SMT PCB manufacturer services are the backbone of modern electronics. Whether you’re building a smartphone, a wearable device, or an industrial controller, you need precision. These manufacturers combine automation, experience, and consistency to help your products come to life. In this blog, you’ll learn how SMT works, what to look for in a supplier, and who the key players are in different markets.
Best Technology is a professional SMT PCB manufacturer. Our SMT factory was established in 2015. SMT PCB quality is our bloodstream. Our Quality Policy commits to customer delight through full engagement. We will achieve a quality and reliable SMT PCB passing rate of 98% by solving customer complaints within 24 hours in 2025. Our product portfolio encompasses Metal Dome, Metal Dome Array, Flexible Printed Circuits (FPC), Rigid PCBs (FR4 PCB), Rigid-Flex Circuits, Metal Core PCBs, Ceramic Substrate PCBs, PCB Assembly Services (SMT/PCBA Manufacturing). These solutions power virtually all modern electronic devices, spanning consumer electronics, automotive systems, medical equipment, and industrial automation applications.
Every PCB product listed above from Best Technology is fully customizable, just feel free to let us know your specific SMT PCB requirement via sales@bestpcbs.com.
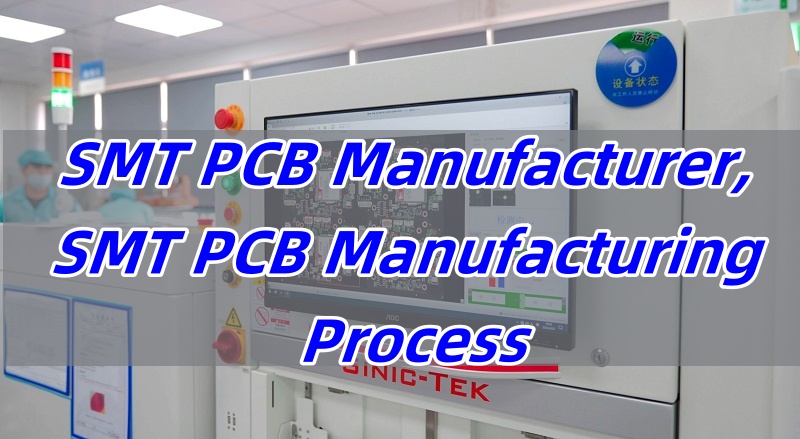
What is SMT in PCB Manufacturing?
Surface Mount Technology, or SMT, refers to placing components directly onto the surface of a PCB. It has replaced the older through-hole method in most modern assemblies. SMT enables smaller, lighter boards with higher component density. This makes it ideal for compact electronic devices.
Unlike the older process, SMT does not need holes drilled into the board. Instead, tiny components are placed using automated machines. Then, solder paste and heat secure the parts firmly in place. The result is efficient and cost-effective production.
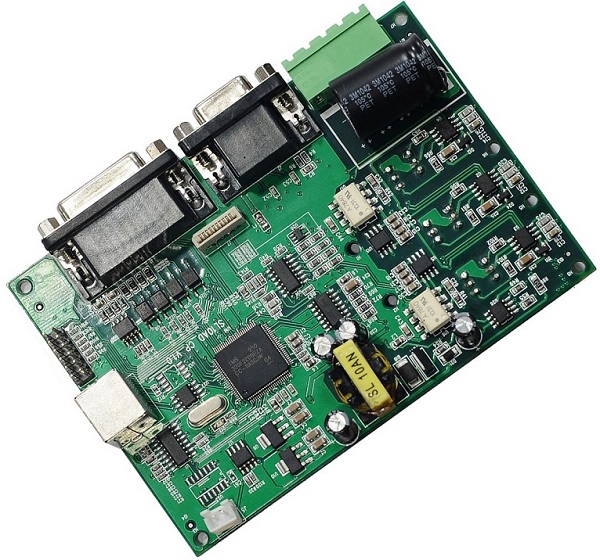
What Services Does an SMT PCB Manufacturer Offer?
