Military PCB manufacturer is not just a titleāit means strict precision, long-term durability, and reliable performance in harsh environments. These PCBs are used in mission-critical systems like radar, communication, and missile control. Thatās why manufacturers must meet tight regulations and deliver consistent quality. In this blog, weāll explore industry standards, manufacturing insights, top companies, and how Best Technology stands out as a top-tier choice.
As an R&D-driven military PCB manufacturer, Best Technology has sophisticated technology in military PCB fabrication and assembly. We guarantee creative innovation, high-quality military PCB production, quick-turn services, and prompt consultancy service to customers. As one of the major PCB manufacturers, whether you require military PCB design guidance, military PCB prototype development, or full-scale military PCB assembly solutions, Best Technology is available to address your needs.ā Just donāt hesitate to reach out to us at sales@bestpcbs.com.
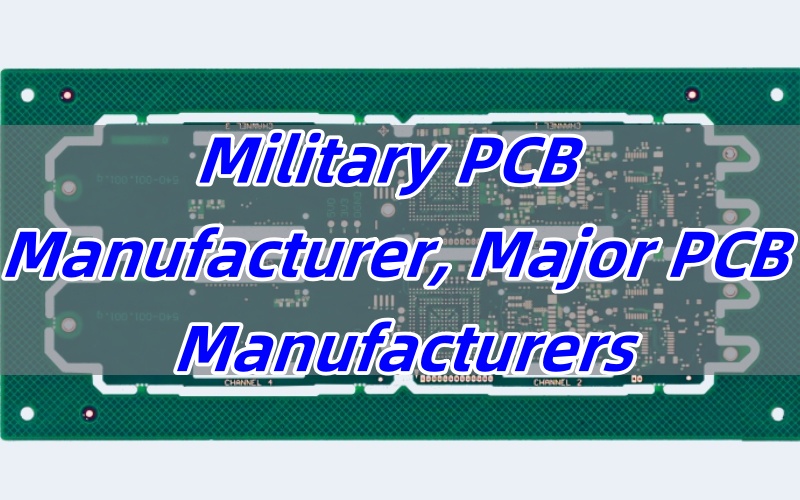
What is the best military PCB manufacturer?
Choosing the best military PCB manufacturer depends on capability, quality control, turnaround, and certification. Itās not about flashy ads; it’s about trust, experience, and proven performance in the field.
Top-tier manufacturers like Best Technology, TTM Technologies, and Sanmina meet or exceed IPC Class 3 or MIL-PRF-31032. These standards ensure military-grade quality.
The best military PCB provider offers:
- Full compliance with MIL standards
- In-house testing and inspection
- PCB fabrication and assembly under one roof
- Strong record of delivering high-complexity boards on time
So, how do you recognize the right one? Look for certifications, years of experience, and defense contracts. The real best are often the quiet giants doing mission-critical work in the background.
What is the military standard for PCB?
The military doesn’t guess. It follows strict documentation and quality validation.
The most recognized military PCB standard is MIL-PRF-31032. It outlines performance specifications for rigid and flexible PCBs. It requires:
- Traceability from raw material to final product
- Quality systems with tight controls
- Performance testing under environmental stress
Another common standard is IPC Class 3, which focuses on high-performance electronic products. Itās widely used in defense, aerospace, and medical fields.
In short, military PCBs go through more checks, tighter tolerances, and stricter documentation than regular commercial boards.
What is the standard PCB drill tolerance?
Even the tiniest mistake in drill size can lead to circuit failureāespecially in defense systems. So, military boards demand high-precision drilling. Typical drill hole tolerance in military PCBs:
- Mechanical drillingā: ±0.004″ (±0.1mm)
- Laser drillingā: ±0.002″ (±0.05mm) or tighter
- Controlled aspect ratios (e.g., ā¤10:1)
- Debris-free holes with smooth walls
- Post-drill inspection mandatory for critical layers
- Laser/CNC processes and rigorous QA ensure reliability in harsh environments.
