In today’s era of rapid technological development, electronic devices have become an indispensable part of our lives. Behind this, a new type of circuit board material, ceramic pcb, is gradually becoming the most favored object in the field of electronics.
What is a ceramic pcb?
Ceramic circuit board, as the name suggests, is a circuit board made of ceramic as the substrate. Compared with traditional organic circuit boards, ceramic pcb have many unique advantages. Ceramic materials have extremely high heat resistance, insulation and mechanical strength, and can work stably under extreme environmental conditions.
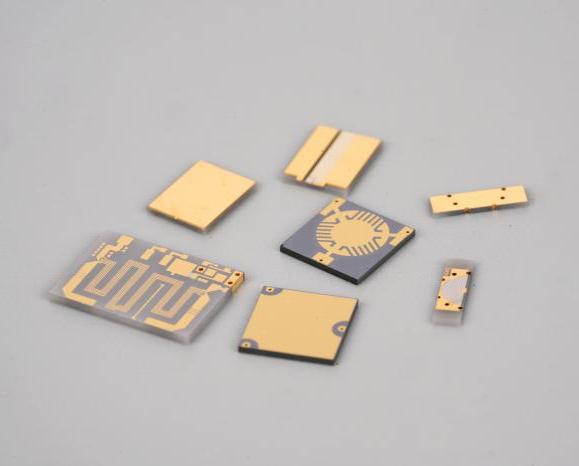
At the same time, ceramic pcb also have good thermal conductivity, which can effectively dissipate the heat generated by electronic components and improve the reliability and stability of electronic equipment.
Briefly describe the manufacturing process of ceramic pcb
The manufacturing process of ceramic pcbs is very complicated and requires multiple processes to complete.
First, it is necessary to select suitable ceramic materials, such as aluminum oxide, aluminum nitride, etc. These ceramic materials have different performance characteristics and can be selected according to specific application requirements.
Then, through precise processing technology, the ceramic material is made into the required shape and size. Next, advanced printing technology is used to print circuit graphics on the ceramic substrate.
Finally, through high-temperature sintering and other processes, the circuit pattern is fixed on the ceramic substrate to form a ceramic pcb.
What are the different types of ceramic PCB?
- Alumina ceramic PCB:
Alumina ceramic PCB is one of the most commonly used types of ceramic PCBs in the current market. It has the advantages of low price, good thermal conductivity, high resistance, high hardness, high electrical insulation, strong corrosion resistance, and high biocompatibility.
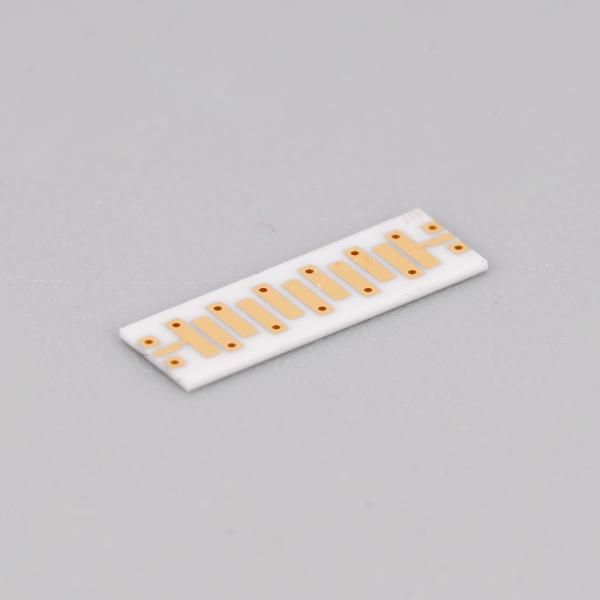
It is mainly used in white light, infrared, VCSEL LED lamps and other fields, usually used for 3W to 5W power LEDs. In the alumina PCB market, there are 75%, 96% and 99% alumina PCBs. The higher the purity, the better the performance, but the higher the cost.
- Aluminum nitride ceramic PCB:
The thermal conductivity of aluminum nitride ceramic PCB is 7 to 10 times higher than that of alumina PCB. It has the advantages of high thermal conductivity and resistance, high hardness, high mechanical strength, high electrical insulation, strong corrosion resistance, high biocompatibility, and thermal expansion coefficient close to Si.
It is considered to be the most promising ceramic PCB in the future and is widely used in high-power LEDs, power modules, laser fields, etc.
- Silicon nitride ceramic PCB:
Silicon nitride ceramic PCB has the advantages of high thermal conductivity, high strength, high fracture toughness, etc., and is mainly used in IGBT modules, vehicle modules, military industry, aerospace, aviation modules and other fields.
Unlike brittle traditional ceramic materials, at high temperatures, silicon nitride PCB has good mechanical strength and fracture toughness, and the thermal expansion coefficient matches that of Si. But the manufacture of silicon nitride PCB is not easy, the bonding of the circuit layer to the ceramic substrate is unstable, and the resistance and insulation are low.
- Silicon carbide ceramic PCB:
Silicon carbide ceramic PCB has the advantages of good strength even at 1400°C, extremely high thermal conductivity and resistance, good semiconductor conductivity, high hardness, etc.
