Are you looking for aluminum clad PCB solutions? Let’s learn more about aluminum clad PCB’s materials, advantages, specifications, manufacturing steps, production case, differences between copper clad aluminum PCB and aluminum clad PCB as well as how to select a reliable manufacturer.
Best Technology specializes in aluminum clad PCB design and manufacturing, delivering unmatched thermal conductivity (2.5 W/m·K) through precision-engineered copper-aluminum bonding with 99.8% defect-free rates. Our UL 94 V-0 certified boards withstand 1,000+ thermal cycles (-40°C to 150°C), ideal for automotive LED and industrial power systems. With ±0.02mm trace tolerance and AI-optimized panel utilization reducing material waste by 15%, we guarantee rapid 72-hour prototypes and 24/7 engineering support. Trust our 40μm dielectric layer control (±2μm) to eliminate high-voltage arcing risks while maintaining 2oz copper thickness consistency. Submit your design now for a free thermal simulation report within 4 hours: sales@bestpcbs.com.
What Is Aluminum Clad PCB?
An aluminum clad PCB, also known as an aluminum-based PCB or MCPCB (Metal Core PCB), is a specialized type of PCB that integrates a metal core (typically aluminum) as its base layer. Unlike standard FR-4 PCBs, which rely on glass-reinforced epoxy laminates, aluminum clad PCBs leverage the metal’s superior thermal conductivity to dissipate heat efficiently.
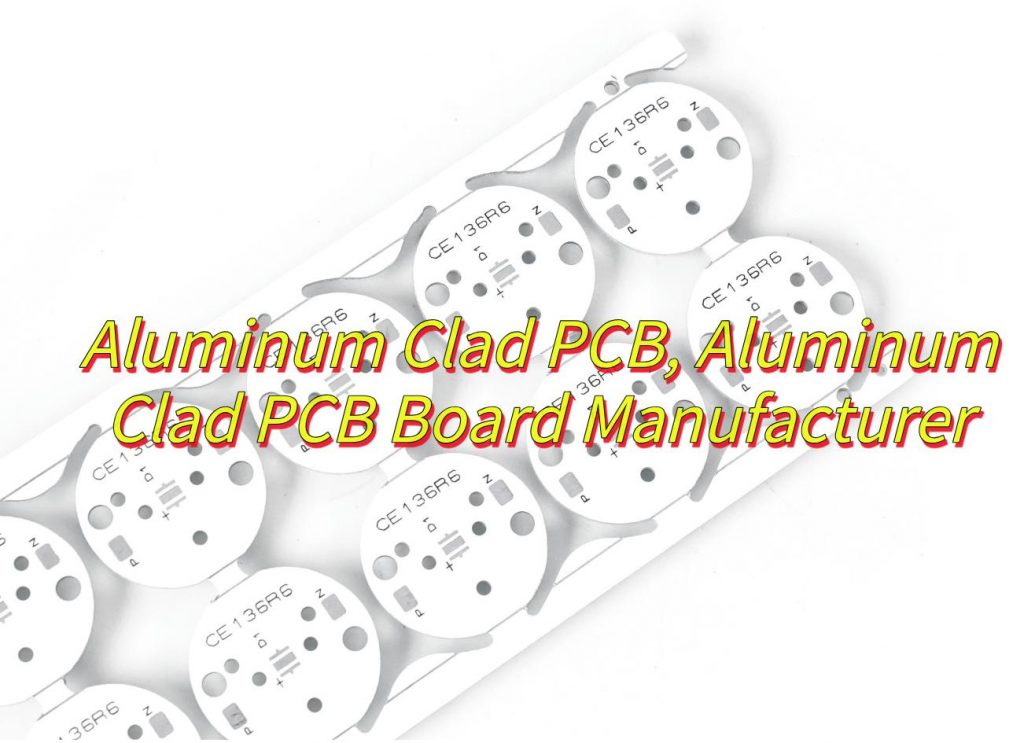
What Are Materials of Aluminum Clad PCBs?
- Copper foil: Copper foil has excellent electrical conductivity and is the main conductive layer of the circuit. When current passes through the copper-clad laminate, the current mainly flows in the copper foil layer, thereby realizing the conductive function of the circuit.
