If you’re designing high-performance electronics, you’ve probably heard about aluminum-backed PCBs. These boards are not just a trend—they’re solving real-world problems in industries like LED lighting, automotive, and power supplies. Let’s break down what makes them unique and why they might be the perfect fit for your next project.
What Is an Aluminum Backed PCB?
An aluminum-backed PCB (printed circuit board) is a type of metal-core PCB (MCPCB) that uses an aluminum substrate instead of a traditional FR4 base. This layer acts as a heat sink, pulling heat away from components. The design typically includes a dielectric layer, copper circuit layer, and aluminum substrate. Perfect for high-heat applications!
- Copper Circuit Layer – The top layer, made of copper foil, is used for electrical connections and signal transmission. The copper thickness varies from 1oz to 10oz, depending on current requirements.
- Dielectric Layer – A thermally conductive but electrically insulating material separates the copper from the aluminum base. The dielectric layer thickness typically ranges from 75µm to 200µm, balancing insulation and thermal transfer.
- Aluminum Base – This metal substrate serves as a heat sink, drawing heat away from active components. The most common thickness is 1.6mm, though variations from 0.2mm to 3mm exist for different applications.
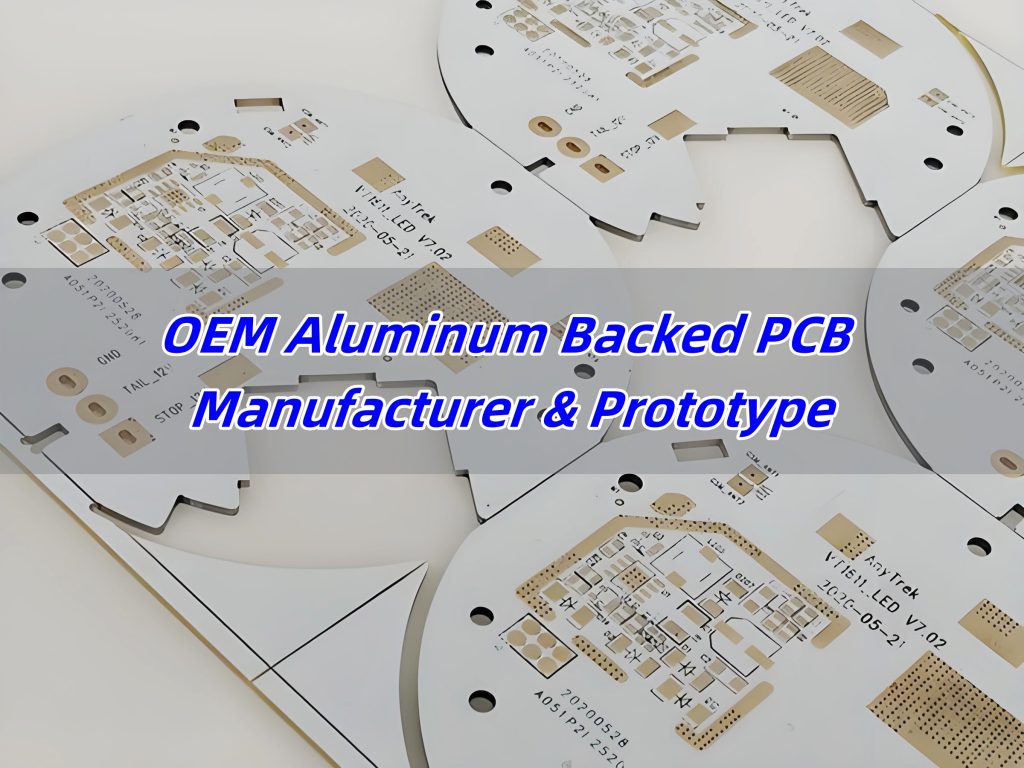
Aluminum PCB vs. FR4 PCB: Which Wins?
FR4 (fiberglass) PCBs are commonly used in consumer electronics, but aluminum-backed boards shine where heat matters. When choosing between aluminum PCBs and FR4 PCBs, key differences must be considered. The table below highlights critical factors that differentiate them:
Parameter | Aluminum PCB | FR4 PCB |
Thermal Conductivity | 1.0–8.0 W/m·K (varies by dielectric material) | 0.3–0.5 W/m·K |
Thermal Expansion | 5–20 ppm/°C (closer to copper) | 14–18 ppm/°C |
Heat Dissipation | Excellent, reduces hot spots | Poor (requires external cooling) |
Mechanical Strength | Excellent due to metal base | Moderate |
Electrical Performance | Consistent, stable | Can degrade under high temperature |
Weight | Heavier than FR4 | Lighter |
Cost | Higher due to metal substrate | Lower |
Note:
- Aluminum conducts heat 8-10 times better than FR4. No more fried components!
