Soldering wire material refers to the specific metals or alloys used to create the solder wire. This wire is essential in joining metal parts, primarily in electronics. The material is designed to melt at a specific temperature, bonding components together securely once it cools. Different materials offer various properties, making them suitable for specific applications.
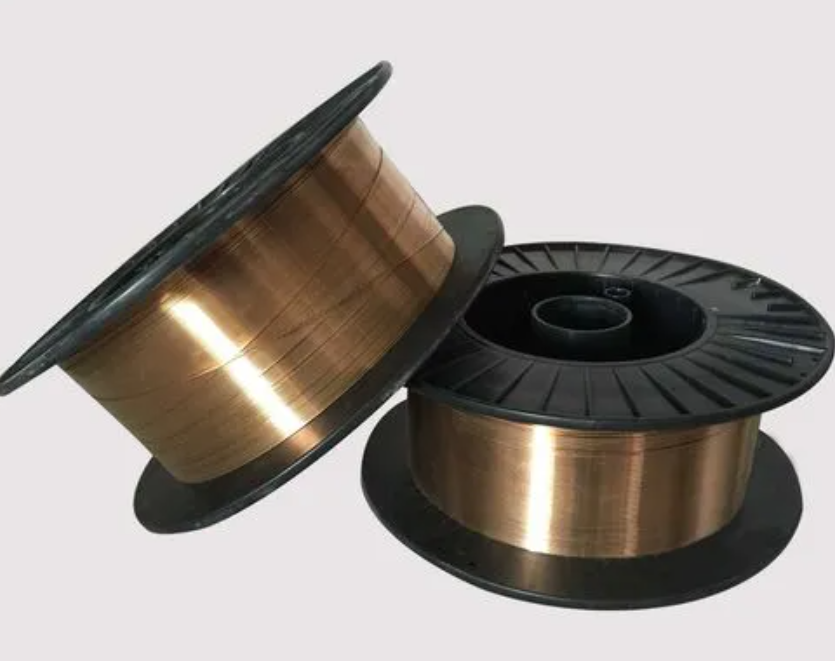
Types of Soldering Wire Material
- Tin-Lead Solder (Sn-Pb)
- Lead-Free Solder
- Silver Solder
- Copper Solder
- Bismuth Solder
- Aluminum Solder
- Rosin-Core Solder
- Acid-Core Solder
Solder Properties
1. Melting point
One of the most significant properties of solder is its melting point. The melting point of solder must be lower than that of the materials being joined. Traditional tin-lead solder melts at around 183°C (361°F), while lead-free solder, often composed of tin with copper or silver, melts at a slightly higher temperature, typically between 217°C (423°F) and 221°C (430°F).
2. Electrical conductivity
The composition of the solder, particularly the percentage of tin, plays a significant role in its ability to conduct electricity efficiently. Tin-based solders offer high conductivity, ensuring that the electrical connections remain stable and reliable.
3. Thermal conductivity
Besides electrical conductivity, solder also has good thermal conductivity. It helps prevent overheating and potential damage to the electronic components being joined.
4. Mechanical strength
Solder joints need to be hard enough to withstand physical stress, vibrations, and thermal expansion without breaking or weakening. The alloy composition, especially the amount of tin and any additional metals like silver, contributes to the overall strength of the solder.
5. Corrosion resistance
Solder alloys are often designed to resist oxidation and corrosion, with lead and tin providing good resistance. However, lead-free solders may require additional coatings or treatments to ensure long-term corrosion resistance, especially in harsh environments.
6. Wettability
Wettability refers to the ability of the molten solder to flow and adhere to the surfaces being joined. Good wettability ensures that the solder spreads evenly, creating a solid and uniform joint. A solder with poor wettability might result in weak or incomplete joints, leading to unreliable connections.
7. Flow characteristics
The flow characteristics of solder describe how easily it melts, flows, and fills the gaps between the components being soldered. Solder with good flow characteristics ensures that the joint is completely filled, minimizing the risk of voids or weak spots.
8. Ductility
A ductile solder can absorb some of these forces, reducing the risk of cracks or fractures in the joint. Tin-based solders are generally quite ductile, making them suitable for a wide range of applications, including those requiring some flexibility in the joint.
Is Soldering Wire Made of Lead?
Traditional soldering wire was commonly made with a mixture of tin and lead. However, due to the toxic nature of lead, many industries have switched to lead-free alternatives. Lead-based solder is still available but is used less frequently, especially in consumer electronics, where regulations have pushed for safer alternatives.
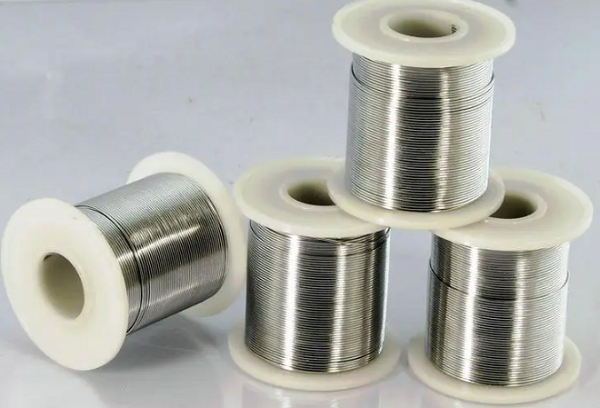
What is the Best Metal Wire for Soldering?
The best metal wire for soldering depends on the specific application. For general electronics work, a lead-free tin-copper wire is often the best choice due to its balance of performance and safety. For more specialized tasks, such as soldering sensitive components, a tin-silver or tin-copper-silver alloy might be preferred for its lower melting point and superior electrical conductivity.
What is Solder Used For?