- Electronic fiberglass cloth: As a reinforcing material, it provides mechanical strength and stability to the board.
- Resin: As an insulating adhesive layer, it prevents current leakage and short circuit, ensuring the electrical safety of the circuit.
- Aluminum substrate: Provides good thermal conductivity, helps dissipate the heat generated by the circuit, and ensures the stability and reliability of electronic equipment when running at high power.
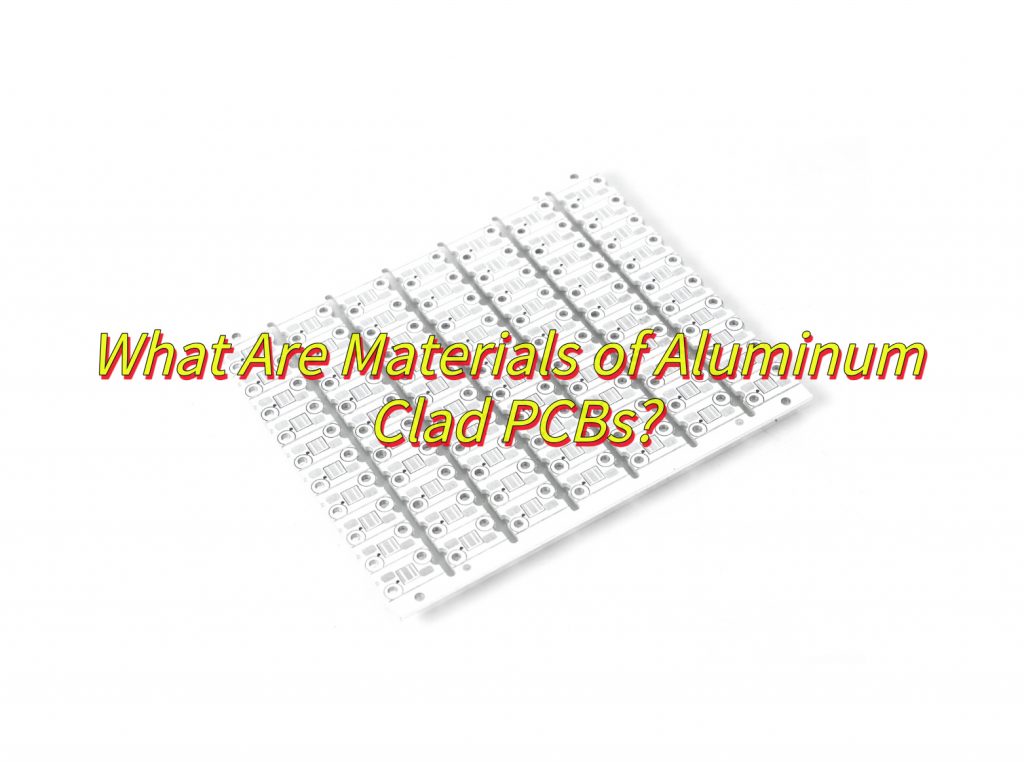
What Are Advantages of Aluminum Clad PCB board?
- Excellent thermal conductivity: Aluminum-based copper-clad laminates have excellent thermal conductivity, which can effectively reduce the operating temperature of electronic devices and improve the stability and reliability of equipment.
- Good welding performance: The copper foil layer provides good welding performance, which is convenient for the assembly and repair of circuit boards.
- High mechanical strength and corrosion resistance: Aluminum-based copper-clad laminates have good mechanical strength and corrosion resistance, and can maintain stable performance in harsh environments.
- High conductivity: The copper foil layer provides good conductivity, which is suitable for high-frequency, high-speed, and high-heat dissipation electronic devices. Lightweight and corrosion-resistant: Aluminum-based copper-clad laminates combine the lightness of aluminum and the conductivity of copper, which is suitable for various electronic devices.