Hole accuracy impacts plating, component fitting, and signal integrity. Thatās why military PCB manufacturers use laser drilling or high-speed CNCs with inspection after every pass. In short, tighter tolerance equals better reliability in tough environments.
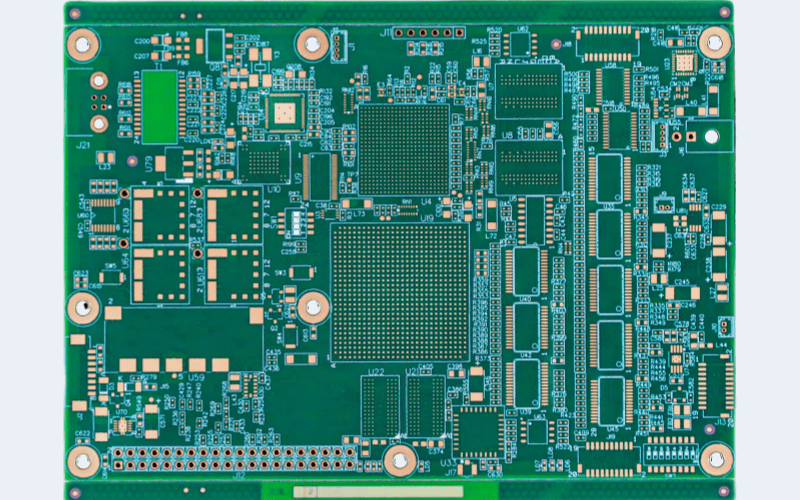
How is a PCB manufactured?
Understanding how a military PCB manufacturer works gives insight into the process behind the reliability. Hereās a simplified 4-layer PCB manufacturing process in Best Technology:
- Design Verification: Engineers cross-check against military requirements.
- Material Selection: High-temp FR4, Rogers, or polyimide is often used.
- Cutting: We begin by cutting raw copper-clad laminate into production-sized panels. This gets the board ready for inner layer circuit work.
- Inner Layer Circuit: The design is transferred to the inner layers using photoresist. Exposure, development, and etching remove unwanted copper, leaving behind precise circuit paths.
- Inner Layer AOI: AOI checks the etched layers for errors like open or short circuits. This prevents early-stage defects from moving forward.
- Lamination: We stack and press the inner layers with prepreg and outer copper sheets under high heat and pressure. This bonds everything into one solid, multilayer board.
- Drilling: CNC drills make holes for layer-to-layer connections. Accuracy is key here, especially for dense or complex layouts.
- Copper Plating: We deposit a thin copper layer inside the holes through chemical plating, then build it up with electroplating. This step creates reliable vias.
- Outer Layer Circuit: Like the inner layers, the outer copper is patterned with photoresist and etched to form surface traces.
- Outer Layer AOI: A second AOI confirms that the outer layers are defect-free before moving to protective coatings.
- Solder Mask: A green (or other color) solder mask is applied and developed. This layer protects the copper from oxidation and short circuits.
- Silkscreen: We print part numbers, logos, and markings on the board to help with assembly and inspection.
- Baking: The board is baked to harden the solder mask and silkscreen layers, improving durability.
- Surface Finish: We add a protective surface finish like ENIG or HASL to keep pads solderable and safe from corrosion.
- Profiling: The PCB is routed or punched into its final shape. Edge features and cutouts are also added here.
- Testing: Each board is electrically tested to catch any shorts or open connections. This step guarantees function.
- Final Quality Control (FQC): Our team does a final inspection to ensure each board meets IPC standards and customer expectations.
- Packing: Boards are vacuum packed with desiccant to protect against moisture during shipping.
- Warehousing: After all checks, boards go into storage and are prepped for delivery based on customer timelines.
