Copper Core Metal Core PCB Definition
A copper metal core PCB is a circuit board that using a copper substrate as its base. Unlike standard FR4 boards, it offers better thermal conductivity and enable to manage high temperatures in demanding electronics. It is primarily used in LED lighting, power electronics, and automotive systems. The copper base improves heat dissipation and reduces thermal stress on components.
In these PCBs, copper doesn’t just act as a trace layer. It becomes the core, ensuring mechanical strength and thermal stability. The copper layer can range in thickness based on heat dissipation needs.

Copper Core PCB Structure
The structure of a copper core PCB includes three key layers:
Copper base layer – This is the thick metal sheet at the bottom, used to transfer heat efficiently.
Dielectric layer – This insulating layer sits between the copper base and the circuit layer. It ensures electrical isolation while allowing heat to pass through.
Circuit layer – This is the top layer where traces and components are mounted. It’s usually made of copper foil, etched to form the required circuit paths.
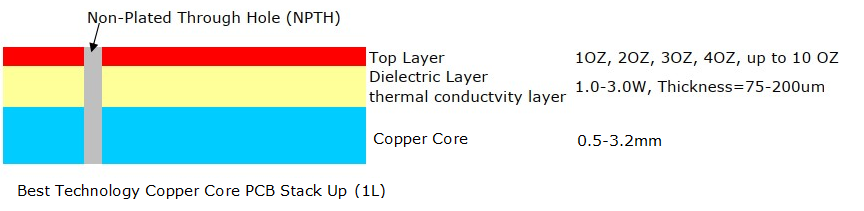
If it is a double-sided copper core PCB, then the copper core located at the center, and bottom layers is the same as top layer – dielectric layer and copper trace layer.
Types of Copper Core PCB
Copper core PCB can be divided into two different types, the normal copper PCB and sinkpad copper PCB.
- Normal Copper Core PCB
This is the most basic version. The structure of normal copper PCB is the same as aluminum core PCB. It consists of the standard three layers mentioned above. It’s simple, effective, and often used in applications where heat needs to be controlled but not aggressively dissipated.
- SinkPad Copper-Based PCB
The sinkpad copper PCB also called thermoelectric separation copper-based PCB. This type of PCB offers more advanced thermal management, up to 400W/m.k. It has a sinkpad we called convexity, which creates a direct thermal path from the heat source (like an LED chip) to the copper core. It removes the barrier between the heat source and the copper base, dramatically improving heat transfer. These boards are often found in high-performance LED lighting, power modules, and heavy-duty electronics.
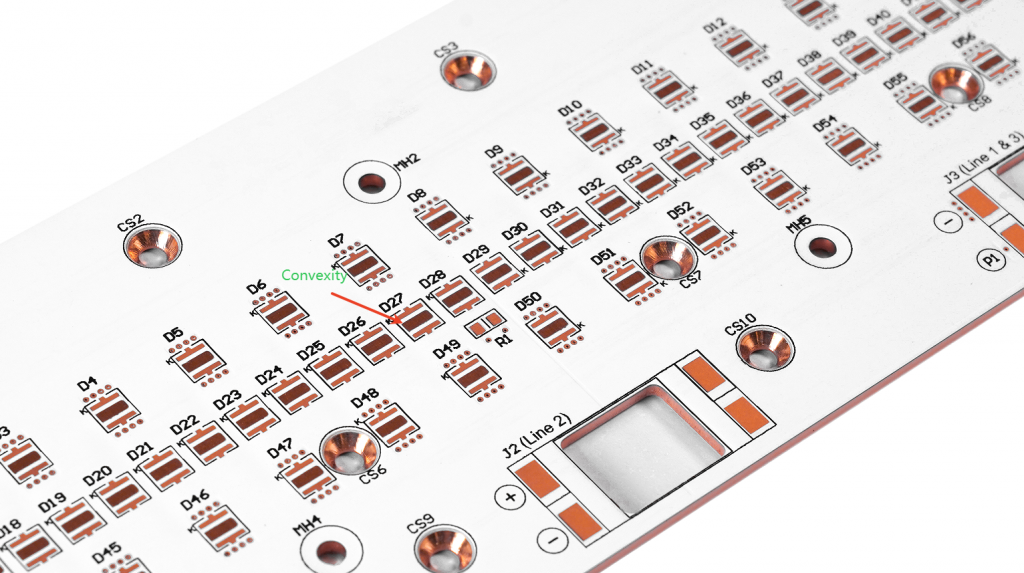
Sinkpad copper-based pcb stack up:
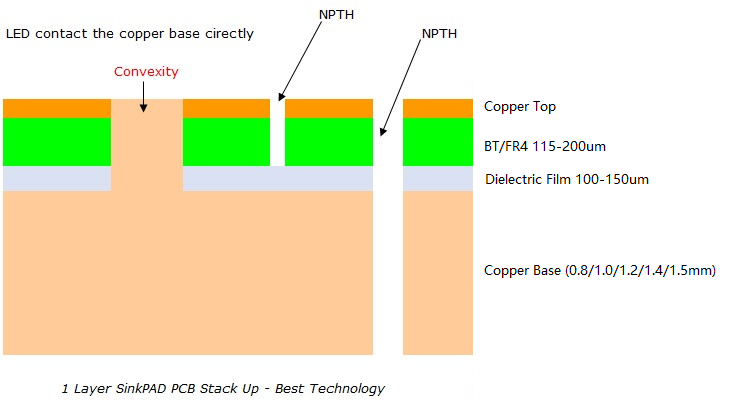
Features of Copper Core PCB