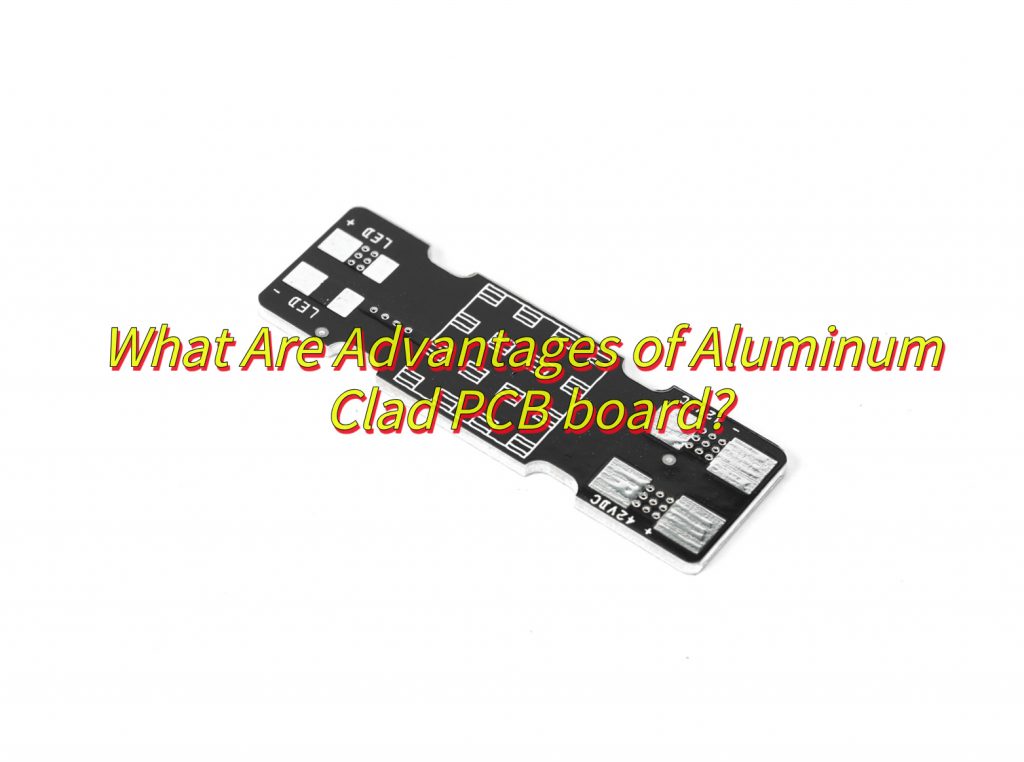
What Are the Specifications for Aluminum Clad PCBs?
Here are aluminum clad PCB specifications:
Base Layer:
- Material: 5052/6061 aluminum alloys (1.0–3.2 mm thickness).
- Thermal Conductivity: 5–10× higher than standard FR-4 substrates.
- Structural Role: Provides rigidity and prevents warping in high-stress environments.
Insulation Layer
- Material: Epoxy-based polymers or ceramic-filled dielectric (50–200 µm thick).
- Thermal Conductivity: 1.5–8.0 W/m·K, balancing electrical isolation and heat transfer.
- Breakdown Voltage: >3 kV to prevent circuit shorting.
Circuit Layer
- Copper Foil: Electrolytic copper (1–10 oz) for high-current traces.
- Peel Strength: ≥1.5 kgf /cm after thermal cycling (230°C).
Electrical Performance
- Power Loop Inductance: Minimized design for GaN-HEMT modules to reduce switching losses.
- High-Frequency Stability: Low parasitic inductance/resistance for RF and power applications.
Thermal Metrics
- Thermal Resistance: 60–80% lower than FR-4, critical for >10W/cm² heat dissipation.
- Cooling Efficiency: Supports continuous operation in power converters and LED modules.
Compliance & Manufacturing
- Standards: Meets UL 94V-0 flame resistance and RoHS directives.
- Compatibility: Optimized for SMT assembly and multichip module integration.
