In today’s era of rapid technological development, the performance and reliability of electronic equipment are attracting more and more attention. As an important carrier of electronic components, aluminum pcb board plays a vital role in the field of electronics.
What is aluminum PCB?
Aluminum PCB board is a metal-based copper-clad board with good heat dissipation function. This board is mainly used for high-end applications. When designed as a double-sided board, the structure is a circuit layer, an insulating layer, an aluminum pcb board, and then an insulating layer and a circuit layer.
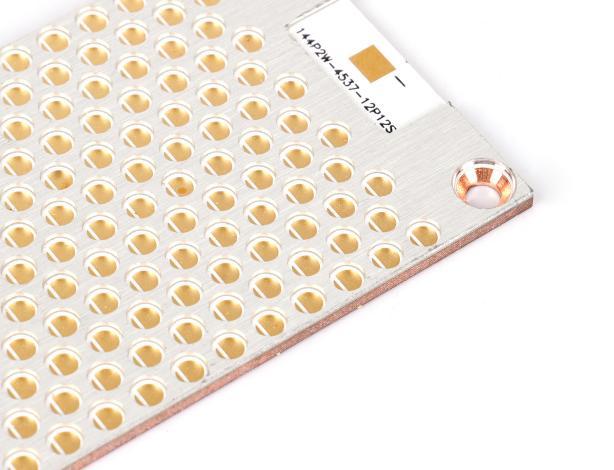
In rare cases, aluminum pcb board can also be designed as multi-layer boards, which are formed by laminating ordinary multi-layer boards with insulating layers and aluminum pcb board.
The unique advantage of aluminum pcb board lies in their excellent heat dissipation performance. The power device is mounted on the circuit layer on the surface. The heat generated by the device during operation is quickly transferred to the metal base layer through the insulating layer, and then the metal base layer transfers the heat away to achieve effective heat dissipation of the device.
This design enables the aluminum pcb board to minimize thermal resistance and has excellent thermal conductivity. At the same time, compared with traditional materials, aluminum pcb board can reduce volume, extend life, and improve power density and reliability while carrying higher currents.
In addition, aluminum pcb board also meet RoHS requirements, are more suitable for SMT processes, and effectively handle heat diffusion in circuit design schemes, reduce the assembly of heat sinks and other hardware, reduce costs, improve the optimal combination of power circuits and control circuits, replace fragile ceramic substrates, and obtain better mechanical durability.
How do you make aluminum PCB?
The production process of aluminum pcb board mainly includes the following steps:
- Cutting: First, cut the aluminum pcb board material according to the design requirements.
- Drilling: Drill holes on the aluminum pcb board according to the circuit design requirements to prepare for subsequent circuit production.
- Dry film photo imaging: Cover the dry film on the aluminum pcb board and transfer the circuit pattern to the aluminum pcb board through photo imaging technology.
- Board inspection: Check whether the circuit pattern on the aluminum pcb board meets the design requirements.
- Etching: Use chemical etching to remove the part not covered by the dry film to form a circuit pattern.
- Etching inspection: Check the etched aluminum pcb board again to ensure the accuracy of the circuit pattern.
- āGreen paintā: Apply protective paint to prevent the circuit from being oxidized and corroded.
- āCharacterā: Print necessary logos and information on the aluminum pcb board.
- āGreen inspectionā: Check the aluminum substrate after applying protective paint to ensure quality.
- āHinningā: Spray tin on the aluminum substrate to improve welding performance.
- Surface treatmentā: Treat the surface of the aluminum substrate, such as applying thermal conductive slurry to optimize heat dissipation performance.
- āPunchingā: Cut the aluminum substrate as needed to form the final product shape.
- āFinal inspectionā: Perform final quality inspection on the finished aluminum substrate.
- āPackaging and shipmentā: Pack qualified aluminum substrates and prepare for shipment.
This series of steps ensures that the production quality and performance of the aluminum substrate meet the design and use requirements. Aluminum substrates are widely used in high-end electronic devices due to their excellent heat dissipation and machining performance.
How much does aluminum PCB cost?
The cost of aluminum substrate PCB is about 230 yuan to 400 yuan per square meter. ā
The cost of aluminum substrate PCB is affected by many factors, including board type, production process, testing cost and other additional expenses.
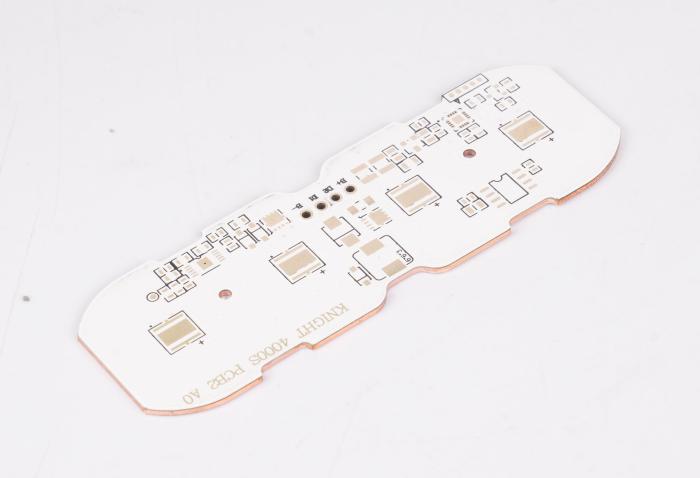
Aluminum substrate PCB is a metal-based copper-clad board with good heat dissipation function. This board is highly praised in certain specific application scenarios due to its efficient heat dissipation performance, but correspondingly, its cost is usually much higher than other types of PCB.
