Are you looking for a LED street light PCB manufacturer with design service? Let’s learn more about advantages, design processes of LED street light PCB, and how to design it for better heat dissipation and lower cost, as well as how to select a good LED PCB supplier.
Best Technology specialize in LED street light PCB design and manufacturing over 18 years. We use a fully automated SMT production line and AOI/X-ray inspection system, and has imported YAMAHA patch machines to ensure that the LED street light PCB patch accuracy can reach ±0.035mm, and the mounting speed can reach 95,000 points/h. Based on the 30W+ high-power heat dissipation requirements, the design end can customize the 2oz copper substrate stack and honeycomb thermal conductive hole structure, and the measured full-load temperature rise is controlled within 12°C. Passed -40°C~85°C batch-level cycle test and RoHS compliance certification, the light decay rate is ≤2.8% for 1,000 hours. Supports 15-day standard delivery and 7-day expedited delivery. If you have any request for LED Street Light PCB, please feel free to contact us: sales@bestpcbs.com
What Is LED Street Light PCB?
LED street light PCB (Printed Circuit Board) is a specialized circuit board designed to power and control LED arrays in outdoor lighting systems. Unlike conventional PCBs, these boards are engineered to endure harsh environmental conditions, including extreme temperatures, humidity, and vibration. They integrate LEDs, drivers, thermal management components, and smart sensors into a single robust platform, ensuring stable operation over decades.
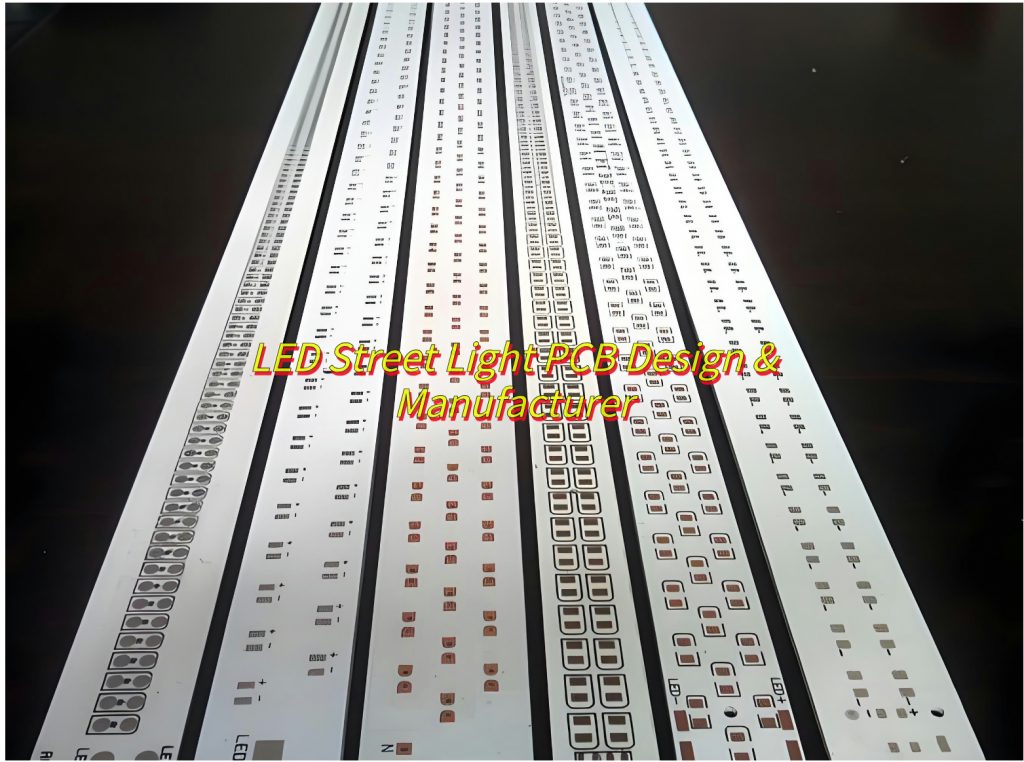
What Are Advantages of LED PCB Street Light?
LED street light PCBs offer multiple technical advantages:
- Enhanced Thermal Management – Aluminum-based structures with thermally conductive dielectric layers efficiently dissipate heat, preventing overheating and extending component lifespan.
