Flex rigid PCB manufacturer plays a crucial role in the electronics industry, providing innovative circuit board solutions that blend flexibility with rigidity. These advanced PCBs are widely used in aerospace, medical, automotive, and consumer electronics due to their durability and space-saving design. Understanding how they are made, their stackup structure, and the key factors in selecting a reliable manufacturer can help businesses make informed decisions. In this blog, we will explore everything from the manufacturing process to design considerations, ensuring you have all the details needed to choose the best supplier for your needs.
Best Technology is a leading flex rigid PCB manufacturer with a direct factory in China. Our FPC factory was established in 2013. Rigid-flex PCB lead time in Best Technology is 2~3 weeks. Rigid-flex PCB lead time in Best Technology is 2~3 weeks. Best Technology support PCBA. Customers provided components. If BOM is purchased by us, 1 week will be added for most cases. For components without stock, or with longer lead time, lead time will be negotiated with customers. If you have any questions or doubts about flex rigid PCB, just feel free to let us know at sales@bestpcbs.com at any time.
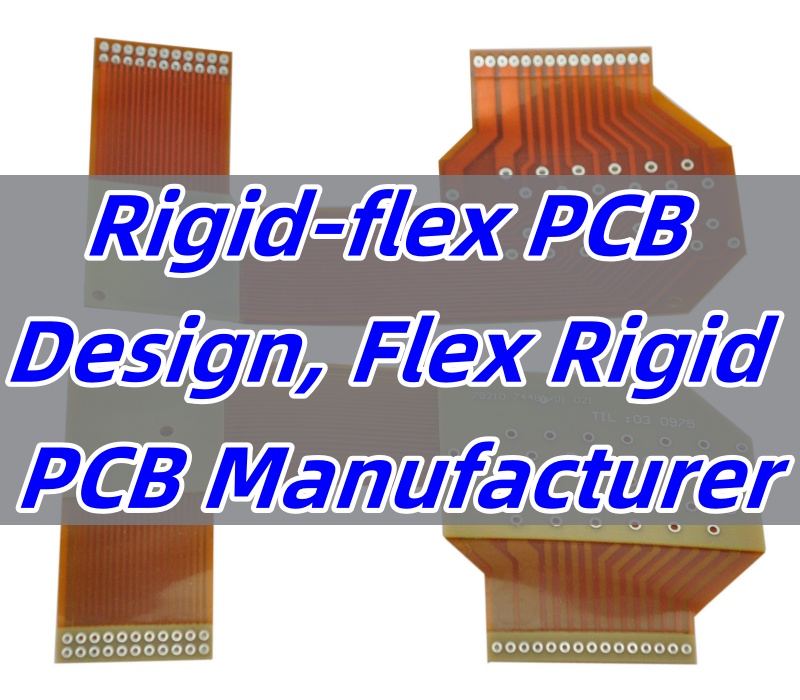
What is a Rigid-Flex PCB?
A rigid-flex PCB combines both rigid and flexible circuits into a single board. The rigid sections provide structural support, while the flexible parts allow for bending and movement. This design eliminates the need for connectors and cables, reducing weight and improving reliability. Many industries, including medical, aerospace, and consumer electronics, use these PCBs for compact and durable devices. By integrating flexible and rigid layers, they enhance mechanical performance and reduce assembly complexity.
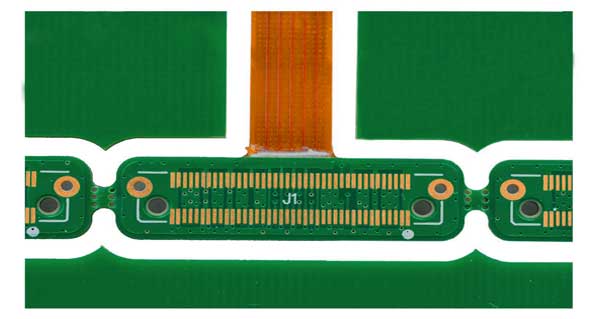
What is the Standard Rigid-Flex PCB Stackup Used by Manufacturers?
A proper stackup is crucial for performance and durability. Manufacturers use multiple layers of flexible and rigid materials bonded together. A typical stackup consists of rigid FR4 sections, flexible polyimide layers, and adhesive or prepreg for bonding. The number of layers varies based on complexity, but maintaining a balanced stackup prevents warping. Some designs also incorporate shielding layers to reduce electromagnetic interference, ensuring signal integrity in high-speed applications.
How Are Rigid-Flex PCBs Made?
The rigid flex PCB manufacturing process involves several key steps:
- Material Selection: Rigid FR4 and flexible polyimide materials are chosen based on application requirements.
- Layer Stackup: The rigid and flex layers are arranged for optimal electrical performance and mechanical stability.
- Drilling and Plating: Holes for vias and components are drilled and plated with copper.
- Circuit Patterning: Photolithography and etching define circuit traces on both rigid and flexible sections.
- Lamination: Rigid and flex layers are bonded using controlled heat and pressure.
- Testing and Inspection: Electrical testing and reliability checks ensure performance and quality.
Precision at each step ensures the final product meets high-reliability standards, making it suitable for mission-critical applications.
