Printed Circuit Board Factory is more than just a place that makes circuit boards. It’s the backbone of modern electronics. From phones to cars, everything starts here. Whether you’re a startup or a large company, finding a reliable factory matters. In todayâs blog, letâs dive into what makes a great PCB factory. Weâll also show you why Best Technology stands out in the crowd.
Best Technology is a PCB manufacturing factory, offering no MOQ and quick turn support with global certifications to global customers. We ship globally and have strong partnerships with our customers. You can get PCB manufacturing, PCB assembly, and testing in one place. If you have any urgent projects, we also offer a 24-hour quick turn for you. We can provide quotes quickly. Our team can send a quote within 1 hour during business hours. We maintain consistency of quality and are not just looking for quantity during production. We are committed to providing the most suitable PCBs for customers. If you have any PCB board projects that need support, pls email your Gerber file to us at sales@bestpcbs.com.
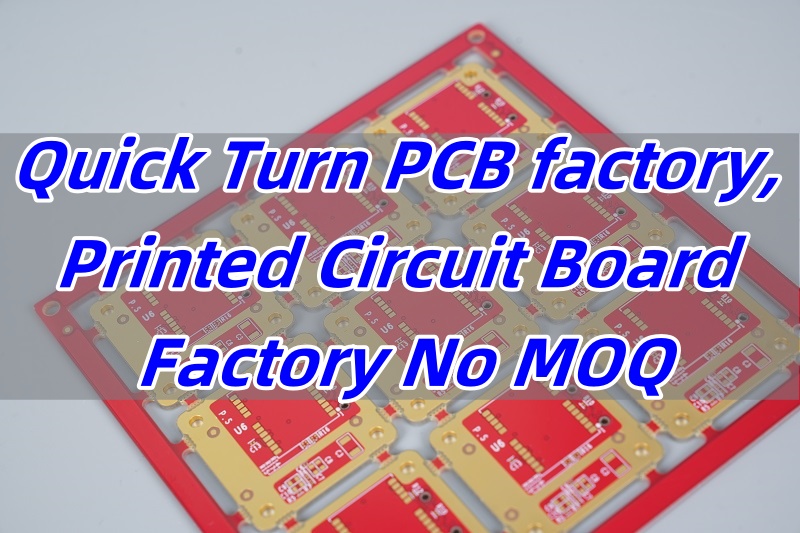
What is the Best PCB Printed Circuit Board Factory?
Finding the best PCB factory depends on what you need. Some offer cheap prices but long lead times. Others promise speed but fail in quality. So, how do you know whoâs best?
A great PCB factory:
- Delivers high quality.
- Meets tight deadlines.
- Offers full PCB assembly.
- Keeps communication clear.
- Has strong certifications.
If you want a balance of speed, quality, and service, look for factories that use advanced equipment and follow global standards. They should support small and big orders alike.
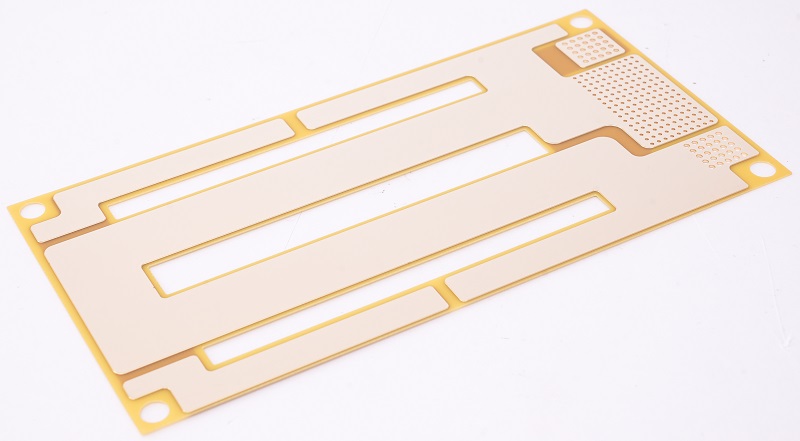
Who Manufactures PCB?
PCB manufacturers are found worldwide. But not all are equal. Best Technology is one of the top PCB board factory options in Asia. We serve global clients with fast service and no minimum order. Best Technology stands out because:
- We use environment-friendly material compliant with RoHS, REACH, and UL. And all material is traceable from our ERP and MES systems.
- We support quick turn and custom designs.
- Our engineers guide you from design to delivery.
- We offer PCB printing, assembly, and testing in one house.
When you choose a reliable partner like us, you save time and reduce waste. That’s key in todayâs fast-moving tech world.
Who is the Largest Printed Circuit Board Factory in the US?
The US is home to some big PCB players. While many companies source from Asia, these local giants lead in medical, aerospace, and high-tech industries:
- TTM Technologies â Offers everything from quick turn to high-layer PCBs. Serves medical and automotive.
- Sanmina Corporation â Strong in PCB assembly and system integration.
- Advanced Circuits â Popular for small orders and fast delivery. Well-known among engineers and startups.
These companies often serve large-volume needs. But for flexible and budget-friendly options, many turn to factories in Asia like Best Technology.
Quick Turn PCB Factory Malaysia
Malaysia is growing as a strong PCB hub. With government support and skilled labor, it offers solid quality with better rates than some Western factories. Some notable names in Malaysia include:
- JJS Electronics â Known for small batch builds.
- Inari Amertron â Supports advanced IC packaging.
- NationGate â Offers EMS and PCB assembly.
While Malaysia is rising fast, Best Technology remains a top choice in Asia for clients worldwide. Our quick turn PCB factory setup cuts lead time while maintaining quality.
