Currently, with the rapid development of the digital era, the demands and requirements for electronics have increased significantly. Many double-sided and multi-layer boards have high density and power, making it difficult to dissipate heat efficiently. Conventional printed circuit board substrates such as FR4 and CEM3 are poor thermal conductors with interlayer insulation, the heat can’t transfer out, which leading to high-temperature failure of electronic components and devices. So, engineers and researchers are aiming to find high thermal conductivity PCBs to solve such problems, and metal core PCB and ceramic PCB stand out at this time.
Metal core PCB is a type of PCB that made by metal alloy material as the base core, commonly are aluminum core or copper core, rarely is iron PCB. They are popular because of its good heat dissipation properties and good mechanical strength.
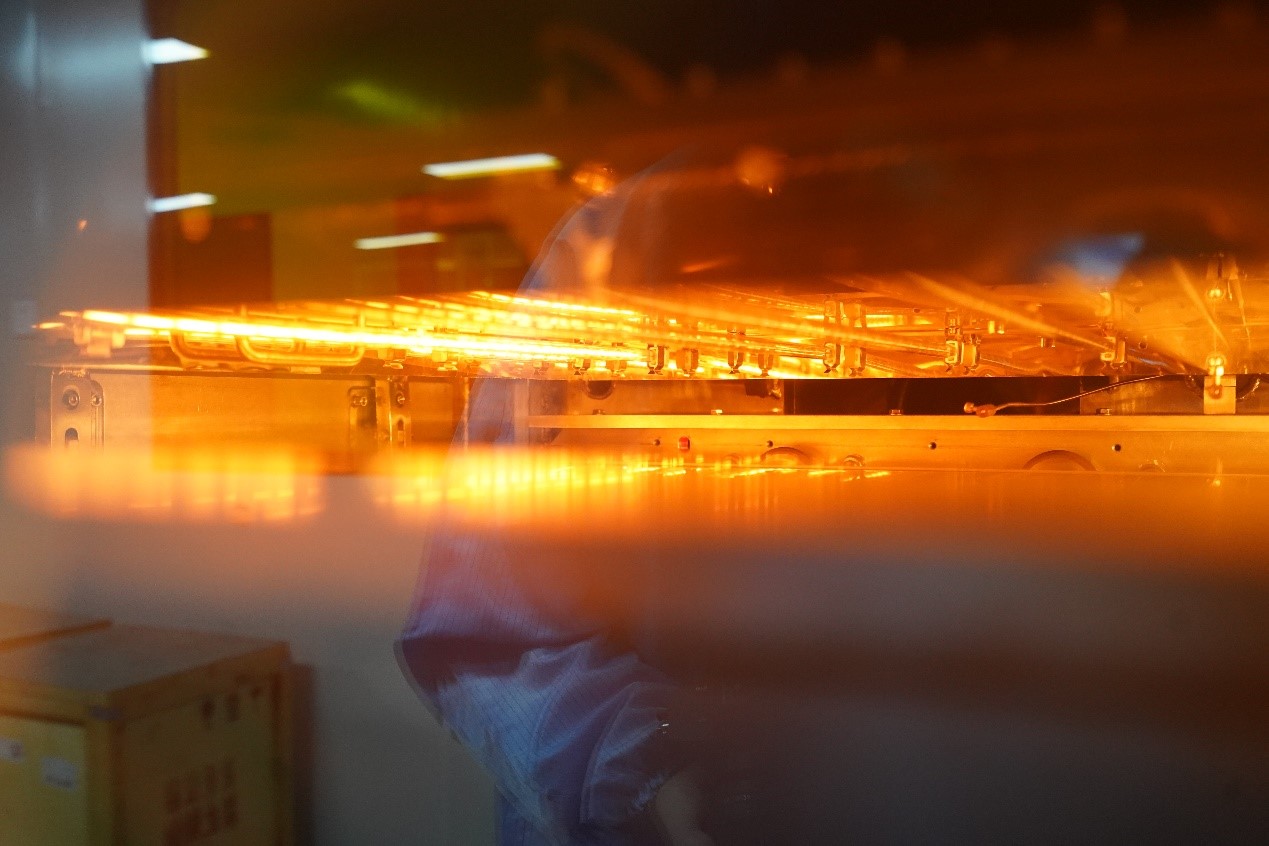
What is Aluminum PCB and Why Use It?
Aluminum substrate is a low-alloyed Al-Mg-Si series high-ductility alloy sheet. It exhibits excellent thermal conductivity, electrical insulation properties, and mechanical machinability. Compared to traditional FR-4, with the same thickness and line width, aluminum substrate can carry higher currents, withstanding voltages up to 4500V. Its thermal conductivity coefficient exceeds 2.0.
A normal single side (1L) aluminum core PCB consists of three layers, aluminum base, dielectric layer and copper trace layer. Generally speaking, 1L aluminum PCB is always used for LED lighting, high current LED, spotlight, etc. So it also called LED PCB. For high-end applications, there are also designs for double-sided boards, structured as circuit layer, insulation layer, aluminum base, insulation layer, and circuit layer. In rare cases, multi-layer boards are used, which can be composed of multi-layer FR4 boards laminated to insulation layers and aluminum base.