- Superior heat dissipation than aluminum PCB, thermal conductivity up to 400W/m.k.
- Stable dimensional, resistant to bending, warping, or mechanical stress.
- Extend the lifespan of components by keeping temperatures low and stable
- Reliable heat transfer, vital for LEDs, power amplifiers, and high-voltage devices.
- High durability under harsh conditions
- Stable electrical performance
Copper Metal Core PCB Design Guidelines
1. Identify heat-generating components early like LED chips and position them close to the copper base or over thermal vias. This way, heat can flow downward into the copper core instead of building up on the surface.
2. The thickness of the copper core can vary from 0.5mm to 3.2mm or even more. Thicker cores handle more heat but also make the board heavier and harder to machine. Choose a thickness that fits your heat dissipation needs without over-engineering the design.
3. If you’re creating a multi-layer board with copper core, make sure your layer stack-up supports signal integrity and EMI shielding. Keep high-speed signals away from noisy power planes and include ground layers where needed.
4. Put heat-sensitive parts like sensors, microcontrollers, or delicate analog chips far from high-power elements like MOSFETs or power LEDs.
5. Copper is harder than aluminum or FR4. Make sure your PCB manufacturer is equipped to handle precise drilling and milling of copper-based substrates without damaging the boards.
6. Before finalizing the design, use simulation tools to predict how heat will spread across the board.
Copper Metal Core PCB Applications
- High power LED (up to 200W)
- Automotive electronics like power control modules, headlight systems, and battery management
- DC-DC converters, MOSFET drivers, motor controllers
- Drives, inverters, and heavy machinery
- Telecommunication systems
- Medical devices – In imaging and surgical tools
How to Choose Copper Core PCB Factories?
Not all copper core PCB factories are the same. Here’s what to look for:
- Experience – Look for manufacturers with years in metal-core PCB production.
- Material sourcing – Ask where they get their copper and dielectric materials.
- Precision capabilities – Can they handle tight tolerances and advanced designs?
- Thermal testing – Make sure they offer in-house thermal testing or simulation.
- Customization – They should be able to tweak thickness, layers, or designs as needed.
- Certifications – ISO9001, UL, and RoHS are a good start.
