What is Design for Manufacturing (DFM)?
Design for manufacturing, or DFM, is the process of designing products with ease of manufacturing in mind. It focuses on making products that are not only functional but also simple to build. When DFM is done well, it helps reduce production costs, shortens the time to market, and improves quality.
At its core, DFM is about creating designs that match the capabilities of the manufacturing process. Engineers and designers can work together with manufacturers early in the process. So that engineer can identify potential problems before mass production or prototype, save much time for customers.
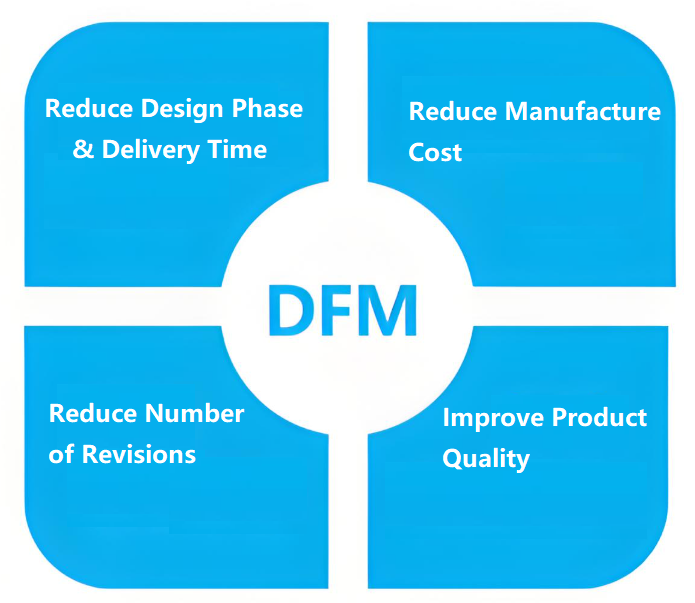
3 Goals of DFM
1. Cost Reduction
By optimizing the design, you can reduce waste, material usage, and labor. Simple shapes, fewer parts, and efficient processes lead to lower costs.
2. Faster Production
Well-designed parts are easier to manufacture. This leads to shorter cycle times and quicker delivery. Less rework and fewer changes speed things up too.
3. Improved Product Quality
DFM encourages consistency. It minimizes variation and errors during production. As a result, you get a higher-quality end product that performs reliably.
Perform DFM before manufacturing can detect potential defectives that we can’t detect, it covers three aspects, including:
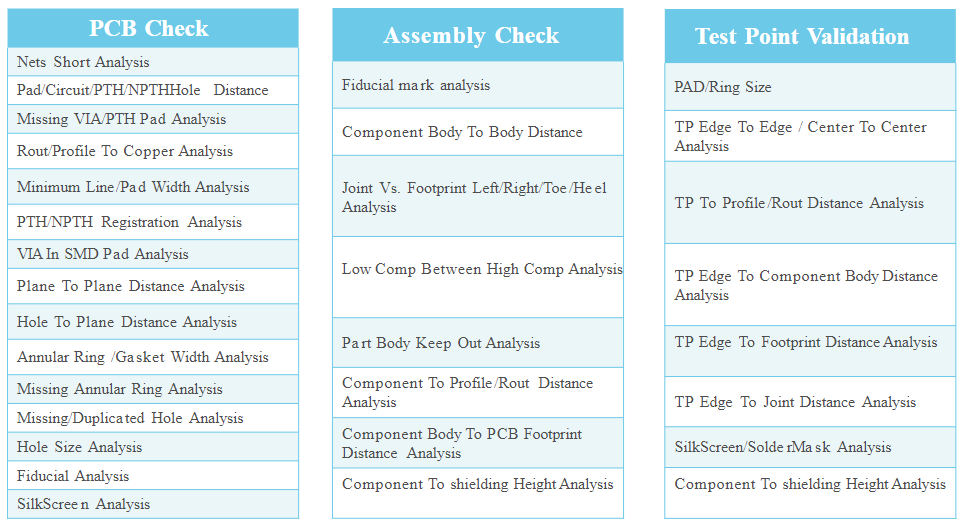
What are the 5 Principles of Design for Manufacturability?
1. Reduce the number of parts/components
By simplifying the design, reducing the number of parts can reduce manufacturing costs and complexity and improve production efficiency. For example, combining multiple parts into one not only reduces the chance of errors, but also saves assembly time and development time.
2. Standardized design
The use of standardized components and design elements helps to reduce production variability and improve product consistency. Standardized design can reduce design time, improve assembly efficiency, and reduce research and development costs.
3. Simplify the assembly process
Considering the convenience of assembly during design can reduce assembly time and cost. Through modular design, the same set of parts can be used alternately, reducing the dependence on specific molds, thereby reducing production costs.
4. Material selection
Select the appropriate material to ensure the manufacturability and performance of the product. Reasonable material selection can not only improve product reliability, but also reduce manufacturing costs.
5. Manufacturing tolerances
Reasonably set manufacturing tolerances to balance manufacturing costs and product quality. Proper tolerance setting can ensure product quality and reduce production costs at the same time.
What is the Difference Between DFM and DFMA?
It’s easy to mix up DFM and DFMA. They’re closely related but serve slightly different purposes.
