequencies, ensuring stable performance while minimizing signal loss and interference. Higher frequency applications typically require specialized materials beyond standard FR4.
Each category serves a unique purpose in various industries, from consumer electronics to aerospace and telecommunications. Selecting the right FR4 PCB type ensures the best performance for specific applications.
What Materials Are Used to Make FR4 PCBs?
FR4 PCBs are primarily composed of:
- Fiberglass (Glass-Reinforced Epoxy) – Provides mechanical stability and durability.
- Epoxy Resin – Enhances electrical insulation and strength.
- Copper Foil – Ensures excellent conductivity for signal transmission.
- Solder Mask – Protects the copper traces from oxidation and damage.
- Silkscreen Layer – Adds component markings for easy identification.
These materials contribute to the PCB’s long lifespan and reliable performance.
How to Design an FR4 PCB?
Designing an FR4 PCB requires a structured approach to ensure optimal performance:
- Define Circuit Requirements – Identify power, signal, and space constraints.
- Select PCB Layer Configuration – Choose between single, double, or multilayer options.
- Layout Component Placement – Arrange components efficiently to reduce interference.
- Route the Traces – Ensure proper signal flow with optimized trace widths.
- Apply Ground and Power Planes – Improve electrical performance and reduce noise.
- Perform Design Rule Checks (DRC) – Validate design before fabrication.
Using advanced PCB design software helps streamline the process and prevent errors.
What Are the Benefits of an FR4 PCB?
FR4 PCBs offer multiple advantages:
- Cost-Effective – Affordable material with high durability.
- High Electrical Insulation – Prevents signal loss and interference.
- Excellent Mechanical Strength – Withstands physical stress.
- Heat Resistance – Performs well under varying temperatures.
- Versatile Applications – Used across multiple industries.
Due to these benefits, FR4 remains the most preferred PCB material worldwide.
What Are the Applications of FR4 PCBs?
FR4 PCBs are used in various industries, including:
- Consumer Electronics – Smartphones, tablets, and gaming consoles.
- Industrial Equipment – Power control systems and automation devices.
- Automotive Electronics – Engine control units and infotainment systems.
- Medical Devices – Diagnostic equipment and wearable health monitors.
- Aerospace and Defense – Communication and navigation systems.
Their reliability and performance make them essential for modern technology.
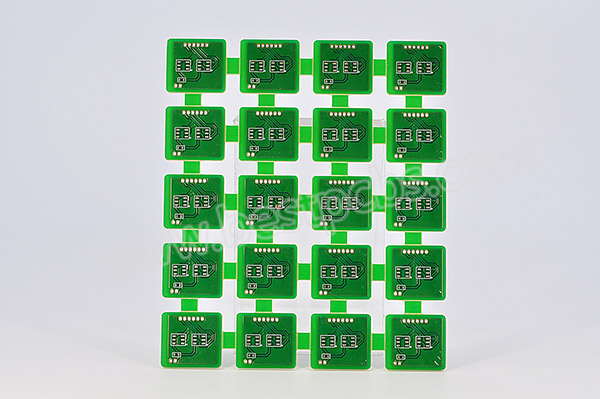
Why Choose Best Technology as Your FR4 PCB Manufacturer?
Best Technology provides various types of FR4 PCBs. Here’s why customers trust us:
- Advanced Manufacturing Capabilities – We use state-of-the-art equipment to produce high-quality FR4 PCBs.
- Custom PCB Solutions – We tailor designs to meet unique customer requirements.
- Strict Quality Control – Every board undergoes thorough testing.
- No MOQ– Best Technology provides flexible order quantity. We support small-batch orders if you are in the initial stage of your projects.
- Fast Turnaround – Quick prototyping and production services.
- Quick & Efficient Service — Our team provides 24/7 engineering support for any questions or technical concerns.
Partnering with Best Technology ensures high-quality and reliable FR4 PCBs. Pls feel free to reach out to us at sales@bestpcbs.com.
FAQs of FR4 PCB
1. Does FR4 Absorb Moisture?
Yes, but at a very low rate. FR4 has good moisture resistance, making it suitable for humid environments.
2. What Does FR4 Stand For?
FR4 stands for “Flame Retardant 4,” indicating its self-extinguishing properties.
3. What Are the Disadvantages of FR4?
While FR4 is versatile, it has limitations, such as lower thermal conductivity compared to metal core PCBs.
4. What Are the Advantages of FR4?
FR4 is cost-effective, durable, and offers excellent electrical insulation, making it the go-to material for many PCB applications.
In a nutshell, FR4 PCBs remain the top choice for various applications due to their durability, cost-effectiveness, and reliability. Whether you need single-layer, double-layer, or multilayer designs, Best Technology can meet your requirements with high-quality FR4 manufacturing. Pls feel free to contact us at sales@bestpcbs.com to discuss your FR4 PCB needs!