FR4 is a commonly used material in the printed circuit boards (PCBs) manufacturing. If you’re in the electronics field, you’ve likely heard of it. It is the footstone of a circuit board, provides good mechanical strengthen and electrical insulation properties. Today, we will share informational about FR4 material, its types, advantages and alternatives. Keep reading if you are interested in.
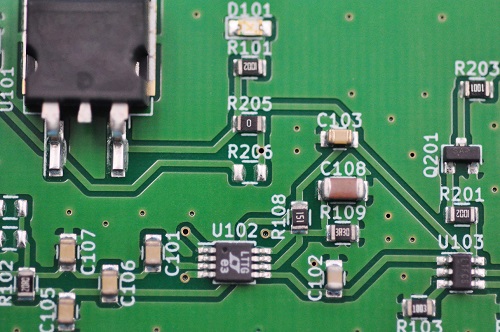
What does FR4 stand for?
FR4 stands for “Flame Retardant 4”, also called FR-4 Epoxy Glass Cloth by PCB manufacturers. It is not a material name, but a material grade, so there are many types of FR-4 grade materials used in general circuit boards. But most are composites made with so-called Tera-Function epoxy resins plus fillers and glass fibers. FR4 is made from woven glass-reinforced epoxy resin. The typical composition of FR4 includes approximately 60% glass fabric and 40% epoxy resin by weight.
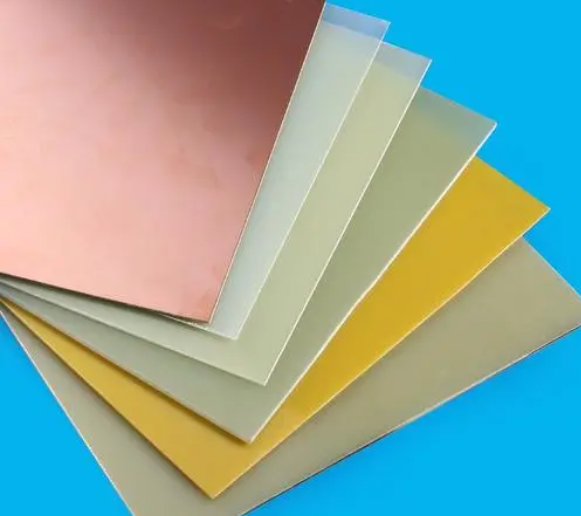
This composite material is known for its high mechanical strength and flame-retardant properties. The “4” in FR4 signifies the level of flame retardancy. It means the material is resistant to catching fire, which is critical in preventing electrical fires in electronic devices.
What are the classifications of FR4 materials?
FR4 materials are classified based on various properties and specifications to cater to different applications and requirements. These classifications help in selecting the right type of FR4 material for specific PCB needs. Here are the primary classifications of FR4 materials:
1. Standard FR4
Standard FR4 is the most commonly used classification. It offers a good balance of electrical insulation, mechanical strength, flame retardancy, and cost-effectiveness. Standard FR4 materials have a glass transition temperature (Tg) typically around 130°C to 140°C. They are suitable for general-purpose PCBs used in consumer electronics, industrial controls, and telecommunications equipment.
2. High Tg FR4
High Tg FR4 materials are designed for applications requiring higher thermal performance. These materials have a higher glass transition temperature, usually above 170°C. High Tg FR4 is used in applications where the PCB is exposed to higher temperatures, such as automotive electronics, aerospace, and high-power devices. The increased Tg provides better stability and performance at elevated temperatures. This is the high Tg FR4 PCB that we made before.
3. Low Dk FR4
Low Dk (Dielectric Constant) FR4 materials are used in high-frequency applications where signal integrity is crucial. So, we called it as “High-frequency FR4”. These materials have a lower dielectric constant, which reduces signal loss and improves signal transmission. Low Dk FR4 is often used in RF and microwave circuits, where maintaining signal integrity is essential.
4. High CTI FR4
High CTI (Comparative Tracking Index) FR4 materials have an improved resistance to electrical tracking. These materials are used in applications where the PCB is exposed to high voltages and harsh environments. High CTI FR4 provides better insulation and reduces the risk of electrical failure due to tracking.
5. Halogen-Free FR4
Halogen-free FR4 materials are designed to meet environmental and safety requirements by eliminating halogens. Which can be harmful if released during PCB manufacturing or disposal. These materials are used in applications where reducing environmental impact is a priority. Halogen-free FR4 offers similar performance to standard FR4 but without the use of halogenated flame retardants.
Benefits of using FR4 as PCB material
- Excellent Electrical Insulation
- High Mechanical Strength
- Flame Retardancy
- Moisture Resistance
- Cost-Effectiveness
- Thermal Stability
- Ease of Fabrication
Properties of FR4 material
Property | Parameter |
Vertical flexural strength | Normal State: E-1/150, 150±5℃≥340Mpa |
Parallel layer impact strength | ≥230KJ/m |
Insulation resistance after water immersion (d-24/23) | ≥5.0×108Ω |
Vertical electrical strength | ≥14.2MV/m |
Parallel layer breakdown | ≥40KV |
Relative Dielectric Constant (50hz) | ≤5.5 |
Relative Dielectric Constant (1mhz) | ≤5.5 |
Dielectric Loss Factor (50hz) | ≤0.04 |
Dielectric Loss Factor (1mhz) | ≤0.04 |
Water Absorption (D-24/23, 1.6mm Thickness) | ≤19mg |
Density | 1.70-1.90g/cm³ |
Flammability | FV0 |
What is the Difference Between IMS and FR4 PCB?
