Are you looking for a competitive LED Star PCB manufacturer? Let’s explore more about LED star PCB’s advantage and application as well as how to select a trusted LED star PCB board manufacturer.
As a trusted LED Star PCB manufacturer with full ISO/UL/CE certifications, Best Technology have scalable SMT production lines, and rigorous IQC-FQC quality protocols validated through thermal/vibration/aging tests. Our vertically integrated supply chain ensures flexible MOQs with affordable price, stable lead times, and end-to-end logistics support from compliant export packaging to freight optimization. And we also support customized LED star PCB, such as material, dimension and color customization. If you have any request for LED star PCBs, please contact us: sales@bestpcbs.com
What Is LED Star PCB?
LED Star PCB is a specialized printed circuit board designed for high-density LED installations, featuring a star-shaped layout that optimizes thermal management and light distribution. This configuration allows multiple LEDs to be arranged in a radial pattern, enhancing heat dissipation through increased surface area and airflow efficiency. The board typically incorporates advanced materials like aluminum or ceramic substrates to further improve thermal conductivity, making it ideal for high-power LED applications. Its modular design enables flexible customization in terms of LED quantity, color (including red LED star PCB and other RGB LED star PCB options), and dimensions, catering to diverse lighting needs such as decorative lighting, stage effects, and industrial illumination.
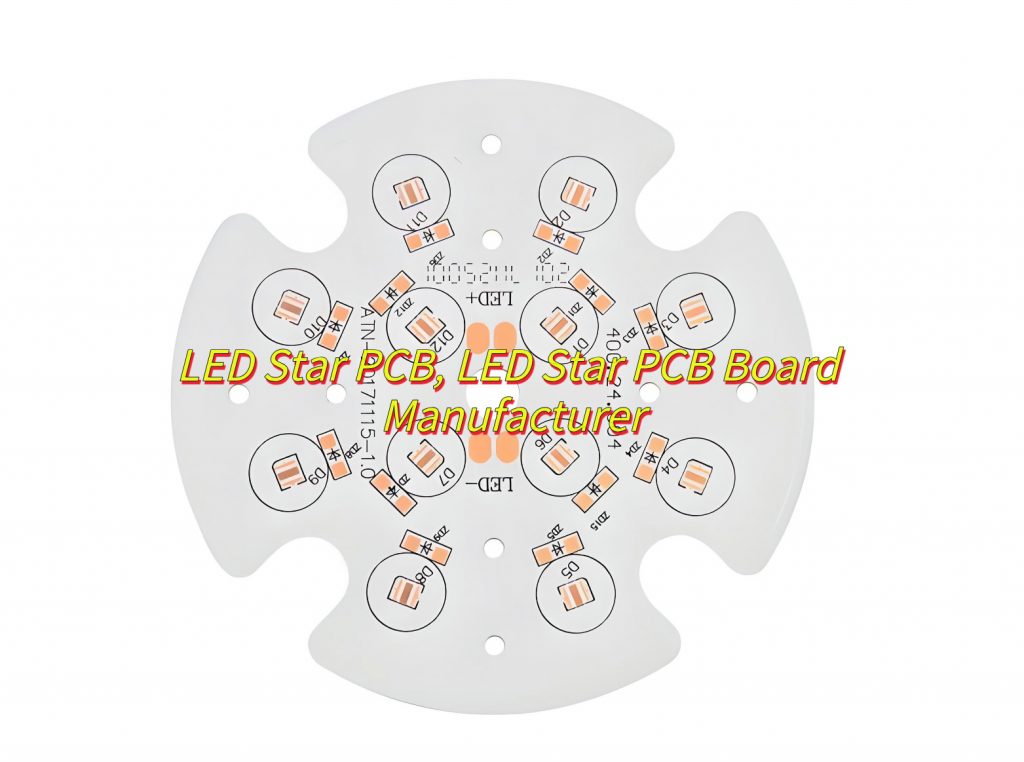
What Are Advantages of Star LED PCB?