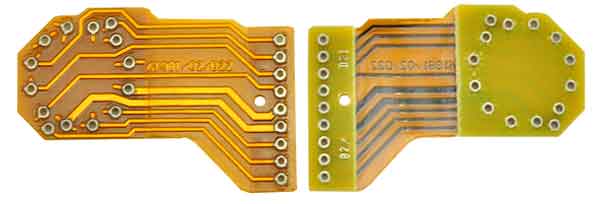
What Are the Key Considerations in Flex Rigid PCB Design?
Designing a rigid-flex PCB requires careful planning to ensure functionality and durability. Key factors include:
- Bend Radius: The flexible section should have a smooth curve to prevent stress fractures.
- Via Placement: Vias should be placed in rigid areas to avoid mechanical strain in flex sections.
- Trace Routing: Conductors should follow smooth curves rather than sharp angles for better signal integrity.
- Material Selection: Choosing the right materials enhances flexibility, thermal stability, and performance.
- Component Placement: Placing components strategically improves durability and assembly efficiency.
Proper rigid-flex PCB design practices prevent mechanical failures, enhance longevity, and improve overall PCB performance.
How Does a Reliable Flex Rigid PCB Manufacturer Ensure Quality?
A trusted flex rigid PCB manufacturer follows strict quality control measures. Here’s how they maintain high standards:
- Advanced Equipment: Precision drilling, laser cutting, and automated inspection tools improve accuracy.
- Material Testing: Verifying material properties ensures they meet electrical and mechanical requirements.
- Process Control: Temperature, pressure, and humidity are monitored during manufacturing.
- Reliability Testing: Flex cycling, thermal shock, and impedance tests confirm performance.
- Industry Certifications: Compliance with ISO, IPC, and UL standards guarantees quality assurance.
Consistent quality control ensures each PCB performs optimally in demanding environments, reducing failures and increasing reliability.
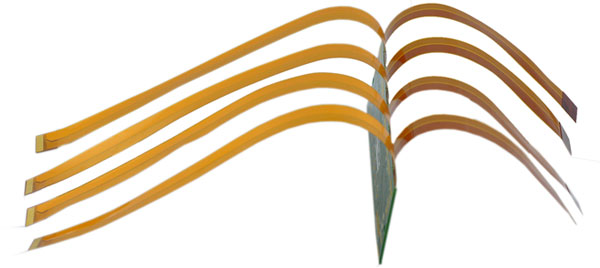
How to Select the Best Flex Rigid PCB Manufacturer?
Choosing the right manufacturer affects product performance and reliability. Consider these factors:
- Experience and Expertise: A manufacturer with years of experience understands complex designs.
- Production Capability: Check their ability to handle multilayer and high-precision PCBs.
- Quality Assurance: Look for certifications like ISO 9001 and IPC standards.
- Customer Support: Responsive service ensures smooth project completion.
- Global Supply Chain: Reliable logistics ensure timely delivery.
A well-established manufacturer guarantees high-quality production, helping businesses meet their technical requirements efficiently.
Why Choose Best Technology as Your Flex Rigid PCB Manufacturer?
Precision Engineering: Utilizing state-of-the-art equipment, we deliver meticulous fabrication and assembly for highly complex non-standard flex rigid printed circuit boards like 16 layers rigid-flex circuit with impedance control. We offer integrated IC programming and in-house testing capabilities, ensuring end-to-end quality for even the most demanding technical requirements.
- Strict Quality Control: Every board undergoes rigorous inspection and testing. In our flex rigid circuit board workshop, we have parallel exposure machines. And each production lot, each product will be checked strictly following IPC standards. And all of our products, Bech Technology are compliant with the latest ROHS.
- Customized Solutions: We tailor designs based on customer specifications. If you have any unique technical and functional requirements, just feel free to let us know in advance, our R&D team and engineers is able to reply within 12 hours.
- Fast and Reliable Delivery: Leveraging our extensive global supply chain network, we guarantee timely shipments and consistent on-time delivery. Best Technology prioritizes efficiency through rapid turnaround processes, with our entire team committed to delivering orders within 2-3 weeks to meet customer needs seamlessly.
Working with Best Technology means partnering with a manufacturer that prioritizes quality, innovation, and customer satisfaction.
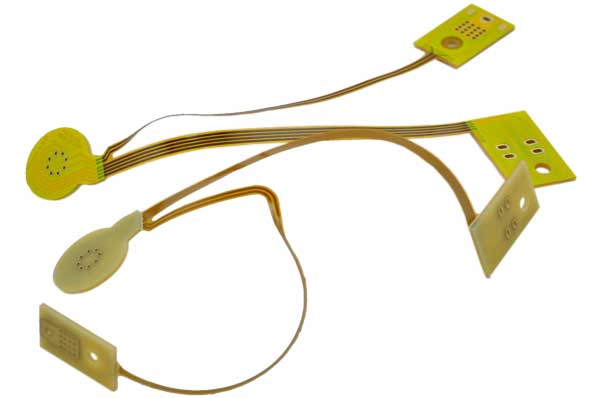
In conclusion, finding the right flex rigid PCB manufacturer is essential for high-performance applications. Understanding the stackup, design considerations, and fabrication process helps in selecting the best supplier. Best Technology stands out with its expertise, quality control, and customer support. Just feel free to contact us at sales@bestpcbs.com to get a quote for any rigid-flex PCB project!
Tags: flex rigid pcb, Flex Rigid PCB Manufacturer, Rigid-flex PCB Design