Ceramic substrate technology plays an important role in modern electronic device manufacturing. Low temperature co-fired ceramics (LTCC) and high temperature co-fired ceramics (HTCC) are two major ceramic substrate technologies, each of which has unique process characteristics and application advantages. This paper provides a comprehensive comparison of LTCC and HTCC technologies, discussing their process characteristics, material properties, performance advantages, and application areas to help engineers and researchers choose the most suitable ceramic substrate technology for their designs and applications.
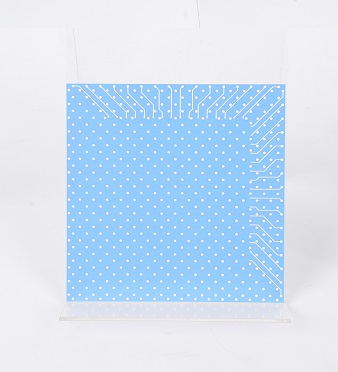
1. Introduction
With the continuous progress of electronic technology, the performance and reliability of electronic components have been put forward higher requirements. Ceramic substrate technology, as one of the key materials for integrated circuits (ICs) and microwave assemblies, provides excellent electrical properties and mechanical strength. Low temperature co-fired ceramics (LTCC) and high temperature co-fired ceramics (HTCC) technologies are the two main ceramic substrate technologies, and this paper will provide an in-depth comparison of these two technologies to clarify their advantages and disadvantages as well as the applicable scenarios.
2. LTCC Technology Overview
2.1 Process
LTCC technology uses low-temperature co-fired ceramic materials, which are typically sintered at temperatures ranging from 850°C to 900°C. The process includes material preparation, printed circuitry, and a high level of sintering. The process consists of material preparation, printed circuits, lamination and co-firing. LTCC materials are usually composed of a mixture of glass and ceramic powders, which melt and fuse well at low temperatures.
2.2 Material Characterization
Low temperature co-fired ceramics (LTCC) materials have a low dielectric constant and low dielectric loss, making them suitable for high frequency applications. The conductive layer can be fabricated by screen printing technology and can support multi-layer integration, which makes LTCC perform well in space-constrained applications.
2.3 Advantages and Disadvantages Analysis
Advantages:
Multi-layer integration capability: Low temperature co-fired ceramics (LTCC) supports complex multi-layer structures, making it suitable for highly integrated circuit designs.
Cost Effectiveness: Lower sintering temperatures reduce production costs.
High-frequency performance: Excellent high-frequency characteristics for wireless communications and microwave applications.
Disadvantages:
Weak High Temperature Resistance: Not suitable for applications in high temperature environments.
Limited material selection: Compared to HTCC, LTCC has a smaller variety of materials, limiting the design for certain applications.
3. HTCC Technology Overview
3.1 Process
High temperature co-fired ceramics (HTCC) uses high-temperature co-fired ceramic materials, which are typically sintered at temperatures between 1500°C and 1600°C. HTCC materials mainly include alumina (Al₂O₃), which is capable of achieving high densities and excellent mechanical properties at high temperatures. The HTCC process involves powder preparation, molding, and sintering steps.
3.2 Material Characterization
High temperature co-fired ceramics (HTCC) materials have very high temperature resistance and chemical stability. The high temperature sintering process gives these materials excellent mechanical strength and wear resistance, making them suitable for use at high temperatures and in harsh environments. Their electrical properties are stable and suitable for high power and high frequency applications.
3.3 Analysis of Advantages and Disadvantages
Advantages:
High temperature resistance: able to withstand extremely high operating temperatures, suitable for high-temperature environments.
High mechanical strength: high strength and wear resistance, making it suitable for harsh application conditions.
Wide range of materials: support a variety of high-temperature ceramic materials to meet different application requirements.
Disadvantages:
High cost: High temperature sintering equipment and process requirements result in high production costs.
Process complexity: the need for high-temperature sintering equipment, the process is more complex.
4. Comparative analysis of LTCC and HTCC
4.1 process complexity
Low temperature co-fired ceramics (LTCC) process is relatively simple, low-temperature sintering reduces the cost of equipment and process difficulties, while HTCC requires the use of high-temperature sintering equipment, process complexity and high cost.
4.2 Material Performance
Low temperature co-fired ceramics (LTCC) materials are suitable for high-frequency and multi-layer integration applications and offer low dielectric loss, while HTCC materials offer higher mechanical strength and temperature resistance for high-temperature and high-power applications.
4.3 Comparison of Application Scenarios
LTCC (Low Temperature Co-fired Ceramics) Application Areas
1. Wireless communications:
Reason: LTCC technology has excellent high-frequency performance and low dielectric loss, which makes it suitable for radio frequency circuit (RF circuit) and microwave applications in wireless communication equipment. Its multi-layer integration capability allows the realization of complex RF circuits on a small substrate to meet the demand for high frequency and miniaturization of modern communication systems.
Application examples: mobile communication base stations, satellite communication systems, wireless sensor networks.
2. Automotive electronics:
Reason: In automotive electronic systems, LTCC can provide stable electrical performance and reliable multi-layer integration, which is suitable for in-vehicle communication modules and sensors that require high-frequency characteristics.
Application examples: automotive radar systems, in-vehicle wireless communications, automotive sensors and control units.
3. Medical devices:
Reason: LTCC technology enables highly integrated and miniaturized designs with good high-frequency performance, making it suitable for electronic components in medical instruments.
Application examples: Medical monitoring devices, medical imaging systems, implantable medical devices.
4. Consumer electronics:
Reason: LTCC’s low cost and high integration capability make it suitable for mass-produced consumer electronics such as smartphones and portable electronic devices.
Application examples: Smartphones, tablets, Bluetooth devices.
HTCC (High Temperature Co-fired Ceramics) Application Areas
1. Aerospace:
Reason: HTCC technology can withstand extremely high temperatures and harsh environmental conditions, making it ideal for high-temperature components and electronics in spacecraft and aircraft.
Application examples: High temperature sensors in spacecraft, electronic control systems in airplanes, rocket engine components.
2. Military equipment:
Reason: Military applications require high-strength, high-temperature-stable materials. HTCC’s excellent mechanical strength and high-temperature resistance make it suitable for use in key components in military equipment.
Application examples: missile systems, military communications equipment, radar systems.
3. High power electronic equipment:
Reason: HTCC is able to maintain stable performance in high power and high temperature environments, making it suitable for electronic components with high power density and high temperature operation.
Examples of applications: high power supply modules, high power amplifiers, lasers.
4. Sensors and devices for extreme environments:
Reason: HTCC materials’ excellent resistance to high temperatures and chemical stability make them suitable for sensors and other electronic devices in extreme environments.
Application examples: deep-sea exploration equipment, geological exploration instruments, sensors in extreme climatic conditions.
5. Conclusion
Low temperature co-fired ceramics (LTCC) and High temperature co-fired ceramics (HTCC) technologies have their own advantages and disadvantages, and the selection of the right technology depends on the specific application requirements. Low temperature co-fired ceramics (LTCC) is suitable for multilayer integrated circuits that require high-frequency characteristics and low cost, while High temperature co-fired ceramics (HTCC) is suitable for applications in high-temperature and high-power environments. Understanding the characteristics of both technologies can help engineers and designers make better choices in their projects, optimizing performance and cost effectiveness.