In the manufacturing process of printed circuit boards, it is very necessary to apply a proper amount of flux. The soldering pads, copper bars of components and the surface of solder paste are the places where flux should be applied, which can improve the firmness of the soldering points and the quality of printed circuit boards.
What is flux?
Flux: A chemical substance that can help and promote the soldering process in the soldering process, and at the same time has a protective effect and prevents oxidation reactions. Flux can be divided into solid, liquid and gas.
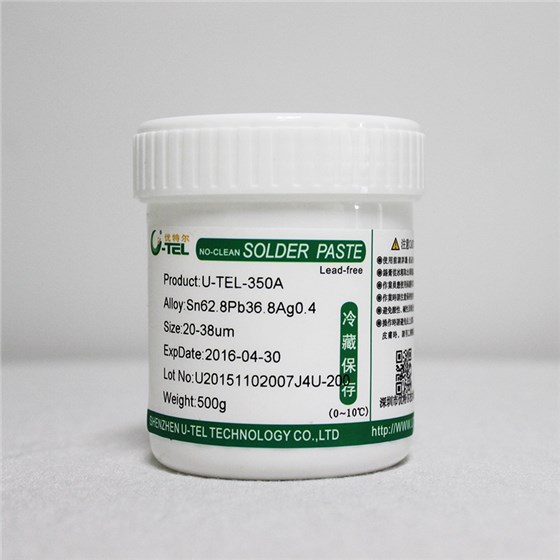
There are mainly several aspects such as “assisting heat conduction”, “removing oxides”, “reducing the surface tension of the material to be soldered”, “removing oil stains on the surface of the material to be soldered, increasing the soldering area”, and “preventing re-oxidation”. Among these aspects, the two most critical functions are: “removing oxides” and “reducing the surface tension of the material to be soldered”.
Do you apply flux before or after soldering?
Use flux before soldering printed circuit boards. ‌
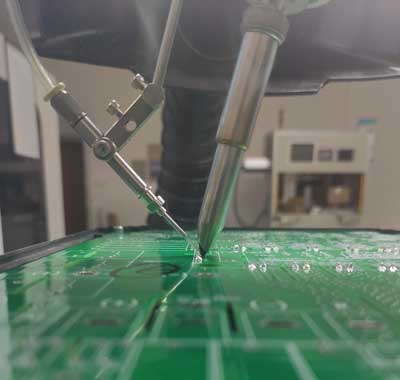
During the soldering process of printed circuit boards, the main purpose of using flux is to improve soldering performance and help the metal avoid the formation of an oxide film that hinders solder wetting when heated, thereby promoting the formation of solder-metal alloys and avoiding the occurrence of cold soldering and false soldering.
Flux can be applied to the printed circuit board before soldering, or it can be used as part of the solder during the soldering process, such as solder paste or solder oil. When tinning the pins of components, rosin should be used as the flux, and if the printed circuit board is already coated with rosin solution, then no additional flux is required during soldering.
After using flux, make sure to wipe off the residual flux at the soldering site after soldering to avoid potential damage to electronic components and circuit boards.
In addition, the preparation work before soldering includes thoroughly cleaning the copper foil surface and then applying rosin water to protect the copper foil and help soldering. This step is performed before soldering to ensure the smooth progress of the soldering process. Therefore, the correct approach is to use flux before soldering printed circuit boards to ensure the quality and reliability of soldering.
How much flux to use when soldering?
When soldering printed circuit boards, the amount of flux used needs to be determined according to the specific soldering method and the type of flux. For wave soldering flux, when using brushing and foaming methods, the specific gravity of the flux should be controlled between 0.82-0.84 (specific gravity of liquid rosin flux stock solution).
During the soldering process, the specific gravity of the flux needs to be measured regularly. If the specific gravity is found to increase, it should be adjusted to the normal range with diluent in time, but the diluent should not be added too much to avoid affecting the soldering quality.
For the quantitative spraying method, the key is that the nozzle can control the spray volume. The nozzle should be cleaned frequently to ensure that the spray hole is not blocked. The spray pressure should be controlled at 0.2-0.3Mpa, the flux pressure should be controlled at 0.4±0.05Mpa, and the spray flow rate should be controlled at 20-35ml/min.
In addition, different types of flux formulas are also different. For example, rosin liquid can be made by mixing rosin blocks and alcohol in a ratio of 1:3. For the flux of printed circuit boards, you can directly use rosin water, and apply the prepared rosin water directly on the surface of the printed circuit board or the solder joints.
When using flux, you should also pay attention to the following points:
Put the bottle cap on immediately after use to prevent the flux from being in contact with air for a long time and causing oxidation reaction or absorbing water vapor in the air to cause the concentration to decrease.
