Direct Plating Copper (DPC) is a ceramic circuit board developed on the basis of ceramic film processing. Aluminum nitride/alumina ceramic is used as the substrate of the circuit, and the composite metal layer on the surface of the substrate is sputtered, and the circuit is formed by electroplating and lithography. Its basic processes are:
- Incoming Quality Control (IQC)
The process begins with the inspection of raw materials to ensure they meet strict quality standards. This step involves checking ceramic substrates for physical defects such as cracks, chips, or surface irregularities, and verifying material properties like thermal conductivity and dielectric strength. Advanced equipment such as microscopes and X-ray fluorescence (XRF) analyzers are used for thorough inspection, ensuring only the best materials proceed to the next stage.
- Laser Drilling
Before laser drilling, a water-soluble, food-grade substrate pigment is brushed onto the ceramic substrate to reduce reflectivity and enhance laser drilling effectiveness. After drying in an oven, a laser drilling machine is used to drill through the substrate, creating pathways for connections between the upper and lower surfaces. Depending on the ceramic material, different laser wavelengths such as infrared, green light, ultraviolet, or CO2 are used to burn away the material with each laser pulse.
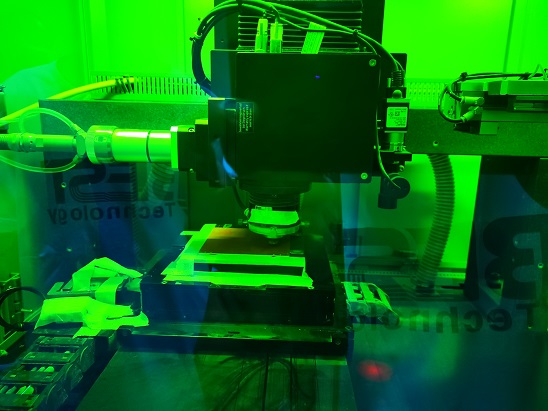
- Laser Marking
Laser marking involves using a laser marking machine to engrave product QR codes onto the ceramic substrate. This step ensures precise and permanent identification marks on the PCB.
- Ultrasonic Cleaning
After laser drilling and marking, the substrates are cleaned to remove any attached particles or residues. This involves coarse and fine debris removal using ultrasonic cleaning, followed by water washing to eliminate any remaining particles. The cleaned substrates undergo micro-etching to roughen the surface, enhancing the effectiveness of subsequent magnetron sputtering, and are then dried to remove surface moisture.
- Magnetron Sputtering
In the magnetron sputtering process, a high-vacuum chamber is used to ionize argon gas, producing an ion stream that bombards a target cathode. This causes atoms of the target material to be ejected and deposited as a thin film on the ceramic substrate. Pre-sputtering treatments such as dust removal, degreasing, and slow pulling are conducted to ensure optimal results.
- Chemical Copper Plating
Chemical copper plating thickens the copper layer, improving the conductivity of the vias and ensuring better adhesion with the sputtered copper layer. This catalytic redox reaction involves pre-treatment steps like degreasing, micro-etching, pre-immersion, activation, and acceleration to ensure proper copper deposition.
- Full-Panel Electroplating
Full-panel electroplating increases the thickness of the copper layer. This involves processes such as degreasing, micro-etching, acid washing, copper plating, and stripping excess copper from the fixtures. The copper plating uses copper balls as anodes and an electrolyte solution of CuSO4 and H2SO4, with the primary reaction being Cu2+ + 2e- → Cu.
- Grinding, Laminating, Exposure, and Developing
Post electroplating, the copper layer is prepared for patterning. This includes acid washing to remove oxides, grinding to roughen and clean the surface, laminating with a photoresist dry film, UV exposure through a photomask to create the desired pattern, and developing to dissolve unexposed areas, leaving behind the patterned photoresist.
