A PCB manufacturing factory is the heart of modern electronics, transforming design concepts into fully functional circuit boards. Every electronic device, from smartphones to industrial machines, relies on PCBs to operate efficiently. The demand for high-quality circuit boards is growing rapidly, making it essential to understand how these factories work.
As a well-equipped PCB manufacturing factory, Best Technology follows precise steps, from raw material selection to final testing, ensuring that each board meets industry standards. Advanced machinery and strict quality control measures give us an access to provide reliable printed circuit boards to global market. Our PCB manufacturing facility is located in Shenzhen, and we would be delighted to welcome you for a visit to discuss your PCB needs. If any questions, just feel free to let us know via sales@bestpcbs.com.
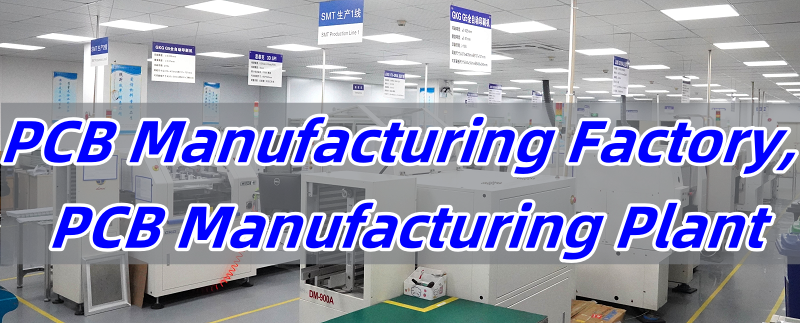
What Does a PCB Manufacturing Factory Do?
A PCB manufacturing factory is responsible for turning design files into functional circuit boards. It handles multiple stages, including material selection, layering, drilling, plating, and final testing. Each step must meet strict accuracy and reliability standards. Factories use automation to enhance efficiency and minimize errors, ensuring customers receive high-performance PCBs.
The process begins with designing the PCB layout using specialized software. Once the design is finalized, the factory selects the appropriate materials based on the application’s requirements. The manufacturing process involves layering copper sheets, etching circuits, and adding protective coatings. After production, PCBs undergo multiple testing phases to detect any defects before shipping to customers.
What Advanced Technologies Are Used in a PCB Fabrication Factory?
A PCB fabrication factory relies on cutting-edge machinery to produce precise and durable circuit boards. Laser drilling, automatic optical inspection (AOI), and advanced plating techniques improve board quality. Many factories use high-speed pick-and-place machines for component assembly. These technologies help achieve finer traces, better signal integrity, and improved thermal management, essential for modern electronic devices.
To improve efficiency, factories also implement AI-driven quality checks. These systems detect defects faster than manual inspections, reducing errors and improving production speed. Innovations like additive manufacturing and 3D printing are also making their way into PCB fabrication, enabling faster PCB prototyping and lower material waste.
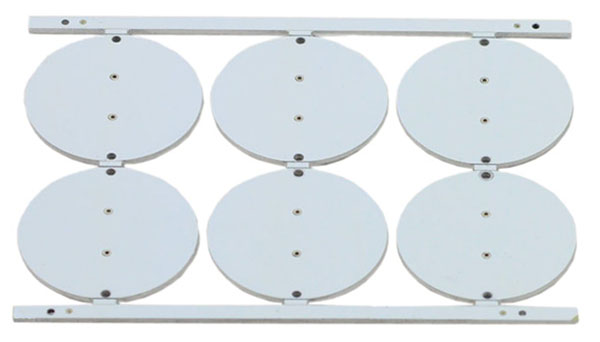
How Does a PCB Manufacturing Factory Handle Custom Orders?
Customization is a key service in a PCB manufacturing factory. Customers often need boards with unique layouts, special materials, or specific layer counts. Factories use flexible production lines to adapt to different designs. Engineers review files for manufacturability, ensuring compatibility with production capabilities. Custom prototypes go through rigorous testing before full-scale production begins, reducing errors and improving efficiency.
Customers can specify various parameters, including board thickness, copper weight, and surface finishes. Advanced factories also offer quick-turn prototyping services, allowing businesses to test their designs before mass production. Best Technology specialized in FR4 PCBs, metal core PCBs, ceramic PCBs, and PCB assembly. All of our PCBs can be customized according to your specific needs. Partnering with Best Technology ensures a seamless customization process with minimal delays.
How Does a PCB Manufacturing Plant Maintain Quality Control?
A PCB manufacturing plant follows strict quality control measures at every stage. Automated testing systems check for defects in circuitry, while X-ray inspection ensures proper solder connections. Factories also conduct thermal stress tests to evaluate board durability. Well-established factories comply with international standards, preventing failures and ensuring reliable performance in real-world applications.
One of the most important aspects of quality control is electrical testing. Flying probe testers and in-circuit testers verify that each PCB functions as intended. Additionally, manufacturers perform micro-section analysis to examine internal layers, ensuring there are no hidden defects. By maintaining high-quality standards, factories reduce failure rates and increase customer satisfaction.
