In our last blog, we simply introduced ENIG surface treatment in PCB manufacturing, and this time, we will share more information about the comparison of ENIG and ENEPIG.
What is ENEPIG Surface Treatment?
ENEPIG stands for Electroless Nickel Electroless Palladium Immersion Gold. This type of metal coating on the PCB pad surface consists of three layers—nickel, palladium, and gold. Apart from protecting the copper surface from corrosion and oxidation, the ENEPIG surface treatment is also suitable for high-density SMT (Surface Mount Technology) designs.
For its manufacturing process, manufacturers begin by activating the copper surface, followed by depositing a layer of electroless nickel, then a layer of electroless palladium, and finally, a layer of immersion gold. The process is somewhat similar to the one they follow in the ENIG process, but adding a palladium layer to the ENIG technology. The palladium layer not only improves the surface protection of the PCB, but also prevents nickel from deteriorating and inhibits interactions with the gold layer.
Pros of ENEPIG Surface Treatment
- Reduce the black pad issues
- Excellent solderability and high reflow soldering performance
- Provide high-reliable wire bonding capability
- High-density design available
- Meet the miniaturization standards
- Suitable for extra thin PCBs
Cons of ENEPIG Surface Treatment
- Expensive than ENIG process
- Thicker palladium layer will decrease the effective of SMT soldering
- Longer wettability time
What are the Differences Between ENIG and ENEPIG?
The main difference between ENIG and ENEPIG is the palladium layer. This is the extra layer that added in ENEPIG process, which provides high oxidation resistance, enhance the electrical performance of the surface cleanliness and improve the abrasion resistance of the PCB surface. However, the palladium layer also increases the cost of manufacturing.
Additionally, the inconsistent surface cleanliness of ENIG, resulting from low solder joint reliability, particularly in gold wire bonding, is a concern. Extra procedures are also required to prevent nickel corrosion in ENIG. When considering it into manufacturing, the ENIG is well-suited for lower-end electronic products.
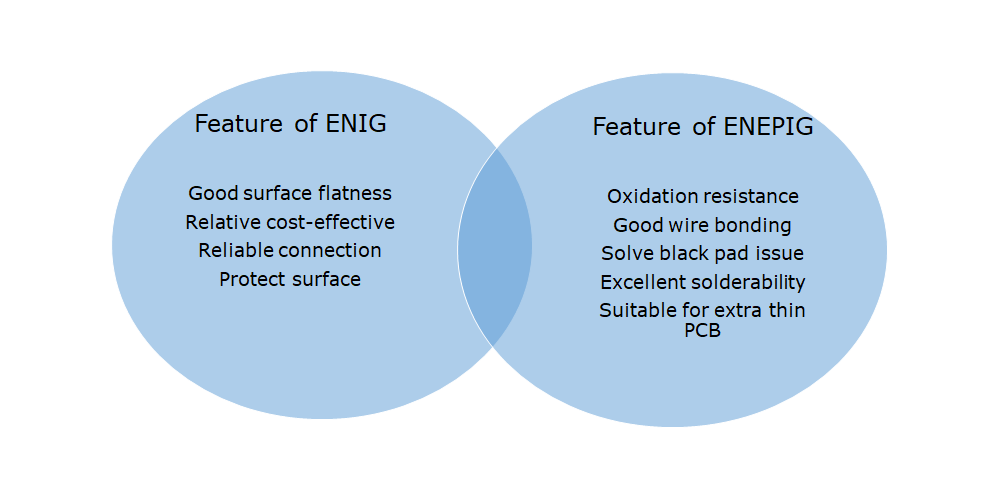
The Considerations of Selecting ENIG or ENEPIG Surface Finishing
Though both two surface treatments offer excellent electrical performance and heat dissipation properties, there are still some conditions that need to consider when choose them.
- Budget
Cost is an important factor when choose a suitable surface treatment. As we explain above, ENEPIG is expensive than ENIG, if you are trying to find a relative cost-effective coating, then ENIG is the best choice.
- End-applications
The end-applications or finished products also determined the selection of surface finishing. For example, if your PCB will be used in high temperature applications, ENIG would be the better one since it can withstand high temperature.
- Flatness
Many traditional surface finishes have poor flatness and smoothness, this brings the big challenge of small-size components mounted. Especially for those fine-pitch components like BGA, an uneven surface can result many problems. However, both ENIG and ENEPIG offer highly smooth surface finishes, forming thin and uniform layers on the solder pads.
- Bonding demand
ENEPIG provides the optimal choice for wire bonding due to its highly smooth surface finish, which enhances wire bonding capabilities.
- Environment-friendly
Some traditional surface treatments contain hazardous substances, making them non-compliant with RoHS requirements. Both ENIG and ENEPIG made by Best Technology are fully RoHS compliant and lead-free, so you are don’t worry about the environment unfriendly.
At the end, the choice between ENIG and ENEPIG surface treatments in PCB manufacturing involves a careful consideration of various factors. While both options offer excellent electrical performance, heat dissipation properties, and compliance with environmental standards like RoHS, specific project requirements and priorities will guide the decision-making process. If you are still confuse about the selection of surface treatment, welcome to contact with us, Best Team will give you a best solution that can meet your specific demands and save money for you.