What Is Solder Mask?
Solder mask also known as S/M, it is a protective layer applied to a printed circuit board (PCB) to shield the copper traces from oxidation and environmental damage. It serves as an insulator between the conductive areas of the PCB and the external environment, preventing unwanted electrical contact. This layer is typically applied after the copper traces are etched and before the components are mounted.
In addition to protection, the solder mask also provides insulation between adjacent copper traces, reducing the risk of short circuits. It allows manufacturers to design high-density boards where components are placed closely together. The solder mask is essential for achieving a clean, functional, and professional-looking PCB.
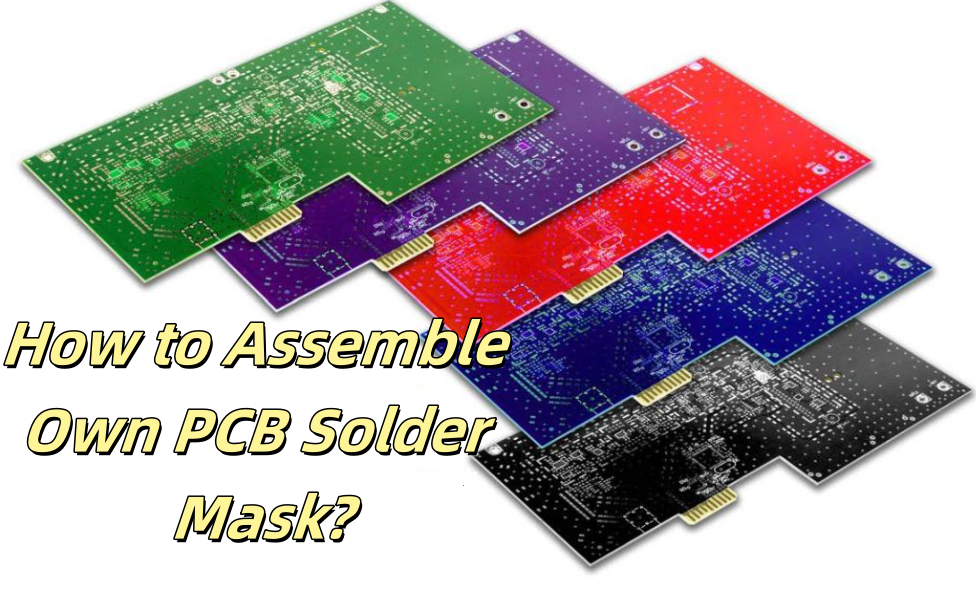
Is Solder Mask Necessary?
In professional PCB manufacturing, a solder mask is more than just a protective layer—it’s a necessity. While some DIY enthusiasts might skip it, especially for simple projects, it plays a critical role in ensuring the board’s functionality and longevity. It’s purposes are mainly including:
- Prevents Short Circuits: By covering the copper traces and exposing only the necessary pads, it minimizes the risk of solder bridges between components. This is especially important for boards with tight spacing.
- Increases Durability: The solder mask acts as a barrier against moisture, dust, and chemicals that could corrode the copper traces.
- Improves Aesthetic Appeal: A board with a solder mask looks clean, organized, and professional. This is particularly important for commercial products where appearance matters.
- Facilitates Easier Soldering: The mask helps guide solder to the right spots, reducing the chances of errors during assembly.
While it’s technically possible to assemble a PCB without a solder mask, the risks outweigh the benefits. Without it, the board is more vulnerable to environmental damage and soldering mistakes.
PCB Solder Mask Material / Solder Mask Ink
The type of solder mask material you choose can significantly impact the PCB’s performance and durability. Each material type has specific characteristics that make it suitable for different applications.
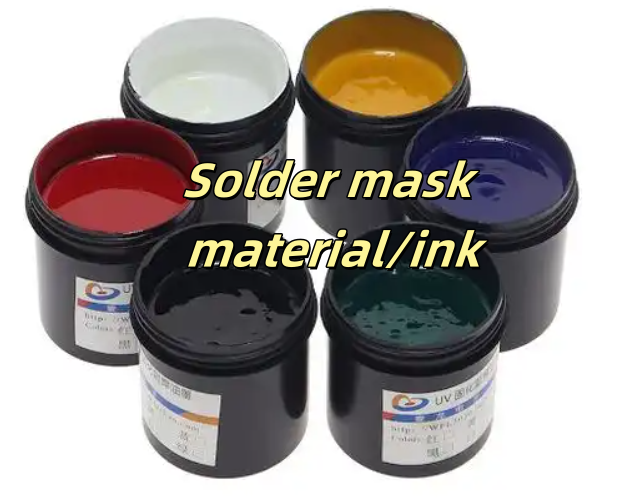
Epoxy Liquid Solder Mask:
This is one of the oldest and most cost-effective types of solder masks. It’s applied as a liquid and cured to form a protective layer. While it provides decent protection, its precision is not as high as more modern materials. It’s suitable for simpler designs or single-layer boards.
Liquid Photoimageable (LPI) Solder Mask:
LPI solder mask is the most commonly used type in modern PCB manufacturing. It’s applied as a liquid and then exposed to UV light through a photomask, which defines the areas to be covered. This method offers excellent precision and is ideal for high-density, multi-layer PCBs.
Dry Film Solder Mask:
This type is applied as a film and laminated onto the PCB surface. It’s often used in high-end applications where uniformity and precision are critical. Dry film masks provide better coverage and are less prone to defects compared to liquid-based masks.
UV-Curable Solder Mask:
This is popular among DIY enthusiasts because it’s easy to apply and cures quickly under UV light. While it doesn’t offer the same level of durability as industrial-grade masks, it’s sufficient for small-scale projects.