Solder is used to create secure, conductive connections between metal components. It is most commonly used in electronics to connect wires and components to circuit boards. Solder can also be used in plumbing, jewelry making, and other applications where a strong, conductive bond between metals is required. Here are some common applications:
- Electronics assembly
- Plumbing
- Jewelry making
- Stained glass
- Automotive repair
- Aerospace and military applications
- Electrical wiring
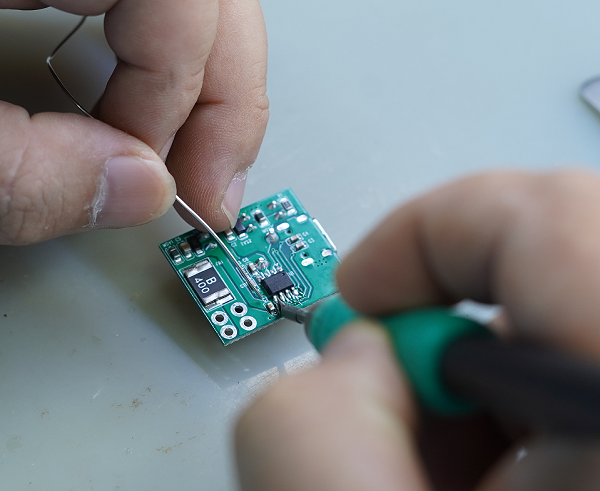
What is Lead-Free Solder Made of?
Lead-free solder is primarily composed of tin (Sn), which acts as the base metal, combined with other metals such as copper (Cu), silver (Ag), or bismuth (Bi) to enhance specific properties. The exact composition of lead-free solder varies depending on the intended application, but some of the most common alloys include:
1. Tin-Copper (Sn-Cu)
One of the most basic and cost-effective lead-free solder compositions, tin-copper solder typically contains about 99.3% tin and 0.7% copper. This alloy is widely used for general-purpose soldering in electronics and plumbing due to its relatively low melting point (around 227°C or 441°F) and good mechanical strength.
2. Tin-Silver-Copper (Sn-Ag-Cu or SAC)
Often referred to as SAC solder, this alloy is a popular choice in electronics manufacturing. It usually consists of 96.5% tin, 3% silver, and 0.5% copper. SAC alloys offer excellent mechanical properties, including high tensile strength and good thermal fatigue resistance, making them ideal for soldering in environments where components are subject to repeated thermal cycling. The melting point of SAC solder is around 217°C to 221°C (423°F to 430°F).
3. Tin-Bismuth (Sn-Bi)
Tin-bismuth solder is another common lead-free alloy, typically containing about 42% tin and 58% bismuth. This alloy has a lower melting point (around 138°C or 280°F) compared to other lead-free solders, making it suitable for soldering heat-sensitive components. It is also used in applications where low-temperature soldering is necessary, such as in surface-mount technology (SMT).
4. Tin-Silver (Sn-Ag)
Tin-silver solder, typically composed of 96.5% tin and 3.5% silver, is known for its high electrical and thermal conductivity. It has a melting point of around 221°C (430°F) and is often used in applications where reliability and durability are critical, such as in medical devices, aerospace, and high-performance electronics.
5. Tin-Zinc (Sn-Zn)
Tin-zinc solder is often used for aluminum soldering due to its ability to create strong bonds with aluminum surfaces. This alloy usually contains about 91% tin and 9% zinc, with a melting point of approximately 199°C (390°F). It’s less common in electronics but is valuable in specific industrial applications.
Is Solder Toxic?
Lead-based solder can be toxic, particularly if ingested or inhaled as fumes during the soldering process. Lead-free solder is less toxic but still requires proper ventilation and handling. It’s important to work in a well-ventilated area and to wash hands after handling solder to minimize any potential risks.
How Do I Choose the Right Solder Wire?
First, choose the right diameter. Generally speaking, the smaller the diameter of the solder wire is used for small electronic parts welding, and the larger the diameter of the solder wire is used for large parts welding. Welding wires with a diameter of 0.8mm or 1.0mm are usually selected, which are easier to control and easier to weld.
Secondly, pay attention to the tin content of the solder wire. The higher the tin content of the solder wire is more smooth when welding, the quality is more stable, but the price is relatively high. For some conventional small electronic parts welding, you can choose a solder wire with a tin content of 60% to 63%.
Also consider the conditions of welding work. If you work outdoors or in a high temperature environment or the component can withstand higher temperatures, you can choose a solder wire with a higher melting point, and if you work in a low temperature environment or the component can withstand lower temperatures, you need to choose a solder wire with a lower melting point. In addition, factors such as quality stability and corrosion resistance should be considered.
The last thing to choose is a reliable brand. The quality of brands varies greatly, and some brands of solder wire may have problems such as solder wire oxidation and lead not smooth, which can easily lead to poor welding and inconvenient use. Therefore, it is recommended to choose well-known brands or brands with reputation. At the same time, pay attention to the packaging and label when purchasing to ensure the authenticity and ease of management of the product.
There is not to blindly pursue cheap goods, it is best to use the electronic scale to weigh the weight, if possible, you can use the detector to detect the tin content, so that you can avoid the loss caused by false information.
What Type of Solder Must Never Be Used to Solder Wires?
When it comes to soldering wires, choosing the right type of solder is essential for creating strong, reliable connections. However, there is a specific type of solder that should never be used to solder wires: acid-core solder.
Acid-core solder contains an acid-based flux, which is highly effective at cleaning metal surfaces and removing oxidation. This aggressive cleaning action makes acid-core solder suitable for certain types of metalwork, such as plumbing, where it is used to solder copper pipes and fittings. However, the corrosive nature of the acid flux makes it unsuitable for electrical and electronic applications, including soldering wires.