What is Aluminum PCB Circuit Board?
An aluminum PCB, also known as an aluminum circuit board, is a type of metal core printed circuit board that uses aluminum as its base material. Unlike traditional PCBs, which are typically made with fiberglass, aluminum PCBs offer superior heat dissipation. This makes them ideal for high-power applications where excess heat can damage sensitive components. Aluminum PCBs are widely used in industries such as LED lighting, automotive, and power equipment because they provide better thermal management.
Aluminum PCBs are made from a combination of the following materials:
- Aluminum Substrate: The base layer, responsible for mechanical support and heat dissipation.
- Dielectric Layer: This layer provides insulation between the conductive layer and the aluminum base, while also helping with thermal transfer.
- Conductive Layer: Made of copper, this layer is etched to form the circuit pattern and provides electrical connectivity.
- Solder Mask Layer: This is a protective layer to protect the traces.
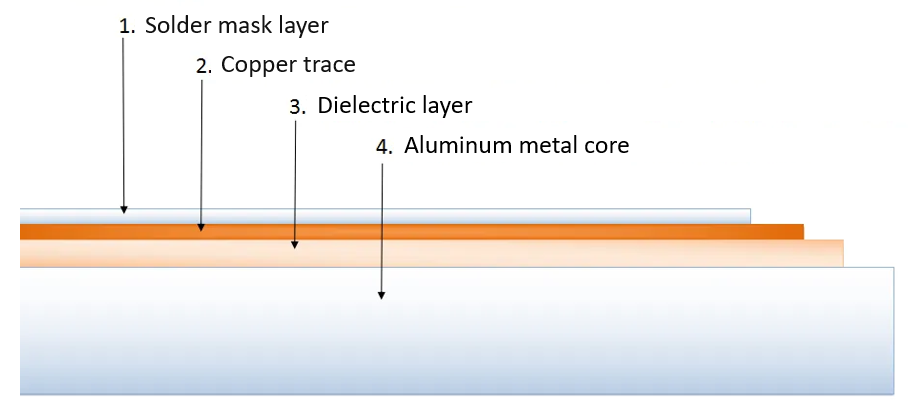
Types of Aluminum PCB
Aluminum circuit board is a kind of metal base copper clad plate with good heat dissipation function, the main types include single-sided aluminum PCB, double-sided aluminum PCB and multi-layer aluminum PCB.
Single sided aluminum PCB
The single-sided aluminum substrate is composed of a conductive graphic layer and an insulating material plus aluminum plate, which is relatively simple in structure and suitable for the installation and connection of some basic electronic components.
Double sided aluminum PCB
The double-sided circuit aluminum substrate has two layers of conductive graphics layer and the insulating material plus aluminum plate superimposed together, providing a larger circuit layout space and better heat dissipation effect, which is often used in electronic devices requiring higher integration and better heat dissipation performance.
Multilayer aluminum PCB
Multi-layer printed aluminum-based circuit board consists of three or more layers of conductive graphic layer and insulating material and aluminum plate alternately laminated together, with complex circuit design and excellent heat dissipation performance, suitable for high-end applications such as LED lighting, automotive electronics .
In addition, there are other special types of aluminum-based circuit boards, such as flexible aluminum substrates, mixed aluminum substrates, etc. Flexible aluminum substrate has excellent electrical insulation, flexibility and thermal conductivity, and is suitable for product design in various shapes and angles. The hybrid aluminum substrate is a multilayer component made of conventional FR-4 bonded to an aluminum substrate with a thermoelectric medium, designed to improve heat dissipation and rigidity, and used as a shield .
Aluminum PCB Features
The aluminum substrate, a metal-based cooling plate (including aluminum, copper, and iron substrates), is made from a low-alloyed Al-Mg-Si series high-plastic alloy plate. This material offers excellent thermal conductivity, electrical insulation, and mechanical processing capabilities. When compared to traditional FR-4 materials, aluminum substrates of the same thickness and line width can carry higher currents. Additionally, they can withstand voltages up to 4500V and have a thermal conductivity greater than 2.0, making aluminum substrates the preferred choice in the industry.
