What is the role of solder paste? Electronic devices have been deeply integrated into our daily lives. Whether it is mobile phones, tablets or household appliances, they are inseparable from electronic components. How are these components accurately soldered to the circuit board? The answer lies in surface mount technology (SMT) and the important material it uses – solder paste.
In the process of SMT patch processing, solder paste is an indispensable and important material. The quality and use method of solder paste directly affect the welding effect and the performance of the final product.
What is the composition of solder paste?
Solder paste is a complex mixture of multiple components, and its main components include metal powder, flux and solvent.
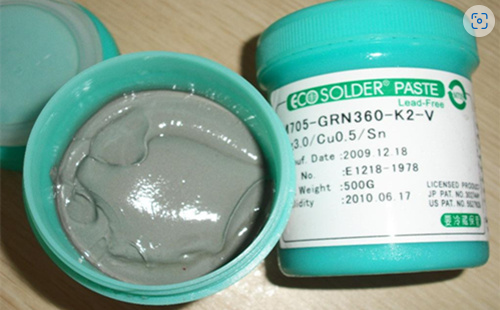
The metal powder in solder paste is usually composed of metal alloys such as tin, silver and copper. The particle size and distribution of metal powder have a direct impact on the welding effect. The smaller the particle size, the more uniform the distribution, and the better the welding effect.
At the same time, the composition of the metal alloy also determines the mechanical strength and electrical properties of the solder joint.
Flux is another important component in solder paste. Its main function is to remove oxides on the welding surface and improve the wettability and reliability of welding.
The type and formula of flux directly affect the melting state and solder joint quality during the welding process. Common fluxes include rosin-based flux, organic acid flux and halogen-free flux.
Solvents are used to adjust the viscosity and printing performance of solder paste. Appropriate viscosity can ensure that the solder paste is evenly distributed during the printing process without problems such as drawing and collapse. The evaporation rate of the solvent will also affect the drying time and welding performance of the solder paste.
What is the role of solder paste in SMT patches?
In the SMT (surface mount technology) patch processing process, solder paste plays a vital role. It is not only used to bond components, but also the key to ensure the quality of electrical connections and mechanical strength.
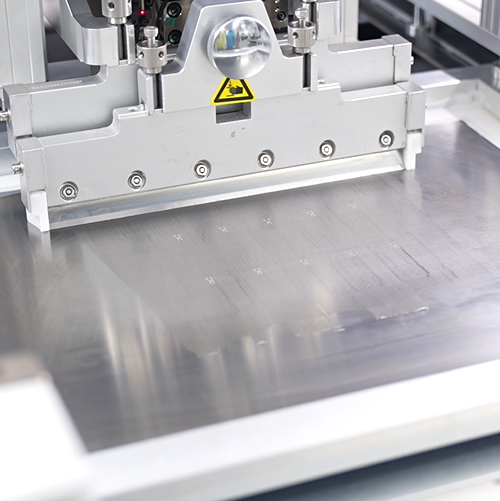
1. Bonding components
One of the main functions of solder paste is to bond components. After the solder paste is accurately printed on the pads of the PCB (printed circuit board), the pins or contact points of the electronic components will be placed on the solder paste. The solder paste melts during the reflow soldering process to form a strong bond, ensuring that the components are stably attached to the PCB.
2. Provide electrical connection
Solder paste melts during the reflow soldering process and forms metal solder joints, which not only bond components but also provide electrical connections. Good electrical connections ensure the effective transmission of electrical signals on the PCB, which is the basis for ensuring the normal operation of electronic equipment.
The solder joints formed by the metal components (such as tin, silver, and copper) in the solder paste after melting have excellent conductivity, ensuring the reliability and stability of electrical connections.
3. Ensure mechanical strength
The mechanical strength of the solder joints is the key to ensuring the stable operation of electronic components in various environments. The solder joints formed by the solder paste after reflow soldering have sufficient mechanical strength to resist external stresses such as vibration, impact, and thermal expansion and contraction. This not only protects the components and PCB, but also improves the reliability and service life of the entire electronic equipment.
Is solder paste the same as flux?
Solder paste and flux are not the same.
Although both solder paste and flux are materials used in the welding process, their functions and uses are different.