Solder Mask Colors
The color of the solder mask might seem like a purely aesthetic choice, but it can also affect the board’s usability during assembly and inspection.
- Green
Green is the industry standard due to its high contrast with the white silkscreen layer and the copper traces beneath. This contrast makes it easier to inspect for defects and errors.
- Red
Red solder masks offer a bold appearance and are often used for specialized or high-end boards. The contrast is not as high as green, but it’s still sufficient for inspection purposes.
- Blue
Blue masks are commonly used in consumer electronics. They provide a unique look and offer good contrast with the copper traces, making inspection relatively easy.
- White
White solder masks are often used in LED applications because they reflect light effectively. However, they can make inspection more challenging since the contrast with the silkscreen is low.
- Black
Black masks give a sleek, professional look but are the hardest to inspect visually. They’re often used in high-end consumer products where appearance is a priority.
Advantages of Solder Mask
Adding a solder mask to your PCB offers several benefits that go beyond aesthetics. Here’s a closer look at its advantages:
- Solder masks act as a barrier between adjacent pads, reducing the chances of accidental solder bridges during assembly.
- The mask shields the copper traces from moisture, dust, and other contaminants, preventing oxidation and corrosion.
- Some solder masks are designed to withstand high temperatures, making them suitable for applications where the board is exposed to heat during operation.
- A well-applied solder mask gives the PCB a clean and professional look, which is essential for commercial products.
- By exposing only the necessary pads and vias, the solder mask guides the solder to the right spots, smooth the assembly process and reducing the chances of errors.
What Is the Minimum Solder Mask Gap in PCB?
The solder mask gap is the distance between two adjacent exposed copper areas on the PCB. For most PCBs, the minimum solder mask gap is between 0.1 mm and 0.15 mm. This is sufficient for standard designs with moderate trace density. But in high-density designs, where traces and pads are closely packed, the gap might need to be as small as 0.05 mm. However, this requires precise manufacturing techniques to avoid defects.
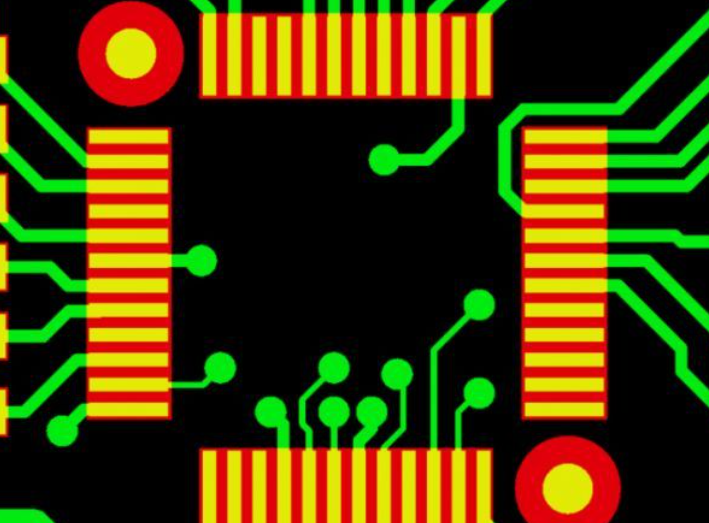
Some applications may have specific requirements for solder mask gaps, depending on the voltage and current levels involved. It’s essential to consult with your manufacturer to determine the optimal gap for your design. If you don’t have a reliable PCB manufacturer, Best Technology is your go-to choice.
How to Add Solder Mask to PCB?
The process of applying a solder mask involves several steps, let me explain it for you:
1. Clean the PCB Surface
Before applying the solder mask, ensure the PCB surface is clean and free of dust, grease, or oxidation. This step is key to keep proper adhesion and reduces the risk of defects during solder mask applying.
2. Apply the Solder Mask
Depending on the type of mask, you can apply it using a brush, spray, or lamination method. For DIY projects, UV-curable solder masks are often the easiest to work with.
3. Expose to UV Light
If you’re using a UV-curable mask, place the PCB under UV light for a specified period to harden the mask.
4. Develop the Mask
After exposure, remove the unexposed areas to reveal the pads and vias that need to remain uncovered.
5. Cure the Mask
Finally, bake the PCB in an oven to fully cure the solder mask and ensure it adheres well to the board.
What Happens If You Solder Without a Mask?
Without solder mask, PCB will have the following problems during soldering:
- Poor electrical performance
No solder bridge will lead to short circuit between the pad on the circuit board and the surrounding wires and components, thus affecting the stability and reliability of the circuit board.
- Reduced reliability
The pad may be accidentally welded, resulting in component damage or failure. In addition, circuit boards without solder bridges are susceptible to dust, dirt, and moisture, which affects the life and stability of the board.
- Increased manufacturing cost
‌The absence of solder mask bridges increases manufacturing costs as manufacturers need to be more careful in the production process to avoid welding errors and other problems.‌
Solder Mask Alternatives
If you don’t have access to a traditional solder mask, here are some alternatives:
- Kapton Tape – A heat-resistant tape that can act as a temporary solder mask.
- Nail Polish – Some DIY enthusiasts use nail polish as a makeshift solder mask, though it may not be as durable.
- UV-Curable Ink – A popular choice for DIY PCBs, offering good protection and ease of application.
Each alternative has its limitations but can be useful for specific applications.
With over 18 years as an industry leader, Best Technology is one of the most experienced PCB and PCB assembly manufacturer in China. Our highly specialized not only in quick-turn PCB prototype and PCB assembly, but also medium and small volume PCB fabrication. We can provide solder mask on your PCBs, and we will try our best to meet the demands of the solder mask.
If you have any questions, please feel free to contact us with sales@bestpcbs.com, we will be happy to help you.