Ceramic substrate PCB is a crucial component in modern electronics, offering significant advantages in applications requiring high thermal conductivity, electrical insulation, and mechanical strength. In this blog, we will delve into the various aspects of ceramic substrate PCB, explaining its materials, benefits, and applications, and explore how it compare to traditional FR4-based PCB. Whether you are new to PCB design or an experienced engineer, this guide will help you understand why ceramic substrate PCB is gaining popularity.
What is Ceramic Substrate PCB?
Ceramic substrate PCB or ceramic PCB is a type of printed circuit board that uses ceramic materials as the base substrate. Unlike traditional PCBs, which are usually made of fiberglass (FR4), ceramic substrate PCB is designed to handle high thermal stresses and provide better electrical insulation properties. This PCB is commonly used in industries like telecommunications, automotive, medical devices, and power electronics due to their exceptional thermal management capabilities and durability.

The main advantage of ceramic substrate PCBs is their ability to dissipate heat efficiently, which is vital in applications where heat management is a critical factor. Ceramic materials, such as alumina (Al₂O₃), aluminum nitride (AlN), and beryllium oxide (BeO), are known for their excellent heat conductivity, making them ideal for high-power electronics.
What is the Best Substrate for PCB?
The best substrate for a PCB depends on the specific application and the requirements of the circuit. For general-purpose electronics, FR4 is the most commonly used substrate due to its balance of cost and performance. However, for applications that demand superior thermal conductivity, high-frequency performance, or electrical insulation, ceramic substrates are often the preferred choice.
Ceramic substrates are especially suitable for high-power, high-frequency, and high-temperature environments. These materials offer lower thermal expansion rates, higher thermal conductivity, and better resistance to extreme conditions than traditional PCB materials. Therefore, in scenarios where heat management is paramount, such as power amplifiers or LED lighting, ceramic PCBs are the best option.
What Material is Commonly Used for PCBs?
The material commonly used for PCBs can vary depending on the application. The most popular materials include:
FR4 (Fiberglass Reinforced Epoxy): This is the most common PCB material, primarily used for general electronic applications. It is affordable and offers decent mechanical and electrical properties.
Ceramic: As discussed, ceramic materials such as alumina, aluminum nitride, and beryllium oxide are used in high-performance PCBs. They are particularly suited for thermal management and high-frequency applications.
Polyimide: Used for flexible PCBs, polyimide provides excellent resistance to heat and harsh chemicals.
Teflon: Ideal for high-frequency circuits, Teflon offers low signal loss and excellent electrical insulation.
While FR4 is suitable for most basic applications, ceramic substrates stand out when specific performance characteristics like high thermal conductivity or resistance to high temperatures are needed.
Which PCB Substrate Has High Thermal Conductivity?
Ceramic PCBs are known for their superior thermal conductivity compared to other PCB materials. Materials like aluminum nitride (AlN) and boron nitride (BN) have the highest thermal conductivity, making them ideal for high-power applications where heat dissipation is crucial.
Aluminum nitride, for instance, offers thermal conductivity values between 170-200 W/mK, which is significantly higher than that of FR4, which typically ranges around 0.3 W/mK. This makes ceramic substrates the go-to choice for applications such as power electronics, LED lights, and other high-heat applications where heat needs to be efficiently transferred away from the components.
What is the Thermal Conductivity of Ceramic PCB?
The thermal conductivity of ceramic PCBs can vary depending on the material used. The most common ceramic materials include:
Alumina (Al₂O₃): This is one of the most frequently used materials in ceramic PCBs. Alumina has a thermal conductivity ranging from 20 to 30 W/mK, making it suitable for medium-to-high-power applications.
Aluminum Nitride (AlN): Aluminum nitride has a much higher thermal conductivity, typically around 170-200 W/mK. This makes it ideal for high-power applications, especially in areas where rapid heat dissipation is needed.
Beryllium Oxide (BeO): While less commonly used due to safety concerns (due to the toxic nature of beryllium), Beryllium oxide offers very high thermal conductivity, around 250-300 W/mK.
When compared to other PCB materials, ceramic substrates offer a distinct advantage in terms of their heat management capabilities. They ensure that sensitive components remain within their operating temperature range, extending their lifespan and improving performance.
How Thick is Ceramic PCB?
The thickness of a ceramic PCB can vary depending on the design requirements and the specific material used. Typically, ceramic PCBs can range from 0.2 mm to 2 mm in thickness, but in some cases, they can be made thicker or thinner to suit specific needs.
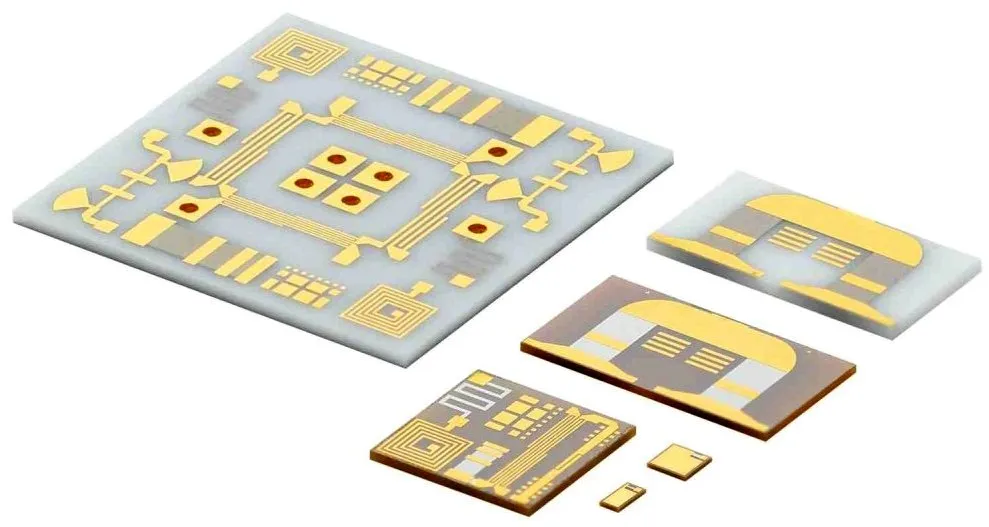
The thickness of the PCB plays a role in both its mechanical strength and thermal properties. Thicker ceramics tend to offer better heat dissipation, but they may be more rigid and difficult to process. On the other hand, thinner ceramics are more flexible but may not handle as much thermal stress. The optimal thickness depends on the application and the required performance characteristics of the circuit.