- Electrical Insulation – The dielectric layer isolates circuitry from the aluminum substrate, ensuring operational safety.
- High-Density LED Layout – Flexible PCB designs enable dense LED arrangements for uniform illumination without visible light spots.
- Durability in Harsh Environments – Heat-resistant materials and robust construction adapt to outdoor temperature fluctuations and mechanical stress.
- Energy Efficiency – Low-voltage operation and optimized thermal design reduce power consumption while maintaining brightness.
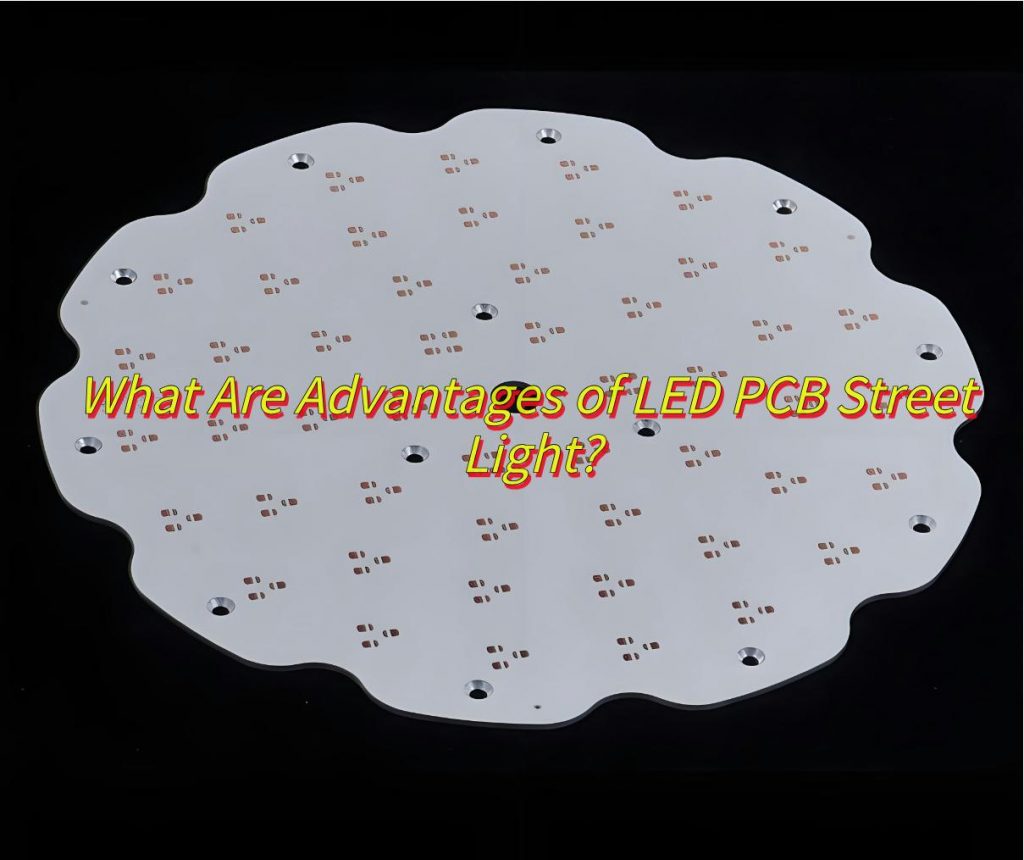
Why Choose Aluminum PCBs for Power LED Street Light Design?
Aluminum PCBs are ideal for power LED street light design due to:
- Superior Heat Dissipation – Aluminum substrates rapidly transfer heat from LEDs, preventing thermal degradation and ensuring stable performance.
- High Thermal Conductivity – Direct heat transfer via the metal core minimizes hotspots, critical for high-power LED longevity.
- Mechanical Durability – Resists warping, vibrations, and corrosion, maintaining structural integrity in extreme outdoor conditions.
- Electrical Isolation – Integrated dielectric layers prevent short circuits while enabling efficient thermal transfer.
- Lightweight & Compact – Simplifies fixture design and installation without compromising heat management.
- Cost-Effective Lifespan – Reduces maintenance and replacement costs by extending LED and driver life.
