IC substrates are usually made of multiple layers of insulating materials, conductors, and semiconductor materials. These materials are precisely processed to form a complex circuit network. The material selection of the substrate has a crucial impact on its performance, such as thermal conductivity, electrical properties, mechanical strength, etc.
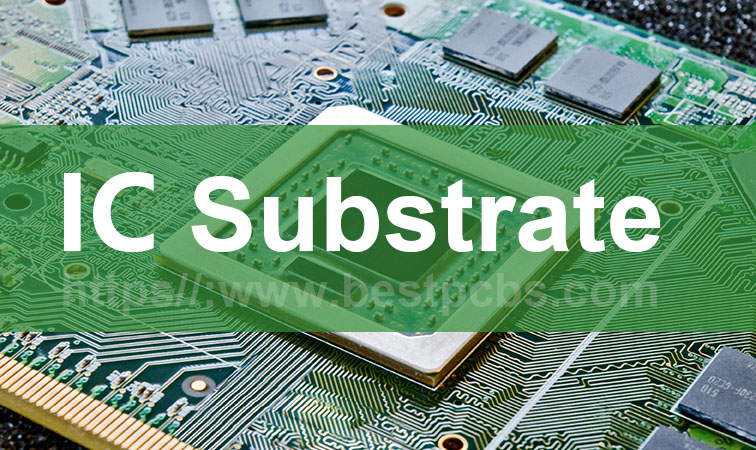
IC substrates play an important role in electronic devices, providing stable support and efficient connections for integrated circuits. With the continuous development of electronic technology, the importance of IC substrates will continue to increase.
What is an ic substrate
IC substrate, also known as ic package substrate, is a substrate used to package bare IC (integrated circuit) chips. It is the core material of chip packaging and has the characteristics of high density, high precision, high performance, miniaturization and thinness.
As an intermediate product, IC substrate connects the chip and the circuit board, plays a role in physical mechanical support, heat dissipation and protection, and provides electronic connection between the chip and the PCB to achieve signal transmission.
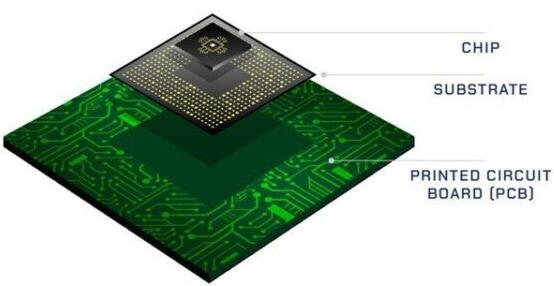
It is a key carrier in the packaging and testing process and is widely used in mainstream packaging technologies such as BGA (ball grid array packaging) and CSP (chip size packaging). The main functions of the packaging method include isolating the exposed chip from the air, preventing corrosion of the circuit on the chip, and providing an intermediate bridge for information transmission between highly refined chips and less refined printed circuit boards.
IC substrate definition
IC substrate is the support of semiconductor integrated circuits. Its main function is to connect various electronic components to form a complete circuit system. As a platform, it provides a solid foundation for various components within the IC to ensure the normal operation of the circuit.
IC substrate manufacturing process
How are ic substrates made? IC (Integrated Circuit) substrate manufacturing refers to packaging electronic components onto a circuit board to form a complete circuit system. The IC substrate manufacturing process mainly includes the following steps: design, proofing, printing, drilling, gold plating, welding, testing and packaging.
- Design, schematic design and layout design are carried out according to the circuit design requirements, the size and number of layers of the circuit board are determined, and process analysis is carried out to determine the substrate manufacturing process.
- Proofing, the designed circuit board sample is generated into a file, and the graphics on the file are transferred to the circuit board through a photolithography machine to form a copper pole, etc.
- Printing, the area on the circuit board on the graphics transferred by the photolithography machine is etched to remove unnecessary copper and expose the glass fiber surface.
- Drilling, use a drilling machine to make the required holes on the circuit board for welding components.
- Gold plating, a layer of metal is covered on the surface of the circuit board through the electroplating process, which can improve the conductivity of the product on the one hand and prevent oxidation on the other hand.
- Soldering: solder IC chips and other components to the corresponding positions of the circuit board, using hot plates and brackets for soldering.
- Testing: test the soldered circuit board to verify whether the electrical performance, signal path and stability of the circuit board meet the design requirements.
- Packaging: label, clean and package the qualified circuit boards to make them suitable for transportation and storage.
how ic substrate differentiate? The IC substrate manufacturing process is a complex and delicate process that requires a series of steps such as design, proofing, printing, drilling, gold plating, welding, testing and packaging. Only by strictly following the process can the quality and performance of the final product be guaranteed.
IC substrate manufacturers
As a leader of IC substrate manufacturer, Best Technology has over 18 years experience, we are so confident that we can provide the highest quality and high specifition IC substrate for you! Backing up with a group of professional engineers, and well established quality system. Best Technology has grown to become a major PCB manufacturer in Asia to serve in diverse customers base. At Best Technology, you can enjoy a full turn-key service from IC substrate design, prototyping, mass production and IC substrate assembly.