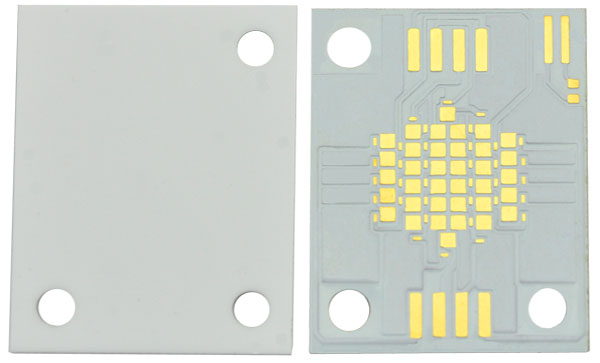
How Do PCB Making Factories Ensure Fast Turnaround?
Speed matters in a PCB making factory. To shorten production time, factories streamline workflows and use automated processes. Quick-turn prototyping services allow customers to receive samples in a few days. Efficient logistics and supply chain management also help reduce lead times. With optimized operations, factories can deliver large production runs without delays.
Factories implement lean manufacturing techniques to eliminate bottlenecks in production. Real-time tracking systems help monitor progress, ensuring orders stay on schedule. Best Technology is implementing 2-3 weeks delivery time for our customers. We have rich experience in handling standard PCB and non-standard PCB projects. Any new inquiry will be replied within 12 hours by our professional engineers. And we believe quality first, quantity second. We are commitment to provide the fast turnaround PCB service without compromising the quality.
What Certifications Should a PCB Manufacturing Company Have?
A trusted PCB manufacturing company holds industry certifications that prove its commitment to quality. Best Technology possessed certifications like ISO 9001, ISO 13485, AS9100D, IATF16949 and IPC standards ensure that manufacturing processes meet global requirements. Besides, all PCBs in Best Technology are in compliance with RoHS and UL standards guarantees that products are environmentally friendly and safe for use in various industries.
To sum up, manufacturers that produce automotive PCBs must comply with IATF 16949, which sets strict quality standards for vehicle electronics. Aerospace and defense industries require AS9100 certification. Choosing a factory with the right certifications ensures that the final product meets safety, reliability, and environmental standards.
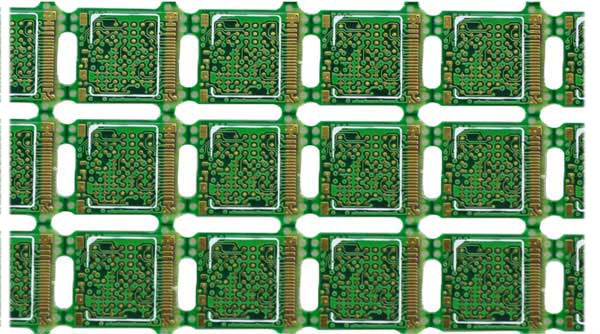
How to Choose the Best PCB Manufacturing Factory for Your Needs?
Finding the right PCB manufacturing factory depends on factors such as expertise, technology, and production capacity. Consider a factory’s track record, customer reviews, and ability to handle complex designs. Check if they offer prototyping services, fast turnaround, and consistent quality. Partnering with an experienced manufacturer ensures a smooth production process and high-quality PCBs.
Before making a decision, request samples or visit the PCB manufacturing factory if possible. Discuss PCB project requirements with the PCB factory’s engineers to ensure they can meet your PCB specifications. A reliable PCB manufacturer will provide transparent pricing, technical support, and flexible solutions to match your needs.
Best Technology is a direct PCB manufacturing factory, we support PCB manufacturing and PCB assembly. In our SMT factory in Shenzhen, there are 2 YAMAHA production lines and 2 JUKI production lines, a totally of 4 production lines. In Vietnam, Best Technology also has a SMT factory. If you have any SMT needs, just don’t hesitate to provide our team with a BOM list, pick and place file, and silkscreen diagram. Best Technology provides you with on-time and quick turn-out service.
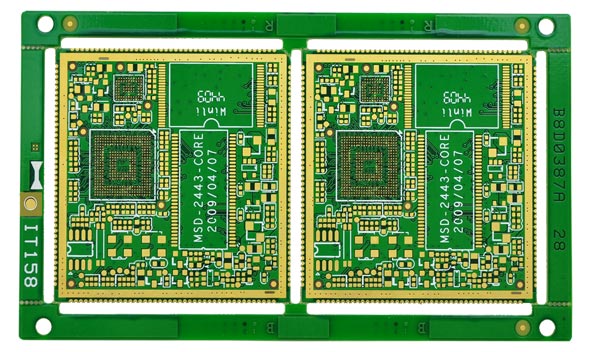
In conclusion, a PCB manufacturing factory is the backbone of the electronics industry, turning concepts into reliable circuit boards. With advanced technologies, strict quality control, and fast production, these factories help businesses bring innovative products to market. Choosing the right partner ensures efficiency, quality, and long-term success. Whether you need standard boards or complex custom designs, Best Technology could provide professional PCB manufacturing services for you. Reach out to us via sales@bestpcbs.com for more information.