If you are familiar with SMT or PCB assembly process, you may know BOM file. It is an important element in the SMT process. Creating BOM is a crucial step in the manufacturing process, especially for PCBs. A BOM serves as a comprehensive list of all the parts, components, and materials needed to build your product. It ensures that everyone involved in the production process is on the same page, reducing the risk of errors and delays. Today, Best Technology would like to introduce BOM and giving you a guide to create a BOM file step by step.
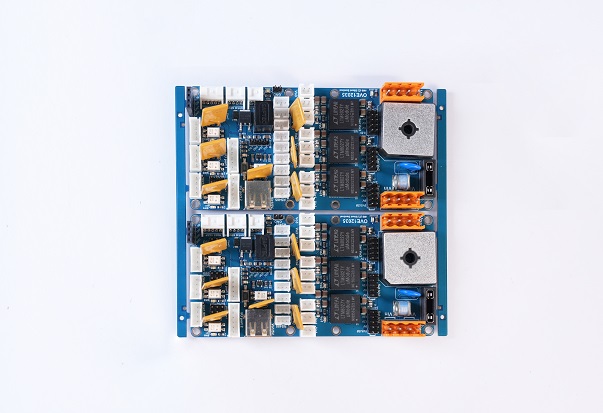
What is a Bill of Materials (BOM)?
A Bill of Materials (BOM) is a detailed list of all the parts, components, and materials needed to manufacture a product. In PCB manufacturing, a BOM outlines every item required to assemble a PCB, including quantities, part numbers, and descriptions. It serves as a guide to ensure that the manufacturing process runs smoothly and that no crucial components are missing.
Types of Bill of Materials
There are several types of BOMs used in different stages of production. Each type serves a specific purpose and provides unique details to streamline processes and ensure accuracy. Here are the primary types of BOMs:
- Engineering BOM
This type of BOM is creating during the design phase. It lists all the parts and components designed by the engineering team, including specifications and relationships as intended in the final product. And of course, it mainly used by design engineers to communicate the product structure and details to manufacturing teams.
- Manufacturing BOM (Formal)
It is a formal BOM files that used in the assembly phase. Different with engineering BOM, it includes additional details necessary for manufacturing, such as packaging, handling instructions and assembly details. And some special instructions.
- Sales BOM
Sales BOM is used by sales teams and includes information relevant to the sales process, such as pricing and availability. It helps in providing accurate quotes, managing customer expectations, and handling sales orders efficiently.
What Should Include in an Effective Bill of Materials?
An effective BOM should be detailed, accurate, and easy to understand. It should include all the details of components and indicated revisions. As a 18 years expertise in PCBA production, we summarized the key elements that should be included in the BOM.
- Component details
It should include all the components and their detailed information, such as names, part numbers (PN), and descriptions for each part.
- Quantity (QTY)
The exact quantity of each component required for the product. Accurate quantities can prevent shortages and overstocking.
- Foot print
It is the package of each component, helping to ensure the correction of part.
- Reference Designators
Unique identifiers that match each component to its specific location on the product layout. These are essential for assembly and troubleshooting.
- Manufacturer Information
Manufacturer information, including the manufacturer name of components and manufacturer part number. It helps to ensure correct parts are sourced. And convenient for alternative part sourcing if it is shortage.
- Supplier information (Optional)
It means the name of the supplier or distributor. The part number used by the supplier, which may differ from the manufacturer’s part number.
- Assembly instructions
Any special notes for assembly such as DNF remark, and version control to track revisions should also be included. Additionally, cost information helps in budgeting, and lifecycle status information helps plan for component availability and avoid discontinued parts.
How to Make a PCB Bill of Materials (BOM)?
Creating a PCB BOM is a systematic process that involves compiling all the necessary information about each component required for the assembly of the PCB. Here’s a detailed guide on how to create a PCB BOM:
- Open a Blank Spreadsheet
Use software like Microsoft Excel or Google Sheets to start with a blank spreadsheet. They are common to use, offering flexibility and ease of use for creating and managing BOMs.
- Define Columns
Set up your spreadsheet with appropriate column headers. Common headers include:
- Part Number
- Component Name
- Quantity
- Reference Designator
- Manufacturer
- Manufacturer Part Number
- Supplier
- Supplier Part Number
- Description
- Package Type
- Cost
- Notes
- Input Data
Enter the required details for each component under the appropriate headers. Please be make sure that all information is accurate and complete. This may involve referencing design files, datasheets, and supplier catalogs. If it is incorrect, then it needs a lot of time to find out and revise the errors, resulting in schedule delay.
- Use Formulas
Utilize Excel formulas to automate calculations, such as summing total quantities or calculating costs. This helps in reducing manual errors and saves time.
- Format for Clarity
Use cell formatting options to highlight important information and ensure the spreadsheet is easy to read. For example, you can use bold text for column headers, color coding for different component types, and borders to separate sections.
- Include Version Control
Add a version control section to your BOM to track revisions and updates. This can be a simple row at the top or bottom of the spreadsheet, indicating the version number, date of revision, and a brief description of changes.