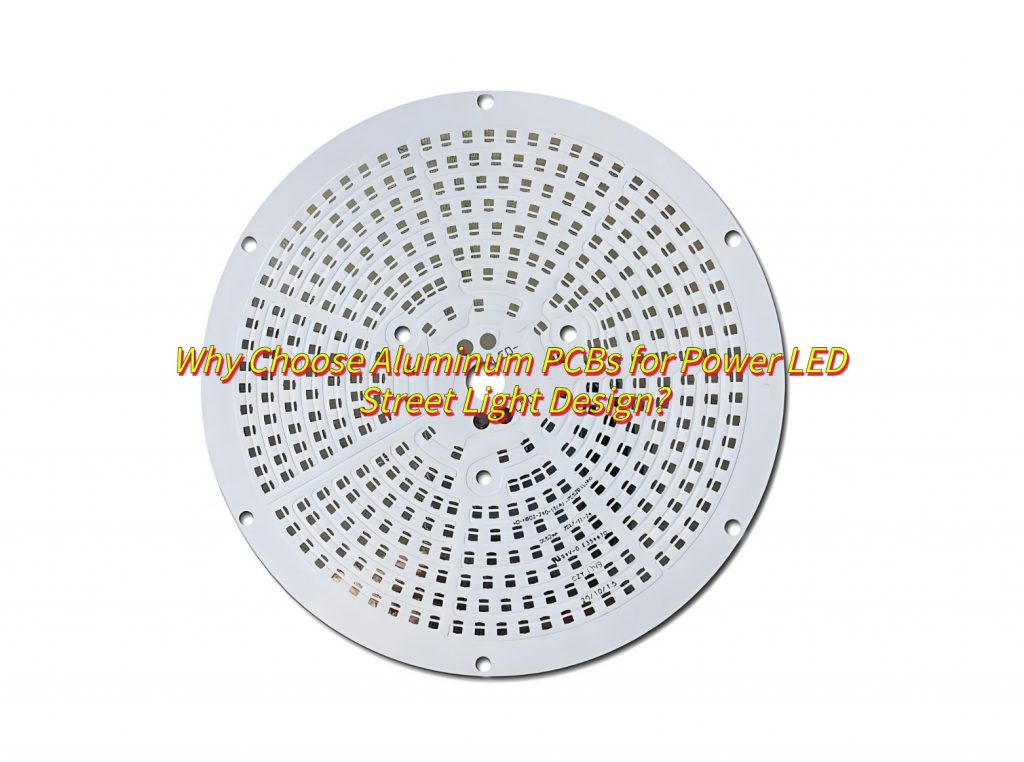
How to Design LED Street Light PCBs for Better Heat Dissipation?
To design LED street light PCBs for optimal heat dissipation:
1. Material Selection
- Use aluminum substrates (e.g., 6063-T5 alloy) with ≥2.0 W/m·K thermal conductivity for direct heat transfer.
- Prioritize 2oz+ copper layers for high-current traces to minimize resistive heating.
2. Layout Optimization
- Cluster high-power LEDs centrally with ≥5mm spacing between COB modules to prevent thermal overlap.
- Route traces with 4-6mm width for 3A+ currents and avoid right-angle bends to reduce impedance.
- Place drivers/ICs ≥15mm from LEDs and orient parallel to airflow direction.
3. Thermal Structure Design
- Implement 0.3-0.5mm thermal vias filled with conductive epoxy under LED pads (≥20 vias/cm²).
- Integrate 4-6mm thick aluminum heat sinks with fin density of 8-12 fins/inch, directly bonded to PCB.
- Apply thermal pads (3-5 W/m·K) between PCB and housing with 0.1-0.3mm thickness.
4. Process Enhancements
- Use reflow soldering with peak temps ≤260°C to prevent dielectric layer degradation.
- Design tear-drop copper connections at solder joints to reduce mechanical stress.
- Apply immersion silver finish (0.2-0.3μm) on traces for optimal thermal radiation.
5. Verification & Testing
- Maintain ≤85°C junction temperature with 25°C ambient in thermal simulations.
- Achieve <15°C temperature gradient across PCB surface in infrared testing.
How to Design LED Street Light PCB to Reduce Production Cost?
