Would you like to know about what is LED grow light PCB and how to select a reliable LED grow light PCB manufacturer? Please see this blog if you want to know.
Best Technology focus on LED grow light PCB design, prototyping and manufacturing since 2006. We adopted IP65 protection standard, epoxy resin glue curing and UVLED protective coating technology, it is suitable for high humidity and dusty planting environments. Then we provide OEM/ODM services with LED grow light PCB , support diversified solutions from single-layer aluminum substrates to multi-layer FR-4 substrates, and meet the needs of different scenarios such as home hydroponics and greenhouses. Lastly we have integrate high-speed or high-frequency PCB technology, support multi-channel spectrum adjustment (such as red and blue light ratio optimization), and accurately control the light parameters required for plant growth. If you have any request for LED grow light PCB, welcome to contact us sales@bestpcbs.com
What Is LED Grow Light PCB?
An LED Grow Light PCBÂ (Printed Circuit Board) is a specialized board designed to power and control LED chips for indoor plant cultivation. These boards are engineered to deliver precise light wavelengths (such as red and blue spectra) that optimize photosynthesis. Unlike standard PCBs, they often use aluminum substrates for superior heat dissipation, ensuring stable performance in high-temperature environments like greenhouses or vertical farms.
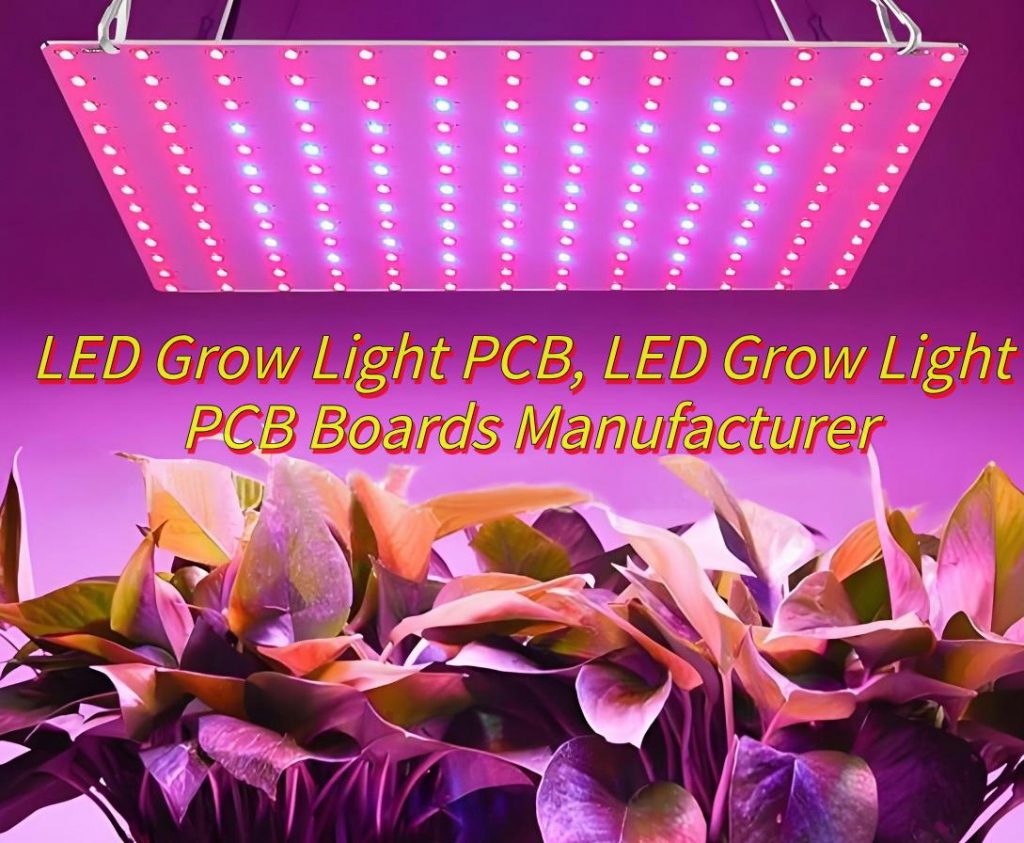
What Are Advantages of LED Grow Light PCB?
LED Grow Light PCBs dominate modern agriculture due to these unmatched benefits:
- Energy Efficiencyâ:Â Consumes 50-70% less power than traditional HID lamps.
- âLong Lifespanâ:Â Operates for 50,000+ hours with minimal light decay.
- âCustomizable Spectraâ:Â Adjusts red (660nm) and blue (450nm) light ratios for different growth stages.
- âLow Heat Emissionâ:Â Aluminum substrates reduce thermal stress on plants.
- âCompact Designâ: Enables modular installations in tight spaces.
- âEco-Friendlyâ: No mercury or harmful UV/IR radiation.