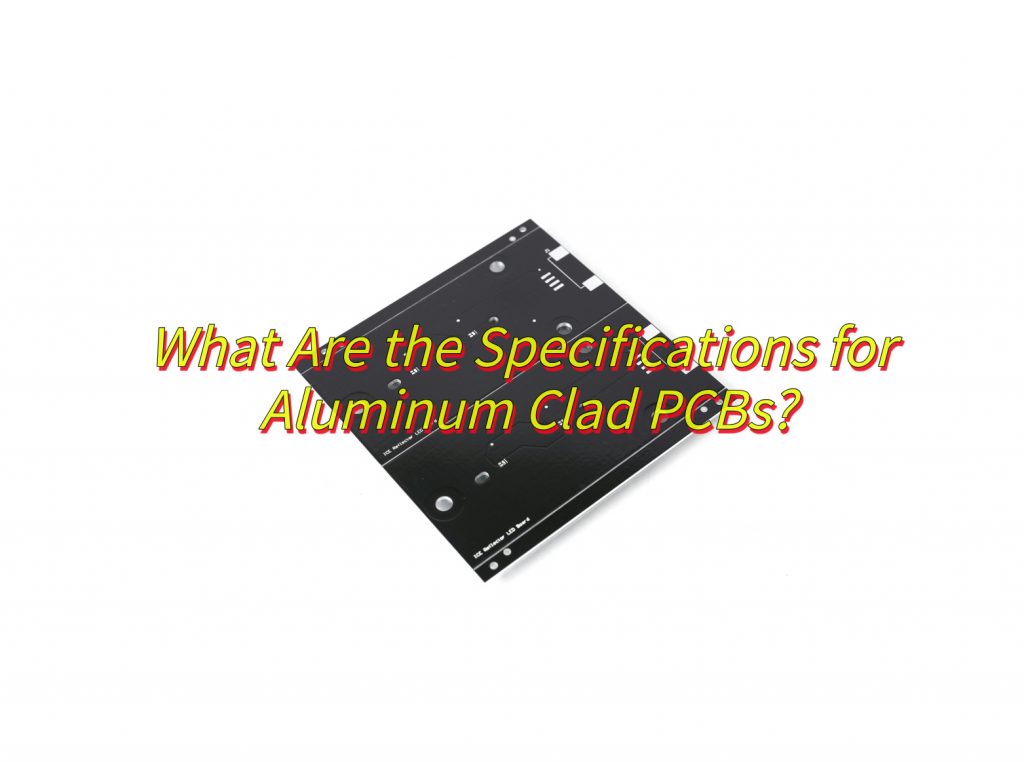
What Are the Steps to Manufacture Aluminum Clad PCB Boards?
Here are steps to manufacture aluminum clad PCB boards:
1. Material Preparation
- Aluminum Base: Select high-purity aluminum (e.g., 1060 alloy) or alloys tailored for thermal conductivity and mechanical strength.
- Dielectric Layer: Choose a material with high thermal conductivity (e.g., 1–10 W/m·K) and electrical insulation properties (e.g., ceramic-filled polymers or epoxy resins).
- Copper Foil: Use thick copper (1–10 oz) for high-current applications, ensuring compatibility with the dielectric layer.
2. Lamination
- Layer Stacking: Combine the aluminum base, dielectric layer, and copper foil in a press under controlled temperature and pressure.
- Bonding: Use adhesives or prepregs to ensure strong adhesion between layers, avoiding delamination during thermal cycling.
3. Drilling
- Hole Formation: Create via holes and component mounting holes using specialized drills designed for aluminum to prevent burrs and maintain hole quality.
- Deburring: Remove sharp edges and debris to ensure smooth plating and assembly.
4. Plating
- Chemical Deposition: Apply a thin copper layer to the hole walls via electroless plating to enable electrical conductivity.
- Panel Plating: Thicken the copper layer using electrolytic plating to meet current-carrying requirements.
5. Imaging and Etching
- Photoresist Application: Coat the copper surface with a photosensitive material and expose it to UV light through a circuit pattern mask.
- Development: Remove unexposed photoresist to reveal the copper traces for etching.
- Etching: Use acidic or alkaline solutions to selectively remove unwanted copper, leaving the desired circuit pattern.
6. Solder Mask Application
- Coating: Apply a liquid photo imageable solder mask (LPI) or dry film solder mask to protect the copper traces from oxidation and solder bridges.