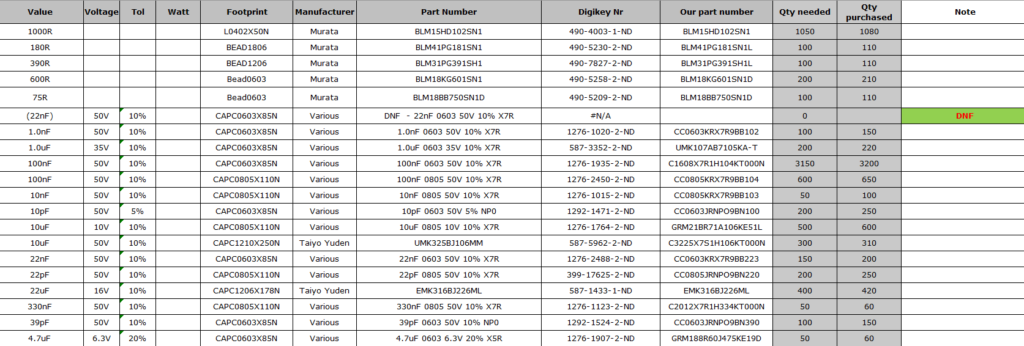
- Save and Update
Save your BOM and update it regularly to reflect any changes in the design or component availability. Regular updates ensure that the BOM remains accurate and up-to-date, preventing issues during production.
- Review and Verify
Have multiple team members review the BOM for accuracy. Cross-check all component details, quantities, and part numbers against the design files. Verification helps catch errors early and ensures the BOM is reliable.
- Communicate with Suppliers:
Maintain open communication with suppliers to confirm component details and availability. This ensures that you can source the correct parts and avoid delays in the production process.
How Can I Optimize My BOM for PCB Assembly?
Sometimes, a simple BOM is not good to process PCB assembly process, and manufacturers may need to spend a lot of time to optimize it, make into convenient for manufacturing. If you are a layman, here are some steps to help you in optimizing your BOM file.
First, it’s a good idea to standardize components where possible. Using standard parts that are readily available from multiple suppliers can simplify procurement and reduce costs. This approach minimizes the risk of shortages and ensures you can get parts quickly and affordably. Also, make sure all entries in your BOM are clear and concise to avoid confusion during assembly. Double-checking part numbers and quantities against design files is crucial to prevent errors that could lead to rework or delays.
Building strong relationships with your suppliers is another key factor. Good communication with suppliers helps ensure reliable component availability and keeps you informed about any changes in lead times or part availability. Regularly updating your BOM to reflect any design changes or component availability issues is essential. Keeping your BOM current and accurate prevents last-minute surprises during assembly.
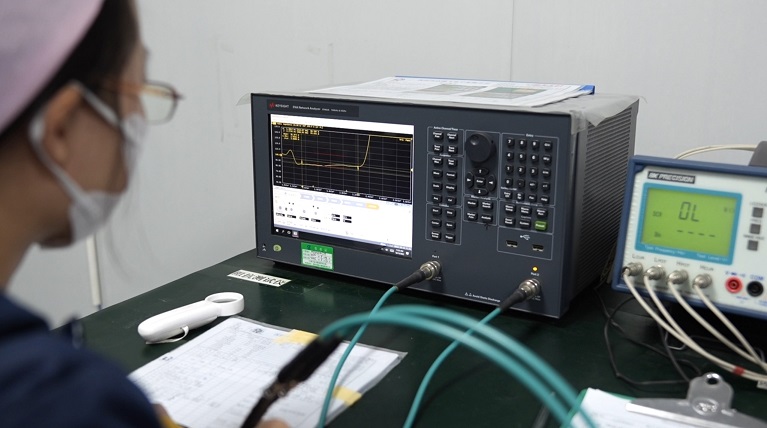
What Common Mistakes Should I Avoid When Creating a PCB BOM?
Avoiding common mistakes in BOM creation can save time and reduce errors. Here are some pitfalls to watch out for:
- Incomplete information – ensure all necessary details are included for each component.
- Incorrect quantities – double-check quantities to avoid shortages or excess inventory.
- Outdated data – keep the BOM updated with the latest design changes and component information.
- Ambiguous descriptions – provide clear and precise descriptions to prevent confusion.
- Lack of version information – implement version control to track changes and ensure the correct BOM version is used.
Creating an effective and accurate PCB BOM is essential for smooth manufacturing and assembly. By following best practices and using the right tools, you can ensure your BOM is comprehensive, clear, and up-to-date, ultimately leading to a successful PCB production process.
Best Technology is an expert in SMT and PCB assembly, we have more than 18 years in this industry, that can offer you a best experience of PCBA solution. In our facotry, we have advanced equipment like full auto pick and place machine, online dual AOI, X-ray, 3D SPI, nitride reflow oven and three-proof paint machine. So that we can ensure the fast lead time and high quality of your PCBA products. Reach us to get a instant quote!