What is Ceramic DIP Package?
The Ceramic Dual-In-Line Package (CDIP or CerDIP) is a sealed enclosure composed of two dry-pressed ceramic parts, encased by a dual-in-line pin frame. This package design effectively prevents the entry of moisture and contaminants once sealed. The CerDIP consists of two main components: the upper section, known as the cap, and the lower section, referred to as the base. It features gold-plated leads attached to the brazed sides and a metal cover that is securely bonded to the chip using a metal seal. The base also includes a cavity designed to house the microchip.
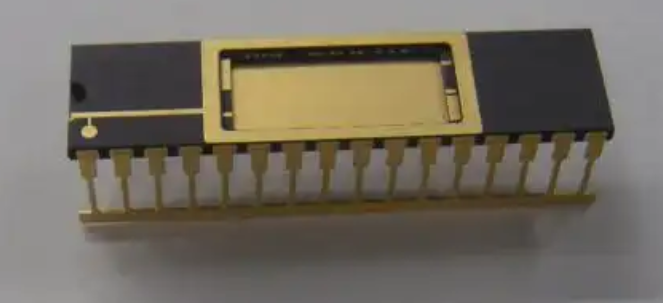
What is the Ceramic DIP Package Made of?
A ceramic DIP package part is usually made of ceramic body, metal leads, sealing materials and internal bonding wires.
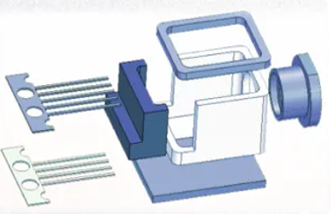
Ceramic Body
The core structure of a CerDIP package is its ceramic body. This part provides mechanical strength, thermal stability, and electrical insulation. Alumina is the most commonly used ceramic due to its excellent dielectric properties, high-temperature resistance, and cost-effectiveness. For applications demanding higher thermal conductivity, beryllium oxide or silicon nitride may be used.
Metal Leads
CerDIPs feature metal leads that extend from the ceramic body to connect the internal IC to external circuits. These leads are typically made of nickel, gold-plated copper, or tin-coated steel.
Sealing Materials
To protect the IC from environmental factors, CerDIPs are often hermetically sealed. This involves the use of materials such as glass or metal seals to create an airtight enclosure.
Internal Bonding Wires
Inside the package, fine bonding wires made of gold or aluminum are used to connect the IC chip to the external leads. These wires ensure electrical continuity and maintain the integrity of the circuit.
Why Are CerDIPs Important in Electronics?
CerDIPs act as a protective casing for ICs, safeguarding delicate components from environmental hazards and operational stress. They are particularly valued in industries where temperature fluctuations, mechanical stress, or moisture exposure can compromise performance.
The ceramic material used in CerDIP packages offers superior thermal conductivity and electrical insulation compared to other materials like plastic. This allows circuits to operate at peak performance even in extreme conditions, such as high altitudes, deep-sea environments, or industrial facilities with fluctuating temperatures. Additionally, CerDIP packages are highly resistant to contamination, providing a long-term reliability and stability. That’s why the ceramic DIP package part so important.
What Sets CerDIP Apart from Other Packaging Formats?
The main differences between CerDIP packages and other packaging formats are their materials, applications and characteristics.
CerDIP is mainly used In ECL RAM, DSP (digital signal processor) and other circuits. The pin center distance is 2.54mm, and the number of pins ranges from 8 to 42. The CerDIP package has a glass window and is suitable for UV-erasing EPROMs and microcomputer circuits with EPROMs inside .
The main differences between CerDIP and other packaging formats are:
- Materials: CerDIP uses ceramic materials, while other package formats may use plastic or other materials.
- Application field: CerDIP is mainly used for ECL RAM, DSP and other circuits, while other packaging formats are suitable for different circuits and application scenarios.
- Features: CerDIP is glass sealed and is suitable for circuits that require sealed protection.
- Heat dissipation: Ceramics efficiently dissipate heat, preventing ICs from overheating.