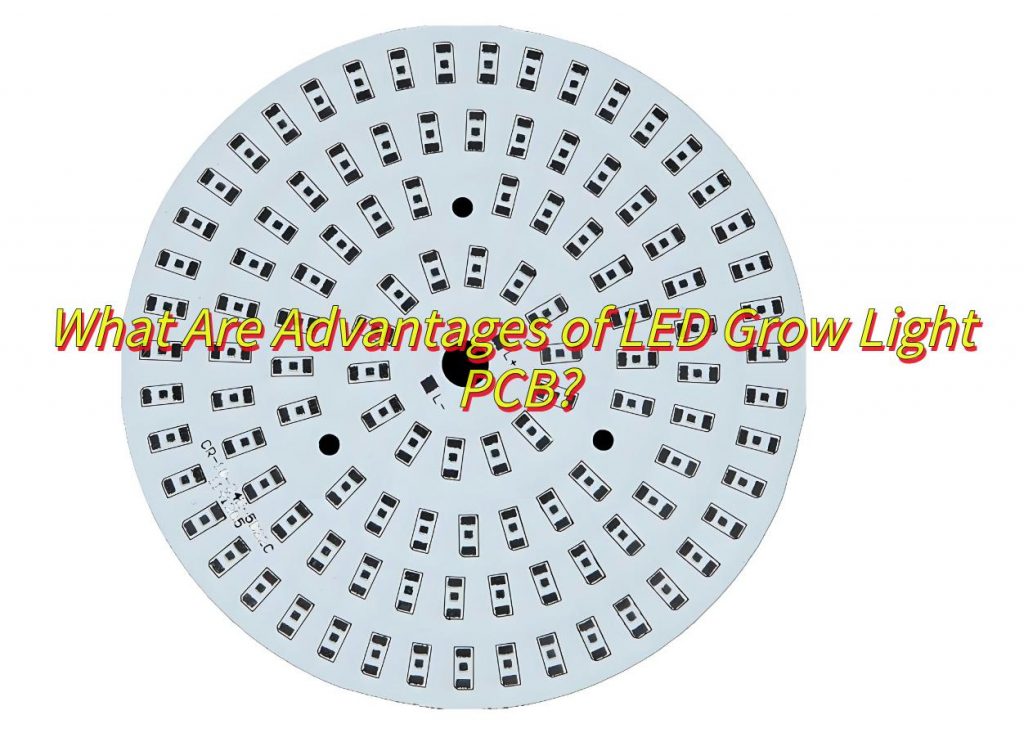
What Are Application of LED Grow Light PCB?
- Indoor Vertical Farming-Custom red-blue light combinations speed up leafy green growth by 30%.
- âGreenhouse Lighting-Replace outdated bulbs to ensure consistent light levels, even on cloudy days.
- âCannabis Cultivation-Adjustable light ratios improve cannabinoid content by 15-20%.
- âHome Hydroponics-Waterproof, low-power boards for growing herbs indoors.
- âResearch Labs-Test how different light spectra affect plant growth.
- âPlant Nurseries-Full-spectrum light cuts seedling growth time by 40%.
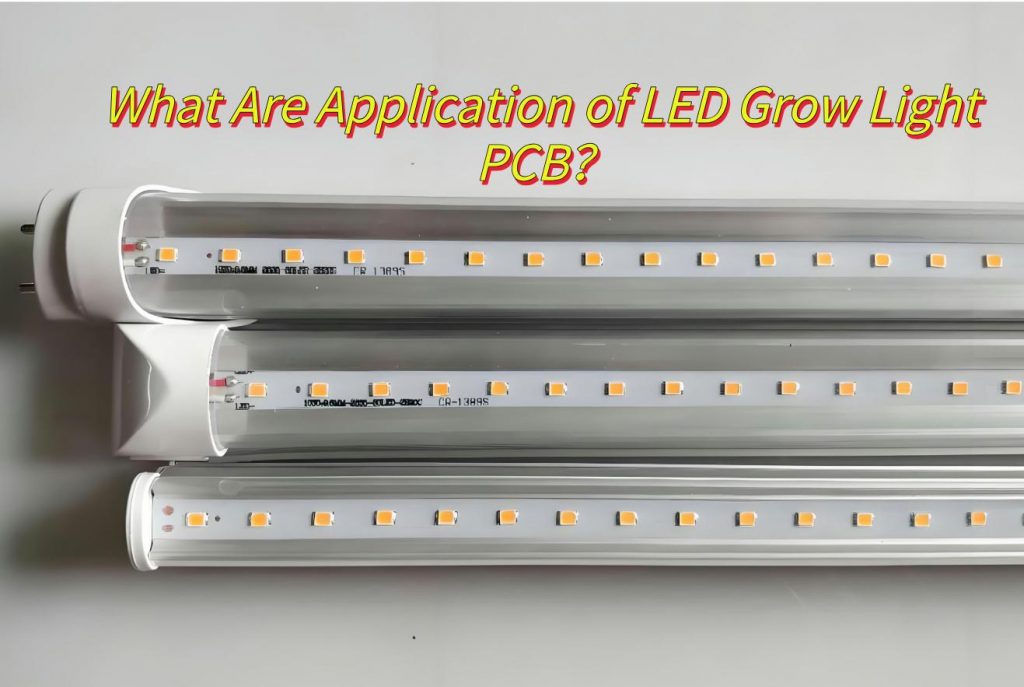
How to Find a LED Grow PCB Manufacturer?