Star LED PCB Advantages:
- Enhanced Thermal Management – Radial layout improves heat dissipation efficiency
- Uniform Light Distribution – Symmetrical LED arrangement eliminates dark spots
- Space Optimization – Compact star design maximizes LED density
- Customization Flexibility – Adaptable LED count, color combinations, and dimensions
- Advanced Material Construction – Aluminum/ceramic substrates ensure durability
- Versatile Applications – Suitable for decorative, architectural, and stage lighting
- Easy Installation – Modular design simplifies assembly and maintenance
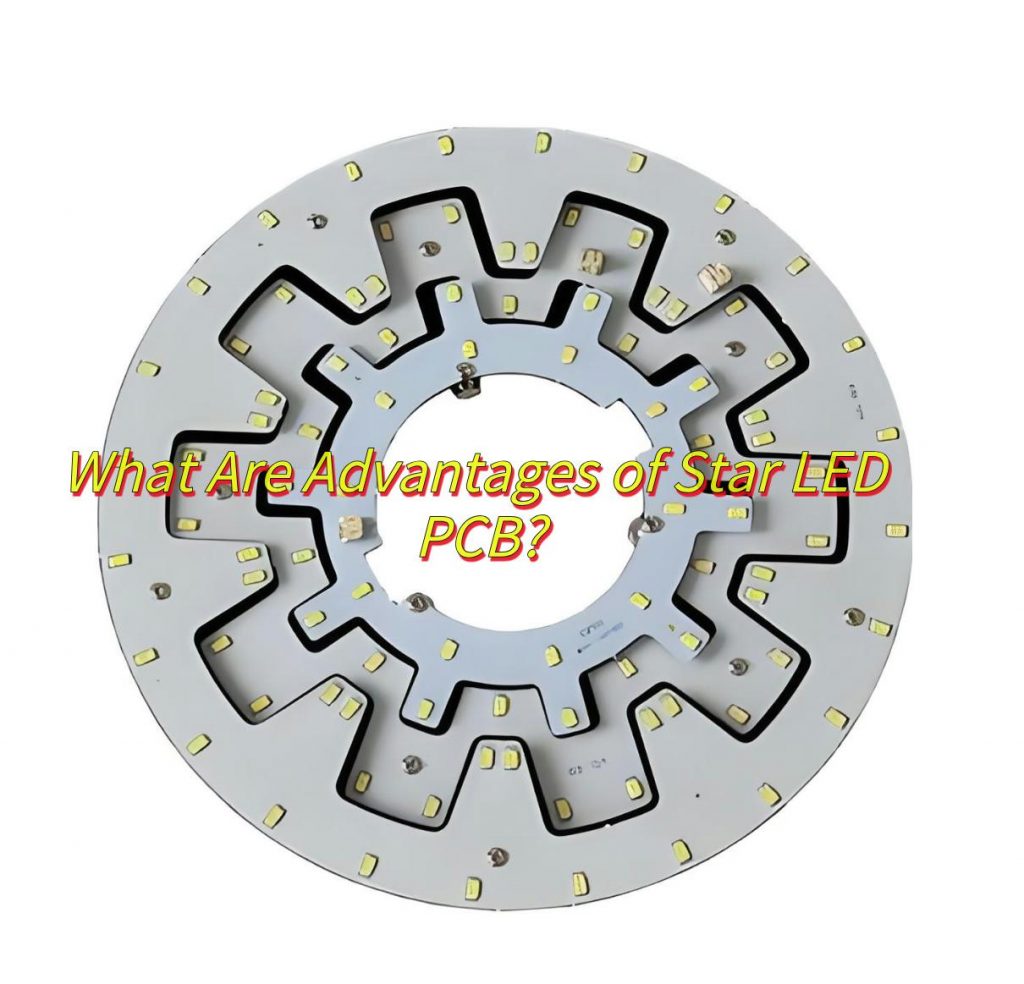
What Are Application of LED Star PCB? Â
LED Star PCB Applications:
- Decorative Lighting – Commercial spaces, art installations, residential accents
- Stage Lighting – Concert venues, theater productions, dynamic color effects
- Architectural Lighting – Building facades, landscape illumination, bridge lighting
- Industrial Lighting – Warehouses, factories, task lighting solutions
- Automotive Lighting – Custom vehicle lighting, interior/exterior car modifications
- Special Effects Equipment – Laser shows, holographic projections, interactive displays
- Smart Lighting Systems – Integrated IoT solutions, programmable lighting control
Why Star PCBs Work Best for Power LED Heat Dissipation?
Here are reasons why star PCBs work best for power LED heat dissipation:
- Radial arms disperse heat from center, eliminating hotspots.
- Extended copper traces maximize surface area for ambient cooling.
- Aluminum/copper bases (2-4 W/m·K) outperform FR4 in thermal transfer.
- Short thermal paths (<5°C/W) ensure stable temperatures under load.
- Thick copper (â„3 oz/ftÂČ) supports high-power applications.
- Compact/symmetrical design adapts to space-constrained or high-cooling systems.
