What is a Solder Wick?
A solder wick, also known as a desoldering braid, is a finely woven copper strip that assists in the removal of solder from electronic components. It is often pre-coated with flux, which helps remove solder more effectively. This tool is vital for repairing circuit boards, replacing damaged components, or correcting soldering errors.

The design of a solder wick is simple yet effective. The copper braid absorbs melted solder through capillary action, leaving the work area clean and ready for repairs. Its ease of use makes it popular among both professionals and hobbyists in electronics. Whether you’re fixing a smartphone or assembling a custom PCB, solder wick is an invaluable addition to your toolbox.
Purpose of Solder Wick During the Desoldering Process
Solder wick plays a critical role in the desoldering process. When a mistake occurs during soldering or a component needs replacement, excess solder must be removed without damaging the surrounding area. Solder wick absorbs this excess solder, clearing the way for rework or repairs.
In the printed circuit board assembly (PCBA) industry, maintaining precision is essential. Solder wick ensures clean and accurate connections by eliminating leftover solder. This tool also reduces the risk of solder bridges, which can cause short circuits. Professionals rely on solder wick to achieve a polished finish and maintain the integrity of circuit boards.
What is Solder Wick Made Of?
The main composition of solder wick is an alloy of tin and lead, usually dominated by tin lead alloy, of which the proportion of tin is slightly higher, the common proportion is 63% tin and 37% lead. In addition, other metallic elements can be added to the solder material, such as silver, copper, antimony, cadmium, etc., to change its melting point and performance.
In the process of making solder wick, flux is usually added. The main components of flux include rosin, flux, water-soluble resin and activator, etc. These components help to remove oxides on metal surface, prevent oxidation during welding, and form a protective film at high temperature. Flux can also be divided into R type, RA type, RAM type, etc., according to different needs to choose different types.
solder wick is widely used in the electronics industry, mainly used to connect electronic components and circuit boards, with low melting point, easy to operate. The development trend of solder materials is environmentally friendly solder, reducing the use of lead to avoid environmental pollution.
Is Solder Wick the Same as Solder?
Although solder wick and solder are closely related, they serve opposite purposes. Solder is a fusible metal alloy used to create electrical connections on circuit boards. It bonds components by melting and solidifying to form a conductive link.
Solder wick, on the other hand, removes solder. It acts as a cleaning tool to eliminate excess solder or fix errors. The contrast between the two highlights their complementary roles in electronics. Solder creates connections, while solder wick clears them when adjustments are needed.
What is the Difference Between Rosin and No-Clean Solder Wick?
Rosin solder wick is coated with rosin-based flux, which is derived from natural tree resin. This type of flux is highly effective at dissolving oxides, making it suitable for removing solder from heavily oxidized joints or components exposed to the environment.
However, rosin flux leaves behind a sticky residue after use. This residue is non-conductive in its solid state, so it doesn’t typically cause short circuits. However, in humid or high-temperature environments, the residue can attract dust or absorb moisture, potentially leading to reliability issues over time. To prevent such risks, the residue must be cleaned off using isopropyl alcohol or a similar solvent. This extra cleaning step adds time and effort, but it ensures a spotless and professional finish.
No-clean solder wick uses a specialized flux that leaves minimal, non-conductive residue on the work surface. This type of flux is designed for modern electronics where quick and efficient processes are essential. The residue left behind is safe for most applications and doesn’t require additional cleaning, which is a significant time-saver for manufacturers or technicians working on tight deadlines.
However, no-clean solder wick is less effective at removing solder from oxidized surfaces compared to rosin-based products. It’s best suited for projects where the components or boards are relatively clean and oxidation-free. Its convenience and efficiency make it a popular choice for high-volume production environments or fieldwork.
The choice between rosin and no-clean solder wick depends on the requirements of your project. If thorough cleaning is not an issue and you’re dealing with stubborn, oxidized solder joints, rosin solder wick may be the better choice. On the other hand, if time efficiency and minimal cleaning are priorities, no-clean solder wick is better.
How to Use Soldering Wick?
Using solder wick is a straightforward process, but proper technique ensures the best results.
- Prepare the area: Before using the solder wick, power on your soldering iron and allow it to reach the required temperature. Ensure the area is clean and free from debris.
- Position the wick: Place the solder wick directly over the solder you want to remove.
- Apply heat: Press the soldering iron tip onto the wick and the solder joint simultaneously. This heats both the wick and the solder, allowing the molten solder to flow into the copper braid.
- Remove the wick: Once the solder is absorbed, gently lift the solder wick. Avoid excessive pressure to prevent damage to the circuit board.
- Trim the wick: Cut off the used portion of the solder wick with scissors to expose fresh material for future use.