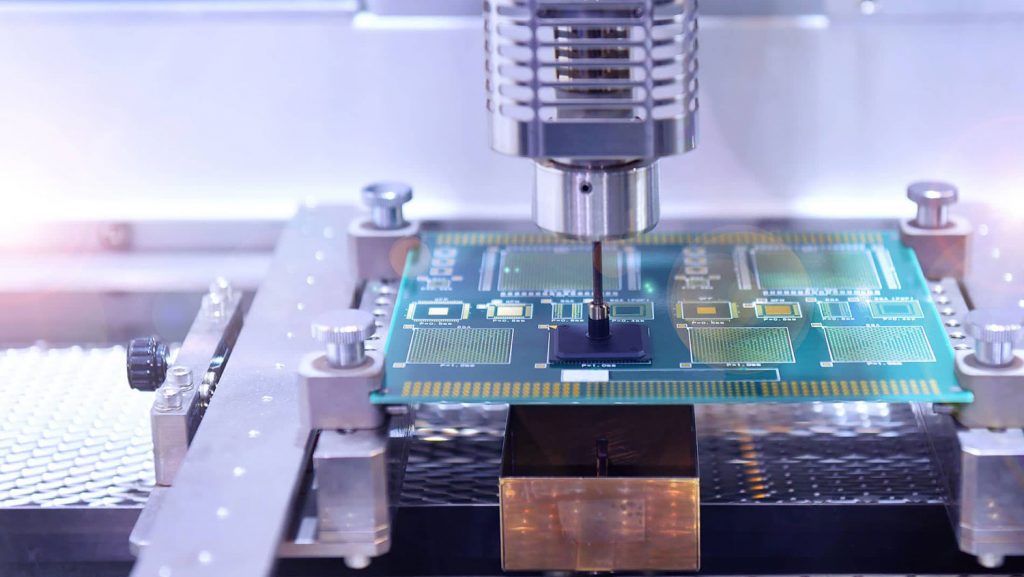
IC substrate manufacturers
How ic substrate differentiate
How to distinguish IC substrates? The distinction of IC substrates can be made in many ways, mainly including classification by package type, material properties, and bonding technology.
1. Classification by package type:
BGA IC substrate: It performs well in heat dissipation and electrical performance, can significantly increase chip pins, and is suitable for IC packages with more than 300 pins.
CSP IC substrate: It is a single-chip package with light weight, small size, and similar size to IC. It is mainly used in memory products, telecommunications products, and electronic products with a small number of pins.
FC IC substrate: By flipping the chip package, it has low signal interference, low circuit loss, good performance, and effective heat dissipation.
MCM IC substrate: It absorbs chips with different functions into one package, which is light, thin, short, and miniaturized, but because multiple chips are packaged in one package, this type of substrate does not perform well in signal interference, heat dissipation, fine wiring, etc.
2. Classification by material properties:
Rigid IC substrate: Mainly made of epoxy resin, BT resin or ABF resin, with a CTE (coefficient of thermal expansion) of about 13 to 17ppm/°C.
Flex IC substrate: Mainly made of PI or PE resin, with a CTE of 13 to 27ppm/°C.
Ceramic IC substrate: Mainly made of ceramic materials such as alumina, aluminum nitride or silicon carbide, with a relatively low CTE of about 6 to 8ppm/°C.
3.Classification by bonding technology:
Wire bonding
TAB (Keyboard Automated Bonding)
FC bonding
IC substrate vs PCB
The differences between IC substrate and PCB are mainly reflected in the definition, materials, structure, manufacturing process and application scenarios. In this article, Jieduobang will introduce the differences between IC substrate and PCB in detail.
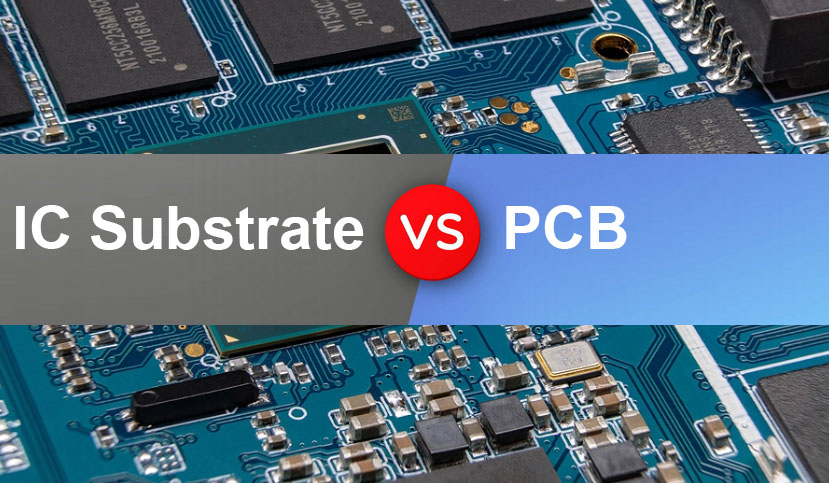
- Definition
PCB is the support of electronic components and the carrier for the electrical connection of electronic components; IC substrate is an integrated circuit chip carrier used to install integrated circuit chips and provide electrical connections with extremely high density and reliability.
- Materials
PCB uses conductive and insulating materials such as copper clad laminate, glass fiber material and PTFE material; IC substrate mainly uses polymer materials (such as FR-4) and brittle ceramic materials.
- Structure
PCB is composed of circuit boards by stacking multiple board layers, which can be connected through holes; the structure of IC substrate mainly includes circuit layer and assembly layer.
- Manufacturing process
PCB manufacturing includes steps such as design, graphic layout, patch, welding and testing; IC substrate needs to undergo tedious processes such as preheating, pitting and buttoning.
Application of IC substrates
PCBs are widely used in the field of electronic product manufacturing, such as computer motherboards, mobile phone circuit boards, etc.; IC substrates are small, high-density, and highly reliable, and are widely used in high-end electronic fields, such as aerospace, national defense, and automotive electronics.
Tags: IC substrate