What is the Difference Between Ceramic Substrate and FR4?
The primary difference between ceramic substrates and FR4 PCBs lies in their material properties and performance characteristics.
Thermal Management: Ceramic substrates excel in heat dissipation, with materials like aluminum nitride offering significantly higher thermal conductivity than FR4. This makes ceramics the better choice for high-power applications.
Electrical Insulation: Ceramic substrates provide superior electrical insulation compared to FR4, making them ideal for applications requiring high voltage isolation.
Mechanical Properties: Ceramic PCBs are often more rigid and can withstand higher temperatures than FR4-based boards, making them suitable for demanding environments.
Cost: FR4 is much cheaper to produce than ceramic substrates, making it the go-to material for mass-produced electronics. However, when performance is the priority, ceramic PCBs provide a much better solution, despite their higher cost.
Overall, the choice between ceramic and FR4 substrates depends on the specific needs of the project. If thermal management, high-frequency performance, or electrical insulation is critical, ceramic substrates are often the better option.
What is Ceramic Board Used For?
Ceramic boards, or ceramic PCBs, are widely used in applications where thermal conductivity, electrical insulation, and mechanical strength are critical. Some of the most common applications of ceramic PCBs include:
Power Electronics: Ceramic PCBs are used in power supplies, inverters, and other high-power circuits, where heat dissipation is crucial for reliable operation.
LED Lighting: Ceramic substrates are used in LED modules, where efficient heat management is essential for preventing thermal damage to the LEDs and improving their lifespan.
Telecommunications: In high-frequency communication equipment, ceramic PCBs help ensure signal integrity and manage heat effectively.
Automotive: Ceramic PCBs are used in automotive electronics, including control systems, power modules, and sensors, which require high thermal conductivity and reliability in harsh environments.
Medical Devices: Ceramic PCBs are used in medical devices such as MRI machines and pacemakers, where high precision and reliability are essential.
The versatility of ceramic PCBs makes them an excellent choice for any application where performance, thermal management, and durability are essential.
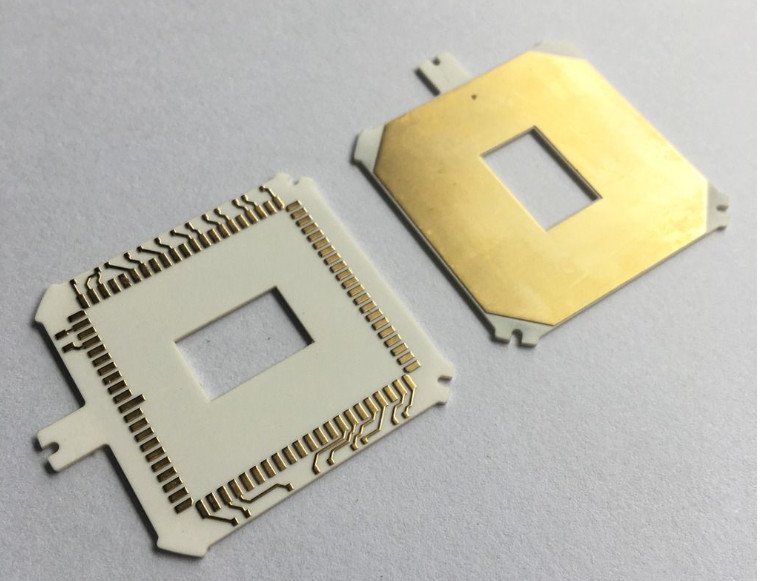
Ceramic substrate PCBs play a vital role in modern electronics, offering superior thermal conductivity, electrical insulation, and mechanical strength compared to traditional FR4-based boards. They are essential in high-power, high-frequency, and high-temperature applications, ensuring that sensitive components operate within their optimal temperature range. While ceramic PCBs tend to be more expensive than FR4, their performance benefits make them the go-to solution for industries where reliability and performance are paramount.
Choosing ceramic PCBs can elevate your designs, particularly when heat management and durability are top priorities. If your application demands top-tier performance, ceramic substrates are a smart investment that ensures long-lasting and efficient operation.
As a ceramic PCB manufacturer, Best Technology specialize in providing high-quality ceramic PCBs tailored to your specific needs. With our advanced manufacturing processes and expert team, we ensure that every PCB we produce meets the highest standards of performance and reliability. If you are looking for dependable ceramic substrate manufacturers, contact us today at sales@bestpcbs.com to learn more about how we can help with your next project.
Tags: ceramic PCB, ceramic substrate pcb, pcb design, PCBA, printed circuit board