Are you finding LED Metal Core PCB solutions? Let’s explore more about LED Metal Core PCB’s benefits, application, thermal Management, 94V0 compliance. and how to find a reliable LED metal core PCB manufacturer as well as cost factors.
Best Technology as a wholesale LED metal core PCB producer with ISO 9001 and UL certifications, ensuring rigorous quality control. The company delivers rapid prototyping with 48-hour lead times for urgent projects, supported by end-to-end services spanning design, prototyping, mass production, and assembly. A stable electronics supply chain guarantees access to multiple material options for diverse applications. Automated production lines and strict thermal cycling, AOI/X-ray inspection maintain consistency in large orders. Engineers optimize heat dissipation layouts (copper thickness up to 6 oz) to extend LED lifespan and reduce cost. Contact us today sales@bestpcbs.com if you have any request for LED metal core PCB.
What Is LED Metal Core PCB?
A LED metal core PCB is specialized circuit boards constructed with a metal substrate—typically aluminum or copper—as their base layer. This design replaces traditional FR4 fiberglass materials to address thermal challenges in high-power LED applications. The structure comprises three primary layers: a metal base for heat dissipation, a thin dielectric layer to insulate electrical components, and a copper circuitry layer for electrical connections.
Their primary function is to efficiently manage heat generated by LEDs, particularly in dense arrays or high-wattage designs. The metal core conducts heat away from the LED junctions, preventing overheating that could degrade performance or shorten lifespan. This thermal management capability makes them ideal for automotive lighting, industrial fixtures, and high-brightness displays where reliability under thermal stress is critical. The rigid metal structure also provides mechanical stability, reducing warping risks compared to polymer-based boards.
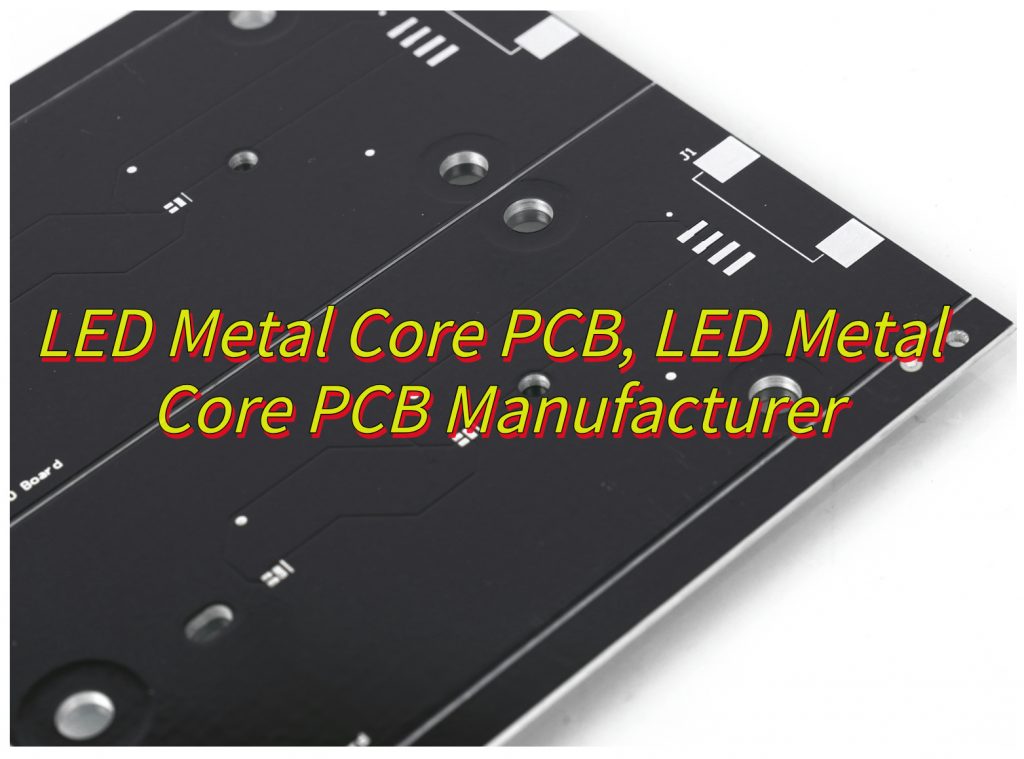
What Are Advantages of LED Metal Core PCB?
Advantages of LED metal core PCB:
- Enhanced Thermal Management: Metal cores (aluminum/copper) dissipate heat 2-3x faster than FR4, preventing LED junction overheating.
- High-Power Compatibility: Supports dense LED arrays and drivers without performance degradation.
- Improved Reliability: Reduced thermal stress minimizes solder joint fatigue and component failure risks.
- Compact Design Potential: Thinner substrates enable sleeker product profiles for modern lighting fixtures.
