Circuit board customĀ solutions help create smarter and smaller devices. Today, many products need personalized designs, fast delivery, and accurate assembly. Thatās where Best Technology becomes your trusted partner.
Best Technology is an R&D-driven corporation providing circuit board custom services in the domestic market and the international market. Maintaining the consistency of quality is our corporate identity and is the anchor for us to gain the trust of customers. Our engineers and other professionals have knowledge of custom circuit board design, prototype, and assembly. And we have a proven track record that more than 1700 customers across 40 countries give us good reviews. If you have any pertinent circuit board custom projects that need us to support, a warm welcome to contact us at sales@bestpcbs.com at any time.
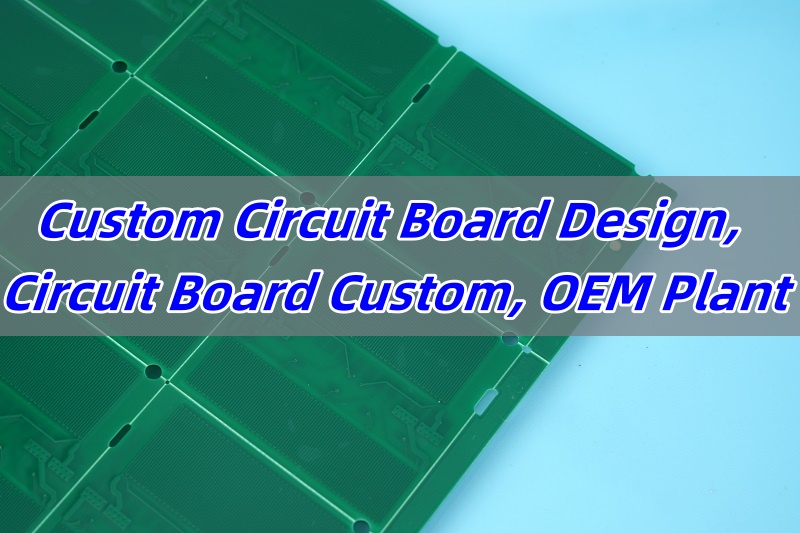
Who Designs Circuit Board Custom?
Engineers with expertise in electronics create these custom boards. They work with software tools like Altium, Eagle, and KiCAD. These experts design the PCB to match your product’s shape, speed, and power needs. Most projects start from your idea. Then the team turns that idea into a schematic, layout, and finally a production-ready design.
Can AI Design Circuit Boards?
Yes, AI tools can now help design circuit boards. They save time by suggesting component placements and routing paths. However, they cannot fully replace skilled engineers. AI speeds up the process, but human review is essential. So, when you need circuit board custom work, a smart mix of AI and experience gives the best results.
How Much Does It Cost to Design Circuit Board Custom?
TheĀ custom circuit board costĀ depends on many things. Size, layer count, complexity, and quantity affect the price. A simple two-layer board can cost under $100 for design. More advanced boards with multiple layers and strict rules may cost a few hundred. At Best Technology, we keepĀ custom PCB priceĀ competitive without cutting corners. Plus, we offer suggestions to help reduce cost during the early design phase.
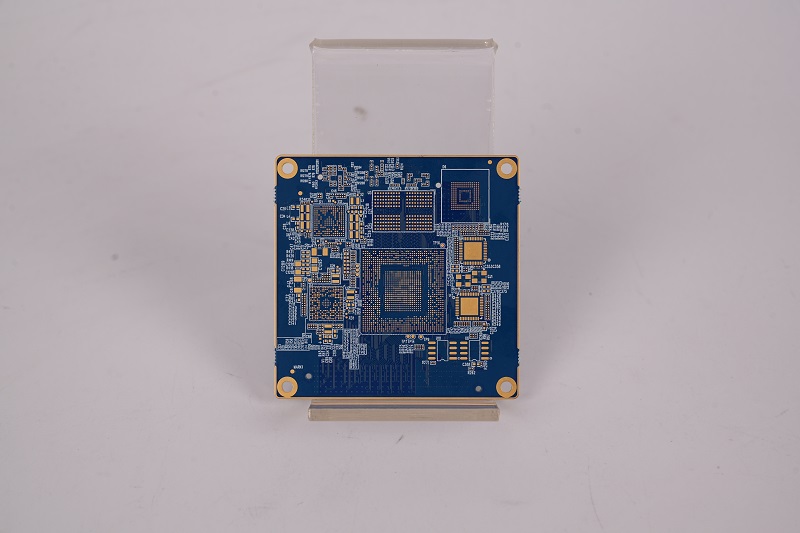
How Much Does a Small Custom PCB Cost?
Small runs can be affordable with the right partner. A PCB board custom order of 5-10 units may cost $50 to $200 depending on size and complexity. We help our clients choose the right volume to balance cost and speed. For prototypes, we also offer quick-turn services to speed up your launch.
What Are Alternatives to Circuit Boards?
