In today’s rapidly developing electronic technology, aluminum substrates, as a key electronic component carrier, play a vital role. Aluminum substrate manufacturers are an indispensable backbone in this field. They provide high-quality products to the electronics industry with advanced technology and strict quality control.
Reasons for the development of aluminum substrate
The continuous updating and improvement of aluminum substrate technology has provided a strong driving force for the development of manufacturers. In terms of thermal conductivity, in order to meet the application needs of different fields, the thermal conductivity of aluminum substrates has been continuously improved, and has now reached more than 180W/mK.
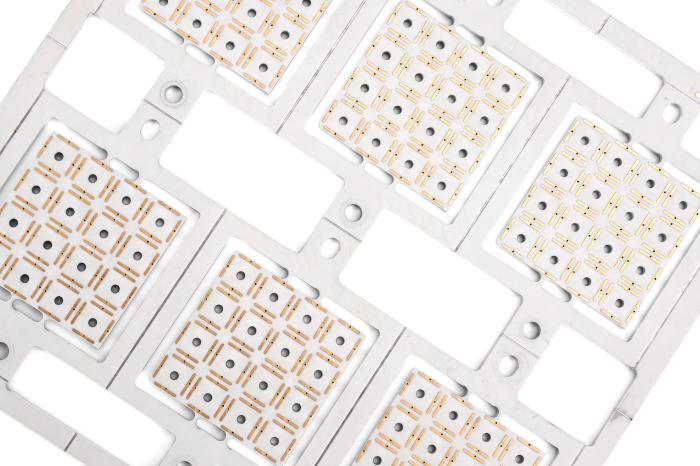
In terms of molding and processing technology, commonly used molding processes include cutting, punching and bending, and the continuously optimized molding and processing technology has improved the production efficiency and product quality of aluminum substrates.
In addition, technological innovation has also promoted the diversified development of aluminum substrate products, such as ultra-thin aluminum substrates, high-frequency and high-speed aluminum substrates, flexible aluminum substrates, composite functional aluminum substrates, environmentally friendly aluminum substrates and other new products have emerged continuously, meeting the needs of different industries and application fields.
What are the types of aluminum substrates?
(I) Flexible aluminum substrate
The material system of flexible aluminum substrate is usually a polyimide resin system with ceramic fillers, which can provide excellent electrical insulation, flexibility and thermal conductivity.
For example, in some portable electronic devices that require special shapes, flexible aluminum substrates can better adapt to the internal space of the device, eliminating expensive fixtures, cables and connectors, and reducing overall costs.
At the same time, due to its good flexibility, it can also play an important role in some bendable electronic products, such as foldable displays.
(II) Multilayer aluminum substrate
In the high-performance power supply market, multilayer aluminum substrates are made of multiple layers of thermally conductive dielectrics. These structures have one or more layers of circuits buried in the dielectric, and blind holes are used as thermal vias or signal paths.
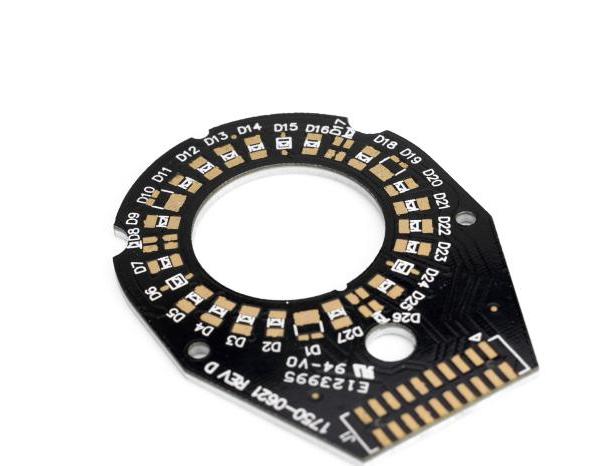
Although it is more expensive and less efficient to transfer heat with a single-layer design, they provide a simple and effective heat dissipation solution for more complex designs. For example, in some high-end server power supplies, industrial power supplies and other fields, the heat dissipation requirements are extremely high. Multilayer aluminum substrates can meet the heat dissipation needs of these complex electronic devices and ensure the stable operation of the equipment.
(III) Through-hole aluminum substrate
In the most complex structures, a layer of aluminum can form the “core” of a multi-layer thermal structure.
Before lamination, the aluminum is pre-plated and filled with dielectrics. Thermal materials or sub-assemblies can be laminated to both sides of the aluminum using thermal bonding materials. Once laminated, the completed assembly is similar to a traditional multi-layer aluminum substrate through drilling.
The plated through-holes pass through the gaps in the aluminum to maintain electrical insulation. Alternatively, the copper core can allow direct electrical connection as well as insulating through-holes. This complex structure makes it play an important role in some high-end electronic devices with extremely high requirements for electrical insulation.
What is the dielectric material of aluminum PCB?
The dielectric material selection of aluminum PCB is diverse, designed to meet different performance requirements. Epoxy resin is widely used for its toughness and heat resistance, while polyimide is known for its high temperature stability and chemical stability.
Polystyrene is favored for its low dielectric constant and dielectric loss tangent, while acrylic ester is selected for its excellent light transmittance. In addition, ceramic materials such as alumina, silicon nitride, zirconium oxide, etc. are also commonly used dielectric materials for aluminum PCBs due to their excellent insulation, thermal conductivity, oxidation resistance, and high-temperature stability.