- Consistent Performance: Maintains efficiency across wide temperature fluctuations (-40°C to 150°C).
- Cost-Effective Durability: Long lifespan reduces replacement cycles and maintenance costs.
- Eco-Friendly Options: Recyclable metal substrates align with sustainability trends.
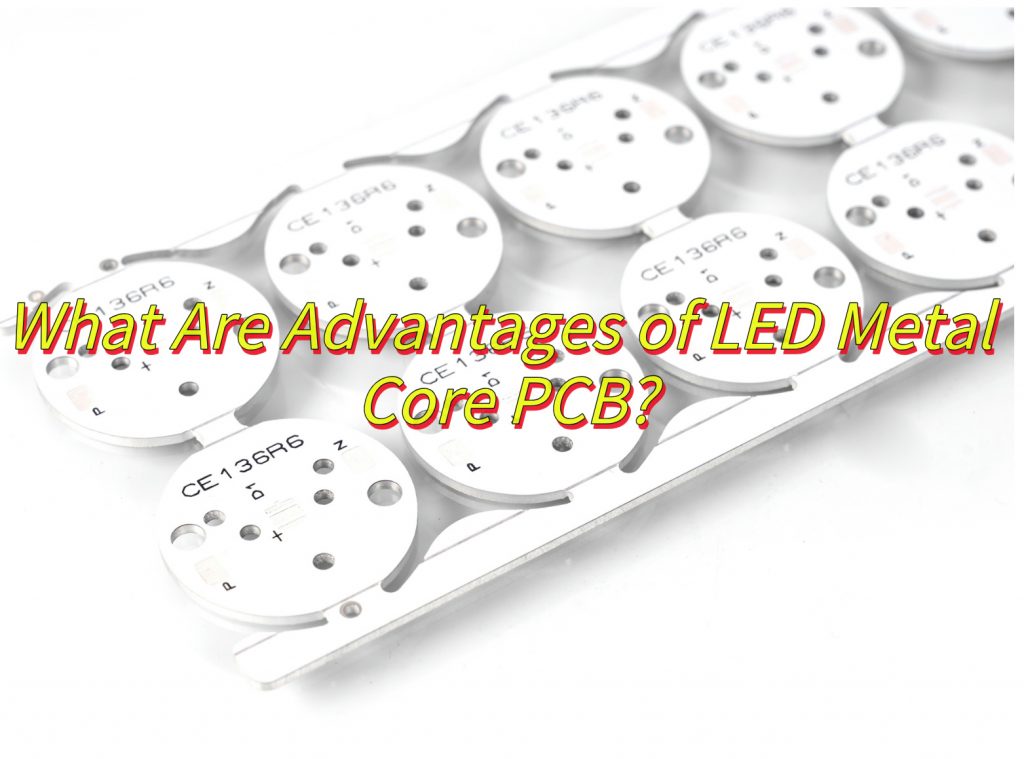
What Are Application of LED Metal Core PCB Board?
Application of LED metal core PCB board:
- Automotive Lighting: Headlamps, fog lights, and interior lighting systems benefit from superior heat dissipation.
- Industrial Fixtures: High-bay lights, streetlights, and machinery lighting require robust thermal management.
- Commercial Displays: LED video walls and digital signage use metal cores for uniform brightness control.
- Medical Equipment: Surgical lights and imaging devices demand reliable performance under prolonged use.
- Outdoor Applications: Floodlights, architectural lighting, and traffic signals thrive in harsh weather conditions.
- Consumer Electronics: Premium TVs, gaming monitors, and projectors utilize compact metal core designs.
- Aerospace Components: Specialized lighting systems in aircraft cabins and control panels prioritize durability.