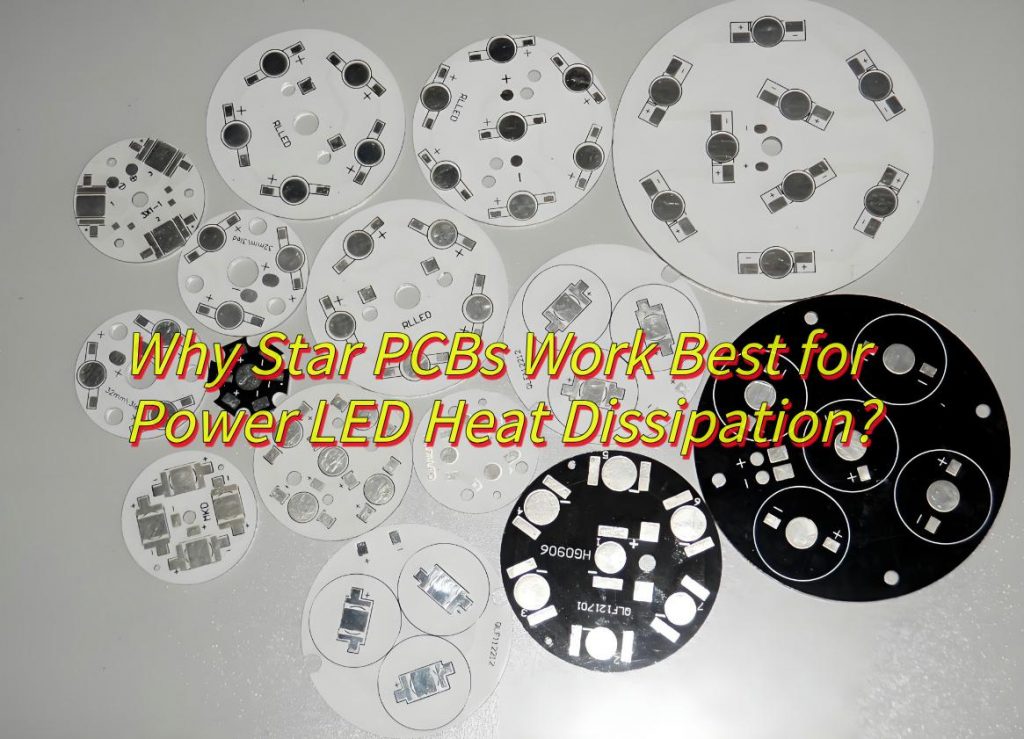
How to Choose a Reliable LED Star PCB Board Manufacturer?
This is how to choose a reliable LED star PCB board manufacturer:
- Verify Core Competencies – Check ISO/UL/CE certifications, factory scale, and SMT line capacity to ensure quality standards and production capability
- Evaluate Quality Systems – Assess IQC/IPQC/FQC processes and request sample testing (thermal cycling, vibration, aging) to validate reliability
- Analyze Supply Chain – Investigate component sourcing, MOQ policies, and lead times to ensure stable production and timely delivery
- Review Customization Track Record – Examine case studies of similar projects and R&D team expertise to confirm design flexibility
- Compare Total Cost Structure – Analyze pricing transparency, material specifications, and hidden costs while balancing MOQ requirements
- Assess Logistics & Support – Confirm export packaging compliance, freight partnerships, and after-sales policies (warranty/technical support)
- Evaluate Long-Term Viability – Investigate financial stability, cultural alignment, and sustainability practices for sustainable partnerships
- Check Risk Mitigation – Verify crisis response plans, insurance coverage, and alternative supply options to ensure business continuity
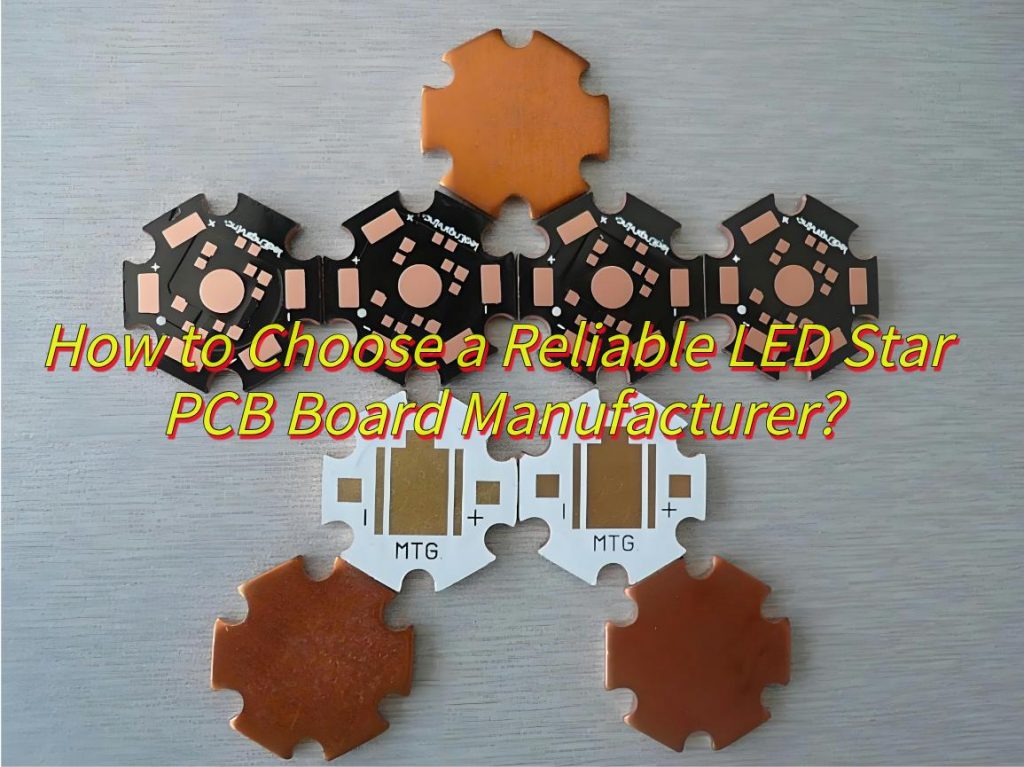
How to Reduce the Production Cost of LED Star PCB?
Here are some methods about how to reduce the production cost of Star LED PCB:
- Standardize Component Specifications-Unify LED packaging formats to minimize redundant layers and blind/buried via designs, reducing material waste and processing complexity.
- Cost-Effective Material Selection-Adopt high-performance FR4 substrates while optimizing copper foil thickness to balance thermal/electrical performance with material cost reliability.
- Streamlined Manufacturing Process-Utilize DFM (Design for Manufacturing) tools to validate layouts, eliminating precision alignment requirements and complex solder mask processes for improved yields and reduced costs.
- Automated Production & Stencil Optimization-Implement automated placement equipment to lower labor costs, paired with optimized stencil apertures that minimize solder paste waste.