- Curing: Harden the solder mask via UV exposure or thermal baking to ensure durability.
7. Surface Finish
- Finishing Options: Apply ENIG (Electroless Nickel/Immersion Gold), HASL (Hot Air Solder Leveling), or OSP (Organic Solderability Preservative) to enhance solderability and corrosion resistance.
8. Silkscreen Printing
- Labeling: Print component labels, logos, and other markings using UV-curable ink for clarity and durability.
9. Routing and V-Scoring
- Contouring: Use a CNC router or V-scoring machine to separate individual PCBs from the panel while maintaining structural integrity.
10. Electrical Testing
- Functional Testing: Verify circuit continuity, insulation resistance, and functionality using flying probe or bed-of-nails testers.
- Thermal Testing: Simulate operating conditions to ensure the aluminum core effectively dissipates heat.
11. Final Inspection and Packaging
- Quality Control: Inspect for defects such as delamination, voids, or plating issues using automated optical inspection (AOI) or X-ray systems.
- Packaging: Protect finished PCBs with anti-static bags, moisture barriers, and cushioning materials to prevent damage during shipping.
Can You Share OEM Aluminum Clad PCB Success Cases?
Here is a case of OEM aluminum clad PCB:
Case Study: High-Power LED Lighting Module Manufacturing
Client: A global LED lighting manufacturer seeking to improve product reliability and reduce failure rates in high-brightness LED applications.
Challenges:
- Overheating issues in existing FR4-based PCBs, leading to premature LED degradation.
- Need for a cost-effective solution to scale production while maintaining thermal performance.
Solution: OEM Aluminum Clad PCB Production
Material Selection:
- Aluminum Base: 1060 alloy (99.6% purity) for optimal thermal conductivity (201 W/m·K).
- Dielectric Layer: Ceramic-filled epoxy resin with 1.5 W/m·K thermal conductivity and 250°C glass transition temperature.
- Copper Foil: 2 oz (70 μm) thickness for high current-carrying capacity.
Main Manufacturing Steps:
- Lamination: Precision bonding of layers under 180°C and 200 kg/cm² pressure to ensure void-free adhesion.
- Drilling: Carbide drills with 0.3 mm diameter to prevent burrs and maintain hole quality.
- Plating: Electroless nickel/immersion gold (ENIG) finish for corrosion resistance and solderability.
- Thermal Testing: Simulated 120°C operating conditions to validate heat dissipation efficiency.
Quality Assurance:
- Thermal Cycling: -40°C to 125°C, 1,000 cycles with <5% resistance drift.
- Thermal Resistance (Rθ): Measured at 1.2°C/W, a 70% improvement over FR4 PCBs.
- Failure Rate: Reduced from 8% to <0.5% in accelerated life tests (10,000 hours at 105°C).
Results:
- Cost Savings: 15% reduction in manufacturing costs through streamlined processes and material efficiency.
- Market Impact: The client secured contracts with major automotive and architectural lighting brands, expanding market share by 25%.
- Reliability: Zero field failures reported in the first 18 months of deployment.
How to Select A Trusted Aluminum Clad PCB Board Manufacturer?
Here are some ways to how to select a reliable aluminum clad PCB manufacturer:
Technical Capability Validation
- Require manufacturers to disclose core specifications:
- Thermal resistance ≤0.5°C·in²/W
- Minimum trace width/spacing ≤75μm
- Multi-layer hybrid bonding capabilities (e.g., FR-4 + aluminum substrate)
- Verify precision equipment ownership:
- Laser Direct Imaging (LDI) systems for ±0.01mm alignment
- Automated etching lines with ±3% copper thickness control
Quality Certifications & Testing
- Mandatory certifications:
- UL94 V-0 flammability rating
- ISO 9001:2015 with valid audit reports
- On-site inspection focus:
- AOI defect detection accuracy (≤15μm anomalies)
- Thermal shock test range (-40°C to 150°C, 100+ cycles)
- Real-time CPK monitoring (≥1.33 for critical processes)
Supply Chain Transparency
- Raw material traceability:
- Aluminum substrates from certified mills
- Copper foil thickness tolerance ≤±3% (3oz+)
- Production flexibility:
- 24-hour rapid prototyping capability
Cost Optimization Strategies
- Demand technical documentation:
- Thermal simulation reports proving ≥30% heat sink cost reduction
- Panel utilization rate ≥92% via intelligent nesting software
- Evaluate standardized process packages for:
- 10-15% lower NRE costs on small batches
- ±5μm dielectric layer consistency
Engineering Responsiveness
- Verify service protocols:
- 2-hour emergency technical support
- 24-hour design change implementation
- Access to failure mode database (50+ aluminum PCB case studies)
- Demand DFM feedback within 4 work hours for:
- Impedance control (±8%)
- Warpage control (≤0.3% on 300mm boards)
What Are Differences Between Copper Clad Aluminum PCB and Aluminum Clad PCB?