Manufacturing is more controlled than commercial PCBs. Every step is validated to avoid defects in the field. As one of the major PCB manufacturers, Best Technology promotes a customer-first spirit. We have served 1700 customers across 40 countries in terms of military-grade PCB manufacturing, which is a proven track record. If you have any questions or doubts about the above FR4 4 Layer PCB manufacturing process, just contact us at any time. Professional talents are replying to you within 24 hours.
Who manufactures PCBs?
Thereās a long printed circuit board manufacturers list, but only a few specialize in military-grade. When it comes to military PCB manufacturers, precision, traceability, and reliability aren’t optional ā theyāre requirements. Several companies in China have built strong reputations in this field by following military standards like IPC-6012DS or MIL-PRF-31032, along with offering high-end fabrication services. Here are a few trusted names in the industry:
1. Best Technology
- Headquartered in Shenzhen, Best Technology has more than 18 years of experience in high-reliability PCB fabrication, especially for military, aerospace, and medical applications. We offer rigid, flex, and metal-based PCBs with full traceability, IPC Class 3 compliance. Our military projects are backed by strict quality control and quick-response engineering support.
2. Victory Giant Technology
- Also known as Shennan Circuitsā sibling company, Victory Giant is one of the largest domestic PCB manufacturers in China. Their core strengths lie in HDI, high-frequency, and multilayer PCBs used in radar systems, secure communications, and defense-grade electronics. The company is AS9100 certified and supports both mass production and prototyping of military boards.
3. Unitech Printed Circuit Board Corp.
- Based in Taiwan, Unitech PCB is a global leader known for its premium quality multilayer and HDI PCBs. They support various defense contractors and are trusted for their high-end production capabilities, including flex-rigid boards, blind/buried via structures, and halogen-free materials. Their facilities are ISO and UL certified, making them a go-to partner for military electronics manufacturers worldwide.
4. TTM Technologies
- TTM operates globally but maintains advanced facilities in both China and Taiwan. They offer full-stack solutions from design to assembly, with a strong emphasis on military and aerospace electronics. Their certifications include MIL-PRF-31032, AS9100, and NADCAP, aligning with the highest defense standards. TTM is also deeply invested in R&D for next-gen radar and satellite platforms.
These manufacturers not only deliver performance and reliability but also understand the secure handling of sensitive projects, which is critical for any military PCB project. Whether you need a small batch for R&D or full-scale production, these companies offer scalable solutions backed by years of industry trust.
Who is the largest military PCB manufacturer in USA?
The largest military PCB manufacturer in the USA isnāt just about sizeāitās about defense capability, certifications, and government contracts. Here are a few names consistently leading the industry:
- TTM Technologies: Headquartered in California. Offers a wide range of defense and aerospace PCBs. Works with top-tier defense contractors.
- Sanmina Corporation: Based in San Jose. They handle high-complexity boards and assemblies for government and aerospace.
- Benchmark Electronics: Known for system integration and board manufacturing. ITAR-registered and ISO-certified.
These firms invest heavily in R&D, inspection, and automation. Their facilities are often audited by government bodies for compliance.
Military PCB Manufacturer California
California is a tech powerhouse. Itās also a key state for military and aerospace contractors. Thatās why many military PCB manufacturers set up shop here. Here are the respected names:
TTM Technologies (Santa Ana, CA)
- Offers high-reliability PCBs for aerospace and defense. MIL-PRF-31032 certified. Strong R&D team and domestic production.
Sanmina (San Jose, CA)
- Delivers full turnkey solutions. Handles everything from layout to final assembly. Trusted by defense primes.
California remains a prime location for military PCB manufacturer options. With defense innovation growing, expect even more manufacturing expansion in the state.
