What substrate is Rogers RT Duroid 5880?
Rogers RT Duroid 5880 is a high-frequency laminate specifically designed for applications where precision and low signal loss are critical. The substrate is a composite material known for its excellent performance in RF and microwave circuits. It uses a PTFE (polytetrafluoroethylene) base reinforced with glass microfibers.
The use of glass microfiber ensures the material is durable but lightweight, making it suitable for applications in which weight is a factor. Its composition is perfect for projects where high-frequency signals are involved. From defense systems to automotive radar, RT Duroid 5880 is a reliable choice. It has become the go-to substrate for engineers and designers looking for efficiency, precision, and durability.
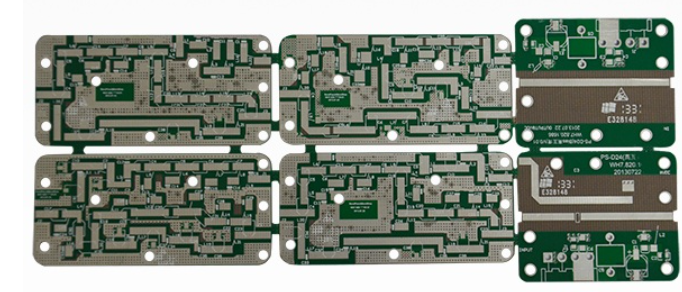
Composition of Rogers RT/duroid 5880
RT Duroid 5880 is composed of PTFE (polytetrafluoroethylene) combined with glass microfiber. PTFE provides a low dissipation factor, which reduces signal loss. This is important for maintaining high performance in RF and microwave applications. Glass microfiber reinforces the material, make it stronger without adding unnecessary weight. The composition also includes copper cladding, which is typically laminated on both sides. The copper layer helps with conductivity, ensuring signals travel efficiently across the board.
The unique combination of PTFE and glass microfiber gives RT Duroid 5880 its excellent mechanical stability. It also minimizes the effect of temperature changes, which is critical for high-frequency circuits. As a result, the material can handle extreme temperatures without affecting the performance of the PCB.
RT/duroid 5880 Specifications
The following table highlights the important specifications of Rogers RT Duroid 5880. These specs reflect the high performance of RT Duroid 5880 for complex RF and microwave tasks.
Property | Value |
Dielectric Constant (Dk) | 2.20 (±0.02) |
Dissipation Factor (Df) | 0.0004 (measured at 10 GHz) |
Thermal Conductivity | 0.20 W/m/K |
Operating Temperature Range | -55°C to +150°C |
Water Absorption | 0.02% |
Volume Resistivity | 1.7 x 10^9 MΩ·cm (minimum) |
Surface Resistivity | 1.4 x 10^8 MΩ (minimum) |
Coefficient of Thermal Expansion (CTE) | 46 ppm/°C (in X-Y axis) |
Tensile Strength | 10.3 MPa |
Flammability | UL 94 V-0 |
Peel Strength | 5.0 N/mm (after soldering) |
RT/duroid 5880 Thickness
RT Duroid 5880 comes in various thicknesses. Engineers can choose the right thickness depending on their project’s needs. Rogers RT/duroid 5880 laminate is commercially available in sheet stock and roll stock forms in a range of thicknesses. Here’s a list of the standard thicknesses available:
Available sheet sizes:
- 304.8 x 457.2 mm
- 457.2 x 609.6 mm
- 609.6 x 914.4 mm
Standard thickness:
- 0.127 mm (5 mils)
- 0.254 mm (10 mils)
- 0.381 mm (15 mils)
- 0.508 mm (20 mils)
- 0.787 mm (31 mils)
- 1.524 mm (60 mils)
- 3.175 mm (125 mils)
Available roll widths:
- 304.8 mm
- 609.6 mm
- 1219.2 mm
- Standard roll length: 76.2 meters
- Thickness range: 0.127 mm to 1.575 mm
RO5880 RF PCB Advantages
Rogers RT Duroid 5880 has a lot of strengths when used in RF and microwave PCB projects:
- Minimal Signal Loss
With a low dissipation factor of 0.0004, it reduces signal loss, which is very helpful for high-frequency systems like radar or satellite communications.
- Strong Stability
It holds up well under temperature changes and in humid environments, keeping circuits running smoothly even in tough conditions.
- Reliable Electrical Properties
The dielectric constant of 2.20 remains stable over a range of frequencies. This helps keep circuits working consistently without interference or signal issues.
- Heat Tolerance
It withstands heat up to 150°C, making it a good choice for systems that need to handle higher temperatures.
- Low Moisture Absorption
With only 0.02% water absorption, the material works well in damp environments. Outdoor systems like antennas benefit from this.
- Ease of Manufacturing
The material is easy to work with during production, which keeps costs lower and speeds up manufacturing.
- Chemical Resistance
The PTFE base resists damage from chemicals and solvents, making the material last longer in harsh environments like aerospace and industrial applications.
Typical Applications of High-Frequency PCB
High-frequency PCBs built with Rogers RT Duroid 5880 serve important roles across many industries:
- Aerospace – used in radar, satellite, and navigation systems, RT Duroid 5880 supports reliable communication and tracking, even in high-pressure environments.
- Telecommunications – in mobile networks, base stations, and antennas, high-frequency PCBs help maintain clear and fast data transmission, supporting the backbone of communication systems.
- Medical Devices – MRI machines, wireless health monitors, and other equipment use high-frequency PCBs to keep medical data accurate and systems working seamlessly.
- Defense – communication gear, and electronic warfare systems.
- Automotive Systems – advanced driver assistance systems (ADAS) and vehicle radar depend on high-frequency PCBs for real-time data, making roads safer for everyone.
- Satellite Communication – RT Duroid 5880 is frequently used in satellite systems where strong signal transmission over long distances is crucial for communication networks.
Common-Used High Frequency PCB Materials in Best Technology
At Best Technology, we use a range of top-quality materials for high-frequency PCBs, depending on the project’s needs. Some of the most popular materials include:
Material | Dielectric Constant (Dk) | Loss Tangent (Df) | Key Features |
Rogers RO4003C | 3.38 | 0.0027 | Low loss, excellent thermal stability, ideal for RF applications. |
Rogers RO4350 | 3.48 | 0.0043 | Low loss, high thermal conductivity, suitable for microwave applications. |
RT/Duroid RO5880 | 2.94 | 0.0037 | Very low loss, excellent performance at high frequencies, good for multilayer designs. |
N4000-13 | 3.0 | 0.009 | Good thermal stability, low moisture absorption, designed for high-frequency applications. |
Taconic RF-60A | 6.15 | 0.0027 | High dielectric constant, low loss, suitable for low-loss RF and microwave applications. |
Each material brings different strengths for specific applications, giving you the best options for your project.
Discuss Your High Frequency PCB Project with Us Today
If you have a high-frequency PCB project in mind, reach out to us. We’re experienced in creating high-quality PCBs that meet your exact specifications. Whether you need RF, microwave, or other types of high-frequency boards, we’ll make sure your project runs smoothly. Contact us at sales@bestpcbs.com today, and we’ll help you turn your plans into reality.