Solder paste is a paste-like viscous body, the main components of which include metal powder, rosin, organic acid, thixotropic agent, and activator, and is used for welding in SMT automatic mounting process.
Flux is a liquid, a mixture with rosin as the main component, which is used to remove oxides on the surface of solder and the base material to be welded, so that the metal surface reaches the necessary cleanliness, prevents the surface from re-oxidation during welding, reduces the surface tension of the solder, and improves welding performance.
In general, although both solder paste and flux are indispensable materials in the welding process, they have obvious differences in form, function, and usage.
What is the storage method of solder paste?
The correct storage method can extend the service life of the solder paste and ensure its stable performance.
1. Temperature control
Solder paste should be stored in a low temperature environment, usually 0-10℃. Excessive temperature will cause the solvent in the solder paste to volatilize, affecting its viscosity and printing performance. Avoid direct sunlight and high temperature environment during storage to prevent the solder paste from deteriorating.
2. Humidity control
Humidity has a great impact on solder paste. Excessive humidity will cause the solder paste to absorb moisture, affecting its printing performance and welding quality. The relative humidity of the storage environment should be controlled below 50% to ensure the stability of the solder paste.
3. Sealed storage
The solder paste should be stored in a sealed container to prevent oxygen and moisture from entering the air. The solder paste after opening should be used up as soon as possible, and the unused solder paste should be resealed and stored in a low temperature environment.
How to use solder paste correctly?
1. Reheating treatment
The solder paste stored in a low temperature environment should be reheated before use. The reheating time is usually 4-8 hours. During the reheating process, it should be avoided to be directly exposed to a high temperature environment to prevent the solvent in the solder paste from volatilizing. The solder paste after reheating should be fully stirred to ensure that the metal powder and flux are evenly distributed.
2. Printing process
Solder paste printing is a key process in SMT patch processing. During the printing process, the scraper pressure, printing speed and template opening size should be controlled to ensure that the solder paste is evenly distributed on the pad. The printed solder paste should have a good shape and should not have problems such as drawing and collapse.
3. Solder paste reflow
The solder paste reflow process is the process of melting the solder paste and forming a firm solder joint with the pad and component pin. The temperature curve should be controlled during the reflow soldering process to ensure that the solder paste melts at an appropriate temperature and fully wets the pad and pin. Too high or too low reflow temperature will affect the welding quality.
4. Solder joint detection
The quality of the solder joint is an important indicator for evaluating the welding effect. After the welding is completed, the solder joint detection should be carried out to check the shape, size and wettability of the solder joint. Qualified solder joints should have a smooth and complete surface without defects such as solder balls and cold solder joints.
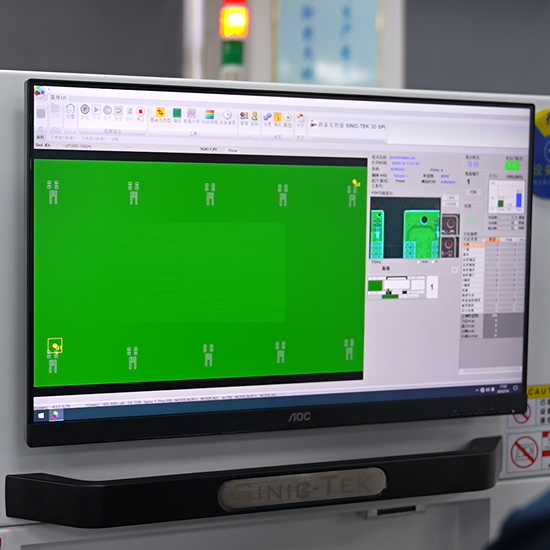
Conclusion:
Solder paste plays a vital role in SMT patch processing. Its composition, selection, storage and use methods directly affect the welding quality and the performance of the final product. By understanding and mastering the relevant knowledge of solder paste, the quality of SMT patch processing can be effectively improved, and defects and rework rates can be reduced.
BEST Technology has rich experience and strict control standards in the selection and use of solder paste, and can provide customers with high-quality SMT patch processing services. If you have any questions about our products or services, please feel free to contact us. Choose BEST Technology , choose quality assurance.