In addition, CerDIP differs from other package formats in pin center distance and pin count. For example, DIP (Dual In-line Package) has a pin center distance of 2.54mm and the number of pins from 6 to 64; The Ball Grid Array (BGA) is surface-mount, the number of pins can exceed 200, and the package body is smaller
What Applications Rely on CerDIP Technology?
CerDIP packages are found in a wide range of applications, particularly in industries where performance and reliability cannot be compromised.
- Aerospace and Defense
In satellites, aircraft, and military systems, CerDIP packages are critical for electronic modules that operate in extreme conditions.
- Medical Devices
Advanced medical technologies like imaging equipment, pacemakers, and laboratory instruments rely on CerDIPs for their precise and reliable performance. These devices often operate in sterile or temperature-sensitive environments, where CerDIP packages thrive.
- Automotive Electronics
As vehicles become more advanced, electronic systems play a larger role in ensuring safety and efficiency. CerDIPs are used in engine control units, advanced driver-assistance systems (ADAS), and other critical components that demand reliability.
- Industrial Equipment
In manufacturing and automation, CerDIPs are part of control systems that manage processes with high precision.
- High-Performance Computing
CerDIPs are used in high-speed computing and telecommunications devices, where heat management and signal integrity are critical.
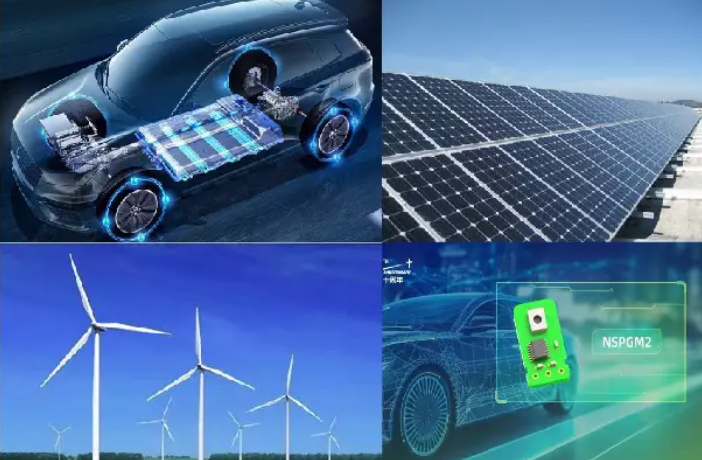
Key Features of CerDIP Packages
- CerDIPs operate reliably over a wide temperature range, from sub-zero conditions to high-heat industrial settings.
- The ceramic material is an excellent insulator, reducing the risk of electrical interference or short circuits.
- CerDIPs can be hermetically sealed, preventing moisture, dust, and contaminants from affecting the ICs inside.
- The rigid structure of the ceramic provides protection against mechanical shocks and vibrations.
- CerDIP packages can be designed to support compact circuit assemblies, making them suitable for space-constrained applications.
How Are CerDIPs Manufactured?
The production of CerDIP packages involves complex and meticulous processes to ensure high quality, here are some basic process that manufacture a ceramic DIP package part:
- Material Preparation: Ceramic powders are mixed with binders and compressed into the desired shape.
- Sintering: The compressed ceramic is baked at high temperatures, a process that enhances its density and strength.
- Machining: The sintered ceramic is machined to precise dimensions, ensuring compatibility with circuit designs.
- Metal Pin Attachment: Pins are attached to the ceramic body to facilitate electrical connections. These pins are typically made of a conductive metal like gold or nickel.
- Sealing: Hermetic sealing ensures that the package is airtight, protecting the IC from environmental factors.
As a ceramic PCB manufacturer, Best Technology not only focus on the manufacturing of ceramic circuit board, but also in ceramic package shell fabrication. We have strong R&D team and most of our engineers are engaging in ceramic PCB manufacturing for over 10 years. They can provide professional technical support for your PCB project. In addition to this, we offer one-stop service from the ceramic PCB design, PCB copy, component sourcing, PCB fabrication, PCB assembly, box building assembly and arrange the shipment. Choose us, we can be your most reliable ceramic package supplier.
Tags: ceramic dip package part