Soldering is a critical process in electronics manufacturing. It involves joining components to a printed circuit board (PCB) using a metal alloy called solder. Over the years, the industry has seen a shift from traditional lead-based solder to more environmentally friendly options. This shift has introduced terms like RoHS and Pb-free into the vocabulary of professionals. Understanding these terms, especially in relation to soldering temperatures, is crucial for anyone involved in electronics production.
This guide will break down the differences between RoHS and Pb-free soldering, focusing on their temperature requirements. We’ll explore what these terms mean and how they impact the soldering process.
What Does RoHS Stand For?
RoHS stands for Restriction of Hazardous Substances. It’s a directive that originated in the European Union, aiming to limit the use of certain hazardous materials in electrical and electronic products. Specifically, RoHS restricts substances like lead (Pb), mercury, cadmium, hexavalent chromium, and some flame retardants in manufacturing processes.
The directive came into effect in 2006 and has since become a global standard for electronics manufacturers. Complying with RoHS means that a product does not contain any of the restricted substances above a certain threshold. This initiative was created to reduce the environmental and health impacts associated with these hazardous materials.
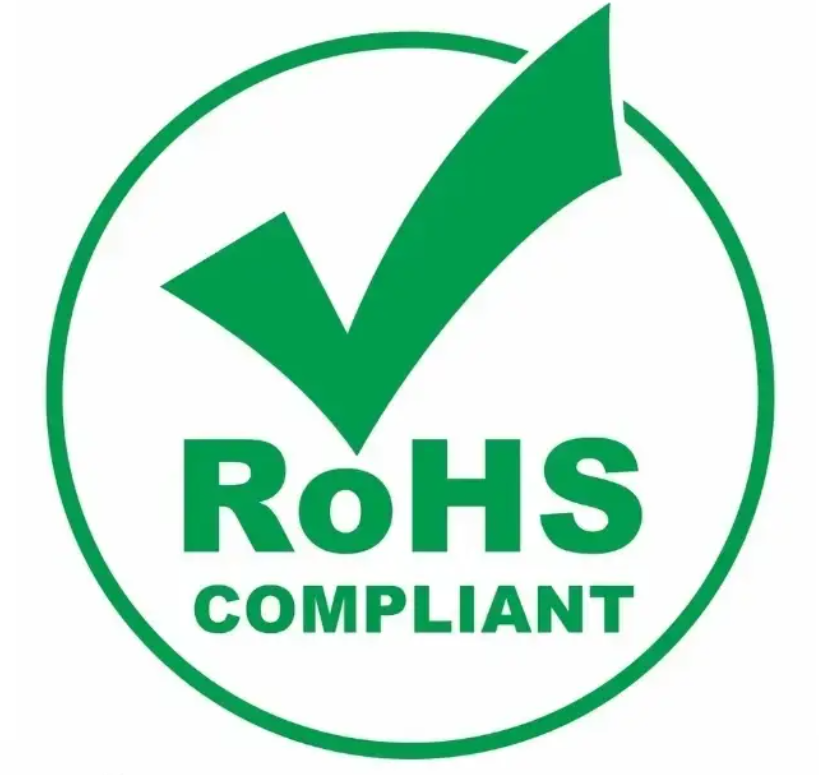
What Does Pb-Free Mean?
Pb-free, as the name suggests, refers to the absence of lead (Pb) in a product or process. In the context of soldering, Pb-free means that the solder alloy used does not contain lead. Lead has traditionally been a key component in solder due to its low melting point, making it easier to work with. However, the toxic nature of lead and its environmental impact has led to a global shift towards Pb-free alternatives.
Pb-free solder usually consists of a combination of tin (Sn), silver (Ag), and copper (Cu). These alternatives have a higher melting point than lead-based solder, which requires adjustments in the soldering process, especially in terms of temperature.
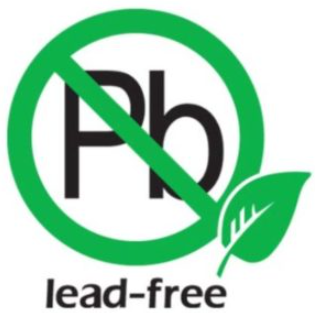
Is RoHS the Same as Lead-Free?