Sometimes, traditionalĀ PCB boardsĀ arenāt ideal. Alternatives include flexible PCBs, ceramic PCBs, and even breadboards for early tests. Some wearable tech uses flexible boards for better fit. But for most products, printed circuit boards offer the best mix of stability, size, and cost.
Custom Circuit Board Manufacturers
There are many custom circuit board manufacturers in the market. But not all offer the same quality, support, or delivery time. Many customers face issues like poor communication, delays, or unclear pricing. At Best Technology, we solve these pain points with clear steps:
- Direct support from engineers
- Quick responses, often within 4 hours
- Fast quotes with full breakdowns
- Free DFM (design for manufacturability) checks
We believe in being partners, not just suppliers. From small runs to large OEM orders, we offer steady quality and full traceability. We are OEM plant, and our services are flexible. Whether you want a single prototype or a large OEM run, we adjust based on your needs. You can reach us at sales@bestpcbs.com or reach out to us through ourĀ circuit board website.
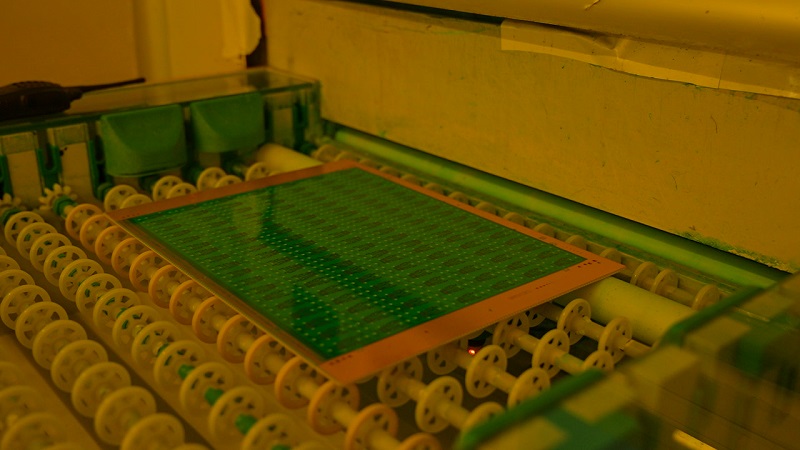
Why Should You Choose Best Technology as Your Circuit Board Custom OEM Plant?
Choosing Best Technology means working with a trusted team. We are not just a PCB maker. We are your long-term partner in innovation. Hereās what sets us apart:
- Full Certifications: ISO 9001, ISO 13485, IATF 16949, AS9100D
- MES System: Tracks every component and step
- Quick turn PCB assembly USA and overseas
- Support for both simple and complexĀ custom circuit board design
- Clean workshops with RoHS-compliant production
- Customized quotes within 6ā12 hours
We understand your pain points:
- Too many steps to get a quote? We simplify it.
- Unclear specs causing rework? We guide early with clear feedback.
- Delays from other custom circuit board makers? We ship fast and keep you updated.
Additionally, we supportĀ custom circuit board artĀ for brands that care about visual identity. Whether you want logos, shapes, or creative finishes, we support your vision.
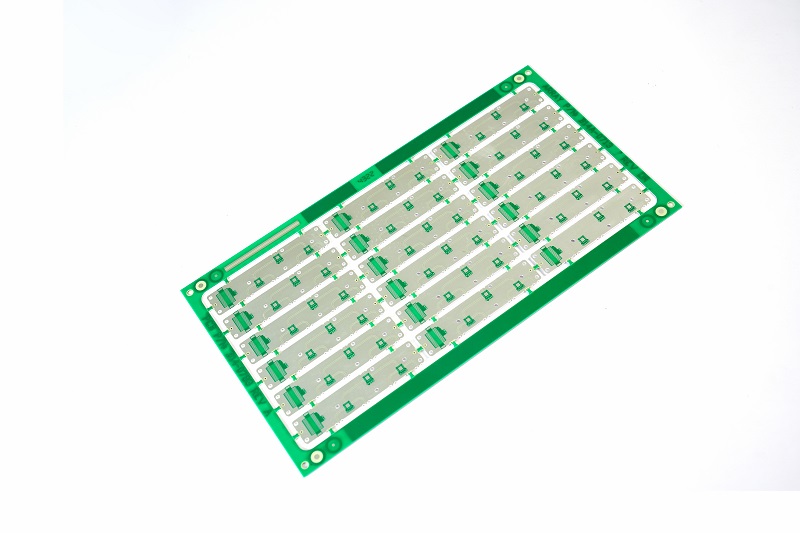
To sum up, when your product needs a smart and reliableĀ circuit board customĀ solution, trust Best Technology. We combine smart design, fast service, and strong engineering. We respond quickly and care about every detail. From design to delivery, we support your goals at every step. If youāre ready to launch your next idea, start with a quote or talk with our engineer at sales@bestpcbs.com.