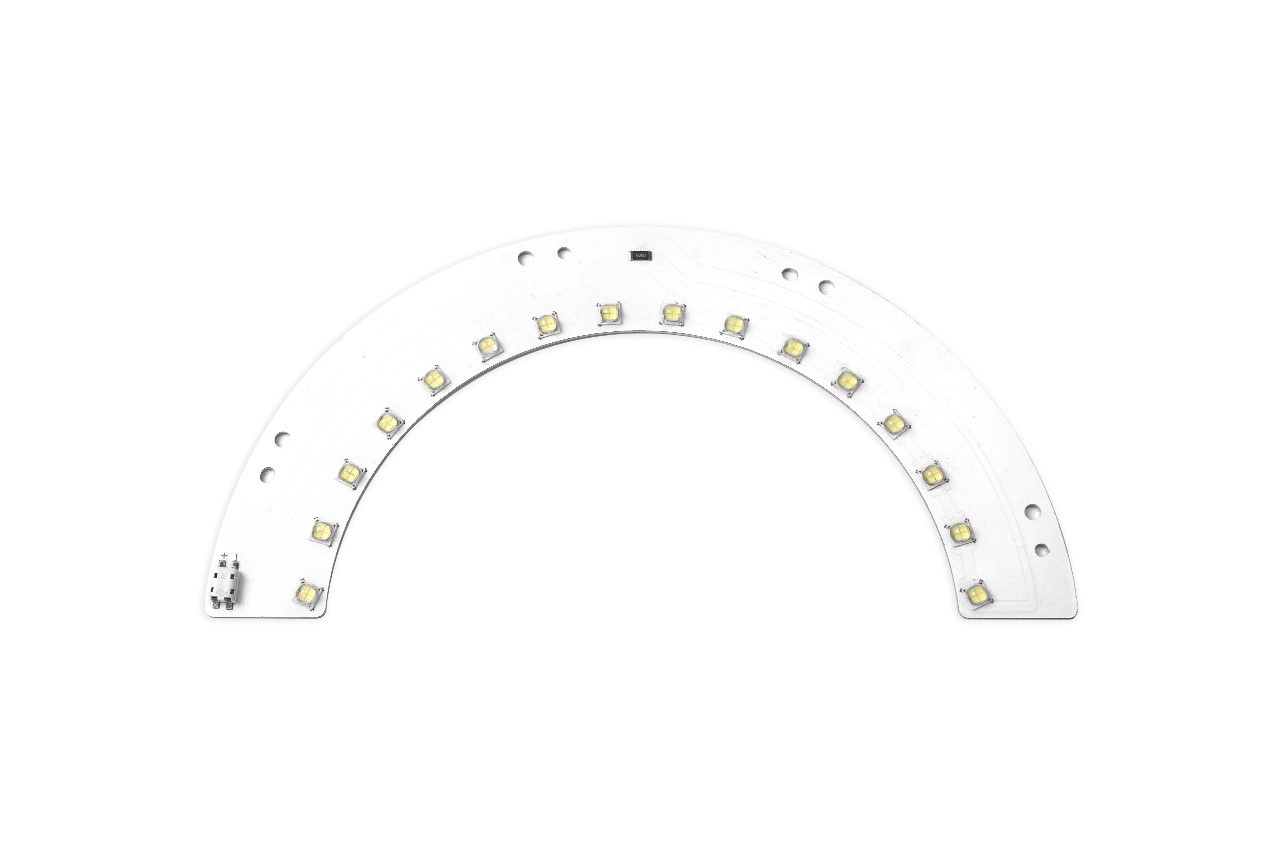
The thermal conductivity of aluminum core is range from 1-3W/m.k, the higher conductivity, the better heat dissipation. However, not all the projects is suitable for higher conductivity, it should depend on the specific requirements, such as mechanical strengthen, corrosivity. Nowadays, Best Technology used 6061, 5052, 1060 aluminum alloy as the metal core, others also available if customers have requirements.
How Does Copper Core PCB Works?
Copper substrate is the most expensive type among metal substrates, offering significantly better thermal conductivity compared to aluminum and iron substrates. It is suitable for high-frequency circuits, regions with large temperature variations, and precision communication equipment for heat dissipation purposes, as well as in the construction and decoration industries.
The copper PCB’s circuit layer requires a significant current-carrying capacity, thus necessitating the use of thicker copper foils, typically ranging from 35μm to 280μm in thickness. The thermal insulation layer is the core technology of the copper substrate, composed of aluminum oxide and silicon powder as the main thermal conductive components, filled with a polymer of epoxy resin. It exhibits low thermal resistance (0.15), excellent viscoelastic properties, and possesses the ability to resist thermal aging, withstanding mechanical and thermal stresses.