● Surface mount technology (SMT);
● Very effective treatment of thermal diffusion in circuit design;
● Reduce product operating temperature, improve product power density and reliability, extend product service life;
● Reduce product volume, reduce hardware and assembly costs;
● Replace fragile ceramic substrate for better mechanical durability.
Aluminum PCB vs. Copper PCB
Both aluminum and copper PCBs have their own advantages, but they cater to different applications:
1. Thermal Conductivity
In general, the higher the thermal conductivity, the more efficient the heat transfer, resulting in better heat dissipation and a longer lifespan. Among metal substrates, copper substrates offer the best thermal conductivity, outperforming aluminum substrates.
2. Electrical Conductivity
Both aluminum and copper are metals and conduct electricity, though their exact levels of conductivity differ. In terms of electrical conductivity, copper is significantly superior to aluminum. In applications that require high electrical conductivity, copper is the ideal choice.
3. Resistance
Resistance is crucial in PCB design as it affects the overall functionality and stability of the components. Given that copper has a higher density than aluminum, its resistance is generally lower. Therefore, in applications requiring thinner circuits and faster power transmission, copper is the better option.
4. Weight
Due to copper’s higher density per unit area, copper PCBs are much heavier than aluminum PCBs with the same design.
In applications where lightweight structures are critical, aluminum is the preferred material. On the other hand, applications where weight is not a major concern often favor the use of copper.
5. Applications
Aluminum substrates are somewhat specialized. They are mainly used in energy-saving lighting products such as indoor lighting, energy-efficient lighting, and street lights. Copper substrates are suitable for high-power lighting equipment like car headlights, tail lights, and some high-tech electronics.
6. Manufacturing Process
The manufacturing process for aluminum-based PCBs is simpler than that for copper-based PCBs, which also impacts their production time and delivery schedules. Below is aluminum PCB and copper core PCB that made by Best Technology:
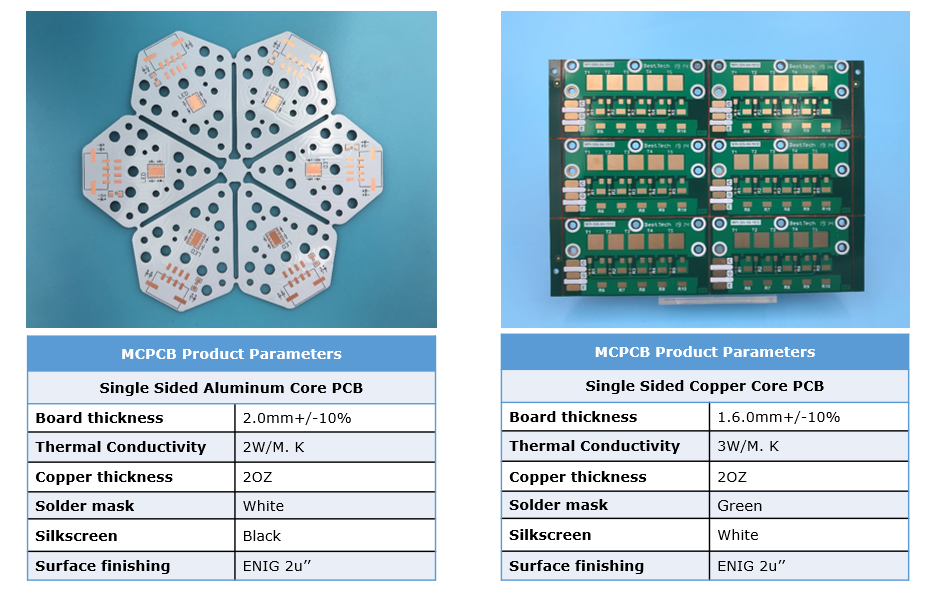
Aluminum PCB Manufacturing Process
The manufacturing process for aluminum PCBs involves several steps to ensure high quality and performance. Here is a basic manufacturing process of aluminum PCB:
1. Substrate Selection and Preprocessing
Aluminum alloys with high thermal conductivity, such as the 5052 and 6061 series, are selected as the base material. The aluminum sheet is first cut and cleaned to remove surface grease and impurities, ensuring proper adhesion for subsequent processes.