- Centralized Procurement & Supplier Collaboration-Partner with manufacturers supporting small-batch prototyping and mass production, leveraging long-term agreements or BOM substitution strategies to reduce component expenses.
- Early-Stage Design Validation-Require suppliers to provide thermal distribution and signal integrity simulation reports to prevent costly rework in later stages.
- Modular Design for Maintainability-Implement replaceable sub-modules to reduce repair costs and extend product lifecycles.
- Dynamic Dimming Algorithm & Driver IC Optimization-Reduce LED counts or adopt cost-effective driver ICs, combining PWM compensation strategies to maintain performance-cost balance.
How to Achieve Multi-color Synchronous Control with RGB LED star PCB?
To achieve multi-color synchronous control with RGB LED star PCB:
- Use I2C driver chips (e.g., IS31FL3236A) combined with STM32F103 MCUâ, supporting 36-channel PWM control to achieve 256-level brightness mixing for 12 groups of RGB LED star PCBs.
- Wired synchronizationâ: Cascade driver chips via I2C/SPI buses with timing synchronization error <1ÎŒs; âWireless synchronizationâ: ESP32-C3 Mesh network synchronizes 100+ nodes with transmission delay <5ms.
- HSV-CIE1931 color space conversion algorithmâ ensures multi-board color difference <±3%; âDMA-driven real-time PWM duty cycle updatesâ eliminate cascaded brightness deviations.
- Symmetrical star-shaped wiring designâ: ±2mm wire length difference between LEDs and MCU to reduce phase mismatch; âLayered stack structureâ (thickness â€1.6mm) integrates LED arrays on top layer and driver circuits on the bottom.
- Logic analyzer verifies I2C clock skewâ (<50ns); âInfrared light meter validates brightness uniformityâ (<5% fluctuation).
Can LED Star PCB Dimensions be customized?
Yes, LED Star PCB dimensions can be fully customized (e.g., diameter 50-200mm). Best Technologyâ also supports color customization through RGB channel configuration, driver chip selection, and dynamic dimming algorithms. Material customization, size adjustments and color control (including multi-color synchronization) are tailored to meet specific application requirements, such as stage lighting or automotive ambient systems. If you want to get a quote for customized LED star PCB, please feel free to leave a message below this blog.