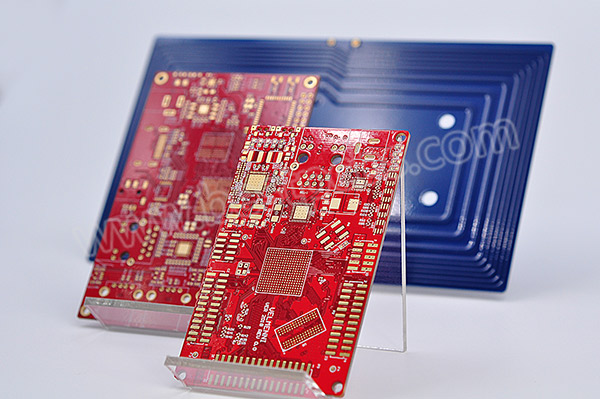
Why should you choose Best Technology as your military PCB manufacturer?
āAs a military-grade PCB manufacturer, Best Technology positions its market presence on delivering multifaceted, high-quality military-grade PCBs combined with quick-turn service solutions. Hereās why Best Technology stands out:
Proven Defense Experience
- Over 18 years in PCB manufacturing. Our boards are used in radar, drones, and communication systems.
Complete In-House Service
- From layout, fab, to assemblyāwe do everything ourselves. That means better control and faster delivery. Not all PCB manufacturing companies are equal. Many outsource layers of their work, leading to loss of control. If you want reliability, choose Best Technology that does all steps with our own equipment, in our own facility.
Certified and Compliant
- We meet MIL-PRF-31032, IPC Class 3, AS9100D, ISO 13485, ISO9001, IATF16949. All materials using in military PCB manufacturing and military PCB assembly are environment friendly and traceable in our MES and ERP system. We provide the UL, REACH, RoHS compliance declaration if you needed.
Materials That Withstand Anything
- We work with high-temp laminates, RF materials, and thermal management systems. All are tested for rugged use.
Strong After-Sales Support
- We donāt disappear after delivery. We support you with engineering, testing, and troubleshooting.
Custom Solutions
- Need a flex PCB or a low-volume prototype? We offer custom runs tailored to defense schedules. Best Technology offers full custom design, including layout, materials, and assembly.
In short, Best Technology doesnāt just sell PCBsāwe deliver trust, reliability, and peace of mind. Maintaining the consistency of high-quality military PCB to our customers is the ground rule in Best Technology.
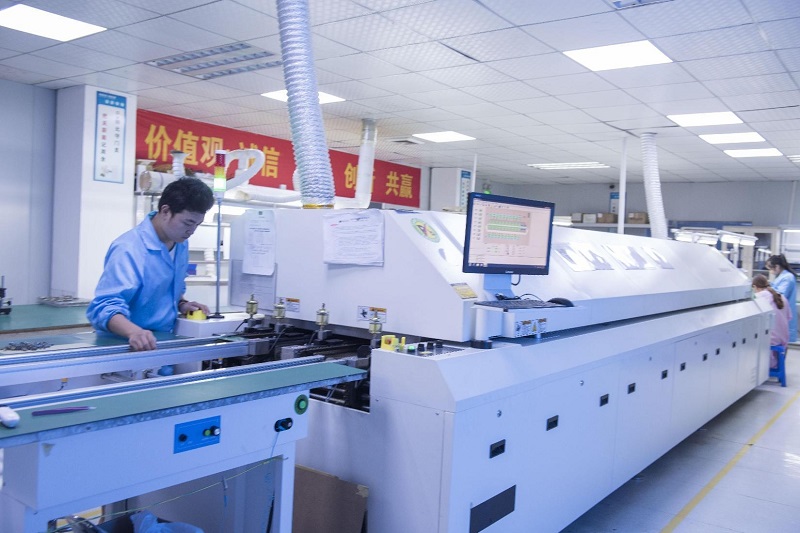
To put it simply, choosing the right military PCB manufacturer isnāt about a logo or brochure. Itās about experience, reliability, and compliance. Whether youāre looking for a flex PCB manufacturer or a partner for a full defense project, working with a trusted name ensures mission success. Companies like Best Technology offer more than PCBsāwe offer confidence in every circuit. Backed by strict standards and decades of experience, weāre ready to support your next military-grade project. Just contact us at sales@bestpcbs.com for your specific requirements.