- Aluminum resists bending and cracking. FR4 can warp under stress.
- FR4 is cheaper for simple designs. Aluminum saves money long-term by reducing cooling needs.
- Aluminum PCBs last longer in high-temperature environments.
- Choose FR4 for low-cost, low-power projects. Go aluminum for heat-heavy applications like LEDs or power converters.
Types of Aluminum Backed PCBs
Aluminum PCB can be divided into several types according to layer counts or used materials. But they commonly classified by layers:
1. Single-Layer Aluminum PCB
Single layer aluminum backed PCB comprises a single conductive copper layer, a dielectric, and an aluminum substrate.
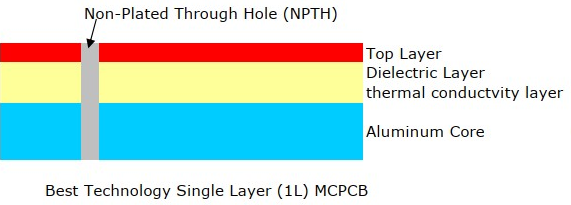
It always called single sided aluminum PCB due to it only has one layer copper trace. It is the simplest metal core PCB design, and it cost-effective due to simple manufacturing. Commonly used in daily LED lighting like swimming pool lighting, office lighting, street lighting…
2. Double-Layer Aluminum PCB
It has two conductive copper layers, generally separated by the aluminum base. But in another case, both the two copper layers can be located on the top of aluminum base, separated by an insulating layer. It can be called single sided two layers aluminum PCB if made in this way.
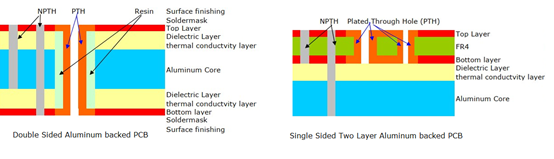
The double layer aluminum PCB provides higher circuit density and improved overall electrical performance. They are commonly used in high power devices where required better heat dissipation like automotive electronics, industrial power modules, and motor control applications.
3. Multilayer Aluminum PCB
Different with multi-layer FR4 PCB, the multi-layer aluminum PCB consists of multiple layers of copper and dielectric materials stacked over the aluminum base. Please see its stack-up as following (4 layers aluminum PCB as example):
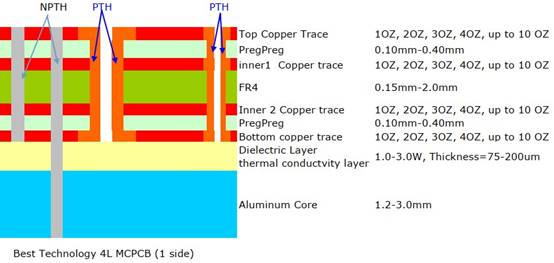
It has more complex circuit designs and is used in high-performance applications such as telecommunication systems and aerospace electronics. Multilayer aluminum backed PCB is rarely used and difficult to manufacture because it requires advanced manufacturing techniques for precise layer alignment and thermal control.
How Thick Is an Aluminum PCB?
Aluminum PCBs come in various thicknesses depending on the application. The most commonly used thickness values are:
- Standard (1.0–1.6 mm): Common in LED lighting and consumer electronics. Lightweight and cost-effective.
- High-Power (2.0–3.0 mm): Used in industrial machinery or EV battery systems. Handles extreme heat and mechanical stress.
- Custom Thickness: Some manufacturers offer tailored solutions. For example, 0.8 mm boards for ultra-slim devices.
Thicker boards improve heat dissipation but increase weight and cost. If it is uncertain, work with your supplier to find the sweet spot.
Why Aluminum PCBs Are Perfect for LED Applications?
Since LEDs generate large heat when working, if unchecked or not install a heat sink, it is easily to shorten their lifespan and dims their output. As a result, aluminum-backed PCBs are widely used in LED lighting as a heat sink. Aluminum PCBs solve this elegantly:
- Cooler LEDs: The aluminum base pulls heat away instantly, keeping junctions 20–30% cooler than FR4.
- Brighter Output: Stable temperatures prevent “lumen depreciation,” ensuring consistent brightness for years.
- Lightweight and Compact: Eliminates bulky heat sinks. reducing size and weight. Enables sleek fixtures for homes, cars, or streetlights.