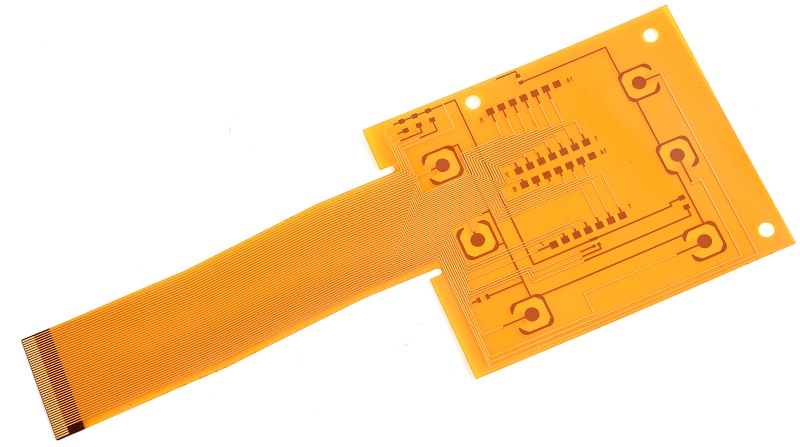
How is Printed Circuit Board Manufacturing Process?
The process starts with your design and ends with a tested board in your hand. Hereâs a simple breakdown:
- Design & Layout â You share your Gerber files and BOM.
- Material Prep â We prepare the copper-clad laminate.
- Imaging â The circuit pattern is transferred using UV light.
- Etching â Unwanted copper is removed.
- Drilling & Plating â Holes are drilled and plated for connections.
- Solder Mask & Silkscreen â We apply protective layers and print labels.
- Surface Finish â ENIG, HASL, or other finishes are applied.
- Testing â Each board is tested for open/shorts.
This process needs precision. Even a tiny flaw can cause failure. Thatâs why a professional factory matters.
How Much Does It Cost to Manufacture a Printed Circuit Board?
Prices vary by size, layers, materials, and quantity. Hereâs a quick look at what impacts cost:
- Layers: More layers = higher cost.
- Board Size: Larger boards cost more.
- Finish: ENIG costs more than HASL.
- Lead Time: Quick turns cost extra.
- Assembly: More components, more cost.
At Best Technology, we give fair prices. No hidden charges. No minimum order. You can even get a quote in 1 hour.
By the way, weâve got some exciting news to share with you! Weâll be at the New-Tech Exhibition 2025 in Israel from May 20th to 21st, and our booth number is 78. Weâll be showing a range of products including PCB, MCPCB, ceramic PCB, FPC, rigid-flex PCB, and PCBA. If any interested, just come visit us at booth 78 and discuss your requirements there face-to-face.
Why Should You Choose Best Technology as Your Trusted Quick Turn PCB Factory?
Best Technology isnât just another Printed Circuit Board Factory. We aim to be your long-term partner. Hereâs why weâre trusted by hundreds of clients:
- Speed â Our quick turn service delivers in as little as 24 hours.
- Flexibility â We support any order size. No MOQ required.
- Certifications â ISO9001, IATF16949, ISO13485, AS9100D.
- Full Service â From PCB printing to full assembly.
- Pro Support â Our team helps with design, DFM checks, and more.
Weâre more than a supplier. Weâre your partner in every step of your product journey.
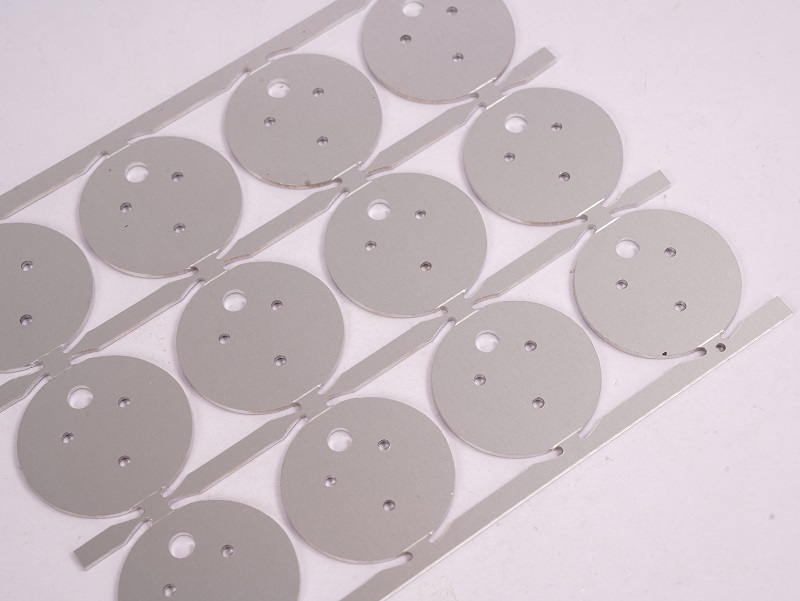
In conclusion, in todayâs world, speed and quality are everything. Choosing the right PCB assembly factory can decide your productâs success. Thatâs why companies in the US, India, Canada, UK, and Malaysia trust Best Technology.
We serve clients from startups to big brands. With no MOQ, fast delivery, and one-on-one support, we help you stay ahead. Whether you’re in need of a circuit board factory for prototypes or mass production, weâve got you covered. If youâre looking for a trustworthy printed circuit board factory no MOQ that meets tight deadlines with top quality, contact Best Technology via sales@bestpcbs.com. We offer complete service from bare board to fully assembled units.