MCPCB (Metal Core Printed Circuit Board) is a key component in modern electronics, especially in terms of heat management. It is widely used in LEDs and can be found in almost all LED products. From LED applications to power electronics, MCPCB plays a vital role in ensuring that devices remain cool, efficient and long-lasting.
What is MCPCB?
MCPCB, full name Metal Core PCB, is also known as aluminum substrate or aluminum-based circuit board. It is a type of circuit board that attaches the original printed circuit board to a metal with better thermal conductivity to improve the heat dissipation performance at the circuit board level.
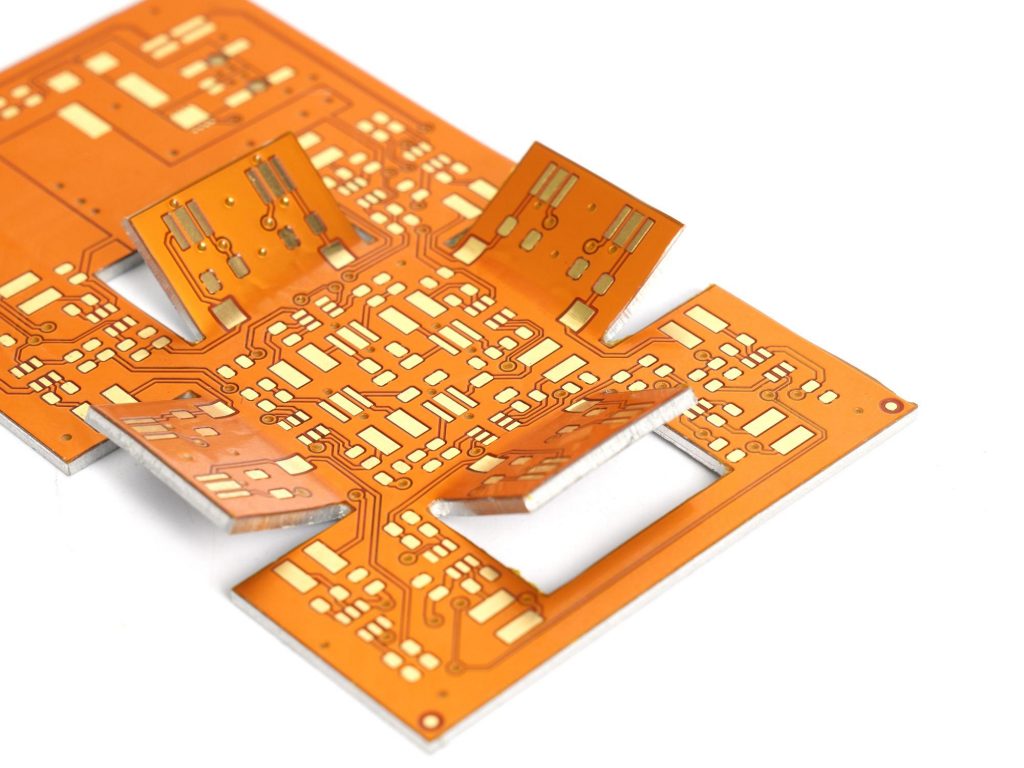
This metal-based printed circuit board usually uses aluminum as the substrate, but also includes the use of other metals such as copper or other high thermal conductivity materials. The design of MCPCB combines the high thermal conductivity of metal with the flexibility of printed circuit boards, making it widely used in various industrial electronic devices.
Especially in the LED industry, MCPCB has become an indispensable component due to its strong magnetic conductivity and excellent heat dissipation. In addition, in the production process of MCPCB, in addition to using aluminum substrates, fiberglass boards (FR-4) are also used for some designs, but special heat dissipation pads need to be designed and fixed by screws or glue.
What is the use of MCPCB?
The main use and advantage of MCPCB (metal core printed circuit board) lies in its excellent heat dissipation performance.
MCPCB, full name Metal Core PCB, is a printed circuit board attached to a metal with better heat conduction effect, thereby improving the heat dissipation at the circuit board level.