A professional SMT PCB manufacturer typically offers full-service support. Here are the most common ones:
- Component sourcing: Reliable sourcing ensures all parts meet the quality standard.
- Stencil design and paste printing: Precision in paste application impacts the entire process.
- Pick and place services: Robotic arms place components with high accuracy.
- Reflow soldering: Heat is applied to solidify the solder paste.
- Inspection and testing: AOI, X-ray, and functional tests ensure product reliability.
Some manufacturers go beyond this with turnkey solutions. This includes design support, box build, and logistics.
SMT PCB Manufacturing Process
The SMT PCB manufacturing process is built around accuracy and speed. An SMT PCB manufacturer like Best Technology follows a strict, detailed process to ensure each board performs reliably in real-world conditions. Our workflow is built for precision, consistency, and speed — especially for projects with demanding specs and tight lead times.
Step 1: Incoming Material Inspection (BGA/PCB)
- Every journey starts with quality. Our team inspects the incoming PCBs and BGA components before they enter the line. We check for warpage, oxidation, and conformity to IPC standards.
Step 2: Baking (Dehumidification)
- Next, we bake moisture-sensitive parts like BGA, IC, FPC, SMD LED and bare PCBs in a temperature-controlled oven. This prevents internal moisture from causing delamination or popcorn effect during reflow.
Step 3: Solder Paste Preparation
- We prepare the solder paste by mixing and thawing it under controlled conditions. This step avoids separation of flux and metal particles, ensuring a smooth application.
Step 4: Solder Paste Printing
- Using high-precision printers and stainless steel stencils, we print solder paste onto each PCB pad. This step is critical, which sets the foundation for perfect component placement.
Step 5: SPI (Solder Paste Inspection)
- Before going further, we inspect every board using SPI machines. They check solder paste height, volume, and alignment. If any deviation is found, it’s corrected immediately.
Step 6: Component Placement (SMT)
- Now comes the core of SMT — pick and place. Our automatic machines accurately place each SMD component, from resistors to complex ICs, onto the solder-pasted PCB surface.
Step 7: Reflow Soldering
- Once the components are placed, boards move into our reflow oven. They pass through a multi-zone system where controlled heat melts the solder and solidifies electrical connections without damaging components.
Step 8: Tail End Cleaning
- After reflow, we clean any excess flux or debris that might affect the final inspection or future use. This keeps the surface clean for the next steps.
Step 9: Post-Reflow Inspection
- Every board undergoes manual and machine-assisted inspections. We check for solder bridging, cold joints, and other visible defects.
Step 10: AOI (Automated Optical Inspection)
- Our AOI machines scan each board to detect alignment errors, missing components, or improper solder joints. This step eliminates most visual flaws before the next process.
Step 11: X-Ray (for BGA only)
- If the board includes BGAs, we inspect solder joints hidden under the package using X-ray equipment. It ensures full connectivity and proper wetting under these tricky parts.
Step 12: Hand Soldering (Post-SMT)
- Some connectors, pin headers, or through-hole parts are added manually. Our skilled operators solder them carefully to maintain stability and cleanliness.
Step 13: Cleaning
- Boards go through a cleaning process again to remove any flux residues, especially after hand soldering. This improves long-term reliability and electrical insulation.
Step 14: Programming and Testing
- Functional tests come next. We flash firmware, check voltages, run diagnostics, and validate every circuit performs to spec. Failed boards are fixed or flagged for review.
Step 15: Conformal Coating
- If required, we apply protective coatings to safeguard against moisture, dust, and chemicals. This is vital for industrial, automotive, or outdoor applications.
Step 16: Potting/Glue Application
- In some cases, we apply epoxy or adhesive gel for mechanical strength or insulation. This prevents vibration damage or corrosion in harsh environments.
Step 17: Final Assembly
- At this stage, we perform product-level assembly — adding housings, displays, connectors, or mechanical parts as needed. This is where your PCB becomes a full product.
Step 18: Labeling
- We add barcodes, serial numbers, or customer-specific labels. This step helps in tracking, traceability, and logistics.