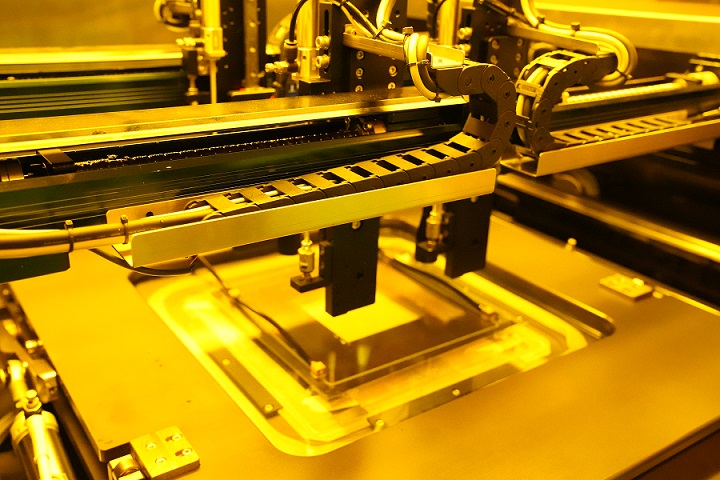
- Pattern Plating (Electroplating Copper)
The exposed and developed areas of the substrate where the circuit pattern is defined undergo further copper electroplating to thicken the circuit traces.
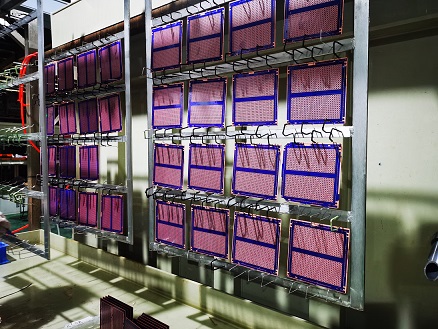
- Etching and Stripping
Unwanted copper and dry film are removed through etching, stripping away excess copper deposited in previous steps. This includes rough grinding, film stripping, copper etching, and titanium etching, ensuring only the desired circuit pattern remains.
- Annealing
The ceramic boards are annealed in a furnace to relieve stresses introduced during electroplating, enhancing the ductility and toughness of the copper layer and ensuring dense copper grain packing.
- Belt Grinding
Post-annealing, the substrate surface may have an oxide layer and rough texture. Belt grinding is used to remove these oxides and smoothen the surface, ensuring the quality of subsequent gold or silver surface treatments.
- Flying Probe Testing
High-speed flying probe testers check for continuity and shorts in the vias and circuit traces, ensuring electrical integrity.
- Sandblasting Before Solder Mask
Prior to solder mask application, the substrate undergoes sandblasting to roughen and clean the surface, removing oxides and contaminants. This includes acid washing, sandblasting, and micro-etching.
- Solder Mask Printing
Solder mask is printed on areas of the PCB that do not require soldering, protecting the circuits during soldering and assembly. Screen printing applies solder mask ink, which is then UV-cured and developed to remove unexposed areas.
- Sandblasting After Solder Mask
After solder mask application, exposed areas that need surface treatments undergo sandblasting to roughen the surface and remove oxides, preparing for gold or silver plating.
- Surface Treatment
Surface treatments like electroless or electrolytic plating of gold, silver, or other metals are applied to the solder pads, enhancing solderability and preventing oxidation.
- Laser Cutting
Laser cutting equipment precisely cuts the finished PCBs from the manufacturing panel, ensuring accurate dimensions and clean edges.
- Testing
Various testing equipment, including thickness gauges, Automated Optical Inspection (AOI) machines, and ultrasonic scanning microscopes, are used to inspect the PCBs’ performance and appearance, ensuring they meet quality standards.
- Packaging and Shipping
Finally, the PCBs are vacuum-packed using packaging machines to protect them during transport. They are then stored and shipped to customers, ensuring they arrive in perfect condition.
Above is the all the processes of DPC muanufacturing. If you are interested in process of other PCBs, welcome to contact us.