Different dielectric materials have different dielectric constants and thermal properties, which are particularly important for applications in high-frequency and high-temperature environments. Polytetrafluoroethylene (PTFE) and ceramic substrates are particularly suitable for high-frequency and high-temperature environments due to their high temperature resistance and low dielectric constant.
In summary, there are a wide variety of dielectric materials for aluminum PCBs, including epoxy resin, polyimide, polystyrene, acrylic ester, alumina, silicon nitride, zirconium oxide, etc. These materials are selected based on their respective advantages to meet the performance requirements of aluminum PCBs in specific applications.
What is the thermal resistance of aluminum PCB?
The thermal resistance of aluminum PCBs ranges from 1℃/W to 2℃/W. This data is in sharp contrast to the thermal resistance of FR4 PCBs, which ranges from 20℃/W to 22℃/W.
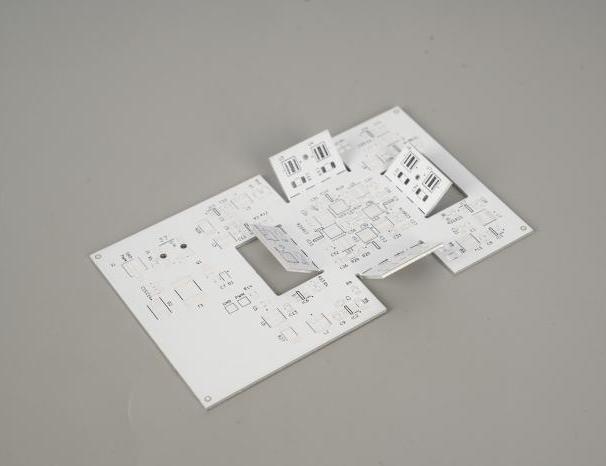
This shows that aluminum PCB is significantly better than FR4 PCB in heat dissipation performance. Aluminum material has good heat dissipation effect, which can effectively reduce the heat generated by electronic equipment during operation and keep components running at a suitable working temperature, thereby improving the stability and service life of the equipment.
What are the production processes of aluminum substrates?
- First, the material is cut, and the incoming material inspection is strengthened to ensure that the sheet with a protective film on the aluminum surface is used. After cutting, there is no need to bake the sheet, and it should be handled with care, paying attention to protecting the protective film on the aluminum base surface.
- Next is drilling. The drilling parameters are the same as those of FR-4 sheet materials. At the same time, the aperture tolerance must be strictly controlled, especially for 4OZ-based Cu. Pay attention to controlling the generation of flash, and drill with the copper skin facing up.
- Then enter the dry film optical imaging link, including incoming material inspection, grinding, filming, board clapping, exposure and development.
- When inspecting the board, the circuit surface must be inspected according to MI requirements for various contents, and the dry film on the aluminum base surface must not have film falling or damage.
- In the etching process, since the copper base is generally 4OZ, etching is difficult. After the aluminum surface without protective film is taken out of the film stripping liquid, it should be washed with water in time to prevent the alkali solution from biting the aluminum surface.
- The production process of the green oil process is grinding the plate (only brushing the copper surface) → silk screen printing green oil (first time) → pre-baking → silk screen printing green oil (second time) → pre-baking → exposure → development → grinding machine pickling soft brush → post-curing → next process.
- Before spraying tin, tear off the protective film of the aluminum substrate with protective film, hold the edge of the plate with both hands, and it is strictly forbidden to touch the inside of the plate directly with your hands. Pay attention to the operation to prevent scratches.
What are the characteristics of aluminum substrate manufacturers?
(I) Good processing and production effect
Aluminum substrate manufacturers can make full use of the material properties of the aluminum substrate itself according to the actual processing size to bring better processing and production effects for building material design.
(II) Stable and reliable quality
Aluminum substrate manufacturers focus on product quality and stability, and use high-quality raw materials and strict production standards. They have a complete production system and quality control system to ensure the quality and stability of products.
(III) Advanced production technology
Aluminum substrate manufacturers use advanced production technology and equipment to ensure product accuracy and stability. They have professional sales and technical teams that can provide high-quality products and technical support.
(IV) Energy saving and environmental protection
Aluminum substrate manufacturers focus on the energy saving and environmental protection of their products, and use energy-saving and environmentally friendly materials and production processes. They have strong R&D and technical strength, and continue to launch new energy-saving and environmentally friendly products and technological innovations.
What is the market prospect of aluminum substrate manufacturers?
The continuous emergence of new generation electronic products, such as smart phones, tablets, wearable devices, etc., has higher and higher requirements for heat dissipation performance and thinness. Aluminum substrates, as a metal-based copper-clad laminate with good heat dissipation function, just meet these needs.
The development of emerging technologies such as 5G has also brought new opportunities to the aluminum substrate market. Aluminum substrates, as a metal-based copper-clad laminate with good heat dissipation and electrical properties, just meet the needs of 5G communication technology.
The trend of lightweight vehicles and the expansion of the new energy vehicle market have also brought new opportunities to the aluminum substrate market. Aluminum substrates, as a metal-based copper-clad laminate with the characteristics of lightweight, high strength and corrosion resistance, just meet the needs of lightweight vehicles.
In short, aluminum substrate manufacturers play an important role in the electronics field. They provide high-quality aluminum substrate products to the electronics industry with advanced technology, strict quality control, continuous innovation and research and development, and good customer service.