DFM (Design for Manufacturing) focuses on manufacturing, refers to the design for manufacturing, mainly focuses on how to simplify the parts processing process through design, reduce the difficulty and cost of manufacturing. Its core goal is to optimize designs and make them easier to manufacture while improving product quality. DFM focuses on parts processing, reducing manufacturing difficulties through design optimization, such as reducing complex processes and avoiding strict tolerances.
DFMA (Design for Manufacture and Assembly) combines the principles of DFM and DFA (Design for Assembly) to optimize the manufacturing and assembly process of products to reduce costs, increase efficiency and improve product quality. DFMA not only focuses on manufacturing, but also on assembly, emphasizing the comprehensive consideration of manufacturing and assembly optimization in the design stage, such as reducing the number of parts, simplifying the assembly process, etc.
In short:
DFM = Can we make this part easily?
DFMA = Can we make and assemble this product easily?
Common Defective Issues Detected by DFM
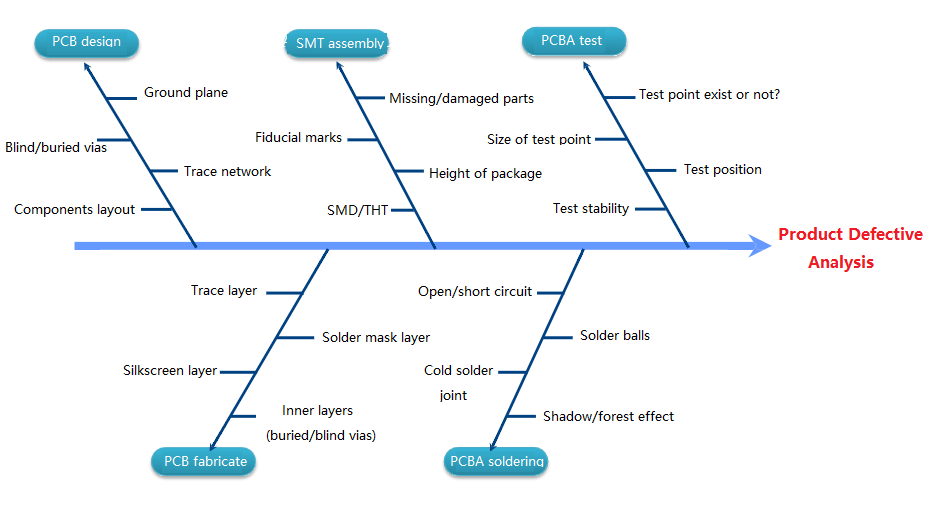
How to Perform Design for Manufacturing DFM?
Performing DFM is not a one-step process. It’s a mindset that should be part of every stage of product development.
1. Engage Early with Manufacturers
Bring in manufacturing experts during the design phase. Their insights help prevent rework and delays later.
2. Evaluate the Design for Each Process
Check if the design works well with cutting, forming, molding, or other methods. Each process has its strengths and limits.
3. Reduce Part Counts
Combine parts where possible. Fewer parts mean fewer connections, less inventory, and easier builds.
4. Analyze Tolerances
Use realistic tolerances. Too-tight specs increase cost and difficulty. Focus on where precision is truly needed.
5. Review Materials and Finishes
Pick materials that are easy to source and suitable for the environment. Avoid special coatings unless they’re vital.
6. Prototype and Test
Use early builds to check for problems. Make improvements based on real data, not just models. DFM is about iteration. Keep refining until the design fits both function and production.
What Should You Consider When Designing for Manufacture?
When designing for manufacturing, many small details matter. These are the key areas to watch:
- Avoid complexity design. Keep PCB simple and easy to shape.
- Design parts that work well with available tools. Custom fixtures can slow things down.
- Think about how the part will be handled. Can it be picked up, rotated, and fixed easily?
- Check how tolerances from one part affect the whole system. Misalignment can come from small errors that add up.
- Use materials that match the product’s goals—strength, weight, heat resistance—but also consider cost and ease of use.
- Don’t ask for polished surfaces unless needed. Extra finishing steps raise cost and time.
- Are the parts easy to source? If not, you may face delays or searching for alternative parts.
- High-volume parts benefit from different methods than low-volume ones. Tailor your design to the production level.
Get Free DFM Support with Best Technology
At Best Technology, we support your design goals from the first sketch to the final board. We offer one-on-one support, PCB fast prototyping, and clear communication every step of the way. After getting your design files, we will perform design for manufacturing analysis, and send the report to you to optimize the design. Our service including:
1. PCB manufacture
FR-4 PCB, High TG FR-4 PCB, Heavy copper PCB, Impedance control PCB, High frequency PCB, Flexible PCB, Rigid-flex PCB, HDI PCB, Aluminum PCB, Copper based PCB, Ceramic based PCB, high speed PCB, IC substrate
2. PCB assembly
SMT, DIP, reflow soldering, Wave soldering, Hand soldering, Mixed assembly, wire harness assembly, PCBA testing, box building assembly
3. Components sourcing
Firsthand components, original manufacturers, BOM checking, components sourcing, IQC checking, ISO9001 certificated
4. PCBA design and duplication
Hardware engineers, Software engineers, Schematic design, PCB layout, Software development, PCBA duplication
Whether you need help choosing the right PCB & PCBA manufacturer or searching for a cost-effective solution, we’re here. In our next article, we will share acknowledges about design for assembly (DFA), if you are interested about it, please collect our website or leave your message at comments.
Tags: design for manufacturability, DFM