IMS (Insulated Metal Substrate) and FR4 PCBs serve different purposes. IMS PCBs are designed for applications requiring efficient heat dissipation. They have a metal base layer that helps manage heat more effectively than FR4. This makes IMS ideal for high-power applications like LED lighting.
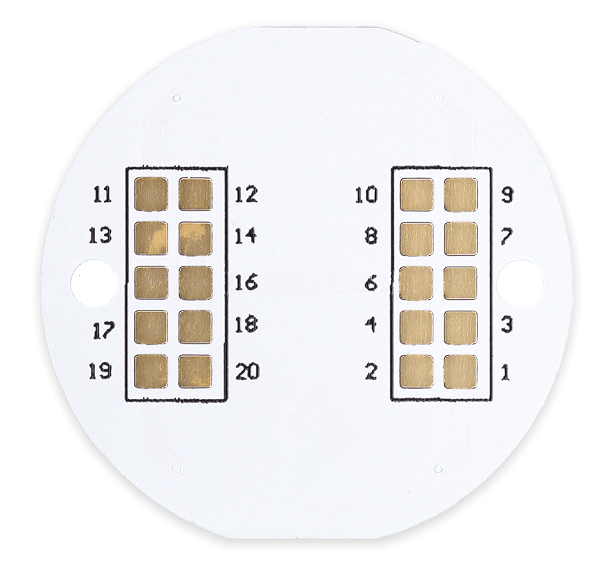
On the other hand, FR4 PCBs are used in general electronic applications due to their balance of performance and cost. While IMS excels in thermal management, FR4 is preferred for its electrical properties and versatility.
What is the Cost of FR4 PCB Per Square Inch?
The cost of an FR4 PCB can vary based on several factors. These include the board’s thickness, the number of layers, and the complexity of the design. On average, the cost per square inch of FR4 PCB ranges from $0.10 to $0.50. However, this is a rough estimate. For a precise quote, it’s best to contact PCB manufacturers with your specific requirements. If you are searching for a PCB supplier, Best Technology is here to waiting for you.
Why is Rogers Better Than FR4 Material?
Rogers material is often considered superior to FR4 in high-frequency applications. Here are some key reasons why Rogers might be chosen over FR4.
- Lower Dielectric Loss
- Higher Thermal Conductivity
- Improved Dimensional Stability
- Consistent Dielectric Constant
- Superior Performance in High-Frequency Applications
- Compliance with Stringent Industry Standards
What Material is Similar to FR4?
Several materials are similar to FR4 and can be used as alternatives. One such material is CEM-1, which is also a composite material made from epoxy and fiberglass. It offers good mechanical strength and electrical properties but is less flame retardant than FR4.
Another alternative is polyimide, known for its excellent thermal stability and flexibility. It is often used in applications requiring high-temperature resistance. However, polyimide is more expensive than FR4. For specific applications, materials like PTFE (Teflon) can also be considered, especially in high-frequency applications.
FAQs
1. Can FR4 be used in high-temperature applications?
FR4 can withstand moderate temperatures, but for high-temperature applications, materials like polyimide are preferred.
2. Is FR4 environmentally friendly?
FR4 is not biodegradable but can be recycled to some extent. Proper disposal and recycling methods should be followed.
3. How does the thickness of FR4 affect PCB performance?
The thickness of FR4 can impact the board’s mechanical strength and thermal dissipation. Thicker boards offer more durability but may also increase the cost.
4. Are there any disadvantages to using FR4?
FR4 has limitations in high-frequency and high-temperature applications. It is also less effective in thermal management compared to materials like IMS.
5. Can FR4 PCBs be used in flexible circuits?
FR4 is rigid and not suitable for flexible circuits. For flexible applications, materials like polyimide are used. But recently, Best Technology developed a new product called “semi-flexible FR4 PCB”, its flex area is made by FR4 material.
- Is FR4 RoHS Compliant?
Yes, FR4 is RoHS compliant. This means that it meets the regulations set by the European Union to limit the use of specific hazardous materials found in electrical and electronic products.
- What is FR4 Tg?
The glass transition temperature (Tg) of FR4 is a critical property that indicates the temperature at which the material transitions from a hard, glassy state to a soft, rubbery state.
Best Technology excels not only in PCB and assembly manufacturing, but also in offering top-quality PCB design services. Our professional engineering team is ready to support your innovation across various industries, including communications, healthcare, industrial, and consumer electronics. We welcome all the questions or inquiries from you.
Tags: FR4 Material, high tg pcb, rogers pcb