While RoHS and Pb-free are related, they are not the same thing. RoHS is a regulatory standard that restricts the use of several hazardous substances, including lead. Pb-free, on the other hand, specifically refers to the absence of lead in a product or process.
In other words, Pb-free solder is a product that complies with the RoHS directive, but RoHS covers a broader range of materials beyond just lead. Therefore, a product can be RoHS compliant without being entirely Pb-free if it still contains lead within acceptable limits set by the directive.
What Is the Difference Between RoHS and Pb?
RoHS is a directive, a set of rules that manufacturers must follow to ensure their products are safe and environmentally friendly. Pb refers to lead, a specific element that RoHS seeks to limit or eliminate in electronic products.
The main difference lies in their scope. RoHS is about regulation, while Pb (lead) is one of the substances that these regulations seek to control. Pb-free solder is a direct result of the RoHS directive’s push to eliminate lead from electronics manufacturing. However, Pb-free soldering requires different handling and temperatures, which brings us to the next key points.
What Temperature Is Pb-Free Soldering?
Pb-free soldering requires higher temperatures compared to traditional lead-based soldering. The typical melting point of Pb-free solder is around 217°C to 220°C (423°F to 428°F). This is significantly higher than lead-based solder, which melts at around 183°C (361°F).
The higher temperature is due to the different alloy composition in Pb-free solder. Tin (Sn), silver (Ag), and copper (Cu) are the main components, and they require more heat to reach a liquid state. This means that when working with Pb-free solder, the soldering equipment must be capable of reaching and maintaining these higher temperatures.
Adjusting to this temperature is crucial because improper soldering temperatures can lead to weak joints, incomplete soldering, or damage to components. Therefore, manufacturers often need to recalibrate their soldering equipment when switching to Pb-free processes.
What Temperature Does RoHS Solder Melt At?
RoHS-compliant solder includes both lead-free and lead-based options, depending on the specific application and compliance level. For lead-free, which is common in RoHS-compliant products, the melting temperature is typically in the range of 217°C to 220°C (423°F to 428°F), similar to Pb-free solder.
However, if the RoHS-compliant product still uses lead-based solder within the allowable limits, the melting temperature would be around 183°C (361°F). This is less common today as more manufacturers move towards entirely lead-free processes to fully comply with RoHS and similar regulations.
The shift to RoHS-compliant soldering involves understanding these temperature differences and adjusting manufacturing processes accordingly. This ensures the reliability and durability of the solder joints in electronic products.
What Is the Best Temperature for Lead-Free Solder?
The best temperature for lead-free soldering typically ranges between 240°C to 250°C (464°F to 482°F). This range provides a buffer above the melting point to ensure proper flow and bonding of the solder.
Working within this temperature range helps achieve a strong, reliable solder joint while minimizing the risk of overheating and damaging sensitive components. It’s essential to monitor the soldering process closely because exceeding this range can cause problems, such as burnt components or damaged PCBs.
Manufacturers must carefully control the temperature during lead-free soldering to maintain the quality and integrity of the solder joints. Proper temperature control is a critical factor in producing durable, long-lasting electronic products.
Which is Best for PCB Soldering?
When it comes to PCB soldering, the choice between lead-based (Pb) solder and lead-free (Pb-free) solder depends on various factors, including environmental regulations, the application of the PCB, and the desired properties of the solder joints. Here’s a breakdown to help you decide which is best for your needs:
1. For environmental compliance, Pb-free solder is the best choice if you need to meet regulatory requirements like RoHS. It’s also better for the environment and human health.
2. Lead-based solder might be better if you’re working on non-compliant projects where ease of use and joint durability are top priorities, such as prototyping or repair work.
3. For modern electronics manufacturing, Pb-free solder is increasingly the standard, especially for products that need to be sold globally. It’s also the best choice for future-proofing your manufacturing processes against tightening environmental regulations.
In conclusion, Pb-free solder is generally the best choice for modern, environmentally conscious PCB manufacturing, particularly when compliance with regulations like RoHS is necessary. However, lead-based solder may still be preferred for specific applications where ease of use and durability are more important than regulatory compliance.