Regularly replace the flux that has been stored for too long, because long-term storage will cause the flux composition to change and the activation performance to deteriorate, affecting the welding quality.
Clean it after welding, because the insulation performance of the flux will drop sharply at high temperature, and the residue may affect the heating components, and in severe cases may cause short circuits.
In summary, the amount of flux used in printed circuit board welding needs to be determined according to the specific welding method and flux type, and pay attention to the use and storage conditions of the flux to ensure welding quality and safety.
What happens if you use too much flux when soldering?
First, the main functions of flux include assisting heat conduction, removing oxides, reducing the surface tension of the material being soldered, removing oil stains on the surface of the material being soldered, increasing the soldering area, and preventing reoxidation.
However, excessive use of flux can lead to corrosion and electromigration. This is because improper use of flux, such as excessive use, can create more favorable conditions for potential chemical corrosion reactions.
In addition, if the flux used is not well controlled, resulting in excessive use of flux, more flux residue will be left, which creates more favorable conditions for potential chemical corrosion reactions.
Therefore, it is very important to control the amount of flux used to avoid negative effects on soldering quality and reliability.
What happens if I don’t use flux?
If flux is not used on printed circuit boards, it may lead to reduced soldering quality, increased soldering difficulty, and affect the performance and reliability of the circuit.
1. Increased soldering difficulty: Without flux, the solder may be difficult to flow to the soldering point, resulting in loose soldering, prone to cold soldering or poor soldering.
2. Reduce welding quality: Without the help of flux, the soldering point may not be smooth enough, with burrs or unevenness, which may affect the normal operation of the circuit.
3. Affect circuit performance and reliability: Flux can reduce the resistance of the soldering point and improve the conductivity of the circuit. Without flux, the resistance of the soldering point may increase, affecting the performance and stability of the circuit.
In addition, the flux can also prevent oxidation to a certain extent, protect the soldering point from the influence of the external environment, thereby improving the life of the circuit. Therefore, in the soldering process of printed circuit boards, it is very important to use the soldering flux correctly.
What is an alternative to soldering flux?
Alternatives to printed circuit board soldering flux include no-clean soldering flux, special solder resist for printed circuit boards, water-based cleaning agents and dry ice cleaning technology. ‌
1. No-clean soldering flux is a new type of soldering flux that does not contain halide activators. It does not need to be cleaned after use, which can save investment in cleaning equipment and cleaning solvents, while reducing the emission of waste gas and wastewater, and the pollution to the environment is also reduced accordingly.
2. The main function of the ‌PCB solder mask‌ is to prevent “wiring” and short circuits during wave soldering and protect the PCB permanently. In addition, it can save solder, reduce the weight of the PCB, and reduce costs.
3. As a new type of cleaning medium, the ‌water-based cleaning agent‌ achieves cleaning through the wetting, dissolution, emulsification, saponification, chelation and other effects of the surfactants, emulsifiers, penetrants, etc.
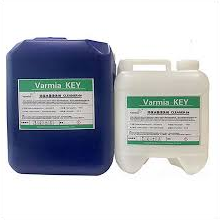
4. The ‌dry ice cleaning technology‌ uses extremely low-temperature dry ice particles to spray onto the treated object under the action of compressed air, so that the dirt is rapidly frozen to brittleness and burst, and then vaporized to take away the dirt.
These substitutes have their own characteristics and are suitable for different application scenarios and technical requirements. When choosing, specific process requirements and cost-effectiveness must be considered.
What does rosin do when soldering?
In the process of printed circuit board soldering, rosin plays a vital role. It is mainly used as a flux to help the soldering process be smoother and more efficient. The role of rosin is reflected in the following aspects:
‌Removing oxide film‌: Rosin can remove the oxide film formed on the copper surface due to contact with air. These oxide films will prevent the tin from wetting the copper wire, thus affecting the quality of welding.
‌Preventing re-oxidation‌: Rosin can not only remove the oxide film, but also prevent the soldering surface from re-oxidizing during the welding process, which helps to maintain the stability and reliability of the welding point.
‌Isolating air‌: Under high temperature conditions of welding, rosin can isolate the air and prevent oxidation of the metal surface.
In summary, rosin plays an important role in the soldering process of printed circuit boards. Through its fluxing effect, it improves the quality and reliability of soldering and is one of the indispensable materials in electronic manufacturing‌.
Conclusion:
Flux is a key part of the soldering process. Without it, your solder will not flow smoothly through the joint and the solder will not adhere properly to the various components on the circuit board. High-quality flux is necessary to produce good solder joints.
BEST Technology is a professional PCB circuit board manufacturer with many years of experience in PCB circuit board welding. The circuit boards it produces are of extremely high quality. We have the most extensive experience to deal with all aspects of PCB welding issues.