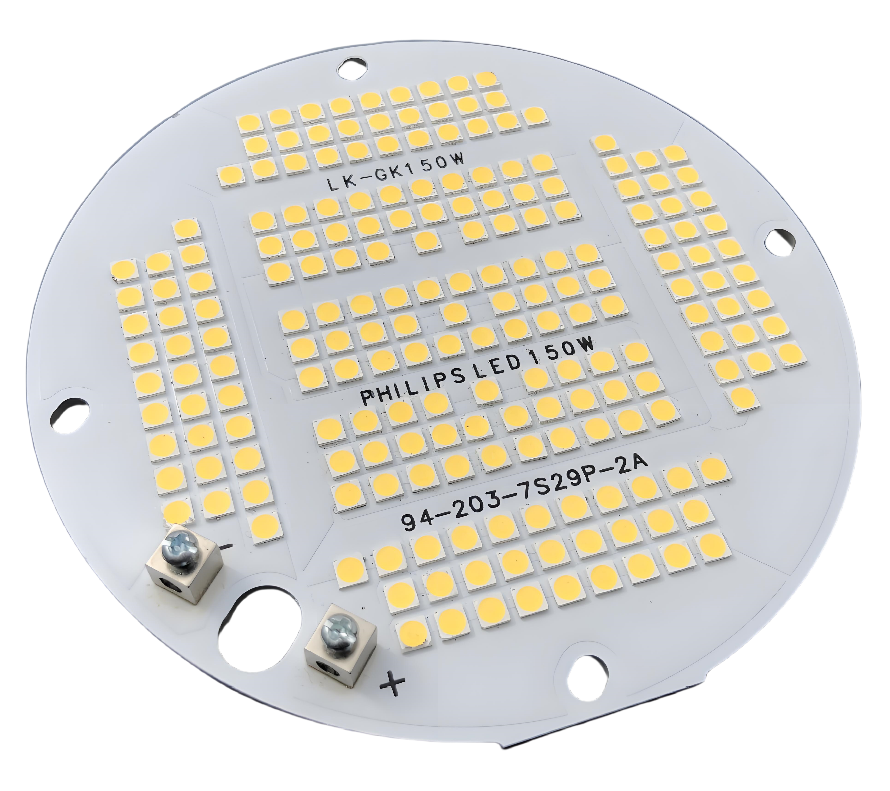
What Temperature Can an Aluminum PCB Withstand?
Most aluminum PCBs handle -55°C to 150°C in a continuous operating temperature. In a short-term peak, it can up to 250°C for limited durations (Please do not try this easily unless you have communicated with your supplier about its maximum temperature). Specialized designs with ceramic-filled dielectrics withstand up to 300°C. Key factors affect its temperature resistance including:
- Dielectric Material: Determines thermal stability and thermal conductivity. Polyimide-based dielectrics excel in extreme heat.
- Component Limits: Even if the board survives, parts like ICs may fail. Always perform FAI (first article inspection) test after full assemblies.
For applications like engine control units or industrial heaters, verify specs with your manufacturer.
What Is the Difference Between Copper and Aluminum PCBs?
Copper is the gold standard for conductivity, but aluminum offers unique advantages:
- Thermal Conductivity: Copper (385 W/m.K) beats aluminum (200 W/m.K), but aluminum is lighter and 30% cheaper.
- Weight: Aluminum is 60% lighter. Critical for drones, EVs, or satellites.
- Cost: Aluminum reduces material and cooling costs. Ideal for high-volume LED or consumer products.
Copper core PCB is a go-to choice for ultra-high-power RF systems, high-power converters, aerospace, while aluminum PCB is suitable for cost-sensitive, weight-conscious designs. Though copper PCBs offer superior thermal conductivity, aluminum PCBs provide a cost-effective solution with sufficient heat dissipation for most high-power applications.
What Is the Cost of an Aluminum Backed PCB?
The cost of an aluminum PCB varies based on layer count, dielectric thickness, and processing complexity.
- Single-Layer Aluminum PCBs: $5–$15 per unit (for standard LED applications).
- Double-Layer Aluminum PCBs: $15–$50 per unit.
- Multilayer Aluminum PCBs: $50–$200 per unit, depending on design complexity.
- Size: A 100x100mm board costs 2–10. Larger sizes increase material use.
- Copper Weight: Heavy copper (4+ oz) adds 15–25% to the price.
- Volume: Ordering 1,000+ units cuts costs by 40–50% through bulk discounts.
Despite their higher initial cost compared to FR4 PCBs, aluminum-backed PCBs eliminate the need for external heat sinks, offering long-term cost efficiency.