Here’s a structured analysis of differences between copper clad aluminum PCB and aluminum clad PCB:
Material Composition & Structure:
- Aluminum Clad PCBs: Consist of an aluminum substrate with a dielectric layer and copper foil on top. The aluminum acts as the primary heat dissipater, while the copper layer facilitates electrical conductivity.
- Copper Clad Aluminum PCBs: Feature copper-plated aluminum conductors (CCA wires) embedded within the board. The aluminum core reduces weight and cost, while the copper layer ensures adequate conductivity.
Thermal Performance:
- Aluminum Clad PCBs: Excel in heat dissipation due to aluminum’s high thermal conductivity (1.0–2.0 W/m·K), making them ideal for high-power applications like LED lighting and power modules.
- Copper Clad Aluminum PCBs: Offer moderate thermal performance. While aluminum aids heat transfer, the copper layer’s thermal conductivity is limited by its thickness, making them less effective than pure aluminum or copper substrates in high-heat scenarios.
Electrical Conductivity:
- Aluminum Clad PCBs: Provide excellent conductivity via the copper foil layer, suitable for high-frequency signals and large currents.
- Copper Clad Aluminum PCBs: Have lower conductivity than pure copper due to the thinner copper layer. This may impact signal integrity in high-frequency applications, requiring careful design considerations.
Cost:
- Aluminum Clad PCBs: Generally more expensive than CCA PCBs due to the use of copper foil and specialized dielectric materials.
- Copper Clad Aluminum PCBs: Offer cost savings of 30–50% compared to pure copper boards, making them attractive for budget-conscious projects without extreme thermal demands.
Mechanical Strength & Durability:
- Aluminum Clad PCBs: Robust and resistant to deformation, withstanding mechanical stress and vibration. However, they are heavier than CCA PCBs.
- Copper Clad Aluminum PCBs: Lighter and more flexible due to the aluminum core, but may be less durable under high mechanical stress. The bond between copper and aluminum can also affect long-term reliability.
Manufacturing Complexity:
- Aluminum Clad PCBs: Require specialized processes like chemical etching and precise dielectric lamination, increasing production complexity and lead times.
- Copper Clad Aluminum PCBs: Are generally easier to manufacture, as standard PCB processes can be adapted for CCA conductors.
Applications:
- Aluminum Clad PCBs: Preferred in high-power electronics, automotive lighting, and industrial controls where heat management is critical.
- Copper Clad Aluminum PCBs: Suitable for consumer electronics, telecom devices, and lighting applications where cost and moderate thermal performance are priorities.
Reliability & Lifespan:
- Aluminum Clad PCBs: Offer longer lifespans due to aluminum’s corrosion resistance and stable dielectric properties, especially in harsh environments.
- Copper Clad Aluminum PCBs: May require additional protective coatings to prevent oxidation of the aluminum core, which could impact long-term reliability.
In summary, that’s all about aluminum clad PCB’s materials, advantages, specifications, manufacturing steps, production case, differences between copper clad aluminum PCB and aluminum clad PCB as well as how to select a reliable manufacturer. If you want to learn more about aluminum clad PCB, welcome to leave a message below this blog. Looking forward to hearing from you!
Tags: Aluminum Clad PCB