As everyone knows for FR4 PCB, people like the vias to be tented or filled for some special applications.
Ceramic PCB is more and more popular because of the thermal conductivity is very high and very good for heat dissipation. Most of customers are going to make the PCB with ceramic material, includes Al2O3, AlN, BeO or Si3N4, etc.
So do the vias can be filled for ceramic PCB becomes the frequently asked questions (FAQ).
The answer is YES.
So what’s the material can be filled in vias for DBC/DPC alumina PCB/ Aluminium Nitride PCB?
The material can be solder mask, Dow Corning 1-4173 and copper/Cu.
Normally, customers want the vias/holes to be filled with copper.
Because copper can fill the vias very well and it is easier to do and it looks very good. Please see below photo.
The left one with filling with copper, the right one without filling copper
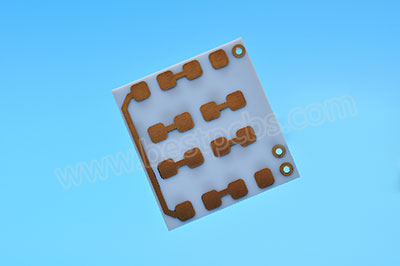
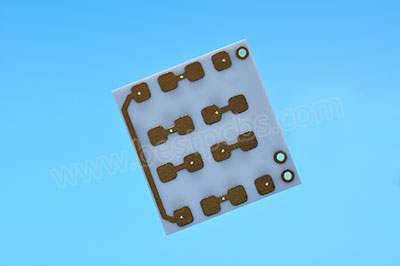
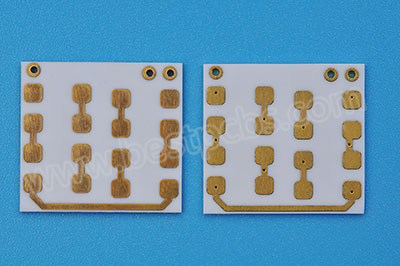
Why you need to fill the vias with copper?
1.Becuase if let the vias open, they will allow solder to flow through to opposite side of PCB during reflow, this causes bridging under components.
Filling the open vias/holes with copper can prevent from the solder pates into the vias.
2.If you need to pull vacuum around them and a hole would compromise that, so need to fill the vias.
There are also other purposes for filling the vias, if you need such ceramic board with filling the vias, please contact Coco in Best Technology sales@bestpcbs.com