Step 19: Depaneling
- If boards were produced in panels, we now separate them using routers, V-cut machines, or lasers. Each piece is carefully handled to avoid damage.
Step 20: Packing Method Confirmation
- Before packaging, we confirm the right shipping method with you — whether that’s anti-static bags, blister trays, bubble wrap, or custom trays.
Step 21: Final Packaging and Shipping
- Boards are packed securely for local or international shipping. We make sure each box is labeled, padded, and ready for safe delivery to your door.
This entire SMT PCB manufacturing process reflects Best Technology’s dedication to consistency, cleanliness, and quality control. Whether you’re prototyping or scaling up for mass production, our process is built to support you every step of the way. Every step affects yield and quality. So Best Technology invests in modern SMT machines and skilled operators.
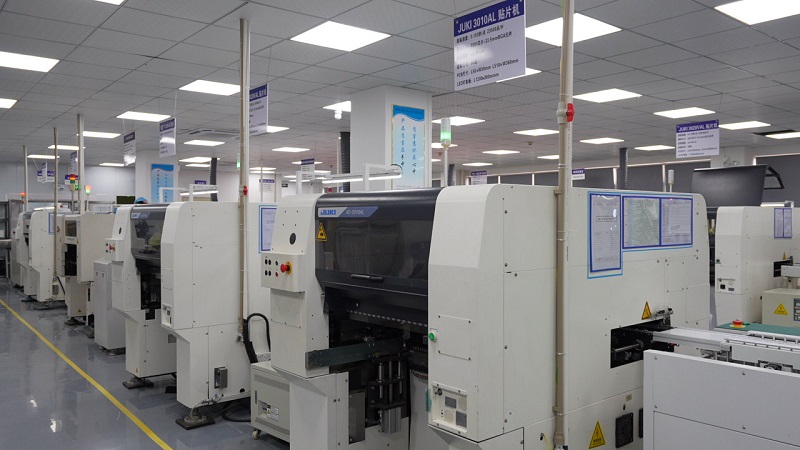
Who is the Top 10 Biggest SMT Company in the World?
Introduction
When searching for a global SMT PCB manufacturer, many companies lead in capacity, quality, and innovation. These firms support industries like telecom, automotive, consumer electronics, and aerospace.
Top 10 Global SMT Companies (Not in ranking order):
1. Best Technology (China) – Known for speed and flexibility in SMT PCB manufacturing.
2. Foxconn (Taiwan) – Major Apple supplier and global electronics giant.
3. Flex Ltd. (Singapore) – Offers large-scale EMS and design services.
4. Benchmark Electronics (USA) – High-reliability assemblies for aerospace and defense.
5. Sanmina (USA) – Full-service EMS with global footprint.
6. Celestica (Canada) – Supports complex, regulated industries.
7. Venture Corporation (Singapore) – High-value manufacturing and R&D.
8. Zollner Elektronik AG (Germany) – Family-run and respected in Europe.
9. Pegatron (Taiwan) – OEM and ODM services for global tech firms.
10. Asteelflash (France) – Fast-growing EMS company across four continents.
These global players have set benchmarks for SMT PCB manufacturing. Their investment in smart factories and automation gives them a leading edge. Choosing such a company brings reliability, scalability, and strong support.
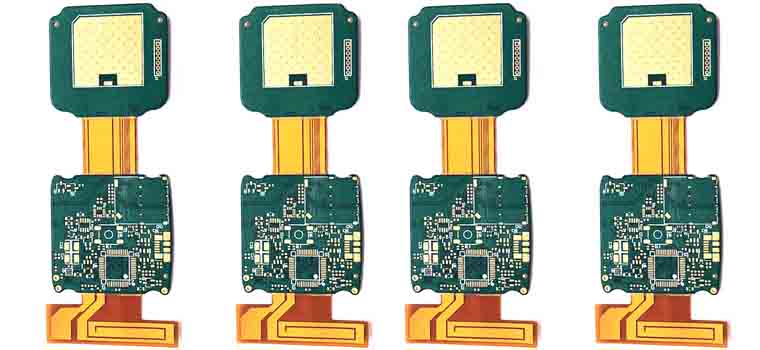
SMT PCB Manufacturer in USA
The USA has long been a hub for innovation. SMT PCB manufacturers here serve high-tech, aerospace, and medical markets. Customers in these sectors need strict quality control, fast turnaround, and confidentiality.