A good partner won’t just make your board—they’ll improve your product.
Top 10 Copper Core PCB Manufacturers (In No Particular Order)
When it comes to sourcing high-quality copper core PCBs, choosing the right manufacturer is crucial for ensuring thermal efficiency and long-term reliability. Here are ten trusted names in the industry, known for their expertise in copper metal core PCB production:
1. Adwin Circuits
Looking for something highly customized? Adwin Circuits is a solid choice if your project needs detailed attention. They’re known for working closely with customers to get everything just right, especially on the thermal side.
2. PCBgogo
Need your boards fast and don’t want to break the bank? PCBgogo is super popular for a reason. They’re fast, affordable, and make it easy to order online—even for copper core options.
3. Millennium Circuits Limited (MCL)
Based in the U.S., MCL focuses on high-quality builds with short lead times. If you’ve got a tight deadline and still want top-notch results, they’re definitely worth considering.
4. Best Technology
With over 18 years in the industry, Best Technology really knows their stuff when it comes to metal core and copper-based PCBs or sinkpad PCB. They handle everything—from design advice to assembly—and specialize in custom builds for demanding applications like LED lighting and power electronics. As an expert, they know what you want and make it into reality.
5. PCBWay
If you’ve ever ordered a PCB online, chances are you’ve heard of PCBWay. They make the whole process super smooth and have a good track record for copper metal core PCBs too. Great support and flexible pricing make them a go-to for hobbyists and professionals alike.
6. Sierra Circuits
These folks are based in California and have a strong reputation in industries like aerospace and medical tech. If you need a copper core board that meets tight specs or certifications, Sierra’s a good fit.
7. JLCPCB
One of the biggest names in online PCB manufacturing, JLCPCB is known for rock-bottom prices and quick delivery. Their copper core options are great for early prototyping and scaling up later.
8. FX PCB
FX PCB is another good option if your project needs serious thermal management—especially in LED lighting or high-power circuits. They’re all about balancing price and performance.
9. PCBONLINE
This one’s a full-service provider, so if you need a one-stop-shop—from bare board to final assembly—they’ve got you covered. Their copper core offerings are strong, and they’ve got solid quality control in place too.
10. Leiton GmbH
If you’re based in Europe or need a manufacturing partner closer to home, Leiton GmbH is a solid German company. They’re known for attention to detail and reliable builds, especially for industrial applications.
Why Choose Best Technology as Your Copper Core PCB Supplier?
Best Technology offers a full-service experience for all copper PCB needs.
Copper Metal Core PCB Prototype
Quick-turn copper metal core PCB prototypes are available for engineers looking to validate thermal designs. Prototyping services include design feedback, material consulting, and fast delivery, even for complex builds.
Copper Metal Core PCB Assembly
Complete copper metal core PCB assembly is available in-house. From surface mount to through-hole soldering, every board is built to exact specifications. Inspection services like AOI, X-ray, and functional testing guarantee reliability.
FAQs
1. What is the advantage of using a copper core PCB over an aluminum core PCB?
Copper conducts heat better than aluminum. It also supports higher mechanical strength and is suitable for high-performance applications.
2. Can copper core PCBs support multilayer designs?
Yes. Copper core boards can be designed as multilayer PCBs. They often include signal, ground, and power planes with efficient heat sinking.
3. What is the typical copper thickness for these boards?
Copper base thickness ranges from 0.5mm to 3.2mm. Circuit layers usually vary between 1oz and 6oz depending on current load.
4. Are copper metal core PCBs expensive?
Yes, they cost more than FR4 boards due to material and process complexity. However, they reduce cooling costs and extend device life, offering long-term value.
5. How can I request a quote from a copper core PCB manufacturer?
Send your Gerber files, BOM list, and specifications to the manufacturer. Then our sales will provide pricing based on volume, complexity, and delivery timelines.
Tags: Copper core pcb factories, Copper core pcb manufacturer, copper metal core pcb