Here are three ways about how to make LED street light PCB design to reduce production cost:
- Aluminum substrate + centralized thermal pathways achieve 0.8cm² heat dissipation area per watt
- 5S2P LED configuration (600mA current limit per string) balances brightness and thermal load
- Non-isolated driver reduces costs while meeting IP65 protection requirements
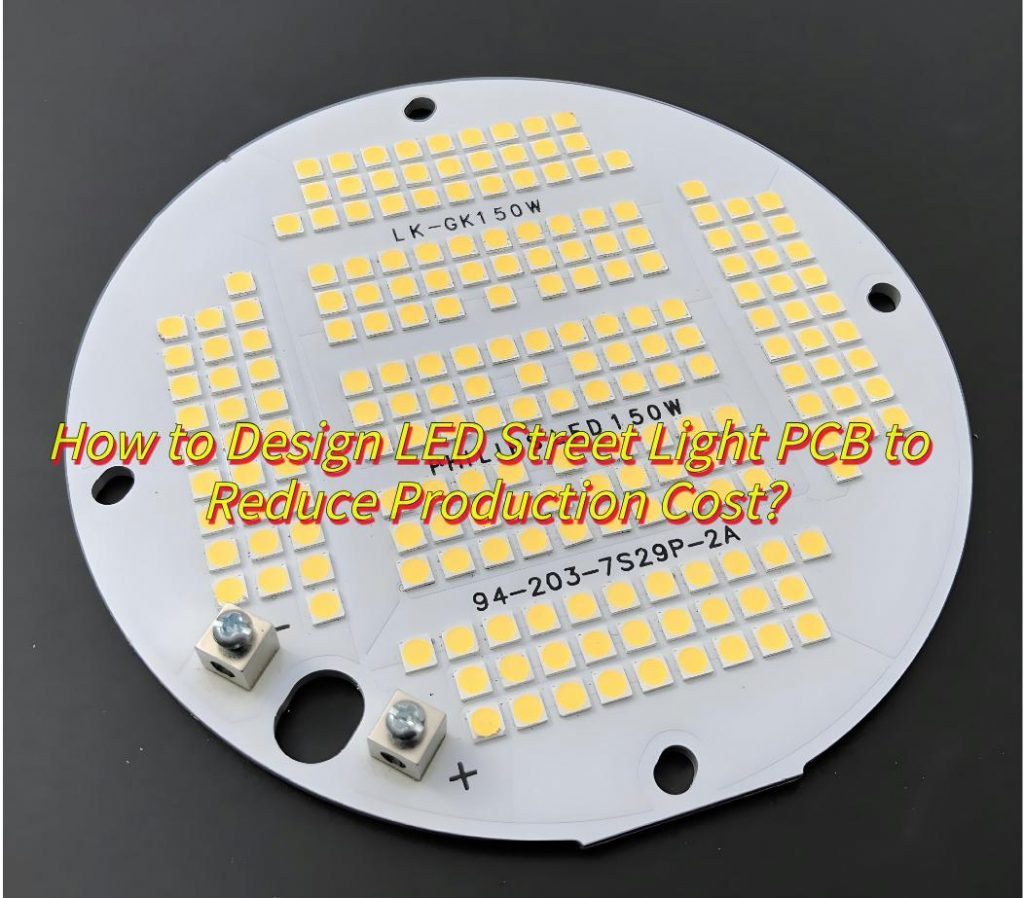
Case Study: 24V/30W LED Street Light PCB Design
1. Core Architecture
- Power Module: Full-wave rectification + AP3766 constant current driver, 24V±10% AC/DC input, stable 30W output.
- LED Array: 6-series×4-parallel COB modules (3V/350mA per unit), total 18V/1.2A.
- Thermal Structure: 2mm aluminum substrate + 6×8 matrix bottom heat dissipation holes (φ0.5mm, 3mm spacing) with external finned heatsink.
2. Key Design Specifications
- PCB Dimensions: 120×80×1.6mm (aluminum substrate).
- Copper Layer Thickness: 2oz copper foil, power trace width ≥5mm.
- Thermal Performance: Pad zone temperature ≤85°C (ambient 25°C).
- Driver Efficiency: ≥88% (1kHz PWM frequency).
3. Layout Optimization
- Current Path: Concentrated layout of rectifier circuit (D1-D4), filter capacitors (C1-C8), and AP3766 chip to shorten main power loop.
- Safety Clearance: ≥6mm spacing between high-voltage (rectifier) and low-voltage (LED array) zones, ≥2mm copper gap.