āBoard costā is one of the main costs of aluminum substrate PCB. The board cost used in aluminum substrate is higher because of its special materials and manufacturing process.
āProcessing costā also occupies a certain proportion. The processing process of aluminum substrate includes cutting, drilling, electroplating, lamination and other links. The equipment and process requirements of each link will affect the final cost.
āQuality inspection costā is also not to be ignored. Strict quality inspection is required during the production process, including environmental adaptability testing, electrical performance testing, etc. The number and strictness of these inspection items will also affect the production cost.
In summary, the cost of aluminum substrate PCB is affected by many factors, roughly between 230 yuan and 400 yuan per square meter, and the specific price will vary according to specific needs and production conditions.
What are the layers of aluminum PCB?
The number of layers of aluminum-based PCB can be single-sided, double-sided or multi-layer. ā
- āSingle-sided aluminum substrateā: On this type of PCB, the parts are concentrated on one side and the wires are concentrated on the other side. Since the wires only appear on one side, this PCB is called a single-sided aluminum substrate.
- āDouble-sided aluminum substrateā: There are wiring on both sides of the circuit board, but to use the wires on both sides, there must be appropriate circuit connections between the two sides.
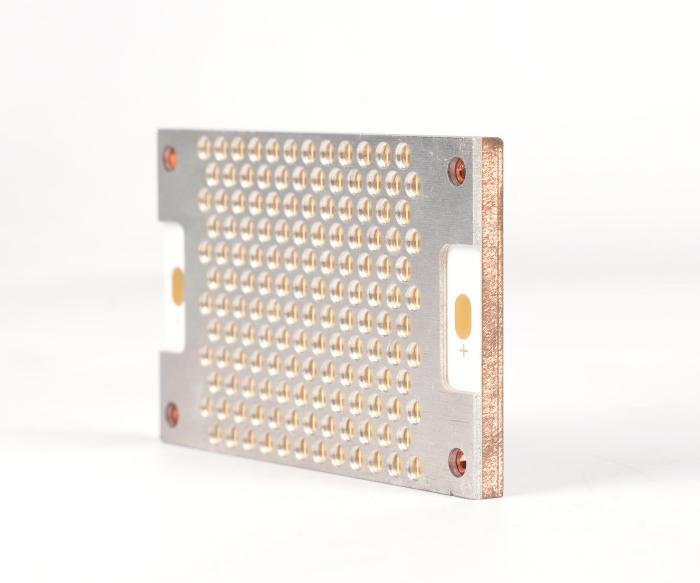
- āMultilayer boardā: In order to increase the area that can be wired, multilayer boards use more single-sided or double-sided wiring boards. The printed circuit board that is alternately connected by the positioning system and insulating adhesive materials and the conductive patterns are interconnected according to the design requirements becomes a four-layer or six-layer printed circuit board, also known as a multilayer printed circuit board.
How thick is aluminum clad PCB?
The thickness of aluminum clad PCB usually ranges from 0.12mm to 0.18mm, with an error of ±0.01mm.
The thermal conductivity of aluminum substrate is one of the important indicators for evaluating its quality, and the thermal conductivity of aluminum substrate is generally 2.0-0.1, which means that the thermal conductivity of aluminum substrate is excellent and can effectively improve the heat dissipation efficiency of circuit boards.
In addition, the thickness of the insulation layer of aluminum substrate is usually 0.003 to 0.006 inches, which is composed of UL-certified aluminum plate cladding and insulating materials, while the base layer is a metal substrate, usually aluminum or copper.
What are the disadvantages of aluminum PCB?
The disadvantages of aluminum PCB mainly include high cost, high process difficulty, non-uniform board material, and easy problems in pressure resistance and electrical strength. ā
- āHigh costā: The cost of aluminum PCB is relatively high, usually more expensive than other types of PCBs, and the price accounts for more than 30% of the total cost of the product.
- āHigh process difficultyā: When making aluminum PCB, due to its special material and structure, the process of making double-sided boards is difficult, and during the manufacturing process, problems in pressure resistance and electrical strength are also easy to occur.
- āInconsistent board materialsā: There is no unified international standard for the material specifications of aluminum PCBs. There are multiple specifications such as CPCA industry standards, national standards and international standards, which increases the complexity of selection and useā.
- āProblems with withstand voltage and electrical strengthā: Aluminum substrates are prone to fail to meet the withstand voltage index, which may lead to safety problems during useā.
Why is aluminum no longer used in integrated circuits?
The main reason why aluminum is no longer used in integrated circuits is that its high resistivity and easy electromigration are gradually exposed with the increase of chip integration and the reduction of feature size, which limits its application in high-performance chips. ā
Aluminum is one of the earliest widely used metals in semiconductor chips. Due to its good conductivity and relatively low cost, it has been widely used as an interconnect metal in early integrated circuits.
However, with the increase of chip integration and the reduction of feature size, the shortcomings of aluminum gradually emerge. In addition, aluminum wires may experience electromigration under the action of long-term current, which will cause the failure of integrated circuits.
As an alternative material, copper has lower resistivity and higher electromigration resistance than aluminum, can carry larger current in thinner metal wires, and is more reliable under high-speed current conditions.
With the continuous development of electronic technology, aluminum substrates are also constantly innovating and developing. In the future, aluminum substrates will pay more attention to product quality, performance and environmental protection, and provide more reliable support for the development of electronic equipment. BEST Technology focuses on circuit board design and production, and has many years of experience in aluminum substrate manufacturing. Choosing BEST Technology will provide you with the best service.
Tags: aluminum pcb board, aluminum substrate, PCB