- Pretreatment-the 1st production process of mcpcb multilayer
Confirm the processing method of the hole: Drilling and punching are used to process the holes of mcpcb multilayer. The feed degree and rotating speed of drilling is different from FR-4 PCB material. Adjustment needs to be made according to base material. Generally, we set the feed degree at 1-1.5 mil/rev, and the rotating speed at 20000-60000RPM. Punching requires specialized tooling to meet the needs of metal punching.
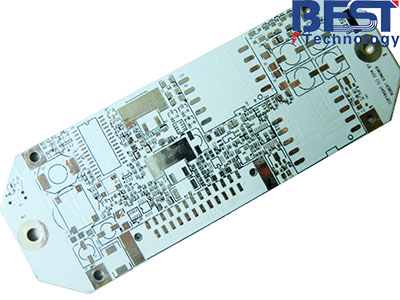
- Outer Layer Drilling-the 2nd production process of mcpcb multilayer
Drilling of the inner layer core board should be carried out, according to the drilling parameters of FR-4 PCB. There should be enough vacuum degree and pressure foot, for keeping holes clean and removing debris. The number of drilling holes and wear condition should be well controlled.
- Making Inner Layers-the 3rd production process of mcpcb multilayer
During the process, we use dry film(1.3-2.5 mil water solubility light induced corrosion resistant dry film), and wet film(wet film light induced corrosion resistant solvent).
- Circuits Electro-Plating/Etching-the 4th production process of mcpcb multilayer
Circuits Electro-Plating: Acid copper plating and tin plating are suitable for double-sided core board.
Etching: During etching process, we need to adjust speed according to the thickness of copper foil. In order that core board can be etched smoothly, we can reduce pressure of etching spraying, or make towing plate.
- Lamination-the 5th production process of mcpcb multilayer
Then complete mechanical and electrical performance of mcpcb multilayer can be established.
- Drilling/Punching and 2nd Drilling-the 6th production process of mcpcb multilayer
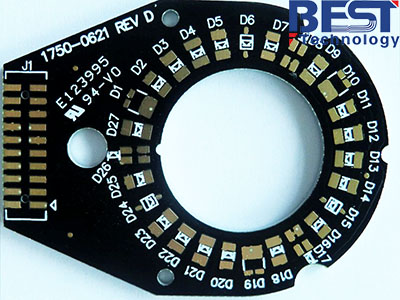
After lamination, when epoxy resin is completely cured, and epoxy resin of board is removed, 2nd drilling should be carried out. This operation involves mechanical processing of metal-base composite material. This is a challenge to structure of mcpcb multillayer. Special attention should be paid during operation, especially location precision and quality of processing holes.
- Making Soldermask-the 7th production process of mcpcb multilayer
There are 4 ways for making soldermask: liquid light induced corrosion resistant solvent; Thermosetting soldermaskï¼›UV curing soldermask; Dry film soldermask.
- Surface Finishing-the 8th production process of mcpcb multilayer
In order to facilitate assembly of components, exposed copper foil surface must be treated, for enough solderability, good bonding power and comprehensive manufacturing performance. There are 4 ways for surface finishing: HASL, OSP, Sn and Ni/Au.
- Profile-the 9th production process of mcpcb multilayer
- Test-the 10th production process of mcpcb multilayer
- Packaging-the last production process of mcpcb multilayer
Packaging of mcpcb multilayer is important for reducing abrasion mark and wear. Using low-sulfur sheet for vacuum sealing is a good choice. Foam can also be used separately. The key is to isolate soldering flux from aluminum surface, in this way, we can eliminate galvanic electricity reaction between different metals.