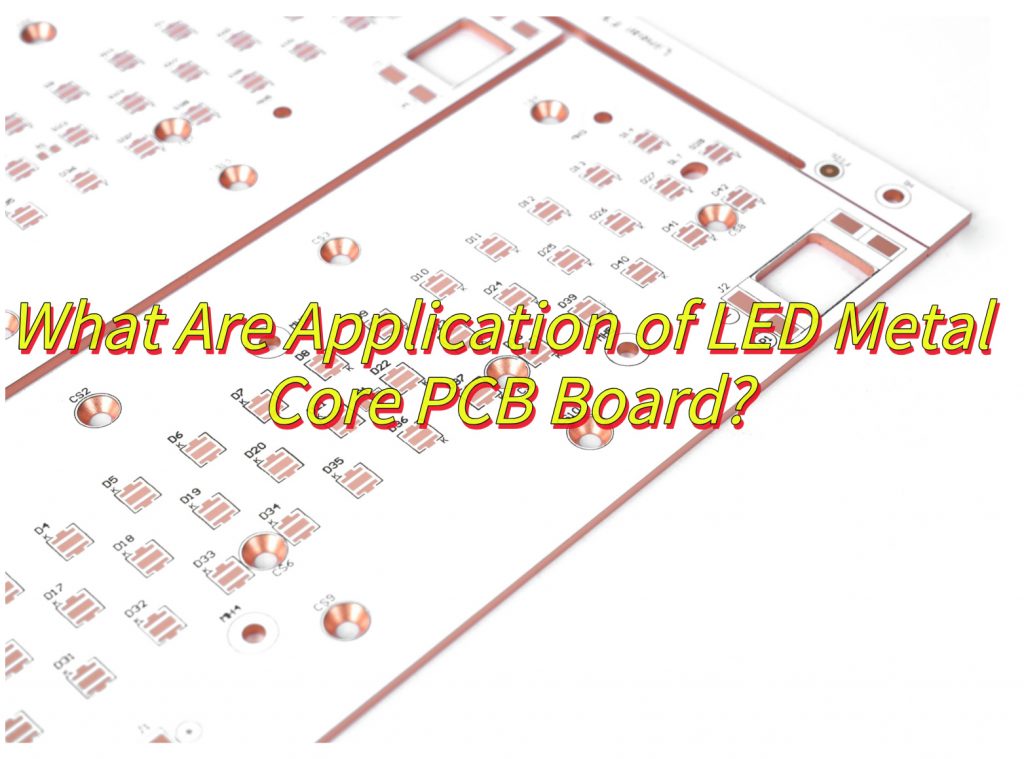
What Makes Metal Core PCBs Better for Heat Dissipation?
- Superior Thermal Conductivity: Aluminum (200 W/m·K) and copper (400 W/m·K) cores transfer heat 2-3x faster than FR4 (0.3 W/m·K), rapidly moving heat away from LEDs.
- Uniform Heat Spreading: Metal substrates distribute thermal energy evenly, preventing localized hotspots that degrade performance.
- Reduced Thermal Resistance: Direct bonding of dielectrics to metal minimizes interfacial resistance, enhancing heat transfer efficiency.
- Mechanical Rigidity: Non-flexible structure maintains consistent contact with heatsinks, ensuring optimal thermal interface.
- High-Temperature Stability: Metal cores maintain dimensional integrity at elevated temperatures, preventing delamination common in polymer boards.
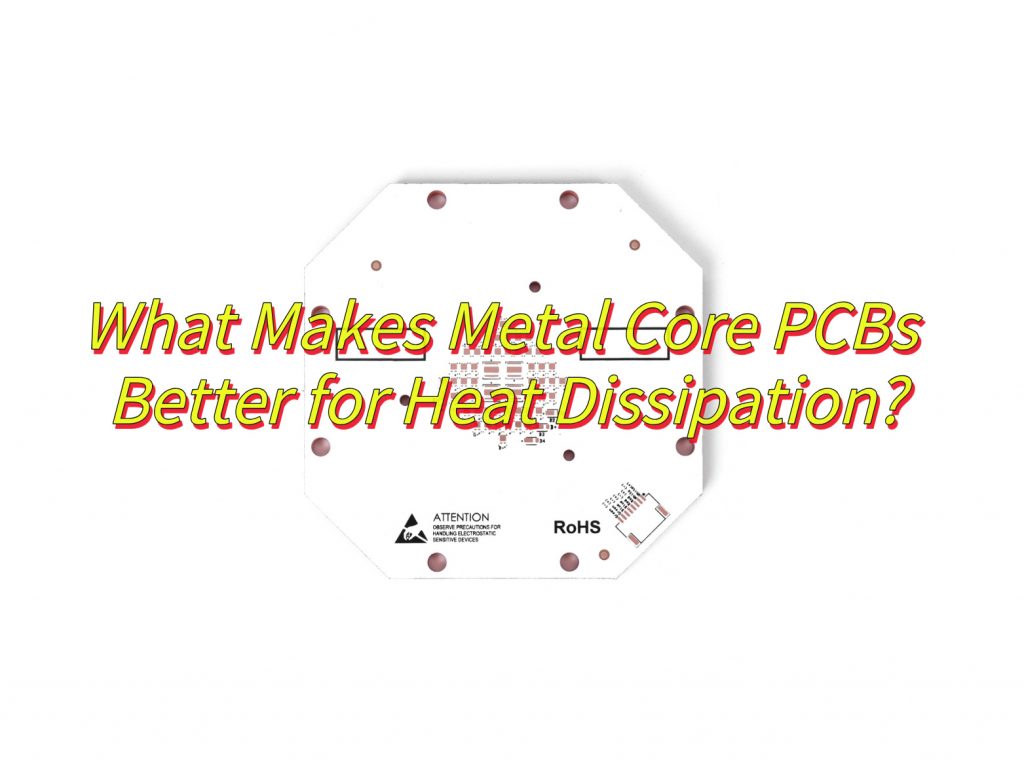
How to Identify A Reliable Metal Core LED PCB Manufacturer?