2. Chemical Etching of Patterns
Photosensitive ink is used to form the desired circuit patterns on the aluminum surface. After exposure and development, the ink-covered areas protect the underlying aluminum from being etched by chemicals, while the unprotected areas are etched away, forming the circuit pattern.
3. Insulation Layer Deposition
To achieve electrical isolation, an insulating material, usually thermosetting resin or ceramic-filled epoxy resin, is deposited on the aluminum substrate. This step is typically completed using screen printing or inkjet printing technology to ensure a uniform and appropriately thick insulation layer.
4. Metallization
Creating conductive paths on the insulation layer is a key step. Copper foil is deposited onto the insulation layer using methods such as electroplating, sputtering, or chemical copper deposition. This copper foil serves as the conductive layer for connecting LED chips and other components.
5. Drilling and Metallization
Holes are drilled in the board according to the design to achieve electrical connections between different layers. The hole walls are then metallized to ensure good conductivity inside the holes.
6. Surface Treatment
To improve solderability and corrosion resistance, the aluminum substrate undergoes additional surface treatments, such as tin spraying, gold plating, or silver plating.
7. Assembly and Testing
LED chips, resistors, capacitors, and other components are soldered onto the circuit board to complete the assembly. Here you can see the whole manufacturing process of aluminum metal core PCB.
What Affects Aluminum PCB Circuit Board Price?
First of all, raw material cost is one of the important factors affecting the price of aluminum based circuit board. The raw materials of aluminum substrate include aluminum substrate and other auxiliary materials, such as insulating layer materials. The price fluctuation of aluminum substrate will directly affect the production cost of aluminum substrate, and then affect its market price. In addition, the cost of electricity is also a part of the production process cannot be ignored, the fluctuation of electricity price will further affect the production cost .
Secondly, market supply and demand is also a key factor in determining the price of aluminum-based circuit boards. If demand increases and supply is insufficient, prices will naturally go up. On the other hand, if there is an oversupply, the price will fall. Changes in demand in the construction, automotive and other industries, as well as changes on the supply side such as the construction of new plants or the closure of old plants, will have a direct impact on the price of aluminum-based circuit boards .