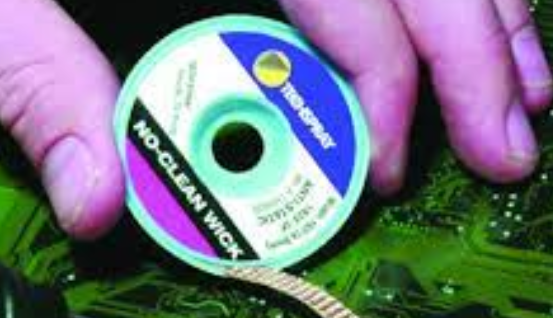
Do You Need Flux with Solder Wick?
Most solder wicks come pre-coated with flux, so additional flux is often unnecessary. However, adding flux can be beneficial in certain scenarios, especially when dealing with oxidized solder or stubborn joints.
Flux helps by cleaning the surface and improving the flow of molten solder, making it easier for the wick to absorb. When using flux with solder wick, ensure it’s compatible with your project. For example, no-clean flux is suitable for applications where residue removal isn’t feasible, while rosin flux might require cleaning after use.
What Can I Use Instead of Solder Wick?
If solder wick is unavailable, there are several alternatives to consider:
- Desoldering pumps: These tools use suction to remove molten solder. They are effective for larger solder joints but may struggle with finer details.
- Copper wire strands: Stripping and braiding thin copper wires can create a makeshift wick. While not as efficient, it can work in emergencies.
- Steel wool: This material can absorb solder but requires careful handling to avoid damaging components.
- Solder sucker bulbs: Similar to desoldering pumps, these devices use air pressure to clear solder.
While these alternatives can be helpful, they may not provide the precision and efficiency of a professional solder wick.
Does Solder Wick Go Bad?
Yes, solder wick can go bad over time, losing its effectiveness due to factors like oxidation, flux degradation, and improper storage.
Oxidation of the Copper Braid
Solder wick is made of finely braided copper wire, which is highly susceptible to oxidation when exposed to air and moisture. Oxidized copper doesn’t conduct heat as efficiently and is less able to absorb molten solder. This makes the wick less effective, requiring more time and effort to remove solder. To prevent oxidation, solder wick should be stored in an airtight container or resealable bag.
Flux Degradation
Flux plays a crucial role in the performance of solder wick. Over time, the flux coating can dry out, evaporate, or degrade due to exposure to air, heat, or light. Without an active flux coating, the wick struggles to absorb solder efficiently, especially on oxidized joints.
You can keep your solder wick sealed in its original packaging or a similar protective enclosure to avoid flux degradation. Avoid storing it in high-temperature environments, such as near soldering equipment or direct sunlight, as heat accelerates flux evaporation.
Physical Wear and Tear
Frequent handling can cause the braided copper strands to fray or deform, reducing the wick’s ability to maintain contact with the solder joint. Worn-out wick may not perform as intended, leading to incomplete solder removal.
Quality of the Wick
The quality of the solder wick also determines how long it will remain effective. High-quality products with better flux coatings and tightly braided copper tend to last longer and perform more consistently. Cheaper solder wicks may degrade more quickly or have inconsistent flux application.
Signs Your Solder Wick Has Gone Bad
- It doesn’t absorb solder efficiently.
- The flux coating appears dry or powdery.
- The braid looks discolored or corroded.
- Excessive heat is required to make it work.
If your solder wick becomes ineffective, replacing it is often the best option. While there are DIY methods, such as re-coating the wick with flux, these are time-consuming and may not restore the wick to its original performance level. Using fresh solder wick ensures consistent, reliable results and avoids complications during repairs.
How Do You Make a Homemade Solder Wick?
Creating a DIY solder wick is possible with basic materials, although it may not match the performance of commercial products. Here’s how:
- Gather materials: Obtain thin copper wires from an old cable or electronic device.
- Prepare the wire: Strip the insulation and braid the wires together tightly.
- Apply flux: Coat the braid with liquid flux or rosin to improve solder absorption.
While this method works in emergencies, professional solder wick remains the better choice for consistent results. Looking for a professional PCBA manufacturer is better.
Professional PCBA Manufacturer – Best Technology
At Best Technology, we specialize in delivering top-quality PCBA services tailored to your needs. From design to assembly, our team focuses on precision and excellence. We understand the importance of clean and efficient soldering in circuit board production, and our expertise ensures flawless results.
Partnering with Best Technology means gaining access to advanced tools, skilled professionals, and reliable support. Whether you’re working on complex projects or simple repairs, our solutions will exceed your expectations.
Contact us today to learn how to get your first PCBA product!
Tags: solder wick