With the rapid development of ceramic industry, Ceramic Circuit Board is widely used in semi-conductors and electronic packages fields because it provides an excellent electric conductivity, low thermal expansion and good insulation properties over standard FR4 based PCBs. As you can see from our website: https://www.bestpcbs.com/products/ceramic-substrate.htm, there are various kinds of ceramic substrate materials in the market, different materials have different functions and properties. Here we illustrated the different kinds of materials in the market as below for you to choose which one is ideal for your designs when needs come out.
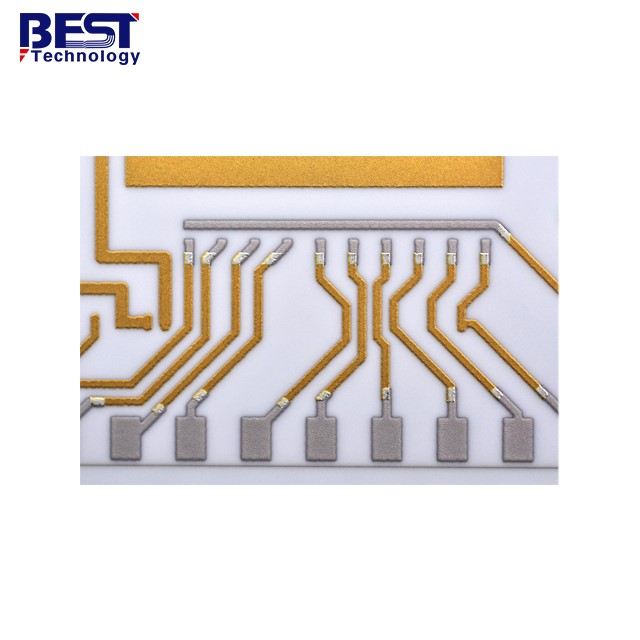
Common ceramic substrate materials
Nowadays, the most commonly material in the market is oxidation material, it always used in automobile products as its wear resistance and good strength.
Besides, there are some nitrides and silicious can be used in high power products.
For a quick look, here I listed as following:
- Alumina Oxide (Al2O3)
- Alumina Nitride (ALN)
- Beryllium Oxide (BeO)
- Silicon Nitride (Si3N4)
- Zirconium Oxide (ZrO2)
- Silicon Carbide (SiC)
Characteristics of different substrate materials
Alumina Oxide (Al2O3)
Alumina substrate characterize as a pure white substrate and the most commonly used ceramic substrate material in the electronics industry because of its high strength and chemical stability compared to most other oxide ceramics in terms of mechanical, thermal and electrical properties, and the richful source of raw materials is suitable for a variety of technical manufacturing and different shapes. The most commonly used Alumina Oxide are 96% alumina and 99.6% alumina.
- 96% alumina can be used to fabricate Thick Film Ceramic Circuits as it has excellent electrical insulation, mechanical strength, good thermal conductivity, chemical durability and dimensional stability. The surface roughness is generally 0.2~0.6μm, and the maximum using temperature of the substrate can reach 1600℃
- 99.6% alumina is the mainstay of most Thin-film electronic substrate applications, commonly used in circuit generation for sputtering, evaporation and chemical vapor deposition of metals. 99.6% alumina has higher purity, smaller grain size, and excellent surface smoothness than 96% alumina (the surface roughness is generally 0.08~0.1μm), and it can withstand maximum 1700°C temperature when applied in applications.
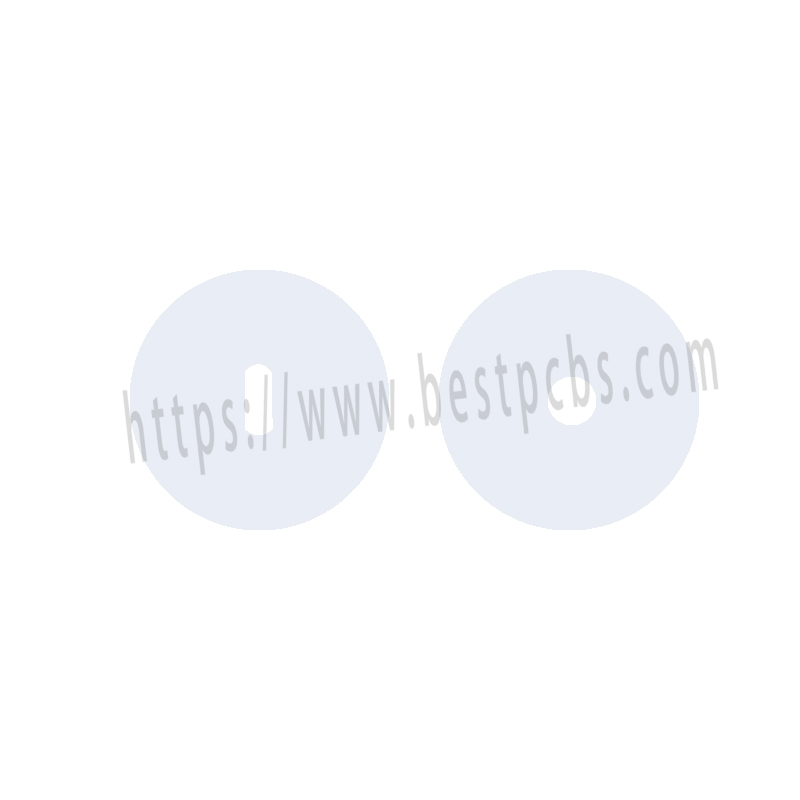
Alumina Nitride (ALN)
Currently, Alumina Nitride won the high attention of the public by means of two key excellent properties: one is high thermal conductivity. Alumina nitride offers a big increasing in thermal conductivity (170Wm.k), which is approximately 100-200 times than FR4 substrates did, while alumina oxide only offers 24W/m.K.