Mainly used in the laser field, it is easy to work at 1000°C. At present, the manufacturing cost of silicon carbide PCB is extremely expensive, but with the advancement of manufacturing technology in the future, it is expected to be more widely used.
What are the advantages of ceramic pcb?
- 1. High thermal conductivity: Ceramic materials have good thermal conductivity and can effectively dissipate the heat generated by electronic components.
- 2. High insulation: Ceramic materials have extremely high insulation properties, which can effectively prevent short circuits and leakage between circuits.
- 3. High mechanical strength: Ceramic materials have high mechanical strength and can withstand large external forces and vibrations.
- 4. Good dimensional stability: The thermal expansion coefficient of ceramic materials is very small, and they can maintain dimensional stability under different temperature environments.
- 5. Good chemical stability: Ceramic materials have good chemical stability and can resist the erosion of various chemical substances.
What are the application areas of ceramic pcb?
- 1. LED lighting: Since LED lamps generate a lot of heat when working, circuit boards with good thermal conductivity are needed to dissipate heat.
- 2. Power electronics: Power electronic devices usually need to withstand high voltages and high currents, so circuit boards with good insulation and mechanical strength are needed.
- 3. Aerospace: The aerospace field has very high requirements for the reliability and stability of electronic equipment, so it is necessary to use circuit boards with good heat resistance, insulation and mechanical strength.
- 4. Medical equipment: Medical equipment has very high requirements for the safety and reliability of electronic equipment, so it is necessary to use circuit boards with good insulation and chemical stability.
- 5. Communication equipment: Communication equipment has very high requirements for the high-frequency performance and stability of electronic equipment, so it is necessary to use circuit boards with good high-frequency performance and dimensional stability.
How thick is ceramic PCB?
The thickness of ceramic PCB varies depending on different types and application scenarios. Generally speaking, the thickness of common ceramic PCBs ranges from 0.25mm to 1.5mm.
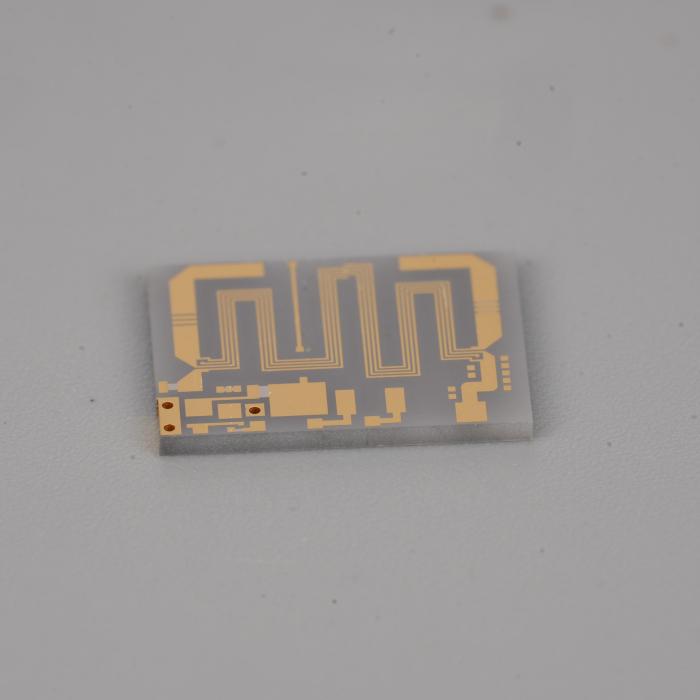
The thickness of alumina ceramic PCBs is usually 0.5mm – 1.5mm. Alumina ceramics are widely used because of their low cost, and the choice of board thickness usually depends on the specific application requirements.
In some occasions where space requirements are not high but a certain mechanical strength is required, thicker alumina ceramic PCBs may be selected, such as 1.2mm or 1.5mm thickness. In some small electronic devices with limited space, thinner alumina ceramic PCBs, such as 0.5mm or 0.8mm thickness, may be selected.
The thickness of aluminum nitride ceramic PCB is relatively thin, generally between 0.25mm – 1.0mm.
Aluminum nitride has better thermal performance, but it is also more expensive. Due to its high thermal conductivity, in some applications with extremely high heat dissipation requirements, such as heat dissipation substrates for high-power semiconductor chips, thinner aluminum nitride ceramic PCBs may be selected to achieve better heat dissipation and more compact design.
In some high-end electronic devices, aluminum nitride ceramic PCBs with a thickness of 0.5mm or 0.6mm may be used.
In short, the thickness of ceramic PCBs has a certain flexibility and can be selected according to specific application scenarios and performance requirements.
At what temperature does ceramic PCB melt?
Ceramic PCBs usually do not “melt” like metals.
Ceramic materials have very high melting points, such as the melting point of alumina ceramics is about 2050℃, and the melting point of aluminum nitride ceramics is about 2200℃. In the normal use environment of electronic equipment, ceramic PCBs will hardly reach such high temperatures.
It should be noted that although the ceramic PCB itself will not melt, the metal circuits, solder, etc. on it may change or be damaged at too high a temperature.
As an innovative treasure in the field of electronics, ceramic pcbs have many unique advantages and broad application prospects. It is believed that in the near future, ceramic pcbswill become the mainstream circuit board material in the electronics field and make greater contributions to the development of electronic technology.
Tags: ceramic PCB, PCB, PCBA