This design not only improves the heat dissipation performance of the circuit board, but also has some specific application restrictions, such as the temperature cannot exceed 140℃ when the circuit system is operating, which is determined by the characteristic limitations of the dielectric layer.
During the manufacturing process, the temperature must not exceed 250℃~300℃, which must be understood in advance before passing the tin furnace. This design of MCPCB makes it widely used in many fields, including but not limited to:
LED lights: used for spotlights, high-current PCBs, high-current LEDs, street safety applications, etc.
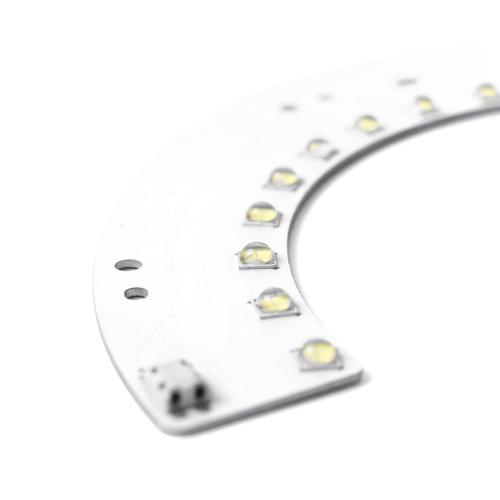
Automotive electronics: used in power conditioners, ignition tools, switching converters, variable optical systems, and motors for electric and hybrid vehicles.
Power supply equipment: such as DC-DC converters, voltage regulators, high-density power conversion, and switching regulators.
Audio equipment: balanced, input-output, audio, power supply, and pre-shielded amplifiers.
Home appliances: flat panel displays, motor controls, etc.
OA equipment: large electronic display substrates, thermal print heads, and printer drivers.
The unique combination of MCPCB (metal plate, insulation layer, and additional copper foil) provides strong magnetic conductivity and excellent heat dissipation, which is particularly important in the LED industry.
In addition, the high thermal conductivity of MCPCB allows the generated heat to dissipate quickly, preventing heat accumulation and ensuring that the LED operates within the optimal temperature range, which plays an important role in improving the performance, thermal management, and overall reliability of UV LEDs.
What is the difference between FR4 and MCPCB?
The main difference between FR4 and MCPCB (metal matrix printed circuit board) is their heat dissipation performance, material composition, and application areas.
1. Heat dissipation performance:
FR4 has a low thermal conductivity and its heat dissipation performance is not as good as MCPCB. MCPCB is based on its metal core (usually aluminum or copper), and transfers heat to the heat sink through the thermal conductive dielectric layer and the metal substrate, and has good heat dissipation ability.
2. Material composition:
FR4 is a multi-layer printed circuit board material composed of glass fiber cloth and epoxy resin. It has good electrical and mechanical processing performance, but general heat dissipation performance.
MCPCB attaches the original printed circuit board to a metal with better thermal conductivity. The design of the metal substrate and the thermal conductive dielectric layer significantly improves the heat dissipation efficiency.
3. Application field:
FR4 is widely used in electronic equipment that requires basic heat dissipation requirements due to its low cost and good electrical performance.
MCPCB is often used in high-power, high-heat-intensive application scenarios due to its excellent heat dissipation performance, such as TVs, monitors and other cost-sensitive products.
In summary, MCPCB has better heat dissipation performance than FR4 through its metal substrate and optimized thermal conductivity design, and is particularly suitable for application scenarios that require high-performance heat dissipation.
What is the structure of MCPCB?
The structure of MCPCB consists of a circuit layer (copper foil layer), a thermal insulation layer and a metal base layer.
Circuit layer (copper foil layer): It requires a large current carrying capacity, so thicker copper foil should be used, and the thickness is generally between 35μm~280μm.