The metal base layer of the copper substrate serves as its supporting component, requiring high thermal conductivity. It is typically made of copper foil, though copper plate can also be used (with copper PCB offering better thermal conductivity, around 1-400W/m.k). These substrates are suitable for conventional mechanical processing methods such as drilling, punching, and cutting.
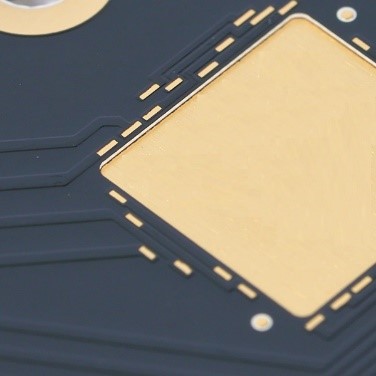
What Are Differences Between Copper and Aluminum PCB?
Though both copper and aluminum are metal core PCB, they still have some differences in characteristic and manufacturing. Knowing their differentiation can help you to understanding and making correct decision in material selection.
- Material
Copper has excellent electrical conductivity and mechanical strength, so copper PCB is well-suit for high frequency circuits and high-power electronic equipment. While aluminum is slightly inferior to the copper base, so it is a good choice of low-power devices.
- Cost
Compared with copper, aluminum PCB has much advantages in cost, so if you have limited budget and require to use for low-power equipment such as LED lights, aluminum is the better one.
- Manufacturing
Due to copper has great hardness and good strengthen, it requires for special technical and complex processes, for example: chemical etching, electro-plating. However, the lightweight of aluminum makes it easy in manufacturing. In addition, PTH (plated through holes) can be created on copper PCBs, but not on aluminum ones.
- Physical Property
The difference in elastic modulus between copper and aluminum is significant, resulting in less warping and expansion/contraction in copper substrates compared to aluminum substrates.
- Application
Aluminum PCB is lighter than copper substrate, the material cost is lower, often used in daily LED lights or electronic equipment. Because of its strong thermal conductivity and better electrical conductivity, copper substrate is usually used in high-speed circuits and high energy circuits. In addition, copper substrates are also widely used in areas requiring high heat transfer and heat dissipation performance, such as power amplifiers, power supplies, power tools, automotive engine controllers and solar inverters.
What is Ceramic PCB? And Its Thermal Conductivity?
Ceramic PCB is one of the high thermal conductivity PCBs in this industry. They have good high-frequency properties and electrical properties, and have high thermal conductivity, chemical stability and excellent thermal stability of organic substrates without. It is a new generation of large-scale integrated circuits and power electronics module ideal packaging materials. The thermal conductivity of the ceramic substrate can reach about 220W/ M.K according to the preparation method and the material formula. Theoretically speaking, the thermal conductivity of ceramic circuit made by alumina is 24-28W/m.k, AlN is 150-240W/m.k and for BeO is 22-250W/m.k.
Ceramic PCB can be divided into various types of PCB according to its different PCB manufacturing process, they are thick film, thin film PCB, DPC, DBC, HTCC and LTCC ceramic circuit board. Different types of PCB made in different temperature and uses different materials, this means they have different chemistry and physical properties. So you should take them into consideration when designing a ceramic PCB for your device.
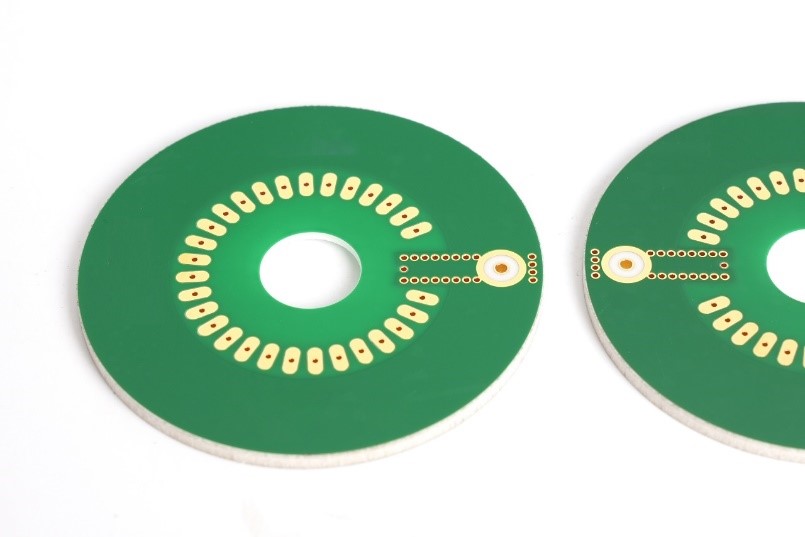
A Reliable PCB Supplier in China – Best Technology
Whatever you choose metal core PCB or ceramic PCB, a reliable supplier is necessary and needed. Best Technology has extensive manufacturing experience in PCB and we are very confident that we can serve you the best service and high-quality product. With rich experience and strong R&D team, we know how to provide you the best solution and evaluate the design files for you. We have professional DFM (Design For Manufacturing) process to identify the mistakes or inappropriate layout in design. Welcome to contact with us to discuss your PCB projects.