Another characteristic is silicon-matched expansion coefficient of 4.7ppm/°C 20~300°C, this makes it suitable for used in extremely harsh environments likely in high temperatures. The disadvantage is that even an extra thin oxidation will affect the thermal conductivity. Only by strictly controlling the material and process, can aluminum nitride substrate be produced with good consistency. That’s why the alumina nitride is expansive than alumina oxide.
By visually, alumina nitride has an off-white color, that give us a chance to distinguish it with alumina oxide easily.
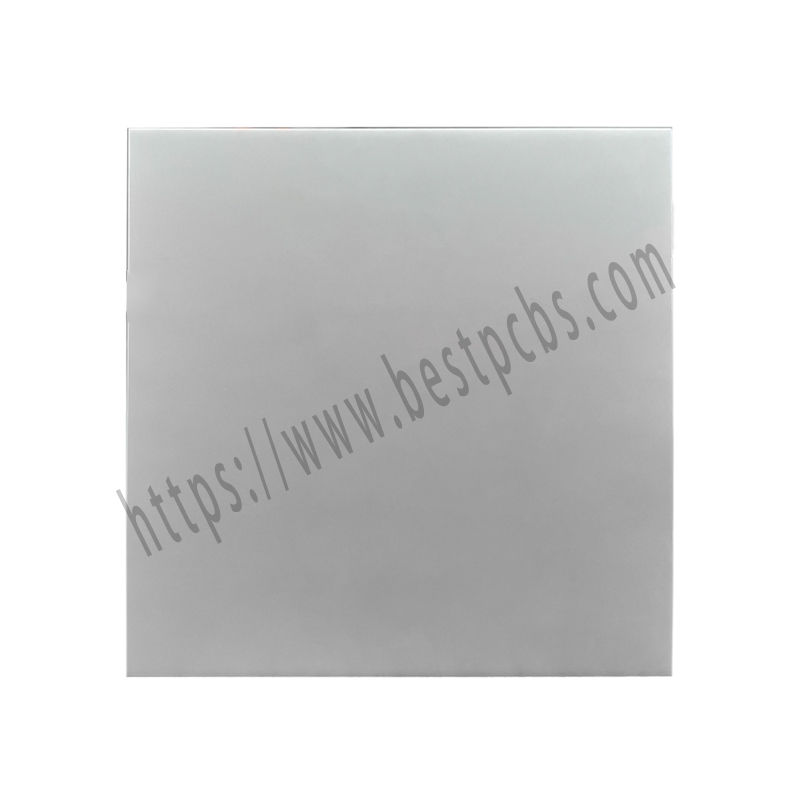
Beryllium Oxide (BeO)
Beryllium Oxide has a high thermal conductivity than alumina, therefore, it almost used where high thermal conductivity required. But when the temperature exceeds 300°C, it drops quickly. It is not as widely used as alumina oxide or aluminum nitride, the most important thing is that its toxicity limits its development.
Silicon Nitride (Si3N4)
Silicon Nitride is a material with high fracture toughness and strong heat resistance are often used as alternative materials for modules in recent years. With strong mechanical, high temperature resistance, corrosion resistance and wear resistance, it is widely used in automotive shock absorber, engine, especially automotive IGBT products, as well as traffic track, aerospace and other fields.
Zirconium Oxide (ZrO2)
Zirconium Oxide is popular as its exceptional strength, toughness, biocompatibility, high fatigue and wear resistance (15times of alumina oxide) render it optimal for dental applications.
Silicon Carbide (SiC)
The essence of silicon carbide ceramic substrate is a silicon material, which determines its high current density characteristics due to its superior thermal conductivity.
In the meantime, the higher band gap width determines the higher breakdown field and higher operating temperature of silicon carbide (SiC) ceramic circuit board.
The core advantages of silicon carbide are high temperature resistance, high pressure resistance, wear resistance, low loss and high frequency work. Therefore, it is used for products with high heat dissipation, high thermal conductivity, large current, large voltage and high frequency operation.
Send us inquiry for fabrication
At present, you should have a brief acknowledge about different ceramic substrate materials and their characteristics, and you should be able to decide which materials is most suitable for you. If you still have some concerns or different opinions about substrate for Ceramic pcb, welcome to contact us, Best Tech will offer you free advice and technical support for ceramic substrate choice.
Tags: ceramic PCB