Thermal insulation layer: This is the core technology of PCB aluminum substrate, usually composed of special polymers filled with special ceramics, with low thermal resistance, excellent viscoelastic properties and resistance to thermal aging, and can withstand mechanical and thermal stress.
Metal base layer: Aluminum or copper metal is used as the base material of the circuit board, and a layer of copper foil or copper plate metal plate is attached to the substrate as a circuit to improve problems such as poor heat dissipation.
How thick is the copper in MCPCB?
The thickness of copper foil in MCPCB is generally 35μm~280μm.
The structure of MCPCB (Metal Core PCB) consists of circuit layer (copper foil layer), thermal conductive insulation layer and metal base layer. The circuit layer requires a large current carrying capacity, so thicker copper foil should be used.
Such thickness can meet the demand of high current carrying capacity. The use of such copper foil guarantees the superiority of MCPCB in electrical performance and thermal conductivity.
What is the thermal conductivity of MCPCB?
The thermal conductivity of MCPCB varies with the materials used, but is generally much higher than that of standard FR4 PCB. Most MCPCBs have a thermal conductivity in the range of 1 W/mK to 5 W/mK. In contrast, the thermal conductivity of FR4 boards is about 0.3 W/mK, which makes them much less efficient in heat dissipation.
The advantage of MCPCB is that its heat dissipation performance is significantly better than that of standard FR-4 structure. This advantage is not only reflected in the thermal conductivity of the dielectric used, which is far higher than that of conventional epoxy glass, but also in its heat transfer efficiency, with a thermal transfer index of one-tenth the thickness being more efficient than that of traditional rigid PCB.
What is MCPCB led?
MCPCB LED refers to a light-emitting diode (LED) that uses a metal core printed circuit board (MCPCB) as a heat dissipation substrate. This technology uses a metal core printed circuit board as a heat dissipation substrate for LEDs to improve the heat dissipation performance of the LED, thereby ensuring stable operation and extending the service life of the LED.
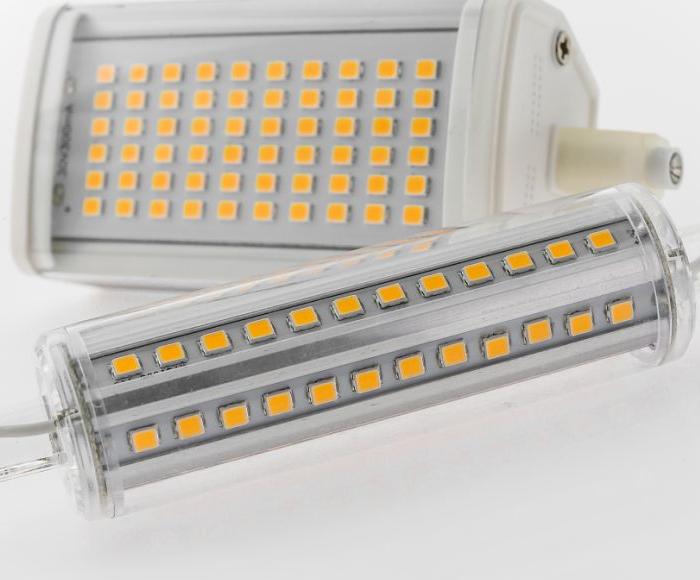
MCPCB is a special printed circuit board in which the metal core acts as a thermal conductive layer, which can effectively conduct the heat generated by the LED to avoid overheating that affects the performance and life of the LED.
In addition, the design and manufacture of MCPCB also consider the needs of electrical connections and physical support to ensure the reliability and stability of the LED module. With the increasing application of high-power LEDs, MCPCB technology has been favored for its excellent heat dissipation performance and has become one of the key technologies in high-power LED packaging.
Conclusion:
MCPCB has a unique structure, including a conductive metal base, a dielectric insulation layer, and a copper circuit layer, which can provide a reliable solution to the heat dissipation challenges in modern electronic products. As the demand for high-performance electronic products continues to grow, the demand for advanced materials such as MCPCB will also continue to grow to meet these thermal management challenges.