The macroeconomic environment also has an important impact on the price of aluminum-based circuit boards. When economic growth is expected to be good, the demand for aluminum substrate in related industries increases, driving up prices; The expectation of economic recession will lead to a decline in demand and pressure on aluminum substrate prices .
Policies and regulations is also one of the factors affecting the price of aluminum-based circuit boards. The government’s environmental protection policies, trade policies and industry subsidies will have an impact on the aluminum substrate market. For example, environmental policies that limit production may reduce supply and push up prices; The establishment of trade barriers may affect the import and export of aluminum substrate, and then affect the domestic market price.
Aluminum PCB Production Capability – Best Technology
Best Technology is known for its strong production capability when it comes to aluminum PCBs. Our manufacturing facilities are equipped with the latest technology to produce high-quality aluminum PCBs that meet industry standards. We have the ability to produce single-sided, double-sided, and multi-layer aluminum PCBs, below you can see our capability of aluminum PCBs:
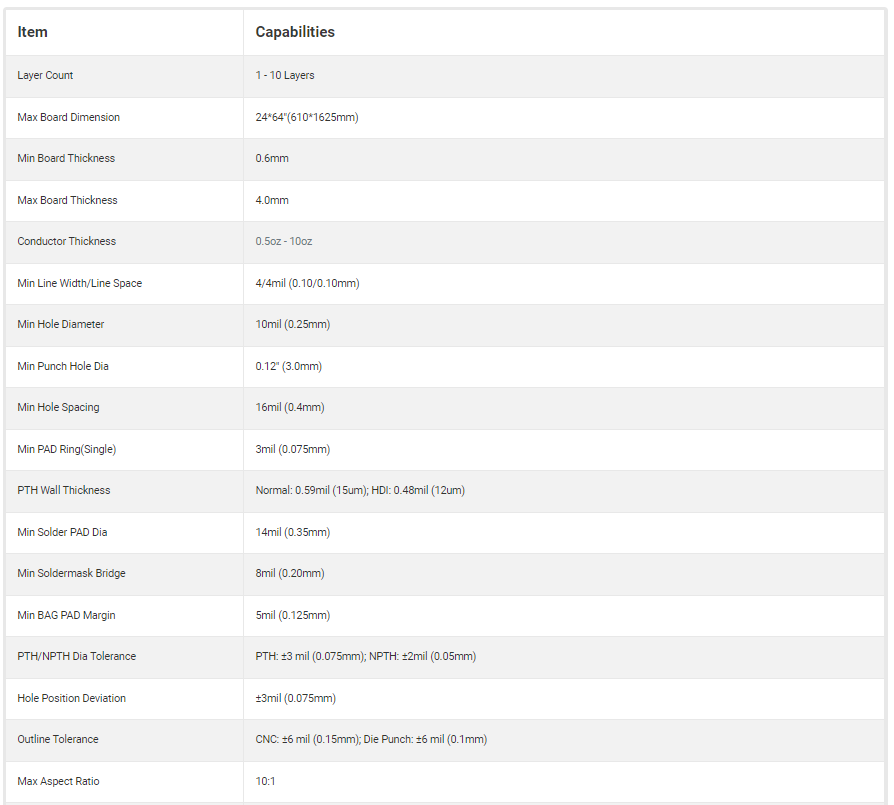
Applications of Aluminum PCB
Aluminum PCBs are used in a variety of applications, particularly where heat management is crucial:
- LED Lighting
- Automotive Electronics
- Power Supplies
- Consumer Electronics
- Medical
- Household appliance
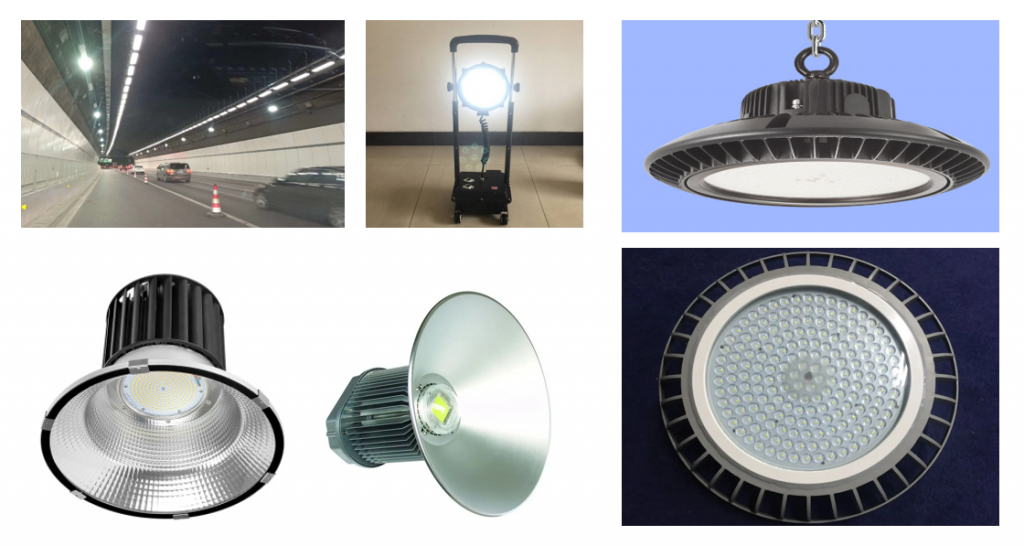
FAQs about Aluminum PCB Circuit Board
1. What is the main advantage of aluminum PCBs?
Aluminum PCBs excel in thermal management, making them perfect for heat-sensitive applications.
2. Are aluminum PCBs expensive?
No, aluminum PCBs are generally affordable, making them a cost-effective option for many industries.
3. Can aluminum PCBs be used in consumer electronics?
Yes, aluminum PCBs are commonly used in consumer electronics, especially in devices that generate significant heat.
4. What industries commonly use aluminum PCBs?
Industries such as automotive, LED lighting, and power supplies frequently use aluminum PCBs due to their thermal properties.
5. Is aluminum PCB better than copper PCB?
It depends on the application. Aluminum is better for heat dissipation, while copper excels in electrical conductivity.