Leading SMT PCB Manufacturers in the USA:
1. Advanced Circuits (Colorado) – Offers full turnkey PCB assembly and prototypes.
2. Tempo Automation (California) – Focused on fast, agile prototyping for startups and engineers.
3. Sanmina (California) – One of the largest electronics manufacturers with global reach.
4. Jabil (Florida) – Offers advanced automation and smart factory support.
5. Emerald EMS (California and Massachusetts) – Focuses on low to mid-volume precision builds.
Working with a USA-based SMT PCB manufacturer brings access to certified facilities and close communication. These companies are ideal for time-sensitive and highly-regulated applications.
SMT PCB Assembly Manufacturers in India
India is growing as a strong force in the electronics manufacturing scene. SMT PCB assembly manufacturers in India offer cost-efficient services with quick turnaround. Many also support large volumes for export markets.
Top SMT PCB Assembly Manufacturers in India:
1. SFO Technologies (Kochi) – A NeST group company with global client base.
2. Dixon Technologies (Noida) – Manufactures for top consumer brands.
3. Sahasra Electronics (Rajasthan) – Focused on LED and industrial PCBs.
4. Kaynes Technology (Mysore) – Offers complete EMS and box builds.
5. Vinyas Innovative Technologies (Bangalore) – Serves aerospace, defense, and industrial sectors.
India’s SMT PCB manufacturers combine affordability with strong engineering talent. As demand rises, these firms are expanding capacity to meet global needs.
What Makes a Good SMT PCB Manufacturer Stand Out in the Market?
Reputation alone doesn’t guarantee results. A strong SMT PCB manufacturer shows excellence through:
- Reliable delivery time
- High yield rates
- ISO and industry certifications
- Transparent communication
- Support with design-for-manufacturing (DFM)
Smart buyers look at case studies, reviews, and production capabilities. A well-managed factory with modern SMT lines can save time and cost in the long run.
How to Choose the Right SMT PCB Manufacturer for Your Project?
Picking the right partner isn’t just about price. Here’s what to consider:
1. Capability Match – Do they handle your board size, volume, and component types?
2. Certifications – Look for ISO 9001, IATF 16949, or others depending on your sector.
3. Responsiveness – A good supplier communicates quickly and clearly.
4. Turnkey Options – One-stop services often reduce lead times.
5. Location – Proximity to your team or market may offer speed or cost advantages.
Take time to ask questions. Visit the facility if possible. Or review sample reports from past jobs.
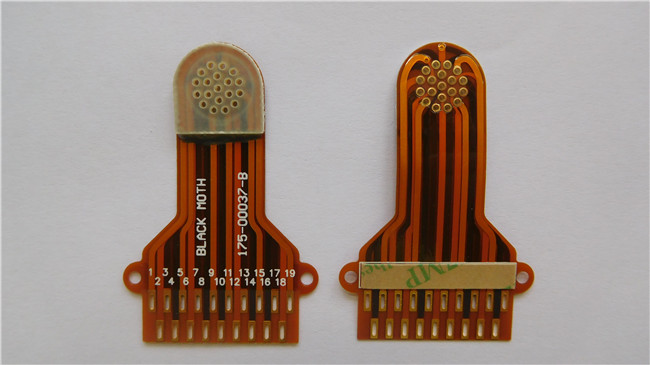
In conclusion, choosing the right SMT PCB manufacturer improves your product’s reliability, lowers cost, and shortens launch time. Look for a partner who listens, adapts, and delivers consistently. Whether you’re working with a local firm or a global giant, trust and technical support matter the most.
If you’re looking for a reliable SMT PCB partner, Best Technology brings 18+ years of experience in custom PCB solutions. From prototypes to volume orders, we provide fast support at any time, just feel free to contact us via sales@bestpcbs.com.