- Thermal Pathway: Three 2mm-wide exposed copper strips under COB modules, directly connected to heat dissipation hole array.
4. Validation Metrics
- Infrared Testing: ≤10°C temperature difference across LED solder joints (full load for 1 hour).
- Aging Test: ≤3% lumen depreciation over 1,000 hours (50°C environment).
How to Select a Trusted LED Street Light PCB Manufacturer?
Here are some methods about how to select a reliable LED street light PCB manufacturer:
Core certification requirements
- Confirm that the manufacturer has ISO 9001 quality management certification and IP65/67 waterproof and dustproof certification to ensure production specifications and product reliability;
- Give priority to manufacturers that have passed UL international safety certification to meet export market needs.
Technology and production capacity
- Investigate the automation level of the production line (such as SMT placement machines, AOI inspection equipment) to improve efficiency;
- Verify customized R&D capabilities (such as the design of heat dissipation solutions for 30W+ high-power street lights).
Quality and cost control
- Require manufacturers to provide RoHS material certification and batch-level high and low temperature cycle test (-40°C~85°C) reports;
- Obtain itemized quotations (PCB unit price, patch processing fee), and negotiate a tiered price of 500 pieces to reduce costs.
Delivery and supply chain management
- Confirm the standard delivery time ≤ 20 days, monthly production capacity ≥ 10,000 pieces, and ensure the stability of batch orders;
Factory inspection and sample verification
- Inspect the details of the workshop ESD protection, temperature and humidity control, etc.;
- Measure the full-load temperature rise (ΔT ≤ 15°C) and the light decay rate (≤ 3%) of the sample.
What Factors Affect LED Street Light PCB Pricing?
1. Material and process
- Substrate material: High thermal conductivity materials (such as 2oz copper substrate) or honeycomb thermal conductive structure can improve heat dissipation efficiency, but the material cost increases by 20-30%;
- Environmental compliance: Lead-free solder and flame-retardant copper clad laminate (FR-4) that meet RoHS standards are 15-20% more expensive than ordinary materials.
2. Production complexity
- Number of layers and wiring density: The processing fee of PCBs with more than 4 layers increases by 30-50% due to impedance control and heat dissipation requirements;
- Testing requirements: AOI/X-ray full inspection and batch-level high and low temperature cycle testing (-40°C~85°C) improve reliability, but the testing cost accounts for 8-12%.
3. Heat dissipation and circuit design
- Driver solution: Constant current driver chip (such as TI/Infineon solution) is 25% more expensive than the basic solution, but can reduce the risk of light decay;
- Thermal management design: Copper substrate + ceramic filling hole structure can control the full load temperature rise within 15°C, and the design fee increases by 10-15%.
4. Certification
- International certification: PCB manufacturers that have passed UL/CB certification generally quote 5-8% higher due to process audit costs.
5. Order size and delivery
- Bulk discount: Orders of more than 1,000 pieces can enjoy a 5-10% step-by-step price reduction, while small batch custom orders have a 30% higher unit price;
- Delivery time compression: The price difference between 15-day standard delivery and 7-day expedited delivery can reach 12-15%.
FAQs of LED Street Light PCB Manufacturing
Q1: How do you ensure consistent quality in bulk orders?
A1: Best Technology employs statistical process control (SPC) and 100% AOI (Automated Optical Inspection) to maintain low defect rates.
Q2: Can you handle custom designs with unique shapes or cutouts?
A2: Yes. Our CNC routing and laser cutting systems support complex geometries with ±0.2mm precision.
Q3: What certifications do your materials hold?
A3: We use UL-certified aluminum substrates and IEC-grade dielectric layers, ensuring compliance with EU and North American safety standards.
Q4: Do you offer waterproof conformal coatings?
A4: Yes, We apply acrylic or silicone coatings (IP67/IP68) to protect PCBs from moisture and chemical exposure.
Q5: What’s your typical lead time for 1,000-unit orders?
A5: Standard production takes 7–10 days, with expedited options available for urgent projects.
In conclusion, that’s all about LED street light PCB how to select a reliable LED street light PCB manufacturer with design service, if you have anything else needs to help, welcome to leave a message below this blog.
Tags: LED Street Light PCB, LED Street Light PCB Design, LED Street Light PCB Manufacturer