Here are some ways to find a LED grow PCB light manufacturer:
- Search Keywordsâ: Use terms like âLED grow light PCB manufacturerâ or âPCB LED grow light factoriesâ or âLED grow light PCB exportersâ on Google website or B2B platforms.
- âTrade Showsâ: Attend exhibitions like âThe China Import and Export Fairâ to meet verified suppliers.
- âCertificationsâ: Filter factories with UL, CE, or RoHS compliance to ensure quality.
How to Choose a Reliable LED Grow PCB Light Manufacturer?
This is what reliable LED grow PCB light manufacturers should have:
- Adopted IP65 above protection standard
- ISO 9001, RoHS, UL-certified factories for consistent quality.
- Support OEM/ODMÂ custom grow light PCB Service
- Competitive Price and fast delivery.( 24 hours delivery)
- Provide one to one free technical support and after-sales service
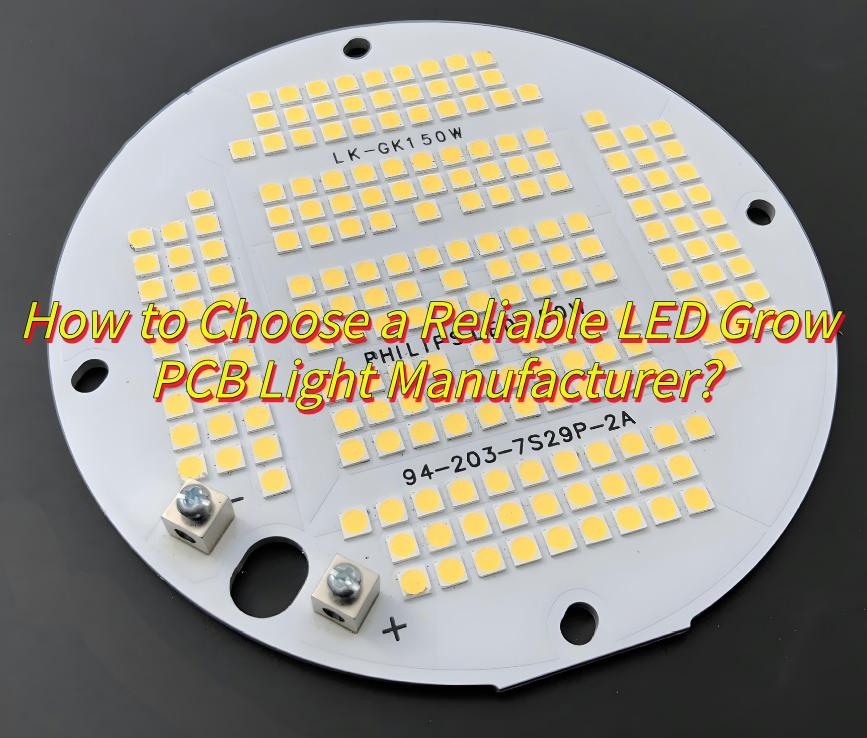
Best Technology all meet these above requirements, if you’re interested in us, please leave a message below this blog.
How Much Does an LED Grow Light Board Cost?
The cost of an LED grow light PCB board varies based on material, design complexity, and order quantity. Basic aluminum PCBs cost around $1 to $5 per piece, while high-performance ceramic PCBs can be more expensive. Bulk orders typically lower the per-unit cost, making it essential to balance quality and pricing when choosing a supplier. If you want to get a quote for your case, please contact us.( The email is at the beginning of this blog)
How to Reduce the Production Cost of LED Grow Light PCB boards?
Design Simplificationâ: Use standard PCB sizes (e.g., 300x300mm) to avoid custom tooling fees.
âBulk Purchasingâ: Negotiate discounts for LED chips and aluminum substrates.
âAutomationâ: Deploy SMT machines to cut labor costs by 40-60%.
âEnergy Savingsâ: Switch to high-efficiency LEDs (e.g., 220 lm/W) to reduce the number of chips per board.
âRecyclingâ: Reuse defective boards for non-critical components.
FAQs of LED Grow Light PCB board
Q1:Can I customize an LED grow light PCB?
A1:Yes, manufacturers like Best Technology offer custom designs based on specific requirements.
Q2:What certifications should an LED grow light PCB manufacturer have?
A2:ISO9001, RoHS, and UL certifications ensure quality compliance.
Q3:Which manufacturers provide customized spectrum LED plant light PCB? â
A3:Professional manufacturers such as BEST technology support red and blue light ratio adjustmentâ.
Q4:âHow does aluminum substrate PCB improve the life of plant lights? â
A4:High thermal conductivity aluminum prevents LED light decay and is suitable for 24/7 greenhouse environmentsâ.
âQ5:âWhat is the waterproof standard for home hydroponic lamp PCB? â
A5:Mainstream products use IP65 protection and are suitable for humid planting scenesâ.
In conclusion, that’s all about LED grow light PCB and how to select a LED grow light PCB manufacturer. More information you can contact Best technology.