Manufacturing Considerations for Aluminum Backed PCBs
Producing aluminum-backed PCBs requires specialized techniques and strict process control to ensure mechanical strength, thermal efficiency, and electrical reliability. The following factors play a crucial role in the manufacturing process:
1. Material Selection
The commonly aluminum base used in industry are 6061, 5052, or 1060 aluminum alloys, each has unique properties. For example, 6061 aluminum has excellent hardness while 5052 is excel in solderability. In addition to this, dielectric material is important since it determines heat dissipation efficiency. Common materials include epoxy, polyimide, and ceramic-filled polymers, offering 1.0 W/m·K to 8.0 W/m·K.
2. Copper Etching
Aluminum PCBs require precision etching due to the thickness of copper layers. Thicker copper layers (>3 oz) require extended etching time and precise chemical control to maintain circuit integrity. Therefore, high-resolution etching equipment is essential to achieve fine-pitch designs and uniformity without excessive undercutting.
3. Drilling and Machining
Due to the hardness of the metal base, carbide or diamond-coated drill bits are used to prevent rapid tool wear and reduce burr formation. Meanwhile, high-speed drilling with controlled feed rates is necessary to avoid damaging the dielectric and copper layers.
4. Insulation and Dielectric Layer Bonding
Layers must adhere without air bubbles. Poor bonding causes delamination under heat.
5. Surface Finishing
HASL (cheap) or ENIG (premium) protect copper from oxidation.
6. Thermal Via Implementation
For multilayer aluminum-backed PCBs, filled or plugged thermal vias improve thermal conductivity while preventing solder migration. Via-in-pad technology enhances heat dissipation for high-power components like MOSFETs and LEDs.
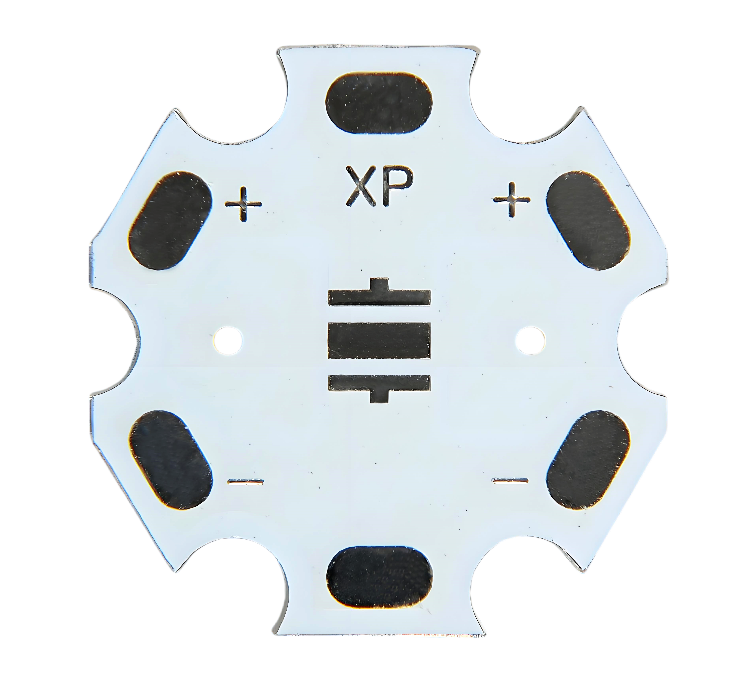
OEM Aluminum-Backed PCB Manufacturers – Best Technology
Best Technology is a leading PCB manufacturer specializing in aluminum-backed PCBs fabrication for LED, power, and automotive applications. With 18+ years of experience, Best Technology offers:
- High-precision CNC milling and drilling for tight-tolerance PCBs.
- Custom thermal via designs for optimal heat dissipation.
- 100% E-test and AOI inspection to ensure zero defects.
- ISO 9001, ISO13485, IATF16949, AS9100D & UL certification, guaranteeing international quality standards.
- Cost-Effective Solutions for OEMs, suit both small-batch prototypes and high-volume production.
- Dedicated R&D team for prototype development and design improvements.
- Strategic partnerships with material suppliers for consistent quality.
- Rapid prototyping services for quick market entry.
- Worldwide shipping with on-time delivery guarantees.
Industries Served by Best Technology
- LED lighting solutions (streetlights, automotive headlights, stadium lights).
- Power electronics (voltage regulators, battery management systems).
- Automotive electronics (ECUs, motor controllers, infotainment systems).
- Industrial control systems (robotics, automation, high-power converters).
- Medical devices (thermal management circuits, high-reliability sensors).
Tags: aluminum backed pcb, aluminum backed pcb manufacturers, oem aluminium backed pcb