Here are some methods about how to identify a reliable metal core LED PCB manufacturer:
- Verify Industry Certifications: Prioritize manufacturers with ISO 9001, UL, or IPC standards compliance to ensure consistent quality.
- Evaluate Manufacturing Expertise: Choose suppliers specializing in wholesale led metal core PCB production, with proven track records in thermal design.
- Assess Material Sourcing: Confirm use of high-grade aluminum/copper alloys and reliable dielectric materials for longevity.
- Check Production Capacity: Ensure they handle large-volume orders efficiently without compromising lead times, with clear communication on delivery schedules.
- Review Testing Protocols: Reliable manufacturers conduct thermal cycling, solderability, and vibration tests specific to LED metal core PCB durability.
- Analyze Customer Feedback: Look for positive reviews regarding post-sale support and warranty claims resolution related to thermal performance.
- Compare Cost Structures: Transparent pricing for wholesale led metal core PCB orders indicates ethical business practices.
- Assess Thermal Design Capabilities: Ensure expertise in optimizing metal core layouts for LED heat dissipation, including via placement and copper thickness.
- Evaluate Customization Options: Manufacturers offering tailored solutions for unique LED configurations demonstrate deeper technical understanding.
- Check for Innovations: Look for patented technologies or proprietary processes that enhance metal core PCB efficiency or lifespan.
Can Manufacturers Customize Metal Core PCBs for Specific LED Designs?
Yes, specialized metal core LED PCB manufacturers like Best Technology adapt metal core PCBs to meet exact LED application needs. Here’s how:
- Adjustable core materials and thicknesses (1.0–3.0mm aluminum/copper) to balance heat dissipation and mechanical stability for high-power LED arrays.
- Flexible order volumes, with tiered pricing for prototypes (1,000+ units) and bulk orders (10,000+ units), ensuring cost-efficiency across project scales.
- Compatibility with harsh environments, using materials like anodized aluminum or advanced dielectric layers to withstand moisture, vibration, or extreme temperatures in industrial LED systems.
- Integrated thermal management, incorporating optimized via patterns and copper layer designs to reduce hotspots in dense LED configurations.
- End-to-end production support, from PCB fabrication to assembly, streamlining workflows for automotive or UV-C LED applications.
What Factors Affect the Cost of Metal Core PCB LED Solutions?
Below are the primary factors influencing the cost of metal core PCB LED solutions:
- Material Selection
Metal core type: Aluminum (lower cost) vs. copper (higher thermal performance) directly impacts material expenses.
Dielectric layer quality: High thermal conductivity insulation materials (1.5–8.0 W/m·K) increase costs but improve heat dissipation for high-power LEDs. - Manufacturing Processes
Precision requirements: Tight tolerances for thermal via drilling or laser-cut patterns raise labor and equipment costs.
Surface finishes: Immersion silver or ENIG coatings add 10–15% to base costs but enhance solderability and corrosion resistance. - Order Volume
Prototyping (1–100 units) incurs higher per-unit costs due to setup fees, while bulk orders (5,000+ units) reduce prices by 20–30% through economies of scale. - Testing & Certification
Compliance with IPC-6012D or UL certification requires additional inspections, increasing production time and costs.
Thermal cycling tests to validate LED lifespan under stress add 5–10% to total project expenses. - Environmental Resistance Needs
Solutions for harsh conditions (e.g., moisture, extreme temperatures) demand anodized cores or specialized conformal coatings, raising material costs by 15–25%. - Supply Chain Efficiency
Partnering with vertically integrated manufacturers reduces logistics delays and material waste, cutting overall costs by 8–12%.
Can 94v0 standard Be Achieve in LED Metal Core PCB Bulk production?
Yes, achieving the 94V0 standard in LED metal core PCB bulk production is achievable with strict material specifications and automated quality checks. Manufacturers like Best Technology maintain consistency by using flame-retardant dielectric materials (e.g., FR-4 or CEM-3) bonded to aluminum substrates, which pass UL 94V0 vertical flame tests. Automated optical inspection (AOI) and real-time thermal profiling during lamination ensure uniform dielectric thickness and adhesion. For bulk orders, statistical process control (SPC) monitors critical parameters like layer alignment and thermal conductivity, while random flame testing on 3-5% of units per batch verifies compliance. High-volume production (5,000+ panels) reduces costs by 25-40% via optimized panel layout and reduced setup waste, ensuring 94V0 consistency across automotive, industrial, and high-power LED systems.